Découpe
Découvrez ce qu'est le procédé de fabrication découpe, comment cela fonctionne et ses usages dans l'industrie.
Quelle est l’histoire des machines de découpe CNC ?
Que signifie découper aujourd’hui ?
Tout outil pointu est capable de couper s’il possède une dureté supérieure à celle de l’objet sur lequel il veut s’exercer, et s’il est appliqué avec une force suffisante.
Même les liquides peuvent ainsi opérer, à condition de s’y employer avec la puissance nécessaire. C’est le cas de la machine de découpe au jet d’eau dans l’usinage CNC (Computer Numerical Control).
Les premiers types de découpes au jet d’eau ont adapté les dispositifs traditionnels, tels que les pantographes mécaniques et les systèmes CNC, basés sur la fraiseuse CN de John Parsons de 1952. Les défis inhérents à cette technologie ont révélé les insuffisances du G-code. Le Dr John Olsen, de la société OMAX Corporation, a développé des méthodes permettant de positionner précisément la buse du jet d’eau tout en spécifiant avec finesse la vitesse à chaque point du parcours. Il s’est servi de PC courants comme contrôleur.
La découpe demeure au cœur de la fabrication tout au long de l’histoire. De nombreuses méthodes exploitent les métaux. L’idée est de produire une pièce en éliminant la matière indésirable d’un bloc de métal, sous forme de copeaux. Les méthodes peuvent s’apparenter à du fraisage ou du perçage, du poinçonnage, du polissage, de la découpe au laser ou encore de l’usinage par électroérosion (EDM), etc.
Chaque technique a ses limites en matière de précision, de coût et d’effet sur le matériel. Par exemple, la chaleur peut endommager la qualité des alliages traités thermiquement, et la découpe au laser est moins adaptée aux matériaux très réfléchissants comme l’aluminium.
Quelle est l’histoire du travail et de la découpe des métaux ?
L’usinage d’aujourd’hui comprend un certain nombre de machines-outils capables de créer une pièce précise et utile à partir des métaux.
La plus ancienne preuve archéologique de l’extraction et du travail du cuivre demeure la découverte d’un pendentif dans le nord de l’Irak datant de 8 700 avant J.-C. Le matériau était martelé jusqu’à ce qu’il devienne cassant, puis chauffé pour être façonné davantage. Cette technologie est apparue vers 4000-5000 avant J.-C.
Plus tard, le lien entre la chaleur et la libération des métaux de la roche est devenu évident, et les roches riches en cuivre, en étain et en plomb ont fait face à une plus grande demande. L’extraction de minerais se développait partout où ils étaient reconnus. Les civilisations anciennes connaissaient sept métaux : le fer, l’étain, le plomb, le cuivre, le mercure, l’argent et l’or.
En dehors de l’Asie du Sud-Ouest, on a découvert et employé ces mêmes progrès et matériaux. La Chine et la Grande-Bretagne se sont lancées dans l’utilisation du bronze, plutôt que du cuivre, laissé de côté. Le Japon a commencé à exploiter le bronze et le fer presque simultanément.
Avec les périodes historiques des pharaons en Égypte, des rois védiques en Inde, des tribus d’Israël et de la civilisation maya en Amérique du Nord, entre autres populations anciennes, les métaux précieux ont commencé à avoir de la valeur. À ces époques, les métallurgistes étaient très habiles pour créer des objets d’ornement, des artefacts religieux et des instruments commerciaux en métaux précieux (non ferreux), ainsi que des armes généralement en métaux ferreux et/ou en alliages.
Au fil du temps, les objets en métal sont devenus plus courants et de plus en plus complexes. La nécessité de les acquérir et de les travailler davantage a pris de l’importance. La disponibilité des métaux et des métallurgistes a fortement influencé le destin et l’économie de civilisations entières.
