Yutaka Electronics
日本机器人装配线制造商 Yutaka Electronics 选择了达索系统的云端 3DEXPERIENCE 平台及其行业解决方案体验 Digital Equipment Continuity,以确保在开始物理调试之前,为客户设计的系统能够正确有效地运行。
通过虚拟调试实现高效的机器人装配线
走进一个现代制造工厂,你很可能会看到各种任务在多种机器人装配线上执行,从焊接和组装,到物料搬运和产品包装。
但是,制造商如何确保他们从自动化装配线中获得最大的收益呢?一个解决方案是借助日本 Yutaka Electronics 这样的产线制造商的专业知识。
“Yutaka 成立于 1964 年,是一家机电一体化技术公司,”该公司总裁兼首席执行官 Takashi Morita 说。"1979 年,它成为日本首批进入工业机器人系统领域的公司之一。从那时起,我们发展成为了一家全方位的系统集成商。我们立志在所从事的行业中做到全球领先。"
Yutaka 分析了工业机器人系统在其客户生产线中的应用情况,这些客户包括汽车、航空航天与国防公司以及 OEM 厂商。然后,它着眼于如何最好地优化该生产线的装配流程,通常借助人工智能(AI)和物联网(IoT)技术。迄今为止,Yutaka 已向 40 多个国家/地区的客户交付了 20,000 多套机器人系统。
“我们仔细检查客户的要求和规格,然后设计最有效的生产线,整合来自知名机器人制造商的机器人系统来实现装配流程的自动化,”Yutaka Electronics 先进技术部总经理 Daisuke Matsuo 说。“最后一步是将设备运送到现场,并在移交之前检查各个部件是否能正常工作。”
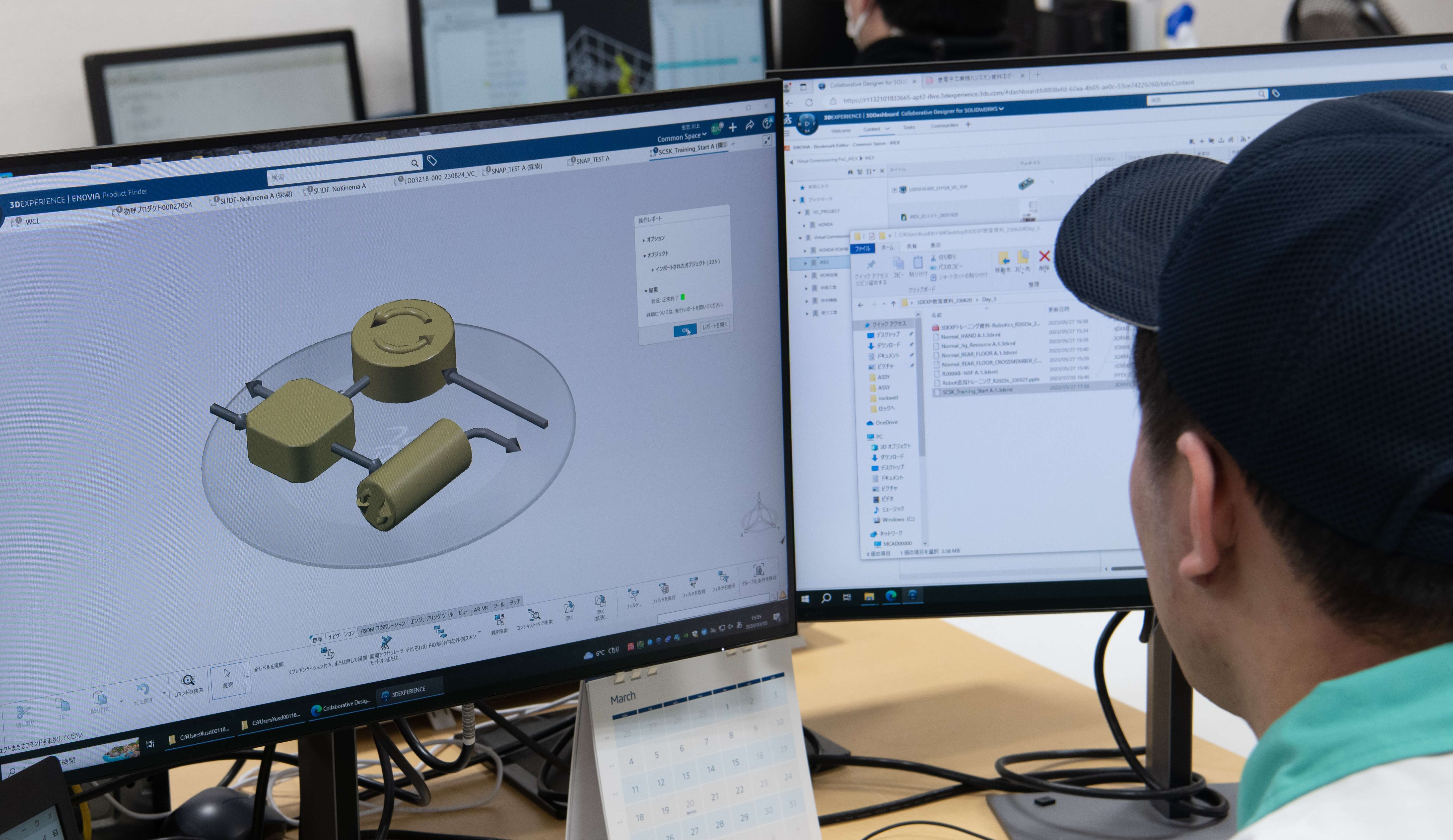
需要更快、更无缝的流程
在竞争日益激烈的市场中,Yutaka 需要快速高效地进行调试,这是一种检查、测试和验证客户机器人装配线组件的工程流程。通常,调试阶段很繁琐,可能导致高达 70% 的项目延误。 Yutaka 也遇到了这个问题:其设计和调试工作是分开进行的。
“过去,我们的绘图员必须在脑海中想象很多流程,”Matsuo 说。“然后使用制造商的数据在 SOLIDWORKS 中起草机械设计。但这些数据中经常存在错误,这导致频繁的返工和回溯。为了检查机器人的操作程序,我们不得不将其导出到第三方软件。这并不是很顺畅。”
Yutaka 意识到它需要一种新的方法,实现虚拟调试并帮助其实现更广泛的数字化转型愿景。Yutaka 已经部署了达索系统的 SOLIDWORKS CAD 软件,并决定使用云端 3DEXPERIENCE 平台作为补充。
