Extrusion de matière
Découvrez ce qu'est le procédé de fabrication de formage Extrusion de matière et ses usages dans l'industrie.
Introduction à l'Extrusion de matière
Le processus d’extrusion crée des objets avec des profils de section transverse fixes en poussant un matériau, généralement des métaux, des polymères, de la céramique, du béton, de l’argile à modeler ou des denrées alimentaires, à travers une matrice de la section transverse souhaitée. Cela est utile pour créer des sections transverses extrêmement complexes et avec des matériaux fragiles, car ces derniers sont uniquement exposés à des contraintes de compression et de cisaillement. L’un des principaux avantages de ce processus est l’excellente finition de surface. Un autre est la résistance accrue des objets métalliques créés par extrusion.
Il existe deux types d’extrusion : continue ou semi-continue. L’extrusion continue implique la production d’un matériau indéfiniment long, tandis que l’extrusion semi-continue implique la production de nombreuses pièces. Le matériau peut être chaud ou froid. Les objets produits par extrusion sont appelés extrudats.
Le premier processus d’extrusion pour la création de tuyaux à partir de métaux mous a été breveté en 1797 par l’inventeur anglais Joseph Bramah. Le métal était préchauffé et forcé à travers une matrice à l’aide d’un piston opéré manuellement. Plus tard, en 1820, Thomas Burr a transposé cette méthode avec un tuyau en plomb et une presse hydraulique, dans un processus appelé « soufflage ». En 1894, Alexander Dick a développé davantage encore le processus d’extrusion pour l’appliquer aux alliages de cuivre et de laiton.
Le processus d’extrusion présente toutefois certains inconvénients. Ceux-ci incluent la fissuration interne et superficielle, des lignes de surface et un réseau d’écoulement qui déposent des oxydes sur la surface et des impuretés vers le centre d’un produit.
Cinq procédés d'extrusion de matière
Les cinq différents processus d’extrusion sont les suivants :
- L’extrusion à chaud s’effectue au-dessus de la température de recristallisation d’un matériau afin d’empêcher l’écrouissage du matériau et de pouvoir le pousser plus facilement à travers la matrice.
- L’extrusion à mi-chaud est réalisée au-dessus de la température ambiante, mais en dessous de la température de recristallisation du matériau. La température peut aller de 424 °C à 975 °C (800 °F à 1 800 °F). On emploie généralement cette technique pour obtenir le bon équilibre entre les forces, la ductilité et les propriétés d’extrusion finales requises.
- L’extrusion à froid est réalisée à température ambiante ou presque. Absence d’oxydation, résistance accrue en raison du travail à froid, tolérances plus étroites, meilleure finition de surface et vitesses d’extrusion rapides si le matériau est soumis à la fragilité à chaud sont les principaux avantages de l’extrusion à froid.
- The Welding Institute, au Royaume-Uni, a inventé l’extrusion par friction et l’a brevetée en 1991. Elle était au départ principalement conçue comme une méthode de production de microstructures et de distributions des particules homogènes dans des matériaux composites à matrice métallique. L’extrusion par friction diffère de l’extrusion traditionnelle en ce que la charge (billette ou autre précurseur) pivote par rapport à la filière. Une force d’extrusion est appliquée afin de pousser la charge contre la filière. En pratique, la filière ou la charge peut pivoter, ou elles peuvent être contre-rotatives.
- La micro-extrusion est un processus d’extrusion par microformage réalisé dans le domaine du submillimètre. Tout comme lors de l’extrusion traditionnelle, le métal est poussé dans la filière, mais la section transverse du produit résultant tient dans un carré de 1 mm.
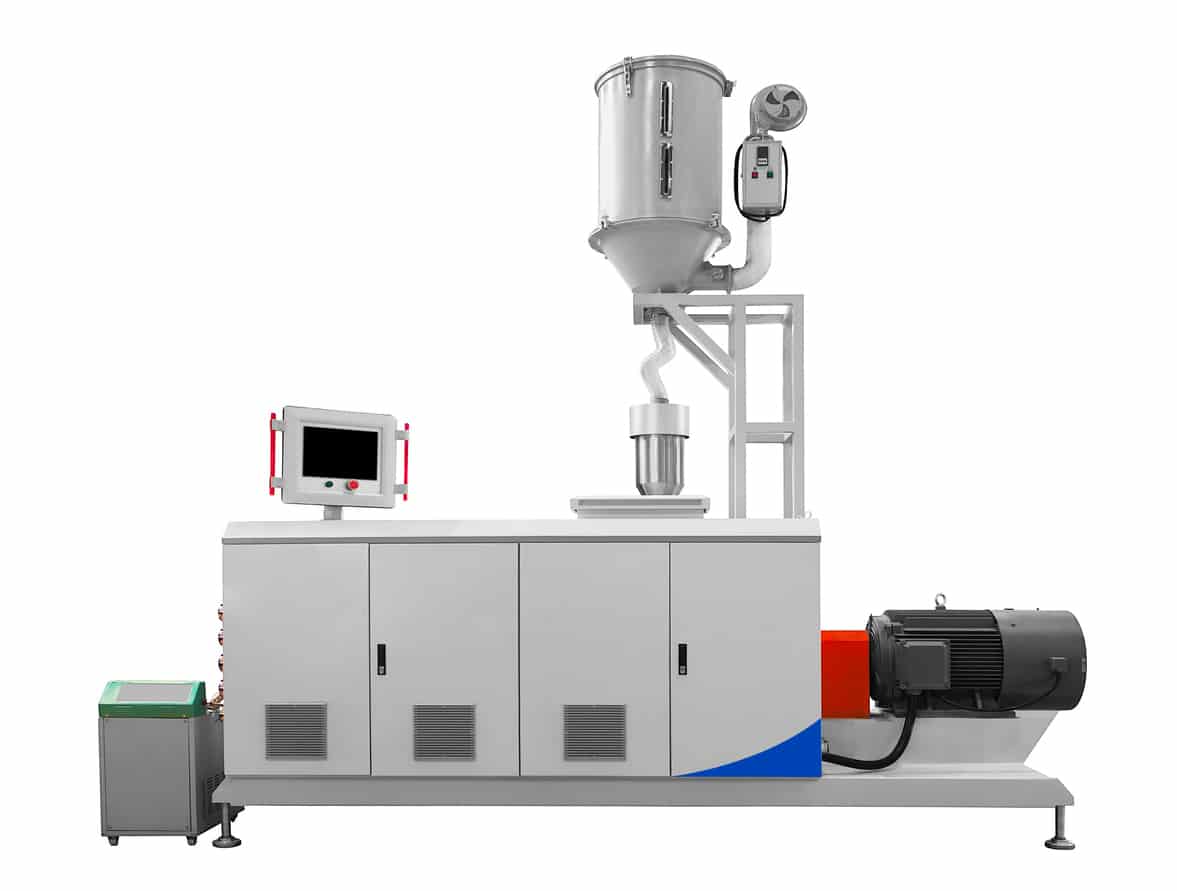
Obtenez plusieurs devis pour vos projets en quelques secondes