Le métallurgiste dépend de l’extraction de métaux précieux pour fabriquer des bijoux, construire des appareils électroniques plus efficaces, et pour des applications industrielles et technologiques allant de la construction aux conteneurs d’expédition, en passant par le transport ferroviaire et aérien. Sans les métaux, les biens et les services cesseraient de circuler dans le monde à l’échelle que nous connaissons aujourd’hui.
Le travail des métaux est généralement divisé en trois catégories : le formage, la découpe et l’assemblage. La plupart des découpes sont réalisées à l’aide d’outils en acier rapide ou en carbure.
Comment découpe-t-on les métaux aujourd’hui ?
La découpe représente un ensemble de procédés dans lesquels le matériau est amené à une géométrie spécifiée en enlevant l’excès de matériau. Cette opération s’effectue à l’aide de divers types d’outils qui laissent une pièce finie, répondant aux caractéristiques demandées. Deux produits constituent le résultat net de la découpe : le déchet ou l’excédent de matériau, et la pièce finie. Dans le travail du bois, les déchets sont la sciure et l’excédent de bois. Dans la découpe des métaux, les déchets sont des copeaux et des excédents de métal.
Les processus de découpe entrent dans l’une des trois grandes catégories suivantes :
- les procédés de production de copeaux, plus connus sous le nom d’usinage. Par exemple, le perçage d’un trou dans une pièce métallique,
- le brûlage, l’ensemble d’opérations par lesquelles le matériau est coupé en oxydant une entaille pour séparer les morceaux de métal. Par exemple, l’utilisation d’un chalumeau oxycoupeur pour diviser une plaque d’acier en plus petits morceaux,
- le processus de spécialisation divers, ne relevant pas facilement de l’une des catégories ci-dessus. Par exemple, le fraisage chimique qui élimine l’excès de matière par l’emploi de produits chimiques de gravure et de masquage.
Il existe de nombreuses technologies pour couper le métal, notamment :
- les technologies manuelles : scie, ciseau, cisaille ou cisaille à métaux,
- les technologies des machines : tournage, fraisage, perçage, rectification, sciage,
- les technologies de soudage/combustion : combustion par laser, oxycombustion et plasma,
- les technologies d’érosion : par jet d’eau, par décharge électrique ou par usinage à flux abrasif,
