Fabrication composite
Téléchargez votre design, obtenez votre devis de fabrication composite, choisissez votre fabricant et recevez vos pièces !
PAIEMENTS SÉCURISÉS
Avec des cartes bancaires ou des bons de commandes
IP PROTEGE
Avec nous, vos données sont confidentielles et sécurisées. Utilisez votre propre accord de confidentialité.
DEVIS INSTANTANE
Pour l'impression 3D et l'usinage CNC
Fabrication composite avec 3DEXPERIENCE Make
Du contreplaqué aux ailes d'avion, les composites sont présents dans toute la société moderne et sont de plus en plus utilisés à la place des matériaux traditionnels comme le bois et le métal.
Depuis des millénaires, l'homme combine différents matériaux pour créer un objet plus durable, plus souple et plus performant que ses composants.
La fabrication de matériaux composites remonte à la fabrication ancienne de briques, lorsque de la paille était ajoutée à l'argile ou à la boue humide pour accélérer le temps de séchage et obtenir une brique finie plus solide. Les barres d'armature métalliques dans les structures en béton remplissent à peu près la même fonction. Le béton, le deuxième matériau le plus utilisé au monde après l'eau, est lui-même un composite de pierres et de ciment.
La principale raison de fabriquer des matériaux composites est d'améliorer la résistance, comme dans les exemples ci-dessus, mais ce n'est pas la seule. Par exemple, un matériau composite peut être moins cher, plus léger, résistant à l'eau et à la chaleur, plus rigide, conducteur d'électricité ou une combinaison des deux.
Les composites modernes ont été conçus pour répondre à un besoin spécifique et sont couramment utilisés dans des secteurs tels que l'aérospatiale, l'automobile, la défense, la marine, les appareils médicaux et les équipements sportifs.
Parmi les exemples courants, citons le bois d'ingénierie, la fibre de carbone, la fibre de verre, les plastiques renforcés de fibres et les céramiques avancées. La liste des composites ne cesse de s'allonger, car les chercheurs expérimentent différentes combinaisons de matériaux et développent de nouvelles variétés, de nouveaux procédés et de nouvelles applications.
