Plastique
Découvrez ce qu'est le plastique ou polymere et les applications de ce matériau de fabrication dans l'industrie.
Introduction au plastique
Le plastique est un matériau constitué de composés organiques synthétiques ou semi-synthétiques, parmi une large gamme. Ils sont malléables et peuvent par conséquent se mouler en objets solides. La plasticité représente la propriété générale de l’ensemble des matériaux qui impliquent une déformation permanente sans rupture. Le nom des polymères provient de leurs propriétés flexibles et plastiques.
Les plastiques sont en général des polymères organiques de masse moléculaire élevée. Ils contiennent souvent d’autres substances. Ils sont synthétiques et découlent le plus souvent de produits pétrochimiques. Cependant, l’attention actuelle portée sur l’environnement conduit à un nombre croissant de plastiques dérivés de matériaux renouvelables comme l’acide polylactique venant du maïs ou la cellulose des bourres de coton.
La démocratisation du plastique dans des produits toujours plus abondants provient de son coût relativement faible, sa facilité de fabrication, sa polyvalence et son imperméabilité à l’eau. Il s’emploie dans des pièces aussi simples que des trombones ou complexes que des avions.
Une large gamme de matériaux plastiques est disponible pour un éventail d'utilisation. L’un des domaines de confection les plus récents et les plus formidables est l’impression 3D. De nouvelles applications d’impression 3D sont découvertes quasi quotidiennement. Une palette d’objets en plastique diversifiée est donc déjà produite à l’aide du procédé d’impression 3D. Ces objets se retrouvent dans les laboratoires de prototypage, les jouets, les boîtes de vitesse mécaniques, les prothèses médicales, etc.
Les plastiques se classent généralement selon la structure chimique du squelette et la chaîne latérale du polymère ; ces catégorisations incluent des groupes importants comme les suivants :
- · Acryliques
- · Polyesters
- · Silicones
- · Polyuréthanes
- · Plastiques halogénisés
À des fins de clarté, cette documentation se concentre sur un ensemble de polymères représentatifs, appelés également plastiques de base, plastiques courants ou plastiques techniques.
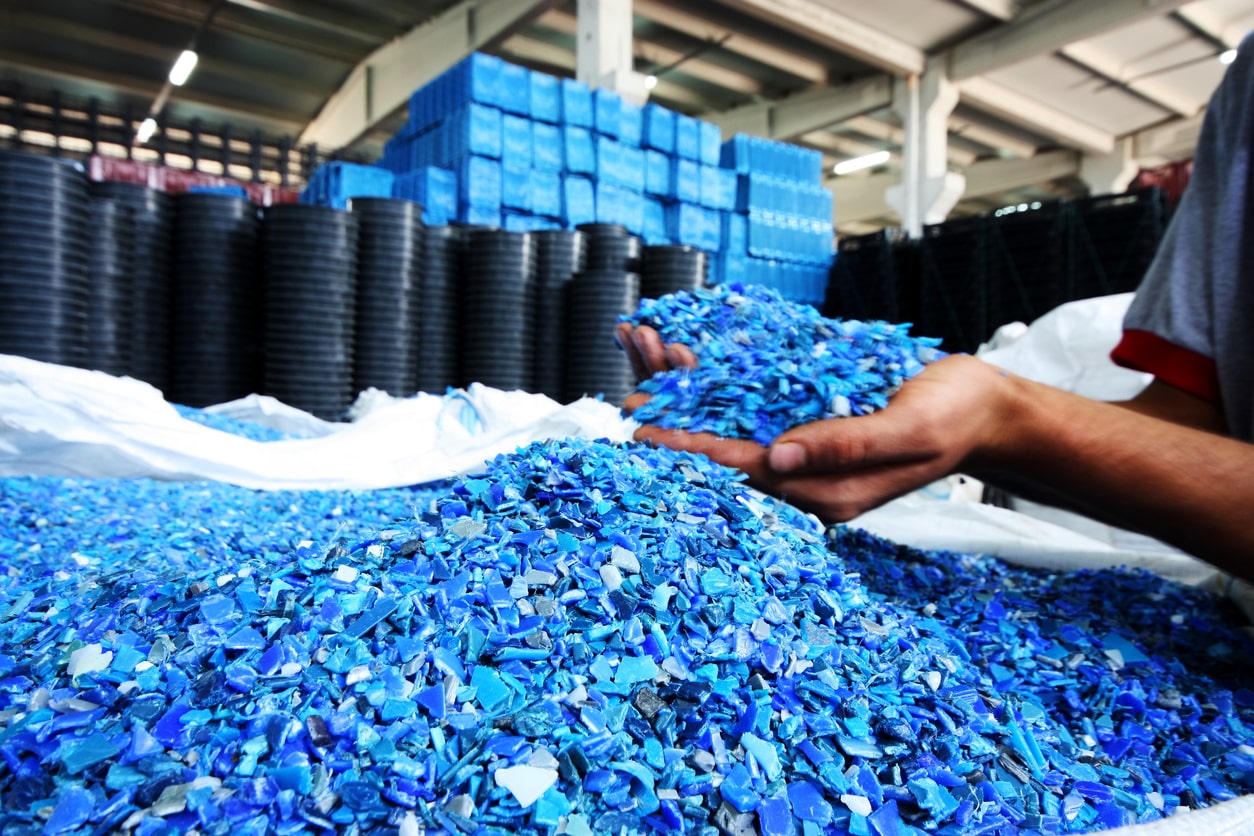
Matériaux plastiques génériques
Le plastique ABS
L’acrylonitrile butadiène styrène (ABS) est un terpolymère obtenu par polymérisation de styrène et d’acrylonitrile en présence de polybutadiène. La plupart des applications peuvent supporter des températures de -20 à 80 °C (-4 à 176 °F). Elles incluent l’équipement électronique, comme les écrans d’ordinateur, les imprimantes et les claviers ainsi que les drains.
Le plastique PA