- Les technologies chimiques : usinage photochimique.
On utilise un liquide de refroidissement lorsqu’il y a une friction et une chaleur importantes à l’interface de coupe entre l’outil, tel qu’un foret ou une fraise, et la pièce à usiner. L’idée est d’éviter une usure excessive de l’outil.
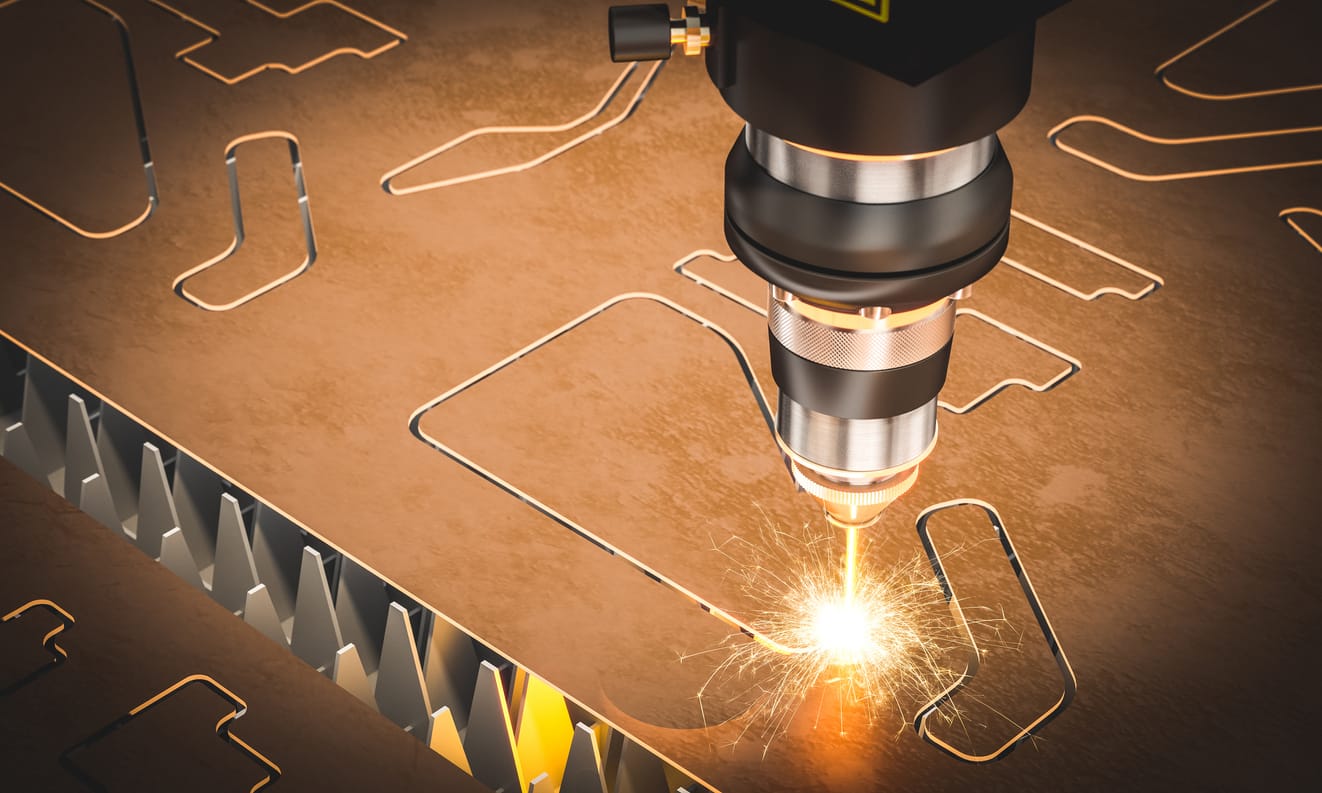
Qu’est-ce que le procédé de découpe ?
L’opération de découpe est souvent associée à l’usinage du métal ; cependant, la découpe du bois ou de tout autre matériau peut également être attribuée à ce processus. En 2016, le marché mondial des machines de découpe CNC des métaux était estimé à 5,99 milliards de dollars. D’ici 2025, il devrait atteindre 10,53 milliards de dollars, avec une croissance du marché de 6,5 %.
Quelles sont les méthodes de découpe ?
La découpe relève d’un ensemble d’opérations au cours desquelles le matériau est amené à une géométrie spécifiée. Différents types d’outils permettent d’enlever l’excès de matière et obtenir un produit fini. De diverses techniques peuvent couper le métal, comme des technologies manuelles (scie), de machines (fraisage, perçage), de soudage (laser), d’érosion (jet d’eau) ou encore chimiques.
- Le fraisage se réalise à l’aide d’une machine-outil dont la fraise tourne autour de l’axe de la broche (comme une perceuse), et d’une table de travail qui peut se déplacer dans plusieurs directions. Les fraiseuses peuvent effectuer un grand nombre d’opérations complexes, telles que la découpe de fentes, le rabotage, le perçage et le filetage, le rainurage, le détourage, etc.
- Le tournage : la pièce est mise en rotation sur une broche et l’outil de coupe y est introduit radialement, axialement ou les deux. Parmi les objets qui peuvent être produits sur un tour, on peut citer les porte-bougies, les vilebrequins, les arbres à cames et les supports de palier.
- Le filetage consiste à créer un filet de vis. On l’utilise lorsqu’il faut une profondeur de filet complète par exemple, quand l’ébauche n’est pas très précise, ou encore le matériau fragile.
- Le meulage recourt à un procédé abrasif, en se servant d’une rectifieuse comme outil. Celle-ci produit des finitions très fines, réalise des coupes très légères, ou des formes de haute précision qui se prêtent bien aux applications aérospatiales entre autres.
