Photopolymérization VAT, SLA, DLP, CDLP
Découvrez comment le procédé de Photopolymérization,, un procédé de fabrication impression 3D, aussi appelé VAT, SLA, DLP, CDLP, fonctionne.
Introduction à la Photopolymérization - VAT, SLA, DLP, CDLP
Photopolymérization, c'est quoi ?
La technologie d'impression 3D par photopolymérisation englobe plusieurs procédés qui reposent sur la même stratégie de base : un photopolymère liquide contenu dans une cuve (conteneur) est durci de façon sélective par une source de chaleur. Couche après couche, l'objet physique est créé en trois dimensions.
Il existe plusieurs types d'appareils de durcissement qui s'ajoutent à la technique la plus ancienne, basée sur le laser. Les projecteurs à traitement numérique de la lumière et les écrans LCD sont maintenant largement utilisés dans la photopolymérisation de matériaux en raison de leur faible coût et de leur résolution très élevée. L'un des avantages de ces deux techniques par rapport au laser réside dans leur capacité à durcir en une seule fois toute une couche de résine, alors que le laser doit progressivement illuminer la surface entière en la dessinant.
Les technologies d'impression 3D par photopolymérisation en cuve incluent :
- La stéréolithographie (SLA), également appelée SL, la fabrication optique, la photo-solidification ou l'impression en résine. Pendant le procédé de fabrication SL, un faisceau concentré de lumière ultraviolette ou un rayon laser est projeté sur la surface d'une cuve remplie de photopolymère liquide. Le faisceau ou le laser est focalisé, créant ainsi chaque couche de l'objet 3D souhaité par réticulation ou dégradation du polymère.
- Traitement numérique de la lumière (DLP) Dans le cadre du procédé d'impression 3D DLP, un écran de projection numérique illumine une seule image de chaque couche sur l'ensemble de la plateforme en une seule opération. Le projecteur étant un écran numérique, l'image de chaque couche est composée de pixels carrés. Le résultat est une couche formée de petites briques rectangulaires appelées voxels. Le procédé DLP permet d'obtenir des temps d'impression plus rapides pour certaines pièces, car chaque couche est exposée en une seule fois au lieu d'être dessinée au laser.
- Continuous Liquid Interface Production (CLIP) par Carbon La technique de photopolymérisation en cuve appelée production par interface de liquide continu (ou CLIP) utilise un conteneur de résine comme matériau de base. La partie du fond de la cuve qui laisse passer la lumière ultraviolette est appelée la fenêtre. Un faisceau ultraviolet traverse la fenêtre et illumine une section transverse précise de l'objet. La lumière entraîne la solidification (photopolymérisation) de la résine. L'objet s'élève suffisamment lentement pour permettre à la résine de s'écouler en dessous et de rester en contact avec le bas de l'objet. Une membrane perméable à l'oxygène repose sous la résine et crée une zone morte. Cette interface de liquide continu empêche la résine d'attacher à la fenêtre, ce qui signifie que la photopolymérisation est inhibée entre la fenêtre et le polymère. Contrairement au procédé SLA standard, l'impression 3D est continue et potentiellement jusqu'à 100 fois plus rapide qu'avec les méthodes d'impression 3D traditionnelles.
- Daylight Polymer Printing (DPP) par Photocentric Au lieu d'utiliser un laser ou un projecteur pour durcir le polymère, le procédé de fabrication par impression de polymère en lumière du jour (ou DPP) utilise un écran à cristaux liquides (LCD). Cette technique, également appelée impression 3D LCD, utilise des écrans LCD non modifiés et un polymère à lumière naturelle spécialement formulé. La société Photocentric a mis au point cette technique en développant l'une des résines les plus sensibles à la lumière.
Deux différents procédés de Photopolymérization
Il existe deux approches différentes dans la catégorie d'impression 3D par photopolymérisation. Toutes deux reposent sur la fabrication de pièce au niveau de l'interface entre la dernière couche et la surface du conteneur de résine. L'approche descendante consiste à placer la source de chaleur sous la cuve. La plateforme d'impression 3D est alors progressivement élevée et la pièce finale est produite de bas en haut. La seconde technique est appelée approche ascendante et consiste à placer la source de chaleur au-dessus de la cuve. Ainsi, la plateforme d'impression 3D est progressivement plongée dans la cuve.