Le polyamide (PA) ou nylon se présente sous forme naturelle, par exemple avec la laine et la soie, et synthétique, comme avec le nylon, la fibre aramide et le polyaspartate de sodium. Les polyamides synthétiques s’emploient dans l’industrie du textile, de l’automobile, des moquettes et tapis et des vêtements de sport pour leur longévité et leur solidité. La consommation de polyamide des secteurs de la fabrication et du transport est estimée à 35 % du polyamide (PA) mondial. Les usages principaux incluent par exemple les fibres, les poils de brosses à dents, les tubes, les lignes de pêche et les pièces de machine à faible solidité dans les châssis de moteurs ou la structure des armes à feu.
Le plastique PC
Les polycarbonates (PC) appartiennent au groupe des polymères thermoplastiques contenant du carbonate. Leur solidité et leur résistance, ainsi que la transparence de certaines classes, en font un élément adapté pour l’ingénierie. De plus, leur flexibilité facilite leur travail, moulage et thermoformage. Par conséquent, les polycarbonates (PC) s’utilisent dans beaucoup d’applications, comme les disques compacts, les lunettes, les boucliers antiémeute, les fenêtres sécurisées, les feux de signalisation et les lentilles.
Le plastique PES
Le polyester (PES) se trouve à l’état naturel, par exemple dans la cutine des cuticules de plantes, et sous forme synthétique dans la polymérisation par étapes comme le polybutirate. Les polyesters naturels, et quelques rares polyesters synthétiques sont biodégradables. L’industrie du vêtement et du textile exploite largement les polyesters.
Le plastique PE
Le polyéthylène (PE) est le plastique le plus répandu avec une production globale annuelle d’environ 80 millions de tonnes. Il s’emploie principalement dans le secteur du conditionnement pour les sacs en plastique, les films plastiques, les géomembranes et les contenants (y compris les bouteilles).
Le plastique PE-HD
Le polyéthylène haute densité (PE-HD), HDPE (High Density Polyethylene) ou PE-HD (Polyethylene High Density) en anglais, est un thermoplastique dérivé du pétrole avec un ratio solidité-densité élevé. On le retrouve fréquemment dans les bouteilles de détergent, les bouteilles de lait, les éléments en plastique moulé, les bouteilles plastiques, les tuyaux anticorrosifs, les géomembranes et le bois composite. Lorsqu’il est utilisé pour les tuyaux, il se nomme parfois alkathène ou polythène.
Le plastique PEBD
Le polyéthylène basse densité (PEBD) est un thermoplastique obtenu à partir de l’éthylène monomère. Produit pour la première fois en 1933 par Imperial Chemical Industries (ICI), sa fabrication est réalisée à l’aide de la même méthode aujourd’hui. Son utilisation reste également répandue dans les mobiliers d’extérieur, les revêtements, les tommettes, les rideaux de douche et les emballages à double coque, malgré la concurrence de polymères plus modernes.