- Le limage s’opère principalement pour les opérations de finition, à savoir dans les opérations d’ébavurage.
Il existe également d’autres méthodes de découpe telles que l’usinage par faisceau d’électrons dans lequel des électrons à haute vitesse sont dirigés vers une pièce, créant de la chaleur et vaporisant le matériau, ou encore l’usinage par ultrasons qui a recours à des vibrations ultrasoniques pour fabriquer des matériaux très durs ou fragiles.
Les différents types de découpes CNC
1. La découpe à la lame
Une scie est un outil composé d’une lame, d’un fil ou d’une chaîne résistante avec un bord denté dur. La plupart des dents des lames sont en acier à outils ou en carbure. Le carbure est plus dur et tient un tranchant beaucoup plus longtemps. La scie est couramment employée pour couper des matériaux durs, particulièrement du bois, mais parfois aussi du métal ou de la pierre. Une scie abrasive est dotée d’une lame circulaire motorisée conçue pour séparer le métal ou la céramique.
2. La découpe au laser
La découpe au laser s’applique pour préparer les pièces, y compris les trous de perçage pour le processus de rivetage. Cette méthode permet d’assembler des pièces à l’aide de rivets, qui offrent une fixation permanente. La soudure au laser est employée comme technique d’assemblage final pour obtenir la résistance et l’endurance qui sont essentielles pour les véhicules ferroviaires, par exemple.
Cette technologie manie un laser pour trancher des matériaux. Le procédé consiste à diriger la sortie d’un laser de forte puissance, le plus souvent par l’intermédiaire d’une optique. Le faisceau laser est dirigé sur le matériau, qui fond, brûle et se vaporise. Un jet de gaz peut aussi le souffler, laissant une arête avec un état de surface de haute qualité.
Le marché mondial des machines de découpe laser était évalué à 3 milliards de dollars en 2015 et devrait atteindre 5,7 milliards de dollars en 2022.
3. La découpe à l’eau
Un découpeur à jet d’eau peut découper une grande variété de matériaux en utilisant un jet d’eau à très haute pression, ou un mélange d’eau et d’une substance abrasive. Le terme de jet abrasif fait spécifiquement référence à l’utilisation d’un mélange d’eau et d’abrasif pour couper des matériaux durs tels que le métal ou le granit, au contraire, d’une découpe au jet d’eau pur ou au jet d’eau uniquement. Ces techniques s’utilisent pour des matières plus molles telles que le bois ou le caoutchouc.
La fabrication de pièces de machines exploite particulièrement la découpe au jet d’eau. Cette méthode est idéale lorsque les matériaux à découper sont sensibles aux températures élevées. Ce procédé est employé dans diverses industries, notamment minières et aérospatiales.
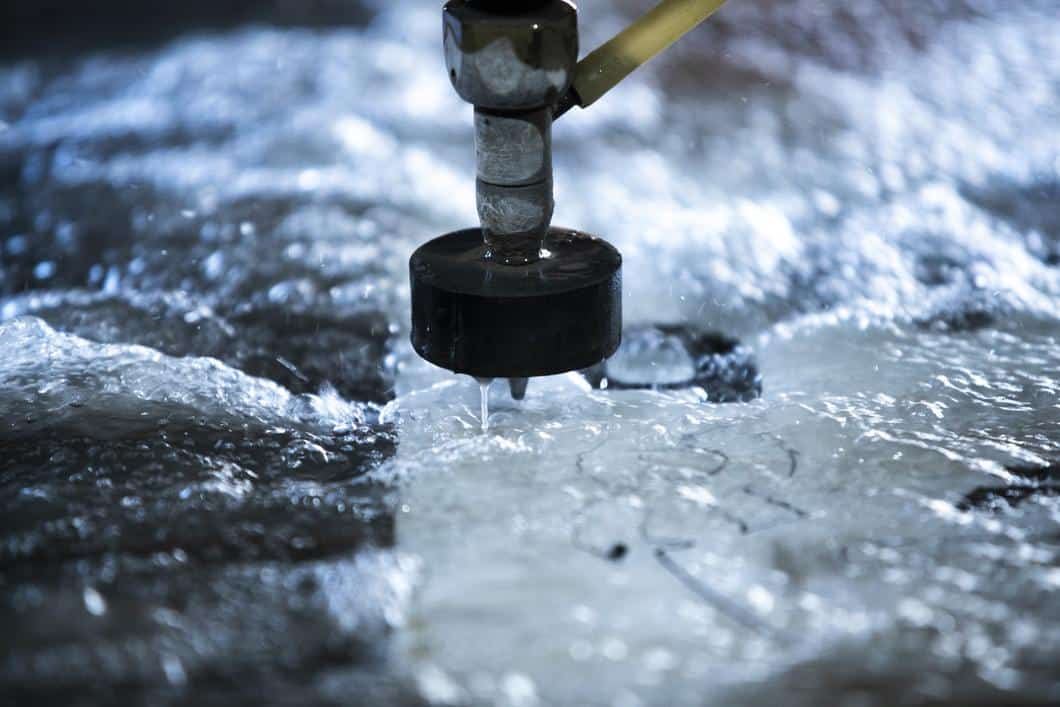
Quel matériau choisir pour la découpe ?
La découpe est une technique qui permet de séparer un objet en minimum deux parties, pour donner suite à l’action d’une force dirigée avec une extrême précision. Dans l’industrie, on retrouve des procédés de découpe par lame, laser ou encore jet d’eau.
