Modélisation virtuelle pour une innovation industrielle accélérée
La modélisation virtuelle révolutionne l'innovation industrielle de l'automobile à la mobilité durable avec la plateforme 3DEXPERIENCE
JUSQU’ICI
Les lignes de production étaient installées une fois pour toutes, sans possibilité d’optimiser ou de modifier leur fonctionnement
DÉSORMAIS
Les modélisations et simulations virtuelles accélèrent l’innovation et le développement industriels en collaborant avec toute la chaîne de valeur pour répondre aux nouvelles exigences des clients, des régulateurs et de la planète
Produire plus vite, moins cher et plus durablement est l’un des grands défis économiques et sociétaux qui inspirent les industriels pour repenser leur outil de production. L’essor des usines intelligentes, la fabrication numérique, la prolifération de l’IA et le pouvoir de la data sont autant de leviers de modernisation. Qu’il s’agisse d’optimiser la conception de voitures, de planifier l’utilisation de robots sur des lignes de production, d’embarquer les industries alimentaires ou navales dans l’ère numérique, ou de dessiner une nouvelle génération d’avions durables, la plateforme 3DEXPERIENCE n’a pas d’équivalent. Les jumeaux virtuels de machines, de procédés et de produits accélèrent la transformation digitale, améliorent l’efficacité opérationnelle et les décisions fondées sur les données tout au long du cycle de vie du produit.
Révolutionner l’ingénierie automobile
Le groupe BMW étend son partenariat stratégique avec Dassault Systèmes pour développer sa future plateforme d’ingénierie avec en son cœur la plateforme 3DEXPERIENCE.
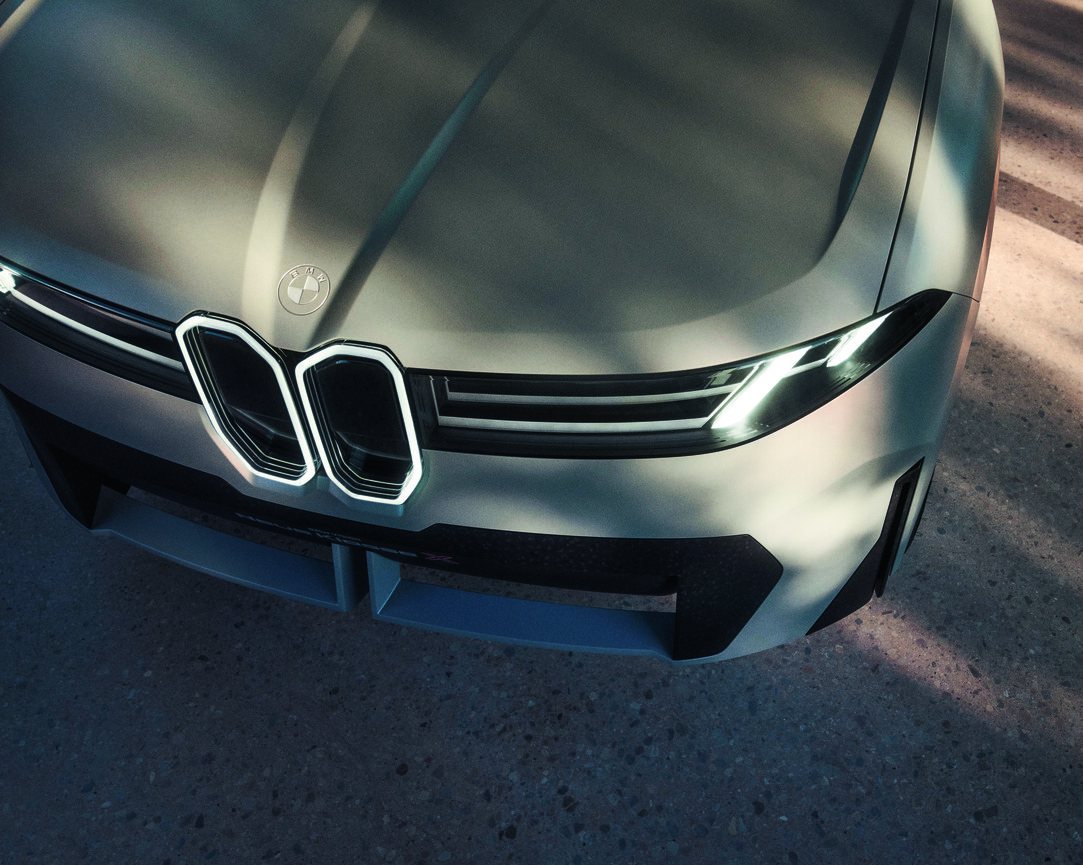
Dassault Systèmes et BMW Group ont étendu leur partenariat pour développer la plateforme d’ingénierie du groupe. La plateforme 3DEXPERIENCE, au cœur de ce projet, va permettre au groupe de repenser ses processus d’ingénierie pour accélérer le développement de ses véhicules, rationaliser la collaboration à l’échelle de l’entreprise et permettre une gestion plus efficace des données.