Le plastique PET
Le polyéthylène téréphtalate (PET), souvent abrégé PET ou PETE, est la résine de polymère thermoplastique la plus commune de la famille des polyesters. On l’exploite pour la production des fibres des vêtements, les contenants des liquides et aliments, le thermoformage pour la fabrication et en combinaison des fibres de verre pour les résines techniques. Les noms de marque incluent : Dacron, Terylene ou Lavsan.
Le plastique PP
Le polypropylène (PP), également appelé polypropène, est un polymère d’addition résistant et anticorrosif qui appartient au groupe des polymères thermoplastiques. Après le polyéthylène, il est le deuxième plastique synthétique le plus produit. L’industrie y recourt pour un large éventail d’applications. Citons le conditionnement, l’étiquetage, les textiles, les éléments stationnaires, les pièces en plastique, les contenants réutilisables, l’équipement de laboratoire, les haut-parleurs, les composants automobiles et les billets de banque en polymère.
Le plastique PS
Le polystyrène (PS) est un polymère aromatique synthétique obtenu à partir du styrène monomère. Il peut se présenter sous la forme de solide ou de mousse. Le polystyrène à usage général est clair, dur et relativement cassant. Il offre un poids de résine par unité peu onéreux. Il est par nature transparent, mais peut être coloré. C’est l’un des plastiques les plus utilisés. Des millions de tonnes par an sont produits. Il s’emploie fréquemment pour les particules de calage dans les emballages, les contenants alimentaires, la vaisselle en plastique, les tasses, assiettes et couverts jetables, les disques compacts (CD) et les boîtiers de cassette.
Le plastique SB
Le polystyrène choc (SB) (HIPS, High Impact Polystyrene) est un copolymère à greffons issu du mélange de polystyrène et de caoutchouc polybutadiène plus étirable au cours de la polymérisation. Cela permet d’obtenir un polystyrène choc, souvent indiqué comme « plastique résistant aux chocs » dans les publicités. Il est fréquemment moulé par injection pour produire des jouets, des revêtements de réfrigérateur, des emballages alimentaires et des tasses de distributeur. Bextrene est un des noms de marque.
Le plastique PUR et PU
Le polyuréthane (PUR et PU) est un polymère composé d’unités organiques jointes par des liaisons de carbamate (uréthane). Même si la plupart des polyuréthanes sont des polymères thermodurcissables qui ne fondent pas lorsqu’ils sont chauffés, des polyuréthanes thermoplastiques sont également disponibles. Les applications courantes incluent : mousse de matelassage, mousses d’isolation thermique, revêtements de surface et rouleaux d’impression. Il s’agit du plastique le plus fréquemment utilisé dans les automobiles.
Le plastique PVC
Le polychlorure de vinyle (PVC), aussi appelé PVC, poly vinyle ou vinyle, est le troisième polymère de plastique synthétique le plus produit au monde après le polyéthylène et le polypropylène. Le PVC est disponible sous forme rigide (RPVC) ou flexible. Les applications communes pour le RPVC incluent les tuyaux de plomberie, les gouttières, les portes, les cadres de fenêtres, et les cartes de membre ou de banque. Celles pour le PVC flexible comprennent les rideaux de douche, les revêtements de sol, le similicuir, la signalisation, les disques, les produits gonflables et les différents usages où il remplace le caoutchouc.