Le métal, un matériau optimal pour la découpe
En raison de sa rigidité naturelle et de sa résistance thermique, le métal reste une pièce simple à découper, car elle supporte la déformation. Par métal, on entend aluminium, acier inoxydable, acier doux, acier allié, acier à outils ou laiton.
Le métal peut être découpé selon différents procédés :
- la production de copeaux, plus connue sous le nom d’usinage. Le perçage d’un trou dans une pièce métallique demeure l’exemple le plus courant. Il peut aussi bien s’agir des technologies manuelles (scie, cisaille à métaux) que celles des machines CNC (tournages, fraisage, perçage, rectification, sciage), ou encore électrochimiques comme l’usinage par électroérosion,
- le brûlage au cours duquel l’oxydation sépare les fragments de métal. Par exemple, un chalumeau oxycoupeur qui divise une plaque d’acier en petits morceaux. Il peut s’agir de techniques de soudage ou combustion comme la découpe au laser ou au plasma,
- les processus de spécialisations divers, ne relevant pas de l’une des catégories ci-dessus. C’est le cas du fraisage chimique qui permet d’éliminer l’excès de matière par l’utilisation de produits chimiques de gravure et de masquage, à l’image de méthodes d’érosion, telle que la découpe par jet d’eau.
Chaque méthode a ses limites sur le plan de la précision, de coût et d’effet sur le matériel. Notamment, la chaleur peut endommager la qualité des alliages métalliques traités thermiquement, et la découpe au laser est moins adaptée aux matériaux très réfléchissants comme l’aluminium.
Le plastique, un matériau répandu
Les plastiques restent très présents dans le monde industriel et dans celui des consommateurs, en raison notamment de leur résistance chimique et leurs propriétés d’isolation électrique. Les matières plastiques thermodurcissables sont généralement privilégiées par la découpe, car des fibres la consolident, comme les nylons renforcés de verre, l’acrylique ou le PEEK. Les matériaux moins rigides ont tendance à se déformer et à se courber lorsque la fraise tente de couper la pièce.
Alors que l’industrie du plastique se métamorphose et innove, créant des produits plus intéressants à acheter pour les consommateurs, elle continue d’utiliser certaines des meilleures technologies pour travailler avec ce nouveau matériau, tel que :
- la découpe à l’emporte-pièce, soit manuelle, soit automatisée,
- la découpe à chaud au couteau pour les matières les plus souples. Par exemple, les blocs de mousse et de polystyrène expansé,
- le poinçonnage pour les feuilles thermoplastiques et thermodurcissables les plus fines,
- la découpe au jet d’eau pour des composants thermodurcissables renforcés de fibres, qui seraient difficiles à séparer par d’autres procédés,
- la découpe au laser et le perçage de certains types d’acrylique et d’autres plastiques, mais pas thermodurcissables. L’outil employé, un laser industriel, fait fondre le plastique, qu’un ordinateur contrôle dans la plupart des cas.
