Formage du plastique sous vide
Le formage sous vide du plastique est une méthode facile pour former des pièces en plastique. Elle est utilisée dans une grande variété d'applications. Apprenez-en plus maintenant !
Introduction : Formage sous vide du plastique
Le formage sous vide est une méthode de fabrication très répandue pour façonner les matières plastiques. Ce procédé est populaire auprès des fabricants en raison de son faible prix et de sa souplesse de conception. Il est le mieux adapté aux produits qui nécessitent un formage de précision sur une seule face. Il est souvent utilisé pour protéger des articles délicats tels que les appareils électroniques et certains aliments et est utilisé pour une grande variété de produits. Inventée dans les années 1800, la première machine de formage sous vide a été construite en 1938 pour l'avion Spitfire, mais ce n'est qu'en 1964 que la première machine de formage sous vide a été brevetée.
Cet article traite du formage sous vide du plastique, de ses avantages, de ses applications typiques et de ses bénéfices.
Qu'est-ce que le formage sous vide ?
Le formage sous vide est un procédé simple qui utilise un moule pour former la géométrie du produit avec une feuille de plastique placée solidement dans un cadre de serrage qui est ensuite chauffé. Elle est placée sur un moule dans lequel sont percés de nombreux petits trous. Cela permet à un vide de former le plastique chauffé pressé sur le moule. Une fois refroidi, le plastique formé est retiré et l'excédent de matériau est découpé. Il s'agit d'un processus relativement rapide qui ne prend que quelques minutes, bien que la complexité de la pièce à fabriquer puisse nécessiter un temps de refroidissement et de découpage plus long.
Il existe deux types de moules sous vide : les moules mâles (positifs) et les moules femelles (négatifs). Les moules mâles sont convexes et épousent les dimensions intérieures de la pièce en plastique. Les moules femelles sont concaves et forment les dimensions extérieures.
Les étapes du formage sous vide sont les suivantes :
- Serrer la feuille de plastique dans le cadre
- Chauffer la feuille de plastique jusqu'à ce qu'elle soit souple
- Mettez la feuille sous vide lorsqu'elle est placée sur le moule.
- Refroidissez la feuille de plastique qui se forme autour du moule - des ventilateurs et des brumisateurs peuvent être nécessaires.
- Détacher la feuille de plastique du cadre
- Coupez l'excédent de matériau.
- Facultatif : le post-traitement peut inclure le ponçage, la peinture, etc.
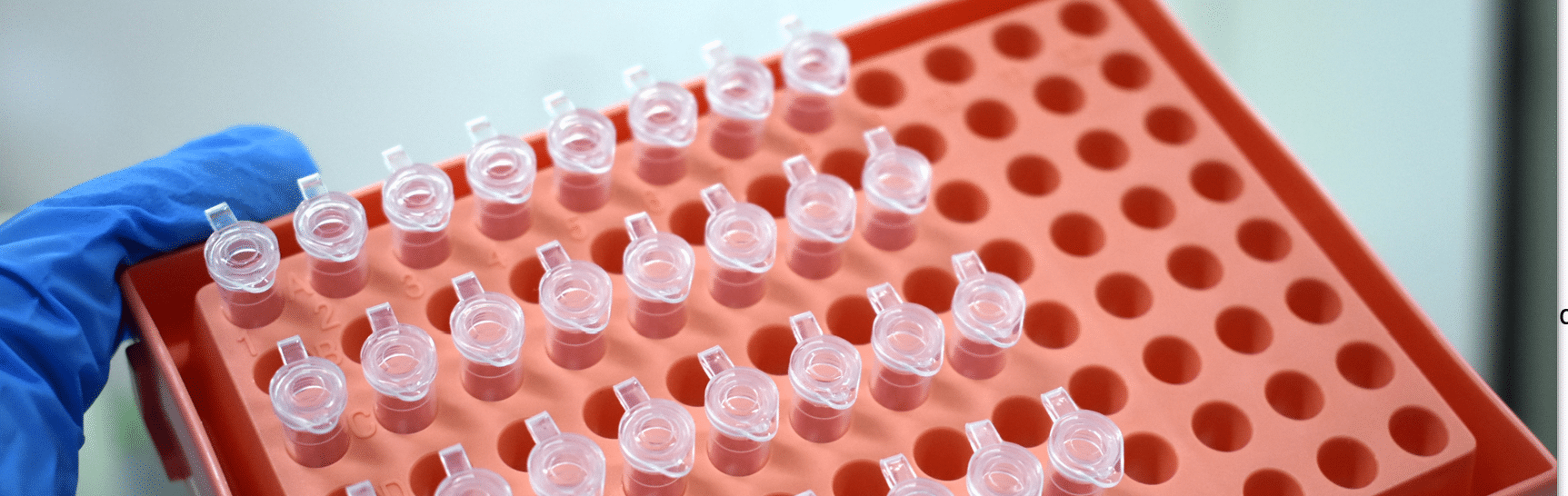
Qu'est-ce que le plastique ?