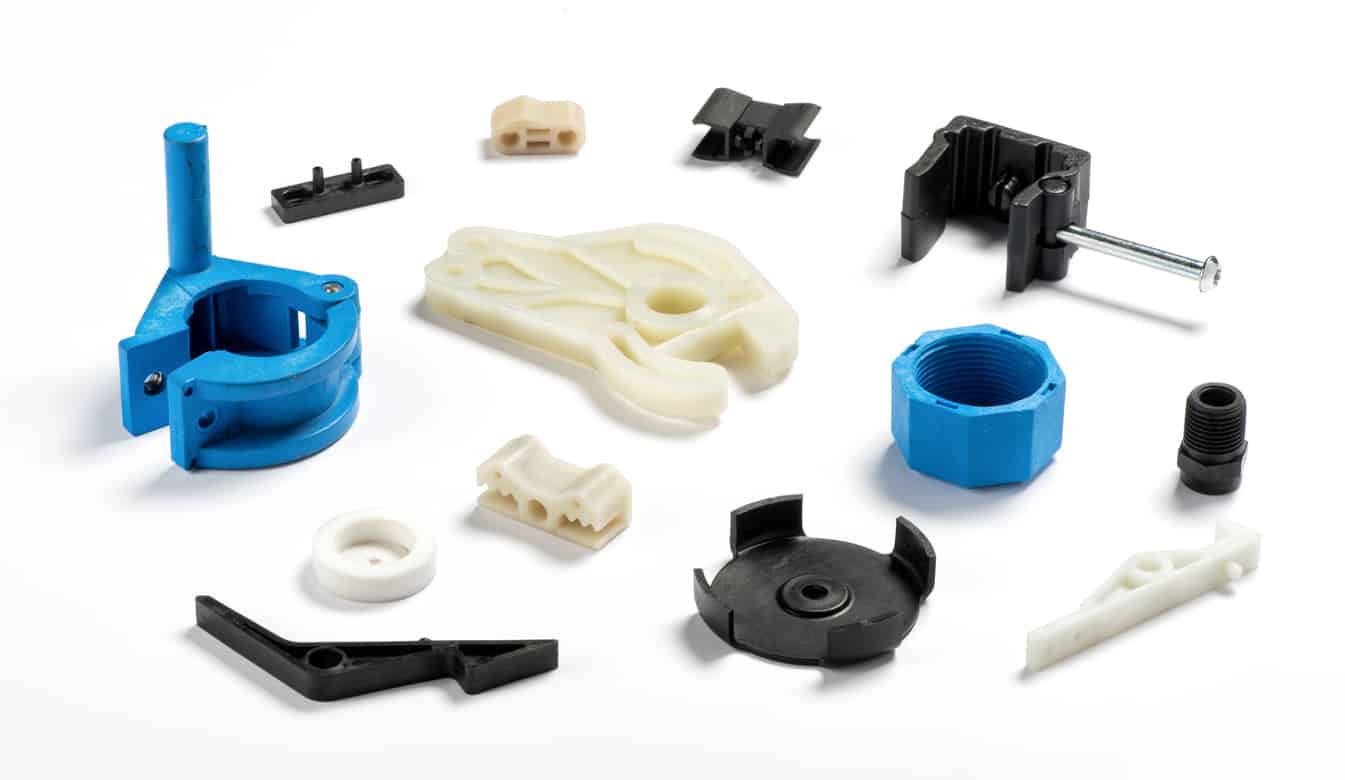
Matériaux plastiques pour les procédés d’impression 3D
Outre les matériaux thermoplastiques génériques, l’industrie de l’impression 3D a adopté certains plastiques pour leurs propriétés techniques.
- Le butadiène styrène (ABS) est un thermoplastique et constitue le matériau phare avec lequel les lego se fabriquent. On le retrouve dans les habitacles automobiles et les équipements ménagers du quotidien. L’ABS s’adapte particulièrement bien pour des applications fonctionnelles complètes. En effet, ses caractéristiques correspondent à 80 % à celles utilisées avec le matériau de production injecté. Bien que l’ABS offre une grande liberté de conception, on considère le niveau des détails imprimés comme moyen même si la qualité d’impression est élevée. La qualité de la surface des objets imprimés en ABS est relativement irrégulière comparée à d’autres matériaux. L’ABS est disponible en rouge, noir ou blanc concernant la finition naturelle et il est résistant aux UV.
- L’ABS simulé possède la résistance de l’ABS tout en proposant des moules (à injection) fonctionnels de précision. Ses caractéristiques majeures sont la solidité, la résistance aux températures importantes, des détails fins et une belle finition de surface lisse. L’ABS simulé présente également une résistance aux impacts et une absorption des chocs élevés. Les prototypes solides et durables sont les principaux candidats pour l’ABS simulé et il constitue le moyen le plus rapide et le plus abordable pour fabriquer des moules à injection de haute précision pour les petites séries de moules à injection de 10 à 100 pièces.