Sur 3DEXPERIENCE Make, nous proposons des options de fabrication de composites à travers plusieurs processus tels que l'impression 3D, l'usinage CNC, la découpe laser et le moulage par injection. 3DEXPERIENCE Make est une plateforme de fabrication à la demande, qui met en relation des concepteurs ou des ingénieurs avec des prestataires de services industriels. Nos fournisseurs de services sont principalement basés en Amérique du Nord (Etats-Unis et Canada) et en Europe (Royaume-Uni, France, Pays-Bas, Allemagne etc...).
Grâce à notre puissant algorithme, vous pouvez obtenir en quelques secondes des devis pour votre projet composite auprès de dizaines de prestataires de fabrication.
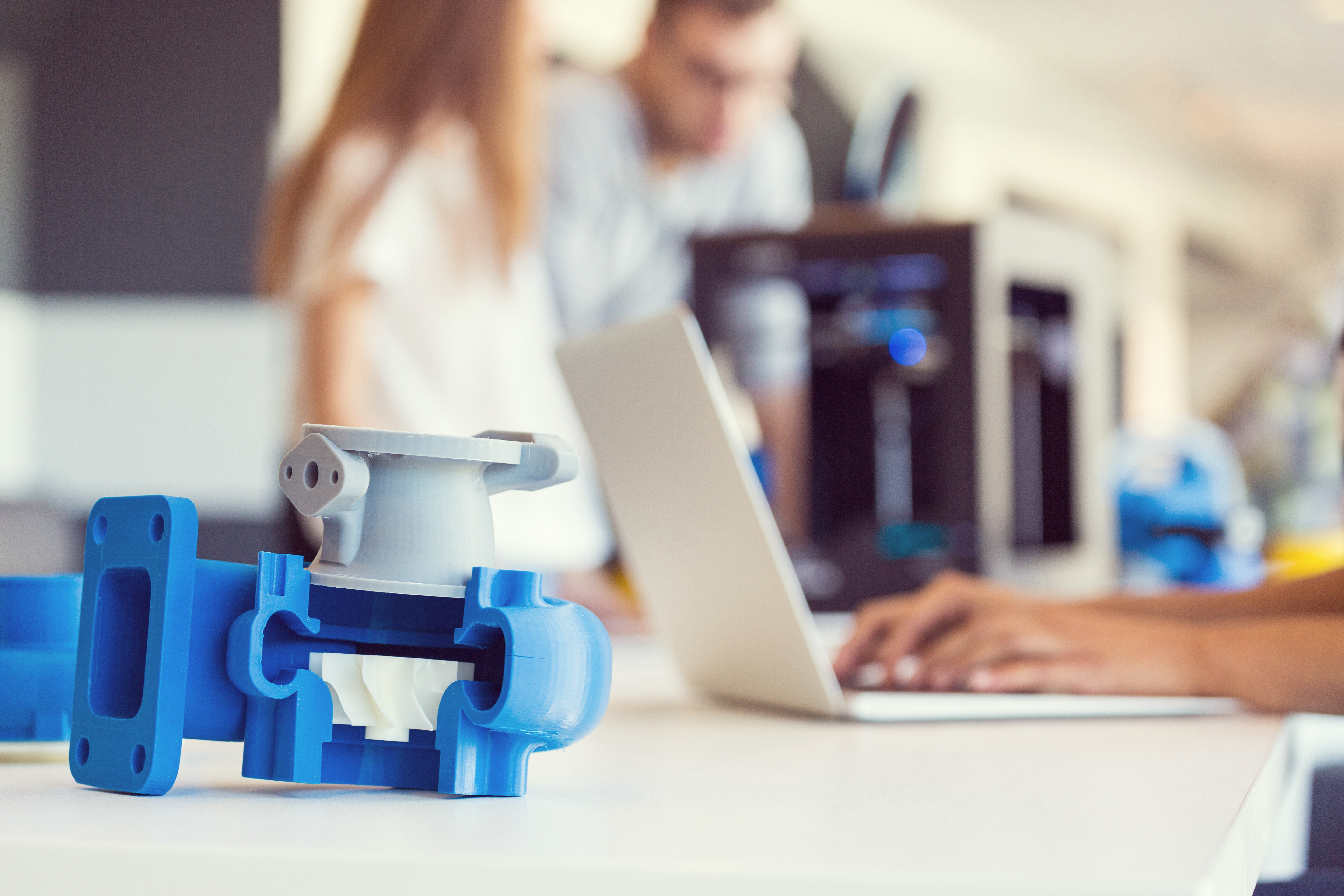
Notre réseau de fabricants de produits composites
Etats-Unis d'Amérique
Canada
Royaume-Uni
France
Allemagne
Pays-Bas
et bien d'autres encore...
Service de fabrication à la demande : comment ça marche ?
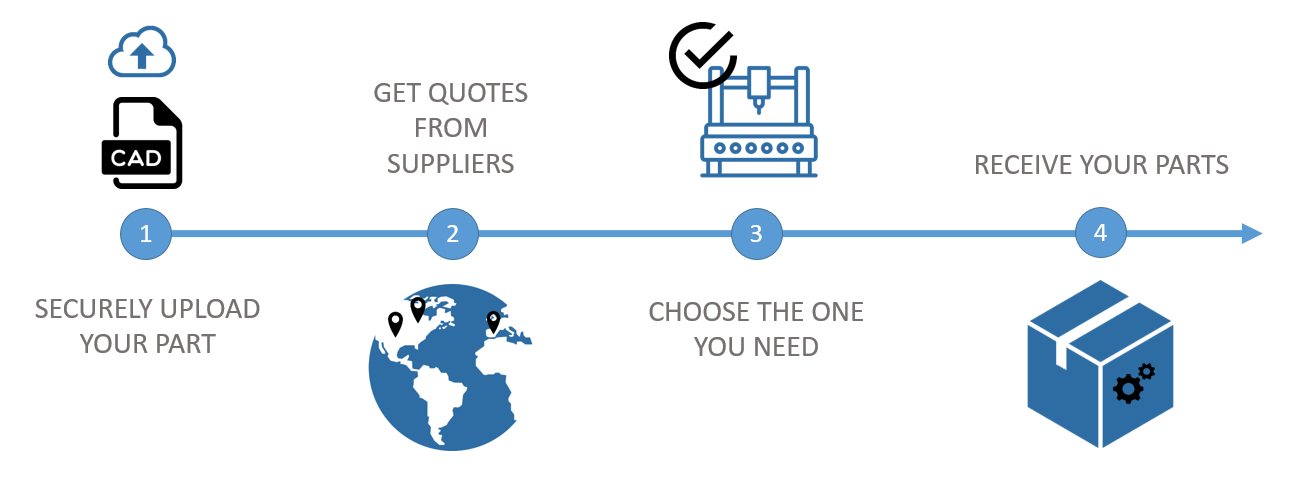
Matériaux composites disponibles auprès de nos prestataires de services
Matériaux composites pour les procédés d'impression 3D
- Fibre de verre en plastique
- Plastique Kevlar
- ABS fibre de carbone
- Gypse
- PA chargé fibre de verre
- PA aluminium
- PA fibre de carbone
- Plastique et fibre de carbone
- PLA bois
- PLA cuivre
- Fibres plastique
- Verre plastique
Matériaux composites pour les procédés d'usinage
- PC fibre de verre
- PA chargé de fibre de Verre
Matériaux composites pour les processus de découpe, de moulage et de formage
- PA chargé de Fibre de Verre
Quels sont les procédés de fabrication composite disponibles dans 3DEXPERIENCE Make ?
Impression 3D - Procédé additif
FDM, SLS, MJF, BJ, SLA...
Découpe
Découpe Laser, Découpe Découpe au jet d'eau, Découpe par lame
Usinage CNC - Soustratif
Fraisage, tournage et électroérosion
Formage
Tôlerie, extrusion, formage, emboutissage
Des fonctionnalités pour vous aider
Check & repair ou Geometry check est une fonction qui vous aide à comprendre les problèmes de géométrie de votre pièce et à les réparer directement et en ligne.
Check & Repair
Check & repair ou Geometry check est une fonction qui vous aide à comprendre les problèmes de géométrie de votre pièce et à les réparer directement et en ligne.
