Fraisage CNC : Recommandations pour la finition et la conception
Vous planifiez votre prochain projet de production de pièces ? Assurez-vous de connaître les recommandations à prendre en compte en matière de finition et de conception pour le fraisage CNC.
Introduction aux recommandations en matière de finition et de conception pour le fraisage CNC
Le fraisage CNC est un processus d'usinage qui enlève de la matière à partir d'un matériau brut pour réaliser la conception finale prévue. Le fraisage CNC utilise des fraises rondes qui enlèvent la matière latéralement. Dans le fraisage CNC à 3 axes, la pièce est maintenue en place pendant que l'outil tourne et se déplace de haut en bas tout en enlevant de la matière. De plus, le support de la fraiseuse CNC à 3 axes se déplace ensuite d'avant en arrière et d'un côté à l'autre.
Le fraisage CNC étant une forme de fabrication soustractive, des marques d'outil seront visibles sur votre pièce lorsqu'elle sortira de la machine. La bonne nouvelle, c'est qu'il est possible d'utiliser plusieurs méthodes de finition différentes pour améliorer le lissage, la résistance à l'usure et à la corrosion et l'esthétique des pièces fraisées par CNC.
Dans cet article, nous examinons de plus près plusieurs recommandations clés en matière de conception pour le fraisage CNC, ainsi que les options de finition pour le fraisage CNC les plus courantes que vous devez connaître lorsque vous commencez à planifier votre prochain projet de production de pièces.
Recommandations pour la conception 3D pour le fraisage CNC
Assurez-vous que les caractéristiques sont compatibles avec les outils de fraisage CNC courants
Lorsque vous commencez à réfléchir à la conception de votre pièce, il est utile de savoir quels sont les outils les plus couramment utilisés pour le fraisage CNC. Idéalement, vous souhaitez concevoir des caractéristiques et des géométries compatibles avec les outils de fraisage standard. Vous pourrez ainsi réduire le délai et le coût globaux. Après tout, le fabricant n'aura pas à dépenser son argent et son temps pour fabriquer ou se procurer des outils de fraisage personnalisés.
Évitez les angles internes aigus
Le fraisage CNC utilise des outils ronds. Par conséquent, les angles internes aigus ne doivent pas figurer dans la conception de vos pièces. En outre, les coins arrondis doivent être plus grands que l'outil de coupe. En fait, le rayon du coin sera la moitié du diamètre de l'outil de coupe. En outre, il est essentiel de garder à l'esprit que les congés sont utilisés lorsqu'une surface inclinée ou ébauchée rejoint une arête vive ou une paroi verticale.
Essayez d'exclure les fentes étroites et profondes de votre conception
Lorsque vous concevez votre pièce, n'oubliez pas que la profondeur finale d'une coupe de fraise ne doit pas être supérieure à 5 fois le diamètre pour l'acier, 10 fois le diamètre pour l'aluminium et 15 fois le diamètre pour les plastiques. En effet, les outils longs peuvent vibrer et devenir instables pendant l'usinage, ce qui crée des finitions de surface avec beaucoup de marques d'outils. Comme alternative, essayez d'augmenter le diamètre de l'outil de coupe (ce qui peut imposer d'augmenter la largeur de l'élément) ou de diminuer la profondeur de l'élément ou de la fente. En outre, si le fabricant peut accéder à l'élément dans deux directions, cela peut réduire la longueur de l'outil. Cependant, cela implique une configuration supplémentaire, ce qui augmente le délai et le coût de votre projet.
Utilisez les plus grands rayons internes possibles
L'une des meilleures façons de réduire le coût de votre projet et d'accélérer votre délai d'exécution est de concevoir votre pièce pour qu'elle soit compatible avec les plus grands rayons internes possibles. En effet, plus la fraise est grande, plus la quantité de matière pouvant être enlevée en une seule opération est importante, ce qui permet de réduire l'outillage et les délais. En règle générale, essayez de vous assurer que vos rayons sont d'au moins 0,8 mm lorsque cela est possible dans la conception de votre pièce. En outre, concevez les congés dans votre pièce pour qu'ils soient un peu plus grands que le rayon de la fraise. Vous créerez ainsi une trajectoire plus douce pour la fraise, ce qui donnera à votre pièce une meilleure finition de surface.
Veillez à une épaisseur de paroi appropriée
Assurez-vous que l'épaisseur de la paroi est supérieure à 0,50 mm pour les matières plastiques et à 0,25 mm pour les métaux. En effet, les parois trop fines sont difficiles à usiner car elles posent des problèmes lorsqu'il s'agit de maintenir les tolérances et la rigidité. De plus, si le fabricant enlève trop de matière, les parois de votre pièce pourraient devenir trop fines, ce qui entraînerait un gauchissement et/ou des tolérances compromises.