- Nylon for the SLS (Selective Laser Sintering) manufacturing process employs laser sintering to deliver functional prototypes and end-use parts by melting extremely thin layers of powdered Nylon to shape and form a solid structure. Le nylon permet de produire des conceptions complexes qui présentent des détails chargés. On l'emploie principalement pour les pièces mobiles et assemblées, les boîtiers, les éléments portatifs ou les adaptateurs. L’inconvénient est qu’il peut comporter des cavités dans sa conception, sauf si le concepteur utilise des trous d’évacuation.
Les fabricants d'imprimantes 3D créent leur propre plastique
Certains fabricants d’imprimantes 3D tendent à développer leur marque. Les différents plastiques à exploiter dans l’impression 3D incluent : le plastique de prototypage, le plastique opaque rigide, le plastique similaire élastomère et le plastique transparent. Chacun de ces plastiques possède ses propriétés et applications spécifiques.
- Le plastique de prototypage utilise les imprimantes FDM (Fused Deposition Modeling) pour produire les prototypes. C’est un matériau idéal pour les concepteurs et les ingénieurs pour réaliser et tester une conception à moindre coût et pour commercialiser les produits plus rapidement. Ses caractéristiques principales sont un délai de fabrication court, un prix économique et un prototypage de forme et d’ajustage. Ses limites incluent une tolérance de +/— 1 mm, un excédent qui nécessite un support et affecte la finition de surface, des couches d’impression visibles et une anisotropie (faiblesse dans la direction Z). Le plastique de prototypage est le plus adapté pour les vérifications de forme et d’ajustage, mais également pour les pièces fonctionnelles comme les enceintes et tuyaux personnalisés.
- Le plastique opaque rigide est le matériau majeur permettant d’obtenir des prototypes réalistes avec des détails distinctifs, une précision élevée et une finition de surface lisse avec des hauteurs de couche allant jusqu’à 16 microns. Ses principaux atouts incluent des modèles dans les moindres détails avec des surfaces lisses, adaptés pour les tests de forme et d’ajustage, pratiques pour les modèles de démonstration en vente et marketing ainsi que son adéquation pour les pièces mobiles et assemblées. Son seul inconvénient est sa sensibilité aux UV.
- Le plastique élastomère permet de simuler du caoutchouc avec différents niveaux de caractéristiques élastomères. Ceux-ci incluent une dureté A sur l’échelle de Shore, une élongation à la rupture, une résistance à la déchirure et une résistance à la traction. La technique principale utilisée avec le plastique élastomère est le frittage par laser. Les produits finis comme les brosses à dents, les surfaces antidérapantes ou molles sur l'électroniques grand public, les appareils médicaux et les intérieurs d’automobiles peuvent être fabriqués avec du plastique élastomère. On le retrouve de temps en temps dans la mode, dans les modèles qui nécessitent une absorption des chocs, dans les gadgets, les modèles souples et les fonctionnels. Sa sensibilité aux UV constitue un inconvénient.
- Le plastique transparent est bien adapté pour la fabrication des pièces translucides et prototypes avec une précision élevée. Il s’agit de l’un des matériaux d’impression 3D les plus transparents sur le marché. Optimal pour les tests de forme et d’ajustage, le plastique transparent présente une finition de surface lisse idéale pour la construction de modèles avec des détails fins ou des produits clairs et tintés. Nous pouvons prendre pour exemple les lunettes, la protection des éclairages et les appareils médicaux. Il est particulièrement adapté pour les modèles de démonstration médicaux/scientifiques dans les ventes et le marketing. Sa sensibilité aux UV constitue un inconvénient.
- Le polyamide pour la technique d’impression 3D SLA (Selective Laser Sintering, frittage sélectif par laser) est une poudre granulaire blanche très fine qui utilise le frittage par laser pour fabriquer des modèles complexes, conceptuels et fonctionnels. Mais aussi des lampes et des petites séries de modèles où plusieurs copies sont reproduites. Le frittage par laser du polyamide offre la meilleure liberté de conception comparée à toutes les autres techniques d’impression 3D. Le produit final obtenu est un objet solide, relativement flexible qui peut supporter des impacts faibles et résister à une certaine pression sous des contraintes de pliage. La surface naturelle est un peu poreuse avec une apparence granulaire, sableuse, et plusieurs possibilités de finition existent. Les objets en polyamide peuvent se terminer avec une surface satinée, polie ou velouteuse ou peuvent être teints ou peints à l’aérosol. Ils peuvent être également étanchéifiés avec une solution aqueuse imperméable.