Contrôle de la fabricabilité
Cette fonctionnalité est disponible uniquement pour le service d'impression 3D. Elle vous aide à vérifier la fabricabilité de votre pièce, en fonction des matériaux et du processus.
Moteur de devis instantanés
Recevez en quelques secondes plusieurs devis grâce à notre moteur de devis instantané.
Focus sur les matériaux composites pour l'impression 3D
Certains fabricants d'imprimantes 3D ont tendance à développer leurs propres matériaux composites, avec une marque spécifique.
L'alumide est un mélange de polyamide et d'une très faible quantité de poudre d'aluminium grise. Le frittage laser est la technique utilisée pour créer des modèles complexes, conceptuels, fonctionnels ou en série, qui sont solides et relativement rigides. Les modèles fabriqués en alumide peuvent également absorber de petits impacts et résister à une certaine pression dans des conditions de flexion. C'est un matériau idéal pour les concepteurs débutants qui recherchent un prix abordable, une liberté de conception maximale et de plus grandes capacités d'impression. En outre, il offre une plus grande rigidité que le polyamide seul et présente un aspect aluminium. La surface est légèrement poreuse avec un aspect sableux et granuleux et peut être finie dans son état mat gris naturel ou teintée avec un assortiment de couleurs.
Le nylon renforcé en fibres permet d'imprimer en 3D des pièces d'ingénierie aussi solides que l'aluminium au prix du plastique. Il est spécifiquement conçu avec la résistance de l'aluminium et possède un rapport résistance/poids plus élevé que l'aluminium 6061-T6, tout en étant jusqu'à 27 fois plus rigide, et 24 fois plus résistant que l'ABS. Le nylon renforcé de fibres permet aux utilisateurs d'optimiser leurs pièces de production imprimées et personnalisées, en particulier les prototypes et les tests fonctionnels, les pièces structurelles, les gabarits, les montages et l'outillage, tout en se concentrant sur la résistance, la rigidité, le poids et la résistance à la température. Il ne convient pas pour les petites pièces au design complexe.