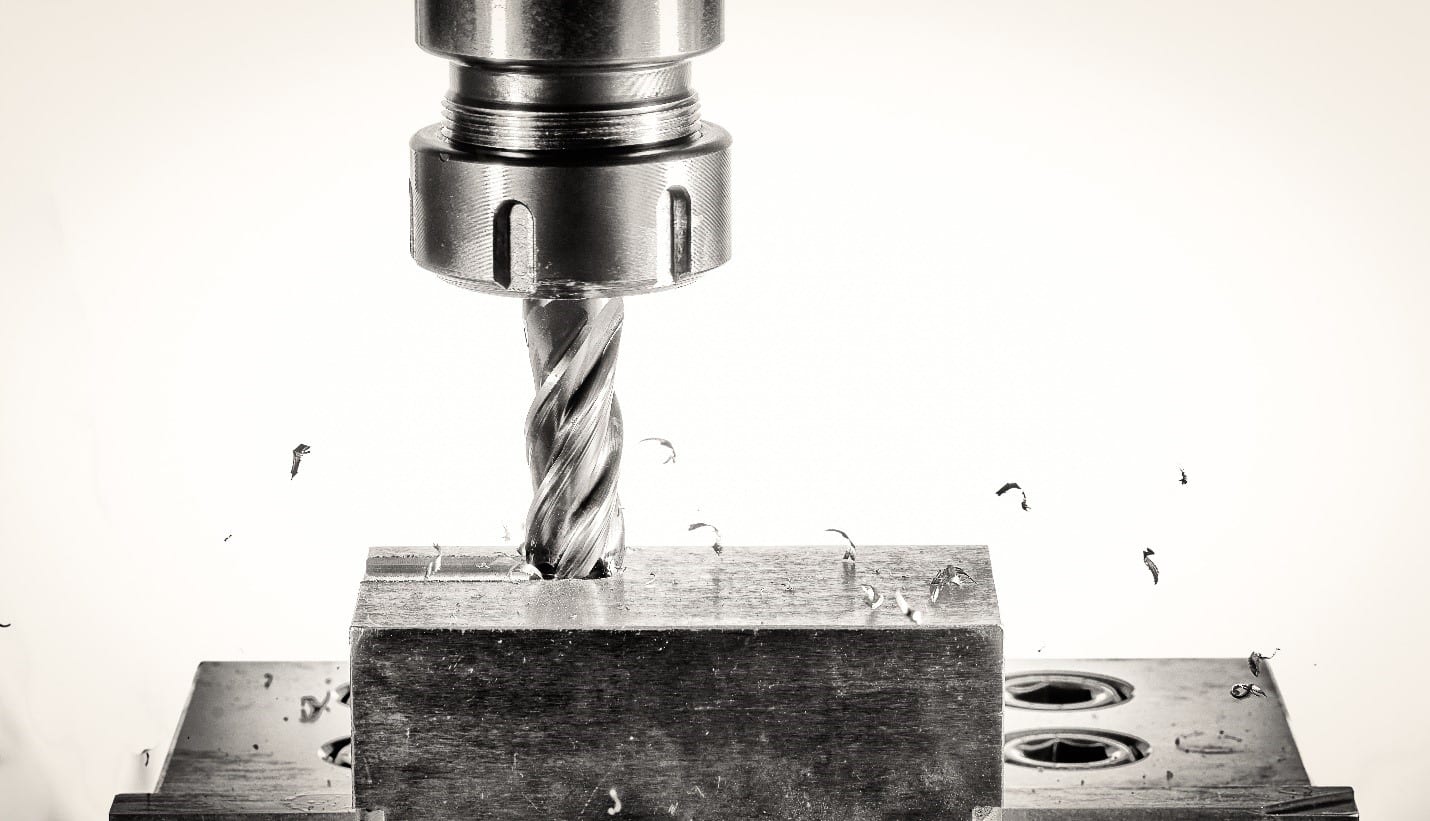
Options de finition pour le fraisage CNC
La simplicité des finitions "telles qu'usinées".