- Polyamide (MJF)) est une poudre granulaire très fine qui utilise la technologie de fusion HP Multi-Jet pour élaborer des modèles complexes, fonctionnels ou conceptuels, ainsi que des petites séries de modèles reproduits à plusieurs exemplaires. La fabrication d’objets en polyamide (MJF) à l’aide de la technologie HP Multi-Jet Fusion offre la plus grande liberté de conception comparée à toutes les autres techniques d’impression 3D. Idéale pour une résolution de surface détaillée et des parois plus fines. Cette technique produit une densité plus élevée et une porosité plus faible que la technique homologue de frittage sélectif par laser. La finition de surface naturelle du polyamide (MJF) est fine, granulaire et grise. La teinture est recommandée pour obtenir une apparence uniforme.
Les caractéristiques et usages de la résine plastique
Les différentes résines utilisées dans l’impression 3D incluent la résine hautement détaillée, la résine mammouth, la résine transparente, la résine grise et la résine standard. Chacune d’entre elles possède ses propres caractéristiques et applications spécifiques.
- Le liquide photopolymère s’emploie pour fabriquer des objets avec une résine hautement détaillée à l’aide des technologies de prototypage PolyJet, de stéréolithographie (SLA) et DLP (Digital Light Processing, traitement numérique de la lumière). La résine hautement détaillée est très bien adaptée pour les modèles visuels de petite taille et/ou finement détaillés. Les modèles produits avec de la résine hautement détaillée présentent des surfaces lisses bien que leur usage fonctionnel soit limitée. Les utilisateurs ont une liberté de conception restreinte, car ils doivent retirer le matériau de support. Le procédé de finition implique le durcissement à la lumière UV tout de suite après le travail au jet, cependant il est nécessaire d’éviter que le modèle ne soit exposé à la lumière directe du soleil pour empêcher la décoloration. Il est possible d’augmenter la résistance aux UV et d’améliorer l’apparence avec de la peinture ou du vernis.
- La résine mammouth sert à produire des modèles de démonstration de qualité supérieure et des moules de référence. Ceci est grâce à l’excellente qualité de sa surface et à son potentiel de finition de qualité supérieure en réalisant des étapes de finition supplémentaires. La stéréolithographie est la technique utilisée pour fabriquer des objets avec de la résine mammouth. Cette technique exige une structure de support pendant l’impression, ce qui limite par conséquent la liberté de conception. La finition est disponible dans son état naturel ou l’objet peut être peint à l’aérosol. Dans sa finition de base, naturelle, certaines couches restent visibles et l’objet est sensible à la lumière UV.
- La résine transparente s’emploie pour fabriquer des modèles qui demandent une apparence de surface lisse, transparente ou propre, comme avec les modèles de démonstration dont la fonctionnalité est limitée. On a recourt à un liquide durci pour confectionner les modèles avec de la résine transparente ; il est solide, ferme, rigide, naturellement imperméable et transparent. La stéréolithographie est la technique utilisée pour produire des objets en résine transparente, ce qui réduit la liberté de conception, car une structure de support est nécessaire pendant l’impression. Surtout adaptée pour les modèles de démonstration, les modèles précis et les modèles à fonctionnalité limitée, sa transparence n’est pas à 100 % claire comme de l’eau de roche. Les modèles solides dont l’épaisseur est supérieure à 2 cm (0,8 pouce) présenteront un éclat bleuâtre. La finition naturelle, appelée finition technique, implique de durcir l’objet sous la lumière UV puis d’appliquer une couche de peinture transparente pour réduire la décoloration à la lumière UV. Il est possible d’ajouter une petite quantité de couleur à la peinture.
- La résine grise s’emploie en général pour fabriquer des modèles de démonstration et des prototypes visuels de haute qualité en utilisant la technique de la stéréolithographie. Le résultat est une couleur grise avec une finition de surface presque luxueuse. La résine grise s’adapte parfaitement pour les modèles de personnage et de jouet, mais elle est adaptable pour les modèles visuels recto avec une fonctionnalité limitée. Elle produit l’une des surfaces les plus lisses parmi tous les matériaux d’impression 3D. Elle présente une résistance mécanique moyenne et est sensible à la décoloration par la lumière UV. La liberté de conception est réduite, car elle nécessite une structure de support pendant l’impression. La surface de finition au verso de la résine grise est matte et révèle visiblement des petits points provenant des structures de support d’impression 3D.