Maîtriser la complexité des configurations véhicules
Depuis plusieurs décennies, Dassault Systèmes et BMW Group ont bâti un partenariat stratégique, ils mutualisent leurs connaissances et leurs savoir-faire pour stimuler l’innovation technologique dans les domaines de la planification et l’ordonnancement de la fabrication, la conception de pièces et l’efficacité de la production. Grâce à la plateforme 3DEXPERIENCE placée au cœur de l’écosystème de développement des produits du BMW Group, toutes les équipes des différentes disciplines d’ingénierie travailleront sur un jumeau virtuel d’un véhicule configurable à partir des variantes de chaque modèle et en utilisant des données intégrées en temps réel. Elles pourront réutiliser les composants plus facilement, maîtriser la complexité des variantes et accélérer le cycle de développement produit de l’ingénierie à la fabrication. De plus, le groupe BMW peut maintenant migrer en toute transparence les données des solutions informatiques existantes et étendre sa plateforme d’ingénierie à d’autres disciplines telles que la modélisation et la simulation.
Accélérer la mobilité durable
L’accélération de la mise sur le marché de solutions de mobilité durable à l’aide d’une technologie de pointe telle que la plateforme 3DEXPERIENCE est un véritable atout concurrentiel dans le secteur de l’automobile autonome. Cette relation de confiance entre Dassault Systèmes et le groupe BMW, approfondie par ce nouveau partenariat, témoigne du rôle transformateur de la plateforme virtual twin experiences. Ils stimulent la collaboration à travers l’entreprise et permettent de gérer la complexité exponentielle à laquelle les constructeurs automobiles sont confrontés lors de l’ingénierie de véhicules autonomes connectés en s’appuyant sur une approche fondée sur les données.
« Nous ne pourrons optimiser notre processus d’ingénierie qu’en pensant numérique, en travaillant de façon connectée et en nous appuyant sur des données intégrées. Pour le groupe BMW, la plateforme 3DEXPERIENCE soutiendra cette approche et nous aidera à atteindre un plus haut niveau de qualité dans nos processus. »
L’odyssée des robots industriels
Avec la mise en service virtuelle – une fonctionnalité aujourd’hui offerte par la plateforme 3DEXPERIENCE sur le Cloud – Robot at Work s’assure de répondre plus aisément et efficacement aux exigences de plus en plus complexes de ses clients et les aide à optimiser leurs lignes de production.
Les industriels sont contraints à la fois de réduire leurs coûts de production, d’accélérer la mise sur le marché, d’améliorer la productivité de leurs collaborateurs, tout en optimisant leur relation client. Un défi qui, pour le spécialiste italien des robots de ligne de production, Robot at Work, signifiait en premier lieu : répondre aux besoins d’automatisation complexes de ses clients avec des robots standards.