- la découpe par ultrasons pour les plastiques les plus fins et plus souples. La haute fréquence, générée par les ultrasons de l’outil, a pour effet de faire fondre localement la matière.
Le composite, le défi d’une découpe précise
Les composites sont constitués de plusieurs matériaux aux propriétés physiques et chimiques différentes qui, associés ensemble, composent un produit plus résistant, plus léger ou plus souple. Il s’agit par exemple du plastique renforcé, de matériaux renforcés à base de fibres de carbone ou de graphite, de fibre de verre ou encore de résine.
Les composites sont découpés grâce notamment à ces technologies :
- la découpe au jet d’eau utilise un jet d’eau hyperbare. La découpe peut être réalisée à l’eau pure, pour les composites séparés au cutter, ou à l’eau chargée d’abrasif, pour toutes les autres pièces,
- la découpe au laser tranche la matière grâce à une grande quantité d’énergie générée par un laser et concentrée sur une très faible surface. Le laser peut être pulsé ou continu (laser CO2 ou azote).
Quelles industries exploitent les procédés de découpe ?
Les industries mondiales automobile, aérospatiale, médicale, de l’énergie et électronique, entre autres, ne peuvent pas se passer d’équipements de découpe, aux avantages nombreux et aux usages variés. Les techniques exploitées offrent aujourd’hui un nouveau niveau de qualité et de fiabilité grâce à des technologies telles que la découpe au laser ou au jet d’eau.
L’industrie aéronautique et spatiale
La découpe au laser s’applique beaucoup dans ce domaine. Cependant, à la différence du secteur automobile, tout doit s’exécuter à une échelle beaucoup plus grande et les produits doivent résister à beaucoup plus de pression. Dans cette optique, les processus impliqués doivent être encore plus précis et fiables.
La découpe au jet d’eau s’emploie également pour concevoir des composants de moteurs à réaction et d’aubes de turbines, ainsi que des matériaux composites pour les avions. En effet, l’eau à haute pression associée à un jet d’eau abrasif réalise des découpes extrêmement précises et nécessaires pour le fuselage, la queue et les ailes des avions ou encore les pales rotatives.
L’industrie automobile
L’industrie automobile a recours à la découpe au jet d’eau pour confectionner des garnitures de toit, des panneaux de portières ou encore de la moquette. Les machines créent des surfaces lisses, planes et ébavurées, même quand les matériaux ne sont pas uniformes, ce qui ne laisse aucune retouche à effectuer.
Les constructeurs automobiles peuvent aussi préférer la découpe laser pour les pièces et les composants très petits et complexes, comme les ouvertures pour les antennes. Cette technologie permet aussi de découper des matériaux comme le tissu pour les airbags. En faisant fondre les bords à très grande vitesse, il ne reste aucun effilochage. Le laser est aussi capable de trancher des composites, utiles pour les pièces intérieures.
L’industrie agroalimentaire
La découpe au jet d’eau présente un grand avantage en matière de temps pour les denrées alimentaires. Il n’est plus nécessaire de changer de couteaux ou d’affûter les lames puisque la découpe s’exécute à l’eau pure. Cette technologie a ainsi permis aux pâtisseries de doubler leur rendement. L’absence de lames favorise un contexte de découpe sanitaire sain, sans risque de contamination. Par ailleurs, la machine-outil est simple d’utilisation, ce qui favorise sa démocratisation. Sa finesse de coupe s’est ainsi généralisée dans le secteur et apporte une valeur ajoutée aux produits, que ce soit des fruits ou des légumes, de la viande ou encore des viennoiseries.