Découverte par des chercheurs japonais et français au début des années 1980, cette invention a été industrialisée et brevetée pour la première fois en 1984 par Chuck Hull, le co-fondateur de la société 3D Systems Inc.
La photopolymérisation convient particulièrement à la modélisation dans le domaine médical et permet de créer des modèles 3D précis de différentes parties anatomiques d'un patient en fonction des données issues de scans sur ordinateur. Du fait de sa haute résolution, cette technique est également idéale pour tous les types de prototypages ainsi que la production de masse. Les procédés de polymérisation en cuve sont parfaits pour produire des pièces aux détails fins et obtenir une surface finie lisse. Cette technologie est idéale pour les secteurs de la bijouterie, de la microfusion et diverses applications dentaires et médicales. Le développement des matériaux a également permis d'imprimer des moules à injection en petites séries. Les principales limites de la polymérisation en cuve sont la taille de l'impression et la résistance de la pièce.
Les résines photopolymères sont disponibles en plusieurs couleurs et présentent différentes propriétés physiques, chacune correspondant à un usage spécifique. La gamme de résines inclut les résines haute résistance, les résines à faible résidu (pour la microfusion), les résines transparentes et les résines en polyuréthane souple.
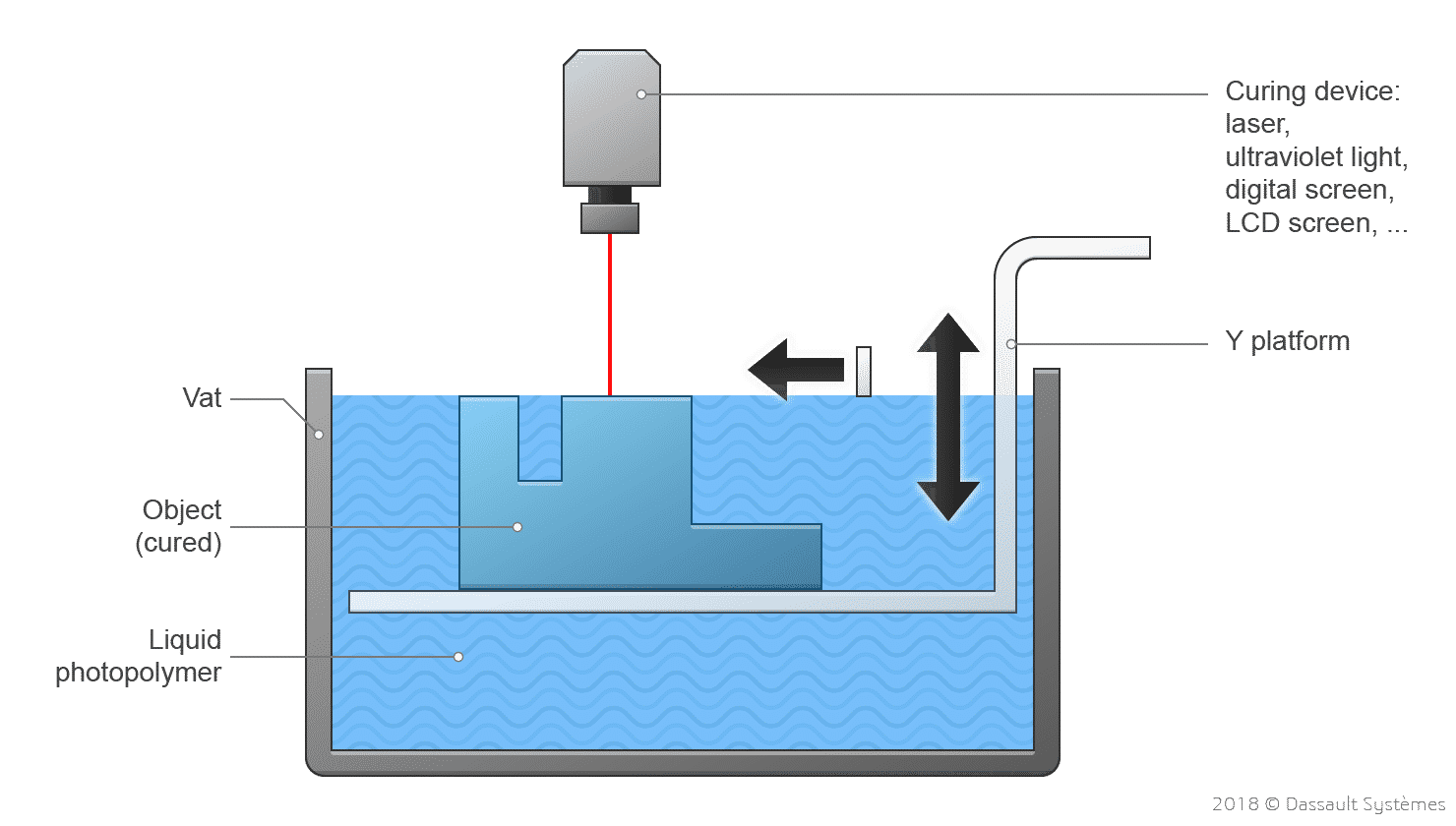
Découvrez comment la Photopolymérization fonctionne avec Sculpteo
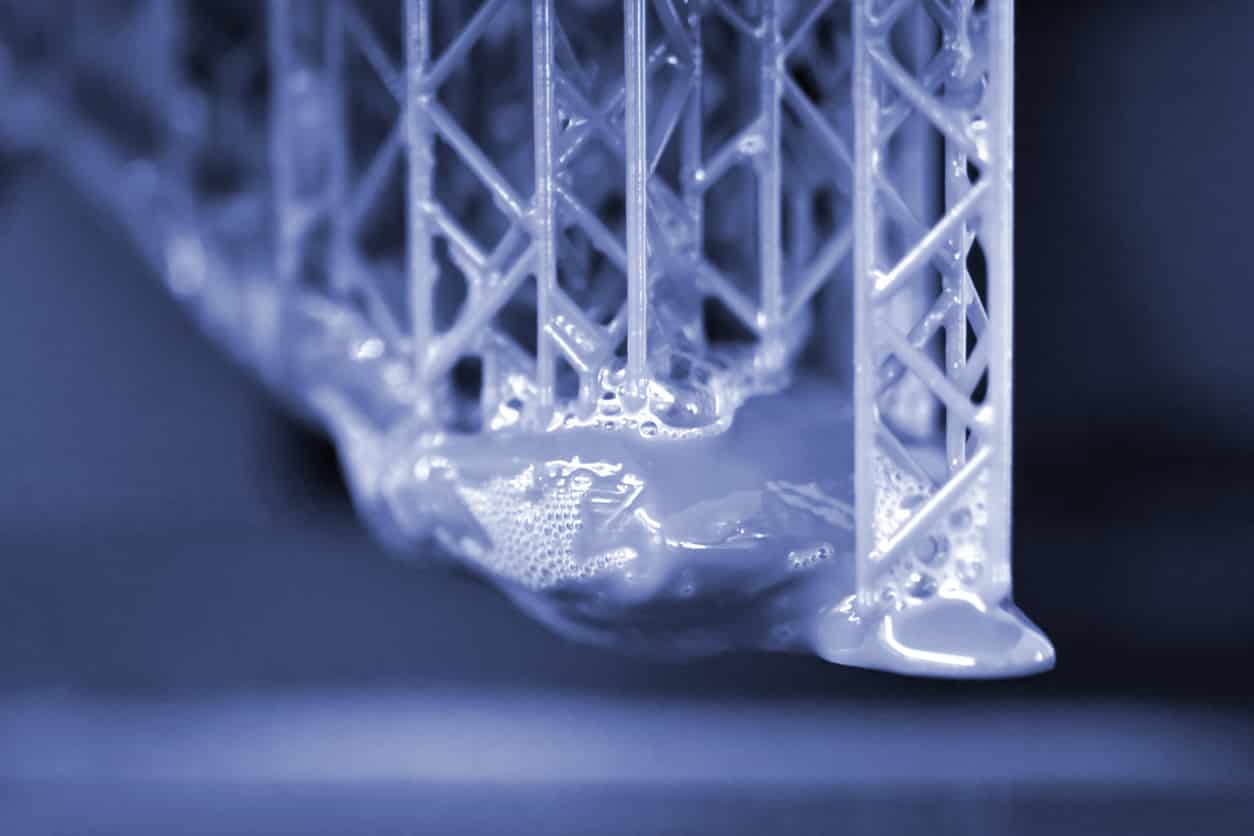
Obtenez plusieurs devis pour vos projets en quelques secondes