“我们发现 3DEXPERIENCE 平台支持我们集中管理所有数据,包括来自 SOLIDWORKS 的数据,”Matsuo 说。“这将对我们产生很大影响。它支持我们能够在更短的时间内完成所有流程,从而加快我们的交付时间。”
虚拟孪生体验使我们能够将调试流程集成到设计工作本身……这将帮助我们消除过去有时被忽视的早期设计缺陷。
验证机器人装配线的单一解决方案
Yutaka 可以通过 3DEXPERIENCE 平台上的 DELMIA 实现机器人生产线的虚拟调试,因为它现在可以在客户制造现场安装物理设备之前验证可行性。以前,公司直到整条生产线完全组装好才能确定节拍时间(为了满足客户需求所需的生产速度)。 这导致额外的现场返工和错过交付日期。
“虚拟孪生体验使我们能够将调试工作集成到设计工作本身,”Matsuo 说。“在进行 3D 建模时,我们可以对包括多个机器人在内的整个系统进行全面的操作检查。这将帮助我们消除过去有时被忽视的早期设计缺陷,从而减少返工。”
基于云的协作
Yutaka 使用 POWER’BY 应用将其在 SOLIDWORKS 中创建的设计连接到 3DEXPERIENCE 平台,而现在机械设计和物理模型仿真在 CATIA 中完成。 公司可以将计算机辅助设计(CAD)和工程物料清单(EBOM)连接起来,并使用 ENOVIA 中的产品生命周期管理(PLM)和数据管理功能来改进变更和问题审核的协作。
通过将所有数据存储在单一的基于云的解决方案中,Yutaka 还可以直接在平台上与客户协作,以安全的方式共享和管理数据。 这也减少了团队前往现场检查生产线的需求。
“在云端集中管理数据会带来强大的协作能力,这会产生巨大的影响,”Matsuo 说。“这意味着我们作为一家公司可以更有效地合作。不同地点可以通过互联网相互连接,查看相同的信息。由于这种更高效的工作方式,我们预计可以节省 20-30% 的时间。”
使用云端 3DEXPERIENCE 平台也在提高正常运行时间的效率。 “过去,当我们使用基于文件的系统时,我们通常需要将数据从一个项目复制到另一个项目,”Yutaka 新技术验证办公室的 Mitsuhikio Ohtake 说。“复制的数据链接有时会中断,这可能会导致我们在测试装配线时出现问题——有时甚至会导致中断和停止。现在在云端进行,我们有单一数据源。我们可以访问准确的数据,这使得操作更加顺畅。数据存储访问和读写速度也变得更快。”
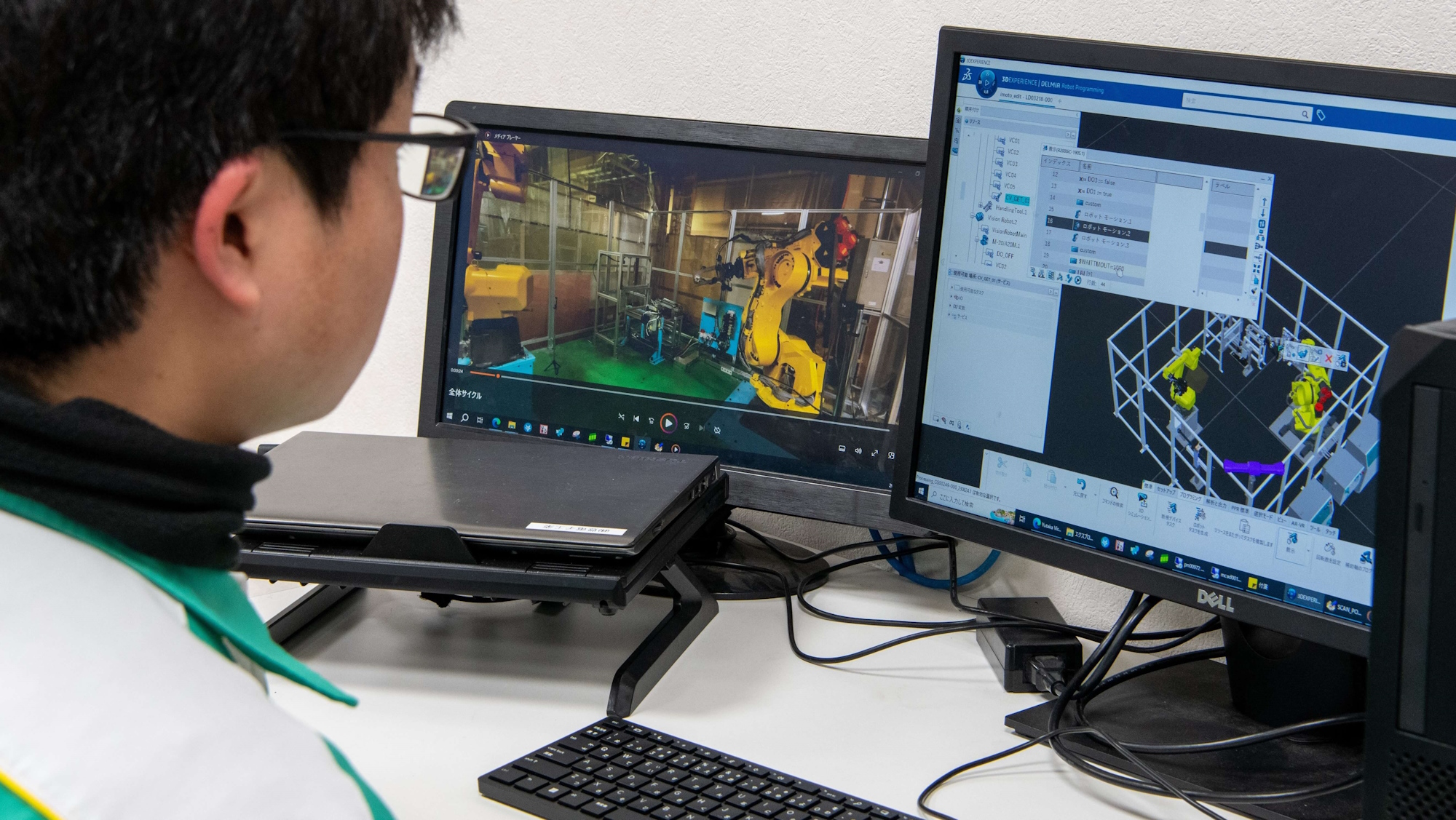
将虚拟调试投入使用
