Why the EV Revolution Requires Battery Evolution
Tomorrow’s electric vehicles demand a revolution in battery innovation – lighter, more powerful, and more sustainable, delivered at unprecedented scale.
The Next Gear in Battery Development
The transition of electro-chemical power systems from the lead battery to the lithium-ion battery, has been an incredible enabler for Electric Vehicles (EVs). But the journey doesn’t stop here. The energy storage systems of tomorrow will need to be lighter, have a higher-energy density, and be far more sustainable if industry-wide electrification is to take place.
Moreover, as well as delivering cutting edge specifications, the high-performance battery of the future also needs to be deployed to market at speed. In the US alone, vehicle battery demand grew 80% between 2021 and 2022 .
A gear shift in manufacturing capacity is needed.
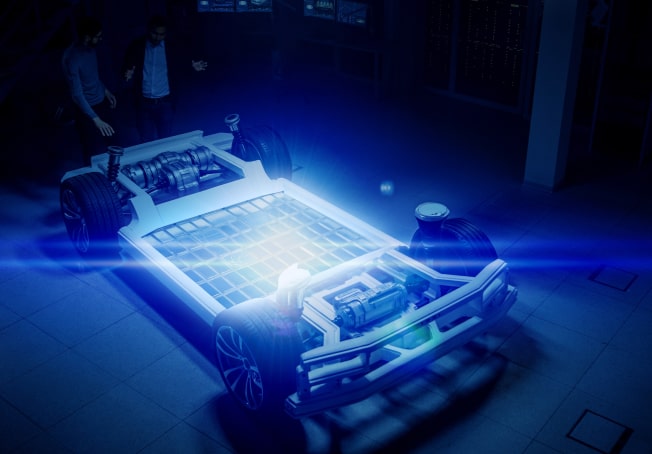
Battery Engineering, Re-energized
These demands have major implications for every step of the battery value chain, from cell innovation to giga-scale battery factories. Delivering truly innovative battery technology – whether that means defining new processes, cultivating new expertise, or building new facilities – is a complex and multi-faceted challenge.
Dassault Systèmes is on hand to provide a full suite of multi-scale, multi-physics virtual twin and simulation solutions that enable battery organizations to navigate this complexity. From new materials development to large scale manufacture, we give battery makers the insight and capabilities they need to define and deliver effective change.
Making Connections: Exploring Battery Manufacturing Challenges in an EV-first World
Aligning battery production with the needs of the EV market will necessitate widespread change. However, just like modules on a circuit board, every node on the battery value chain is connected to every other node; if we change one, we impact all the others, from chemical processors and refiners all the way to automakers. Enabling change in such a complex and interconnected system demands visibility and flexibility, embedded everywhere.
Here, we explore three scenarios reflecting three core challenges facing the Transportation & Mobility industry today:
Q&A with our Battery Experts
What are the best ways to overcome the issues impacting your battery business? Our experts answer battery makers’ most frequently asked questions:
The big story today is the drive to improve while maintaining and enhancing the safety of batteries. Design and optimization of cell chemistry will pave the way to achieving this goal, and all the time we are seeing new breakthroughs – like lithium-sulfur batteries or solid-state electrolyte batteries – which promise to be safer while also having higher energy density.
– Lalitha Subramanian, Senior Director and Fellow, BIOVIA
Simulation’s ability to model complex behaviors from the atomic scale up is incredible in helping design safer and more high-performant batteries.
- Molecular dynamics simulations help researchers identify materials that will power the next generation of powerful, resilient, and cost-effective batteries.
- Finite Element Modeling techniques allow developers to analyze stress, strain, and heat distribution within battery cells, and design robust, thermally-efficient cells.
- Microstructural simulations allow designers to optimize electrolyte, aging, safety, and performance of batteries.
- System-level simulations model entire battery packs, from interactions between single cells and battery management systems (BMS) or degradation mechanisms.
And, by reducing prototyping and improving right-first-time, it also means that we can deliver next-gen batteries whilst cutting cost- and time-to-market.