Le grès polychrome produit des modèles et des sculptures photoréalistes en couleur et convient particulièrement bien aux modèles architecturaux, aux sculptures réalistes, aux cadeaux et aux souvenirs, ainsi qu'aux beaux-arts. Essentiellement, il est fabriqué à partir de gypse et incorpore une texture colorée à la surface. La fragilité du matériau limite son application en tant que pièces fonctionnelles ou pièces au design complexe. Ce matériau en grès est parfois appelé multicolore.
FAQ Fabrication composite
Les procédés de fabrication utilisés pour créer des fibres de verre et de carbone sont essentiels pour comprendre la fabrication moderne des composites.
La fibre de carbone est fabriquée à partir de polymères organiques d'une largeur de 5 à 10 microns (environ 0,005 mm à 0,1 mm). Les ingrédients exacts des fibres dépendent généralement du fabricant et de la marque, mais la plupart contiennent des polymères organiques.
1. Les matières premières sont filées et étirées en longues chaînes fibreuses de molécules maintenues ensemble par des atomes de carbone.
2. Ces brins sont lavés et stabilisés à l'aide de produits chimiques.
3. Les fibres sont chauffées à environ 300 degrés, ce qui oblige les molécules de carbone à se lier étroitement entre elles. Ce processus, appelé carbonisation, concentre et purifie le carbone et fournit un rapport résistance/volume élevé.
4. La surface des fibres est traitée pour les oxyder et améliorer les propriétés de liaison.
5. Les fibres de carbone sont ensuite enroulées sur des bobines et chargées dans des machines à filer pour tordre les fibres en fils de différentes épaisseurs et les tisser en tissu. Les feuilles ou les bandes de ce tissu sont généralement imprégnées de résine et laissées à durcir. Ou bien, les fibres libres sont pressées ensemble avec un polymère plastique par la chaleur, la pression ou le vide pour former un matériau composite.
La fibre de verre est fabriquée à partir de sable de silice avec d'autres ingrédients tels que le calcaire et le carbonate de soude pour réduire la température de fusion et contrôler d'autres propriétés.
1. Les matières premières sont fondues dans un four à température contrôlée.
2. Le mélange fondu qui en résulte descend dans un canal jusqu'à une machine qui le transforme en petites billes.
3. Ces billes sont inspectées pour vérifier l'absence d'impuretés avant d'être à nouveau fondues.
4. Le verre fondu passe ensuite dans des filières métalliques couvertes de minuscules orifices.
5. La force centrifuge pousse le verre fondu hors des orifices sous forme de fins filaments. Ces filaments peuvent être conservés tels quels ou tissés en un long fil continu.
Diverses techniques sont utilisées dans la fabrication des composites et la méthode employée reflète l'application prévue. D'autres facteurs décisifs sont le coût des matériaux et de l'équipement et le nombre d'articles à produire.
Les propriétés de l'article fini seront déterminées par les propriétés des matériaux constitutifs et par la façon dont la matrice et le renfort sont combinés.
Les procédés courants de fabrication des composites sont les suivants
- Moulage par stratification manuelle - Le matériau de renforcement est déposé dans un moule et la substance de la matrice est appliquée au pinceau, au rouleau ou au pistolet. Le moule peut être laissé ouvert ou fermé et on le laisse durcir. Ce procédé manuel est relativement peu coûteux et est largement utilisé pour la production de petits volumes sur mesure.
- Moulage par transfert de résine (RTM) - Des feuilles de matériau de renforcement sont placées dans un moule qui est ensuite fermé dans une presse chauffée. La matrice liquide est prémélangée avec un catalyseur de durcissement et injectée sous pression dans le moule par de petits canaux, puis on la laisse durcir. Un vide est parfois utilisé pour améliorer l'écoulement de la matrice (moulage par transfert de résine assisté par le vide). Ce procédé est bien adapté à la production de volumes moyens et nécessite un équipement spécialisé.
- Moulage par injection de réaction - Une résine et un catalyseur de durcissement sont pulvérisés dans un moule par deux jets. Ce procédé peut également être appliqué par des robots programmables qui pulvérisent le mélange directement sur des feuilles de matériaux de renforcement préformées disposées dans un moule. Les systèmes automatisés contribuent à rendre ce processus plus efficace et plus précis.