Le plastique est dérivé de nombreuses matières synthétiques provenant soit de combustibles fossiles, soit de matières renouvelables comme le coton ou le maïs. La cellulose végétale permet de transformer le maïs et le coton en matières plastiques. Ces matériaux sont légers, durables et peu coûteux à fabriquer.
La physique définit la plasticité comme la propriété d'un corps qui ne s'oppose pas à une force déformante, et le corps est déformé de façon permanente. Le mot "plastique" provient du terme "plasticité".
Les principaux types de matières plastiques sont basés sur des structures chimiques, notamment les acryliques, les plastiques halogénés, les polyesters, les polyuréthanes et les silicones. Dans le secteur de la fabrication, les plastiques sont classés en fonction de l'objectif de conception du produit, ce qui inclut les plastiques biodégradables, les polymères conducteurs, les élastomères, les plastiques techniques, les thermoplastiques et les thermodurcissables.
Avec toutes les différentes classifications des plastiques, les familles de polymères sont classées selon que le matériau est réversible ou non après le processus de déformation. Ces deux familles de polymères sont :
- Thermoplastiques - La composition chimique de ces plastiques ne change pas lorsqu'ils sont chauffés. Ces plastiques redeviennent souples lorsqu'ils sont réchauffés. Les matériaux les plus courants sont l'acrylique, le nylon, le polypropylène, le polyéthylène, le polystyrène et le chlorure de polyvinyle (PVC).
- Polymères thermodurcissables : également appelés " thermodurcissables ", ces polymères ne peuvent être fondus qu'une seule fois. Ces polymères ne se ramollissent jamais à nouveau lorsqu'ils sont chauffés. Les matériaux standard sont le polyester, l'ester de vinyle et les polyimides.
L'utilisation du plastique est très répandue dans nombre de nos emballages et produits. Plus de 10 milliards de tonnes de plastique ont été utilisées au cours des 70 dernières années, et leur utilisation augmente de façon exponentielle.
Application du plastique pour le formage sous vide
Les plastiques formés sous vide sont utilisés dans la plupart des produits que nous achetons et utilisons quotidiennement. Voici quelques-unes de ces applications :
- Automobile et transport - Pare-chocs, tapis de sol, pièces de carrosserie, consoles, conduits d'air, doublures de lit, remorques, plaques de protection, ...
- Biens de consommation - Jouets, décoration intérieure, housses de réfrigérateurs, Tupperware®, housses d'aspirateurs, housses et pièces d'appareils électroménagers, ...
- Électronique - Supports, boîtiers, housses pour imprimantes, moniteurs, ...
- Emballage alimentaire - Réserve alimentaire, coquilles de palourdes, caisses à œufs, plateaux diviseurs, ...
- Industrie - Caisses, conteneurs, plateaux, ...
- Médical - Composants d'IRM et de radiographie, chariots médicaux, coussins chauffants, kits chirurgicaux, protège-doigts, blisters, ...
- Emballage - Contenants pour brosses à dents, cosmétiques, rasoirs, électronique, ...
- Autres applications - Présentoirs pour salons professionnels, décorations personnalisées, ...
Vous trouverez ci-dessous quelques-uns des nombreux thermoplastiques utilisés dans le formage sous vide :
- Acrylique (PMMA)
- Acrylonitrile butadiène styrène (ABS)
- Polycarbonate (PC)
- Polyéthylène (PE)
- Polyéthylène téréphtalate glycol (PETG)
- Polypropylène (PP)
- Polystyrène (PS)
- Chlorure de polyvinyle (PVC)
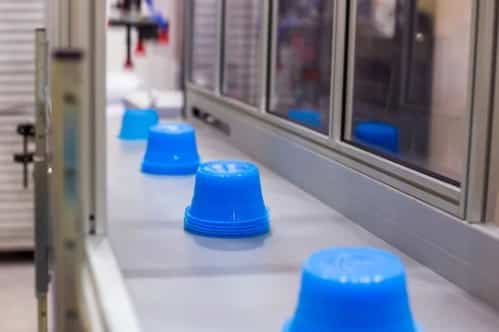
Avantages du formage sous vide du plastique
Le formage sous vide des plastiques est un procédé de fabrication abordable, facile à prototyper et à fabriquer. L'outillage est beaucoup moins coûteux, et la rotation des produits est plus rapide car l'outillage est plus facile à fabriquer. Le temps de production est inférieur à la moitié de celui du moulage par injection. Le produit est solide et robuste, et le processus est évolutif.
Le formage sous vide offre la souplesse nécessaire pour tester de nouvelles conceptions et de nouveaux prototypes sans perte significative de productivité et d'utilisation. Comme il est rentable, c'est le procédé préféré pour les petites et moyennes séries de production. Les options de couleur sont nombreuses, et la personnalisation des produits n'est pas compliquée. Le formage sous vide permet de fabriquer des produits de qualité alimentaire qui sont stériles. Des matériaux d'ingénierie sont disponibles pour diverses applications.
Tous ces avantages se traduisent par une mise sur le marché plus rapide d'un produit relativement peu coûteux et durable.
Obtenez plusieurs devis pour vos projets en quelques secondes