- La résine standard s’utilise pour fabriquer des modèles de démonstration de qualité supérieure et des prototypes visuels à l’aide de la technique de stéréolithographie. Le résultat est un objet translucide avec une teinte de couleur jaune. La résine standard est bien adaptée pour les modèles de personnage et de jouet, mais aussi pour les modèles visuels recto avec une fonctionnalité limitée. Ces modèles sont particulièrement attractifs lorsqu’ils sont peints. La résine standard produit l’une des surfaces les plus lisses parmi tous les matériaux d’impression 3D. La liberté de conception est réduite, car elle nécessite une structure de support pendant l’impression. La surface de finition au verso de la résine standard est matte et sensible aux UV, et révèle visiblement des petits points provenant des structures de support d’impression 3D.
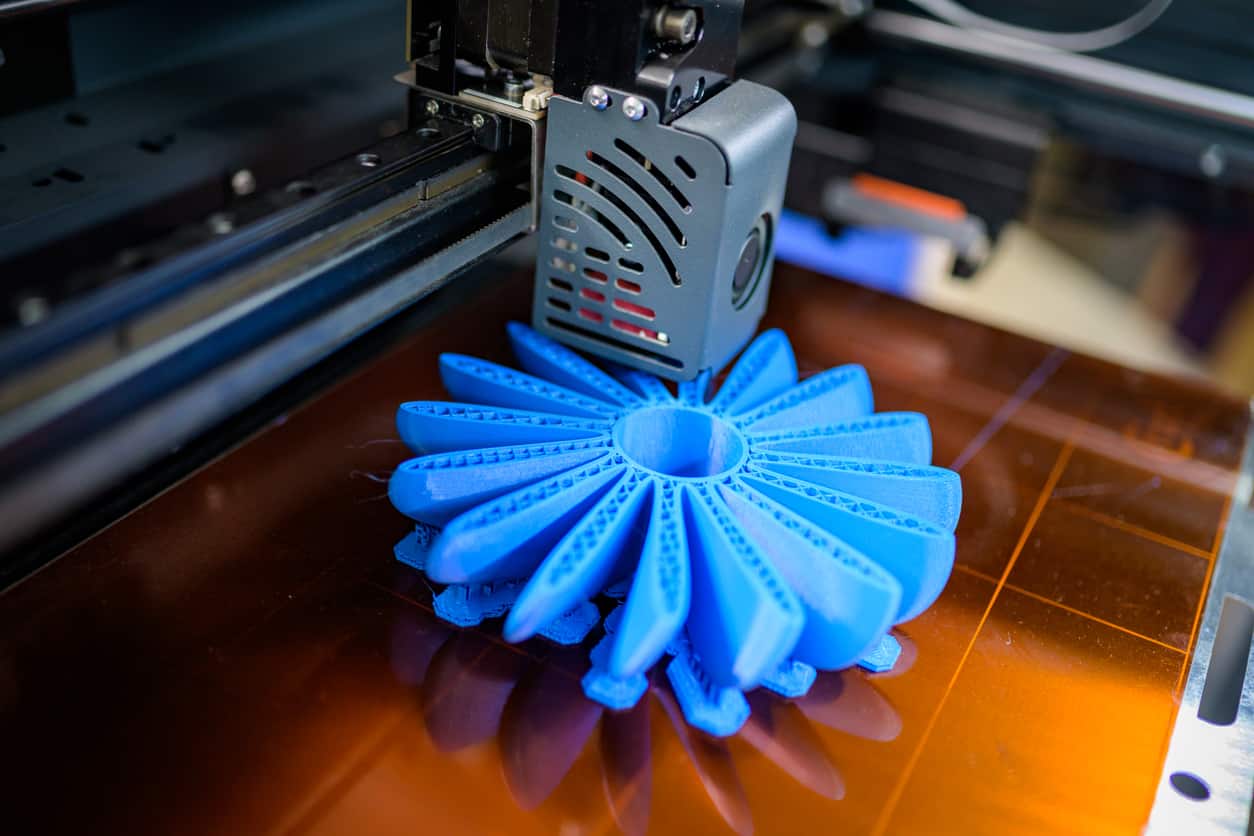
Obtenez plusieurs devis pour vos projets en quelques secondes