- Infusion de film de résine (RFI) - Un film de résine gélifiée est superposé à des feuilles de matériaux de renforcement préformés. La chaleur et la pression sont appliquées, la résine se liquéfie et lie le composite.
- Moulage par injection - Un mélange prémélangé de fibres de verre hachées et de résine, appelé "bulk molding compound" (BMC), est introduit de force dans un moule chauffé. Il se liquéfie et remplit le moule, puis il est refroidi et une fois durci, la pièce est éjectée. Ce procédé peut être utilisé pour la production de gros volumes.
- Moulage par compression - Les feuilles de résine et les fibres coupées sont serrées ensemble sous pression. Une fois bien combinées, elles sont chauffées à nouveau et une matrice métallique est appliquée sous pression. Le composite en fibre de verre prend la forme de la matrice, durcit et est éjecté. Plusieurs pièces peuvent être fabriquées à partir de chaque feuille et, avec l'équipement adéquat, l'ensemble du processus peut être automatisé, ce qui le rend idéal pour la fabrication en grande série.
- Pultrusion - Un matelas continu de fibres de renforcement est tiré à travers un bain de résine chauffé et guidé à travers une filière chauffée qui applique la forme requise. Le composite est ensuite refroidi, durci et la longue feuille est découpée en pièces individuelles.
- Extrusion - Les préparations de fibres longues de verre ou de carbone peuvent être prémélangées avec un thermoplastique spécialisé et forcées à travers une filière sous pression. Cela forme une forme continue qui peut être durcie et coupée en longueurs. L'extrusion est plus couramment utilisée pour fabriquer du plastique mais a récemment été développée pour être utilisée avec des matériaux composites.
1. Rapport résistance/poids - Les composites présentent généralement un rapport résistance/poids nettement supérieur à celui des matériaux traditionnels tels que le bois, le métal et le plastique.
2. Flexibilité de la conception - Les composites peuvent être formés en formes et géométries complexes aussi facilement que les formes simples, souvent en une seule pièce, et peuvent être finis de différentes manières.
3. Possibilités de fabrication - Les composites existent dans une grande variété de tailles et d'épaisseurs et sont généralement faciles à travailler. Ils peuvent être formés à proximité de la forme finale de l'objet et nécessitent donc un minimum de formage ou de finition par rapport à un matériau comme le métal.
4. Polyvalence - Il existe de nombreux matériaux composites différents, chacun ayant ses propres propriétés et caractéristiques. De plus, des changements relativement mineurs dans les matières premières utilisées ou dans le processus de fabrication peuvent modifier le comportement du composite et ses applications potentielles.
5. Isolants - De nombreux composites ne conduisent ni la chaleur ni le froid, ce qui les rend idéaux pour la protection contre le feu et les explosions et pour les applications en dessous de zéro.
6. Durabilité - La plupart des composites sont résistants à l'eau, aux produits chimiques et à d'autres formes de corrosion, ce qui les rend idéaux pour une utilisation en extérieur ou dans des environnements difficiles.
7. Isotropique - Les composites n'ont pas de grain et ne se fendront donc pas, contrairement au bois.
1. Coût - Les matières premières, le processus de fabrication et les outils nécessaires à l'utilisation des composites peuvent être coûteux.
2. Fragilité - Les composites peuvent être plus fragiles que les autres matériaux et donc plus facilement endommagés.
3. Réparabilité - Il est possible de réparer les composites, mais cela peut compromettre l'intégrité structurelle, prendre du temps et coûter cher, et nécessiter un équipement spécialisé.
4. Recyclabilité - Les composites sont généralement difficiles à recycler en raison de leur structure et de la façon dont la matrice et le renfort sont mélangés.
5. Inspection - La résistance des matériaux composites rend l'identification de tout dommage structurel plus difficile, car les défauts et les faiblesses peuvent se trouver sous la surface ou sembler identiques à d'autres zones.
Découvrez nos autres matériaux
Métal
Aluminium, Nickel, Inox, Acier, Titane, etc...
Plastique
ABS, POM(Acetal/Deltin), PEEK, PTFE, HDPE, PEI, PC, PP, etc...
Cire
Support de cire, UV Curvable, etc...
Sable
Obtenez plusieurs devis pour vos projets en quelques secondes