Jusqu’ici, à chaque commande, Robot at Work devait imaginer comment une cellule robotisée pourrait s’intégrer dans la ligne de fabrication de l'usine. Il a été inspiré par l’efficacité de la mise en service virtuelle (à l’aide de modèles numériques des usines et des équipements) adoptée par ses clients de l’industrie automobile. Robot at Work a décidé d’exploiter cette technologie pour tester les capacités de ses robots, évaluer leurs fonctionnalités et identifier les éventuels défauts et axes de progrès, avant de les implémenter chez ses clients.
Une conception 100% virtuelle
Les solutions DELMIA de la plateforme 3DEXPERIENCE offrent à Robot at Work des fonctionnalités avancées pour programmer ses robots en fonction de la ligne de production et simuler leur comportement avec précision. D’autres solutions de la plateforme lui permettent de créer des usines virtuelles pour simuler une infinité de scénarios de configuration de lignes de production avant qu’un client ne s’engage dans la construction ou la restructuration physique de celles-ci. Ces solutions pouvant être déployées sur le Cloud, Robot at Work a pu se lancer sans investir massivement dans une infrastructure informatique.
Désormais, Robot at Work peut simuler de manière précise le comportement de tous les robots d’une ligne de production et comparer plusieurs marques pour sélectionner celle qui répond le mieux aux besoins d’un client. En définissant chaque ligne de production dans le moindre détail, son équipe peut identifier les robots les mieux adaptés à telle ou telle tâche et regrouper plusieurs fonctions en une seule cellule. La conception virtuelle garantit la meilleure solution pour chaque client, en évitant à Robot at Work les coûts, retards et erreurs liés à une approche traditionnelle, à savoir installer physiquement une ligne de production et tenter de la corriger et de l’optimiser sur site.
Un service après-vente nouvelle génération
La mise en service virtuelle constitue un levier de transformation pour Robot at Work. Elle lui permet non seulement de répondre aux besoins de plus en plus complexes de ses clients mais aussi de leur apporter de nouvelles opportunités de services une fois la ligne mise en opération. Nombreux sont les clients qui modifient leur production deux à trois fois par mois. Grâce à la technologie de Dassault Systèmes, Robot at Work peut leur fournir une cellule opérationnelle dans les meilleurs délais. Cette réactivité et le fait de pouvoir visualiser la rentabilité de leur investissement avant de lancer la construction rassurent les clients et renforcent la relation commerciale.
« Nos clients ont désormais la possibilité de visualiser en amont l’intégralité de leur ligne de production et les résultats de leur investissement. Cela nous rapproche considérablement. »
Devenir leader de la foodtech
Groupe français parmi les leaders de l’industrie agroalimentaire, le groupe Bel est mondialement connu pour ses marques emblématiques comme Babybel ou Pom’Potes. Bel et Dassault Systèmes unissent leurs forces pour contribuer à une alimentation plus saine, innovante et responsable à base de lait, de fruits et de végétaux.
Entreprise familiale de plus de 150 ans, la mission du Groupe Bel pour une transition alimentaire positive dans l’industrie agroalimentaire s’incarne à travers une large gamme de portions fromagères, fruitières et végétales accessibles à tous. Le groupe est engagé dans cette transition plus responsable à travers le développement d’une offre plus saine, le soutien à des pratiques agricoles plus durables et régénératives, et la réduction du gaspillage alimentaire.
Pour cet ambitieux projet, Bel s’est associé à Dassault Systèmes. L’objectif ? Allier les forces et les expertises respectives pour le développement de technologies innovantes – comme la fermentation de précision – permettant de répondre à complexité de la demande alimentaire mondiale.
À travers ce partenariat, les objectifs de Bel sont d’améliorer l’efficacité opérationnelle, de déployer des plateformes en ligne de pointe et de développer la digitalisation dans la gestion du cycle de vie des produits.