利用云端 3DEXPERIENCE 平台的虚拟调试功能的第一个机会出现在一个机器人展览会上,Yutaka 创建了一条生产线,可以用来展示机器人装配流程的潜力。如果没有虚拟调试,这通常需要 Yutaka 一整天的时间才能完成设置。然而,通过首先创建其机器人的数字复制品并仿真它们的行为和集成,安装只花了四个小时。
Ohtake 提供了一个例子:“如果机器人的手臂正在操作非常复杂的夹具,我们可以在 3D 虚拟模型中很容易看出是否有任何干扰,”他说。“以前,我们可能直到生产线建成才发现这类问题,所以我们不得不重新开始。”
该项目展示了 Yutaka 可以通过虚拟孪生提供的附加价值,通过在物理调试之前根据客户的需求配置工作质量、周期时间、空间布局和工作流。“通过在现场组装前预先验证可行性和节拍时间,可以减少物理测试,”Ohtake 说。“因此,我们将样机设计交付周期缩短了 50%。”
Yutaka 充分利用达索系统工具的功能后,有望进一步提高其运营和调试系统的可视化,同时在将来的项目中重用知识和过去的经验。
最终,Morita 认为,Yutaka 的专业知识和 3DEXPERIENCE 平台提供的能力结合起来,巩固了其在市场上的地位。“我们的优势在于我们与所有行业都有联系,可以根据所有行业的客户要求提出最新的机器人系统自动化,”他说。“随着各行各业数字化转型的推进,我们的优势将保持不变。作为系统集成商,我们可以并将继续结合最新的技术,例如 3DEXPERIENCE 平台,为我们的客户提供卓越的附加价值。”
常见问题
机器人作为一种装配自动化的手段,帮助大大小小的公司高效生产我们所见的各种产品——从消费品到工业装备。现在,人们可以使用协作机器人,人和机器可以一起工作。
机器人装配是一种自动化产品装配的方法,提升了效率和生产力。
工业机器人可以帮助搬运物料,执行重复性任务,例如拣选或装卸,甚至检查产品。
了解更多有关 Digital Equipment Continuity 行业解决方案体验的信息。
00:00 – 00:27
旁白:
精度。速度。质量。Yutaka Electronics 因其在机器人生产线构建方面的专业而得到客户信赖,无论是为汽车 OEM 厂商还是为航空航天与国防企业服务。
00:28 – 00:43
Takafumi Morita,Yutaka Electronics 总裁兼首席执行官:
我们公司成立于 1964 年,以机电一体化技术为基础。1979 年,我们在日本是最早进入工业机器人系统领域的企业之一,自那时起,我们一直作为整体系统集成商活跃在这个领域。
00:44 – 00:53
Yutaka Electronics 先进技术部总经理 Daisuke Matsuo:
