Julian Chee: Just Build It!
Why learning by doing is so important
It's a short step from paper airplanes to becoming a 3DEXPERIENCE Edu aerospace champion for Julian Chee. A true model of “learning by doing”, Julian immerses us in his passion for aerospace through his projects, which he has been able to develop thanks to the skills he has acquired on the 3DEXPERIENCE platform. Having just started his Master's Degree at the University of Wischita, this 3DEXPERIENCE Edu champion shares with us his vision of the skills to be acquired in school and the challenges facing the aerospace industry.
Discover how Julian built his rocket
Tell us a little bit about yourself and how you came to work with the 3DEXPERIENCE platform.
I grew up with a lifelong fascination with aerospace. I flew a lot of remote-control airplanes and designed a lot of origami airplanes as a kid. In fact, back in 2022, me and my friends broke a Guinness World Record for the furthest paper airplane flight.
My first experience with Dassault Systèmes tools was when I went to an aerospace workshop for new students in Malaysia and we learned how to use CATIA for 3D modelling. Shortly after, in 2018, I moved to the US to study aerospace engineering at Wichita State University. One of the undergraduate classes that I took was engineering graphics. We used CATIA for this because it was the main tool used by the surrounding aerospace companies.
After that, I started doing a lot of my own projects, so I bought a student version of CATIA on the 3DEXPERIENCE platform and picked it up from there.
What skills have you acquired through your projects with the 3DEXPERIENCE platform?
I think the most important skill is practice. Because I have a student version of the 3DEXPERIENCE platform, I have been able to practice using Dassault Systèmes solutions long after taking my course. I don’t think this is typical: Most students don't touch the software they have learnt once they have finished their studies until they are forced to by an employer.
By continuing to use the software, I have become a lot more competent in performing trade studies.
For example, if I sketch up a few concepts for an airplane or rocket and I can't decide on a specific design, I can quickly model different concepts and see how various parts integrate before I make a 3D print or laser cutter prototype.
This has given me a much higher level of attention to detail in my work. I model everything – even the screw holes, wiring and switches – so that I can be sure there are no integration errors.
I think the quality of my work has also increased. CATIA on the 3DEXPERIENCE platform has advanced rendering and fly through features, so I can create very realistic graphics in the click of a button. This makes my work look more professional.
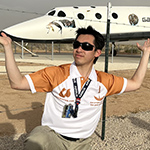
About Julian
Julian Chee, a Malaysian aerospace engineer, earned his bachelor’s degree at Wichita State University and gained experience at Airbus. He later returned to Wichita State for a master’s in Aerospace Engineering while working as a Graduate Research Assistant.
If you didn’t have the chance to cross paths with this rocket design enthusiast at university, don’t worry! Julian shares his passion and expertise widely: on his YouTube channel, LinkedIn, and within the student community. Follow Julian and get inspired to reach for the stars:
You’re a big advocate of learning by doing. Tell us why you believe this is so important.
At Wichita State University, we've got so many prototyping workshops, manufacturing capabilities, equipment and tools available to us, so we can build whatever comes to mind. However, in my experience, many students have big aspirations, but they lack execution. It's always a lot more difficult to bring everything together and create a physical product than it is to just think up a cool idea.
But execution is everything in aerospace. I think it is important to master the discipline and just get it done: Abide by the basic limitations of our analysis, know our limits, buy the materials and just build that thing.
It turns us into better designers since there’s always something to be learned when you go from the CAD world to a physical product. Even out in the industry, the faster we can put out a prototype and a mock up, you know, the faster you can iron out production and operational challenges.
So that's why my motto is ’just build it’.
How are environmental concerns challenging the aerospace and defense industry, and with these concerns in mind, what is your vision for the future of the industry? Additionally, what skills are essential to achieve these ambitions?
I'm a junior engineer at Airbus. We are working on improving old airplanes while also thinking up new clean-sheet designs.
The standard practice is always to make aerospace products lighter, make them cheaper to build and make them more aerodynamic so there’s less fuel to burn. We will definitely see a transition to sustainable aviation fuels in the future. Airbus is also looking quite aggressively into hydrogen combustion airplanes.
I don't work on those new airplanes yet, but one of the biggest challenges when looking to make older designs more sustainable is that a lot of the parts for older airplanes don't really exist in CAD.
However, digital replicas of parts or products always inform us better. They allow us to optimize parts a lot further and figure out more information about them such as how strong they are. Therefore, one of the key skills students should hone is the ability to reverse engineer. A lot of the junior engineers at here in Wichita work at a local Research Institute where they can bring in their model airplanes and scan them so that they can reverse engineer all the old parts and immediately recreate them in in 3DEXPERIENCE – so that’s a great strategy.
How do you think tools like the 3DEXPERIENCE platform can equip future engineers like you with the skills required to realize your vision?
Understanding new engineering methods like systems engineering is crucial.
Traditionally, we work with many different software solutions, but software like the 3DEXPERIENCE platform that allows us to do more model-based systems work where everything is integrated is really changing the game for us – and will be key to the future of the industry.
Something else that I was hit with when I first started working at Airbus is how complicated different processes were. Product life cycle management, configuration management, release processes – these are all formalized processes that we don’t tend to experience fully as students.
What’s great about the 3DEXPERIENCE platform is that we can get to grips with all these processes. It gives students an opportunity to work in the same way as they would in a big aerospace company. I’d really urge students to use the project management side of the 3DEXPERIENCE platform to keep things on track. The platform allows a lot of customization so students can pin their timetable, their to-do lists and other priorities to their dashboard without having to open different programs.
Another great tool in the 3DEXPERIENCE platform is the student community. There are a lot of students and industry experts on hand to answer questions and provide help. I think this is a unique and valuable feature. This collective knowledge is just growing and growing. It's always on standby and allows us to fix problems faster.