Lorsqu'on utilise le fraisage CNC pour de nombreuses pièces et prototypes, une finition "telle qu'usinée" est plus que suffisante pour leurs besoins. Avec une finition "telle qu'usinée", l'outil de coupe peut effectuer une passe de finition supplémentaire pour réduire la rugosité, ou la pièce peut simplement être acceptée telle quelle, sans passe de finition et avec des marques d'outil visibles. La rugosité de surface standard telle qu'usinée est généralement de 3,2 μm. Si une passe de coupe de finition est effectuée, la rugosité de surface peut diminuer à 1,6, 0,8, voire 0,4 μm. Les passes de finition sur le fraisage CNC augmentent évidemment le coût de production en raison des étapes supplémentaires qu'elles impliquent.
En plus d'effectuer une passe de finition avec l'outil de coupe de fraisage CNC, les pièces telles qu'usinées peuvent être polies et lissées davantage si vous le souhaitez, mais ce faisant, vous enlèverez une partie du matériau de surface, ce qui pourrait affecter les tolérances finales de votre pièce. Néanmoins, les finitions usinées offrent généralement les tolérances les plus étroites de tous les procédés de finition pour le fraisage CNC.
Le microbillage permet d'obtenir une finition encore plus lisse
Certains concepteurs de pièces souhaitent obtenir une finition de surface plus raffinée qu'une finition brute d'usinage. Le microbillage est une option pour ces concepteurs car il permet d'obtenir une finition satinée ou mate et d'éliminer les marques d'outils.
Dans le processus de sablage, de petites billes de verre sont pressées contre la surface de la pièce sous une pression d'air élevée. La force de contact des billes élimine la matière de la surface, ce qui permet d'obtenir une finition plus lisse. Il est essentiel de garder à l'esprit que si votre pièce présente des caractéristiques avec des tolérances critiques telles que des trous, vous pouvez les masquer pendant le sablage afin d'éviter que vos dimensions ne soient modifiées.
Le revêtement par poudre offre une protection supplémentaire
Le revêtement par poudre est une autre option de finition pour les pièces fraisées CNC. Au cours de ce processus de finition, une fine couche de polymère est appliquée sur la pièce pour protéger sa surface. Cette couche de polymère est durable et résistante à la corrosion, ce qui contribue à protéger la pièce contre l'usure. L'un des avantages du revêtement en poudre est qu'il peut s'adapter à tout matériau métallique. En outre, le microbillage peut être utilisé en combinaison avec le revêtement par poudre pour obtenir des finitions de surface lisses.
La méthode utilisée dans le processus de revêtement par poudre ressemble beaucoup à la peinture par pulvérisation, sauf qu'une poudre sèche est pulvérisée au lieu d'une peinture liquide. Pour commencer le processus de revêtement par poudre, la pièce est souvent apprêtée pour améliorer la résistance à la corrosion. Une fois l'apprêt appliqué, un pulvérisateur électrostatique recouvre la pièce de poudre sèche. Enfin, la pièce est durcie dans un four à haute température. Comme pour l'anodisation de type II, le revêtement en poudre peut être nécessaire pour obtenir une variété de couleurs à des fins esthétiques.
Anodisation de type II et de type III pour la protection et l'esthétique
L'anodisation est une autre option de finition des pièces par fraisage CNC. L'anodisation crée une fine couche de surface en céramique qui offre une protection contre l'usure et la corrosion. Le revêtement qui en résulte est très durable, ne conduit pas l'électricité et peut prendre la forme de nombreuses couleurs différentes à des fins esthétiques. Les concepteurs et les ingénieurs doivent savoir que l'anodisation ne peut être effectuée que sur des alliages d'aluminium et de titane.
Dans le processus d'anodisation, la pièce est plongée dans une solution d'acide sulfurique, et une charge électrique passe entre le composant et la cathode. La réaction électrochimique qui en résulte transforme la surface de la pièce en oxyde de titane ou d'aluminium durci. Il est possible de masquer au préalable les zones de votre pièce sensibles aux tolérances ou conductrices d'électricité afin de ne pas compromettre la précision dimensionnelle et que ces zones puissent toujours conduire l'électricité après l'anodisation.
L'anodisation se présente sous deux formes : Type II ou Type III. Voici un aperçu de chaque type :
- L'anodisation de type II - communément appelée anodisation " décorative " - peut produire des revêtements d'une épaisseur allant jusqu'à 25 μm. Cette forme d'anodisation produit des pièces avec une surface lisse de différentes couleurs tout en assurant une bonne résistance à la corrosion.
- L'anodisation de type III - communément appelée anodisation " hard coat " - peut produire des revêtements d'une épaisseur allant jusqu'à 125 μm. Cette forme d'anodisation offre une excellente résistance à l'usure et à la corrosion. Cette durabilité supérieure rend ces revêtements parfaits pour les applications fonctionnelles.
Obtenez plusieurs devis pour vos projets en quelques secondes