根据客户的要求或规格,我们先评审该设备,然后进行设计,接着开始制造。
00:54 – 01:03
旁白:
Yutaka 现在在云端 3DEXPERIENCE 平台上进行虚拟调试,以便在实际生产线构建之前测试和验证客户的机器人生产线的组件。
01:04 – 01:24
Daisuke Matsuo:
通过将我们的流程与 3DEXPERIENCE 平台集成,数据实现集中管理,我们可以提前检查数据是否正确。这可以显著提高生产力,为我们节省了很多时间。
01:25 – 01:37
旁白:
这个平台支持 Yutaka 预先验证可行性,并确定合适的节拍时间。这减少了物理测试,并将样机制作交付时间缩短了 50%。
01:38 – 01:50
Yutaka Electronics 先进技术部主管 Daiki Sakakibara:
以前,机器人仿真仅包括机器人的运动。但现在,我们还可以监控执行器的运动,并对 AGV(自动导引车)的移动进行监控。
01:51 – 01:57
Yutaka Electronics 系统集成部副经理 Mitsuhikio Otake:
能够如此轻松地以 3D 和虚拟方式查看运动是一个很大的优势。
01:58 – 02:06
旁白:
使用基于云的 3DEXPERIENCE 平台,Yutaka 可以与客户共享数据,实现快速轻松的协作。
02:07 – 02:35
Takafumi Morita:
作为系统集成商,我们可以整合来自世界各地的最新技术,提供独一无二的附加价值。我们计划将这一做法持续下去。
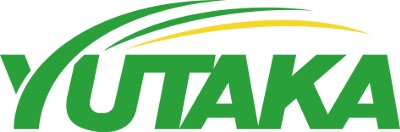
聚焦 Yutaka Electronics
Yutaka Electronics 是日本最大的系统集成商之一。公司拥有 700 多名员工,全天候运营,提供广泛的服务,不仅包括机器人系统和分布式控制系统的制造,还涵盖从前期设计开发提案到交付后的维护和售后服务的全面支持。Yutaka Electronics 在 7 个国家/地区设有业务部门,作为一家以开发为导向的系统工程公司,凭借其先进的技术专长和创新理念为全球客户提供强有力的支持。
欲了解更多信息,请访问: https://www.ytk-e.com/
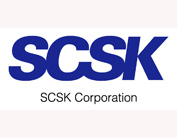
聚焦 SCSK
成立于 1969 年,SCSK 公司为日本乃至全球的公司提供广泛的系统集成服务。 SCSK 旨在成为 IT 服务行业的第一梯队,专注于五个战略业务领域:工业、金融、解决方案、产品和服务以及移动出行。