L’industrie électronique
Le monde devenant de plus en plus numérique et technologique, il est de plus en plus nécessaire de développer des pièces et des produits électroniques. Au fur et à mesure que les technologies ont progressé, on a rendu les objets électroniques minuscules, par exemple avec les ordinateurs ou les smartphones. Les produits s’adaptent, tout comme les processus de fabrication. La découpe au laser s’emploie principalement en raison de sa capacité à segmenter des pièces minuscules et complexes.
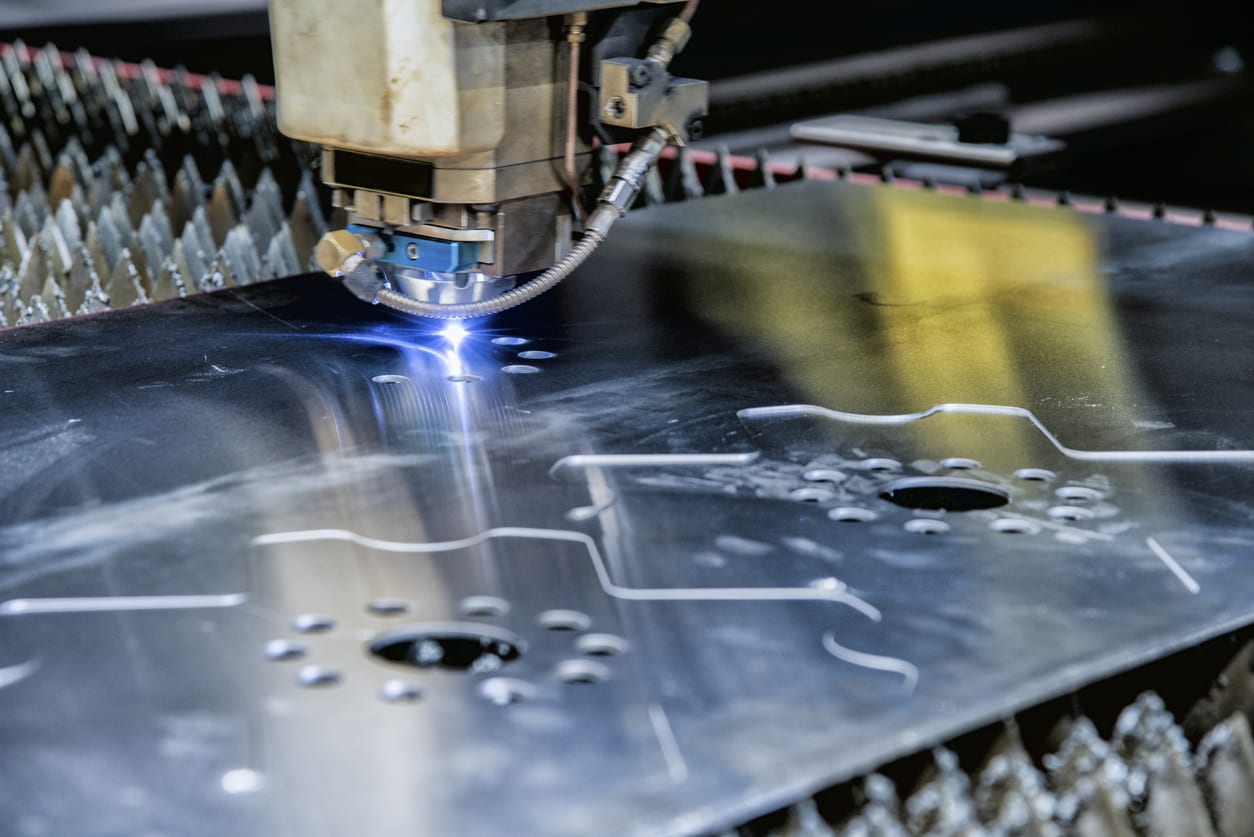
Obtenez plusieurs devis pour vos projets en quelques secondes