Dans cet enjeu, Dassault Systèmes vient renforcer les capacités du groupe Bel en matière de science des données dans onze de ses usines dans différentes régions à travers le monde. Ensemble, les deux groupes travailleront à déployer des solutions industrielles pour tirer parti de la digitalisation et de l’intelligence artificielle au service de choix alimentaires innovants, plus sains et plus durables pour tous.
USINES AU BÉNÉFICE DE MILLIERS D'OPERATEURS DU GROUPE BEL
CHERCHEURS EN R&D IMPLIQUÉS DANS LE GROUPE BEL
Ouvrir une nouvelle voie dans la construction navale
Damen, groupe international de chantiers navals, veut devenir le constructeur naval le plus durable et le plus connecté au monde. La plateforme 3DEXPERIENCE lui permet de mener une métamorphose d’une entreprise centrée sur le produit à une entreprise centrée sur le service.
L‘explosion de la demande de navires personnalisés, durables et compétitifs fait de la transformation numérique une voie stratégique pour la construction navale, une industrie complexe à forte intensité de main-d’œuvre. Avec ses 12000 collaborateurs répartis sur 35 chantiers navals, Damen a adopté la plateforme 3DEXPERIENCE pour consolider ses applications numériques et regrouper ses bureaux d’ingénierie, ses sites de construction et ses parties prenantes dans un espace numérique centralisé qui place le client au cœur des processus.
Grâce à la plateforme, les ingénieurs de Damen gèrent avec agilité les configurations complexes et les modifications lors de l’ingénierie des navires, et anticipent la planification de la production, de l’assemblage et de la maintenance dès la conception. Ils peuvent ainsi collaborer plus efficacement avec leur écosystème industriel et livrer dans les délais des navires à la pointe de l’innovation, tout en optimisant les coûts et la qualité, et testant des options pour optimiser leurs performances environnementales. Au-delà, Damen prévoit d'utiliser la plateforme 3DEXPERIENCE au sein de sa division de bateaux spécialisés. Mais son objectif ultime est de créer le jumeau virtuel d’un navire complet, qui couvrirait toute sa durée de vie, de l’idéation de composant à la conception d’équipements de surveillance permettant une maintenance prédictive.