– Rudy Pastuzak, Battery Industry Solution Experience Director, ENOVIA
A key challenge facing battery supply chains will be meeting skyrocketing demand for key materials like lithium, cobalt, nickel, manganese, and copper; particularly when new mines are not opening fast enough – and a new mine can take more than a decade to become operational. Long-term partnerships will be essential in ensuring adequate supply. That can mean opening new mines. But others are starting to seriously explore recycling, not just a sustainability play, but as a source of battery materials.
– Nicolas Vallin, Battery Expert, Transportation & Mobility Industry
The future battery cell factory will be very large, occupying several thousand square meters. Human participation will be greatly reduced; machinery will be extensively automated, and autonomous guided vehicles (AGVs) will be common – allowing for round-the-clock operation. Digital solutions, like virtual twins, will facilitate operator decision-making, and power new capabilities like predictive maintenance, remote monitoring, smart parameter setting, or smart inline control.
– Simon Mellier, Industry Process Consultant, DELMIA
One of the key benefits of virtual twins is battery developed is enabling effective collaboration between otherwise siloed parts of the value chain.
- Developers and materials providers can collaborate on a single model of the battery factory.
- Machine makers and the battery cell designers can share technical models and reduce back-and-forth between different design teams.
- Process engineers and product engineers can evaluate production feasibility, ensure right-first-time operations, and reduce time-to-volume.
- Operations managers can establish real time visibility by combing model and shop-floor data, and identify and remediate operational issues.
– Simon Mellier, Industry Process Consultant, DELMIA
Simulation allows for the virtual testing of various manufacturing parameters, such as electrode coating, electrolyte mixing, and cell assembly, and can identify optimal conditions for consistent quality and performance. Simulation can also be used to train workers, enhance skill levels, accelerating onboarding and improve overall productivity. All this can lead to improved quality, higher yields, enhanced efficiency, and reduced waste and cost, giving battery makers the competitive edge.
– Rudy Pastuzak, Battery Industry Solution Experience Director, ENOVIA
Making truly sustainable batteries is a complex and multifaceted task, but those looking to build a sustainable and circular battery business must:
- Select materials with minimal environmental and political impacts.
- Optimize energy efficiency to limit resource consumption and waste.
- Extend battery lifetimes, reducing disposal and replacement.
- Design for easy disassembly and regeneration of the component materials.
- Encourage the use of recycled batteries in less demanding and critical applications.
- Ensure compliance with regulations like the Battery Passport.
– Lalitha Subramanian, Senior Director and Fellow, BIOVIA
All these challenges require clear visibility of product, factory, and supply chain. Virtual Twin Experiences provide battery makers with the visibility to build successful circular business practices right across the battery life cycle.
– Nicolas Vallin, Battery Expert, Transportation & Mobility Industry
Accelerating Battery Development with Digital Solutions
Explore the tabs below to find out how Dassault Systèmes solutions can help build a battery manufacturing ecosystem fit for the EV future.
- Manage Battery Materials Innovation
- Design High Performance Batteries
- Innovation in Battery Cell Manufacturing
- Solve the Battery Recycling Conundrum
Management for battery materials innovation
Learn how Dassault Systèmes BIOVIA Solutions can help battery makers organize their cell chemistry R&D, integrate their data, manage materials, shorten formulation development cycles, and increase productivity by 40%.
Accelerate and optimize the design of high-performance batteries
Simulation can be instrumental in helping design EV batteries smarter and faster. Learn from Dassault Systèmes about how you can apply virtual twins to help you tailor the range, performance, longevity, and safety of your next-gen high-performance batteries.
Unlocking innovation in battery cell manufacturing
Discover how DELMIA MOM, our fully integrated, scalable, and sustainable manufacturing operations management platform, can help battery makers increase the resilience, flexibility, and manufacturing efficiency of their processes, and meet the global EV boom.
Solve the battery recycling conundrum
Ready to tame the complexity of battery recycling? Discover how virtual twin technology on a unified platform can help battery stakeholders safely extract valuable materials, while reducing your carbon footprint.
Deep Dive into the Challenges
Explore how we can support meeting your battery design challenges, whatever your domain.
Our Customers
Discover how our Transportation & Mobility customers are making high-performance batteries a reality.
Explore our industry solutions
Find out how our industry solutions can help companies accelerate battery development, from cell innovation to gigafactory scale-up.