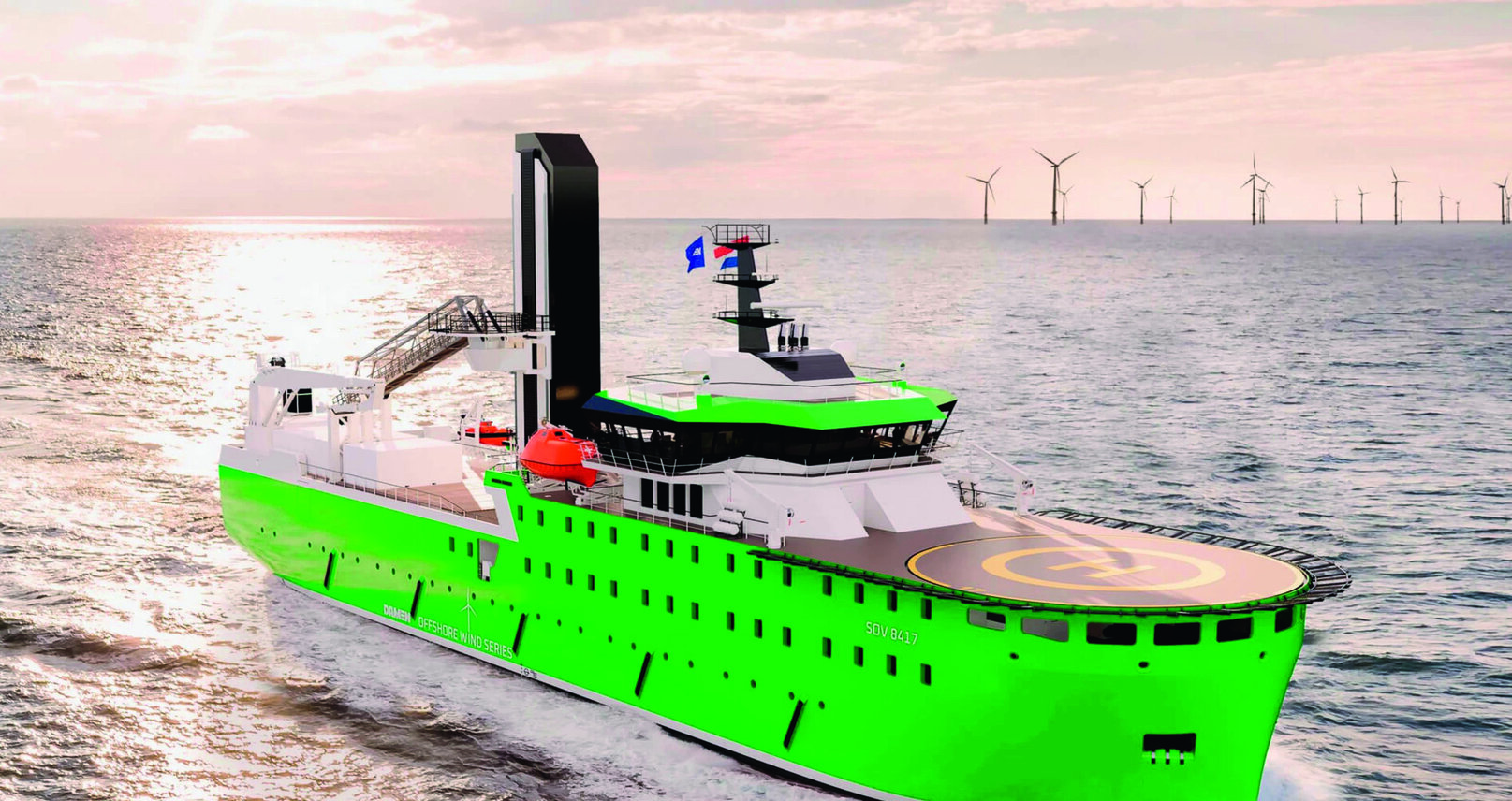
Avènement de l’avion hybride
La start-up française VoltAero fait entrer l’avion électrique dans une nouvelle ère grâce à la propulsion électrique-hybride. Son fondateur, Jean Botti, explique comment l’entreprise a collaboré avec notre DesignStudio pour développer un design exclusif et une proposition de marque unique.
"La plateforme 3DEXPERIENCE nous a permis d'optimiser l'aérodynamisme tout en réalisant quelque chose de très beau."
Comment s’est déroulée la conception de l’avion hybride Cassio 330?
VoltAero conçoit des avions ultraperformants pour le transport de passagers, de fret ou encore les évacuations sanitaires. L’espace collaboratif fourni par la plateforme 3DEXPERIENCE nous a permis de développer notre nouvel appareil durable de A à Z selon une méthode de conception intégrée.
Que vous a apporté la plateforme 3DEXPERIENCE sur le plan de la conception opérationnelle et de la durabilité?
Grâce au concours de Dassault Systèmes et à sa technologie de modélisation par immersion virtuelle, le Cassio 330 est à la fois élégant et optimisé en termes d’aérodynamique, pour un vol sûr et une empreinte carbone allégée.
Comment le DesignStudio de Dassault Systèmes a-t-il aidé VoltAero à définir son image de marque?
Nous avons utilisé la solution de réalité virtuelle de Dassault Systèmes pour présenter le Cassio 330 sous toutes ses coutures à nos clients et nos parties prenantes. Cette expérience a marqué une étape décisive puisqu’elle nous a permis de démontrer en quoi cet avion révolutionnaire reflétait notre identité et notre proposition de valeur unique.
MOINS D'EMISSIONS GHG POUR LE CASSIO 330 EN MODE HYBRIDE