The Essentials of surface modeling explained
When designers want to create a realistic 3D model, they use a variety of computer aided design (CAD) techniques. Surface modeling is used to enhance a simple wireframe model or add detail to a 3D solid model and make it appear more textured and lifelike. Join us as we take a look at the essentials of surface modeling.
What is surface modeling?
Surface modeling is a mathematical technique used by CAD software to add more detail to a simple 3D solid model or wireframe model. It is a much more complex process than simple wireframe modeling but less involved than solid modeling.
As the name suggests, surface modeling is used to create surfaces. The technique allows the designer to flesh out a model’s exterior shapes and contouring. It can be used to create lifelike textures, depict smoothness, and show imperfections. Surface models can be seen from any angle in three dimensions, but unlike solid models, they can’t be split open to view internal workings.
Surface modeling is commonly used to create visual representations of products, mechanical objects, or organic shapes like humans or animals. Designers can create shapes that are wildly fantastic and do not need to conform to realistic geometries, mass, and thicknesses. It is possible to create a model just using surface modeling techniques, but generally, it will be used in conjunction with solid modeling.
Explore the surface modeling solutions from Dassault Systèmes
Designers and engineers across all industry sectors rely on Dassault Systèmes for sophisticated, intuitive, and powerful surface modeling solutions.
Surface modeling vs solid modeling, what is the difference?
Solid modeling is a complex technique that is used to create geometrically precise solid shapes in three dimensions. When creating a solid model, a designer needs to depict both the inside and the outside of the model.
While this is highly useful as it shows how a design operates internally and depicts its external features, the process of creating a solid model is highly complicated. Solid models must have clearly defined dimensions that are realistic and uniform. It is most often used to design engines, machinery, vehicles, and aircraft.
Surface modeling is a much more freeform style of CAD modeling. When using this technique, designers are only concerned with the exterior of the model. A surface model is just that – it’s all surface detail and is completely hollow inside.
With a surface model, designers can push and pull the shapes and contours of the model to create any form they want, regardless of how uneven or unbalanced it is. Surface modeling can be viewed as sitting between the simple process of creating a wireframe model and the more complicated process of building a solid model. Surface modeling is used for animations, video game characters, special effects, and for product and architectural visualizations.
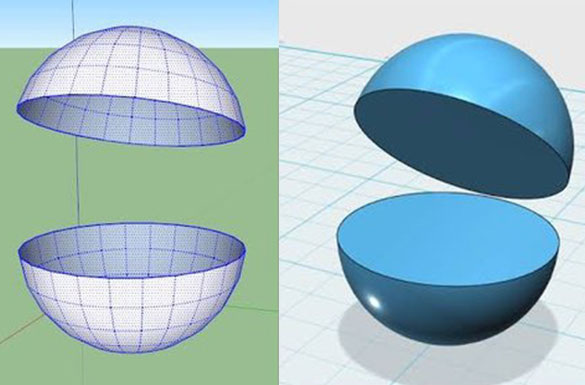
Different types of surface modeling?
When creating a 3D surface model, designers use a variety of methods. What types of surface modeling methods they use depends on the shapes they wish to create and the scope of the surface modeling software they are using. Common surface modeling methods include:
- NURBS
- Polygonal modeling
- Subdivision modeling
- Implicit modeling
NURBS(Non-Uniform Rational B-Spline) modeling
URBS modeling uses complex mathematical equations to create realistic circles, arcs, and 2D surfaces that are used to draw flexible, accurate, and highly lifelike 3D models.
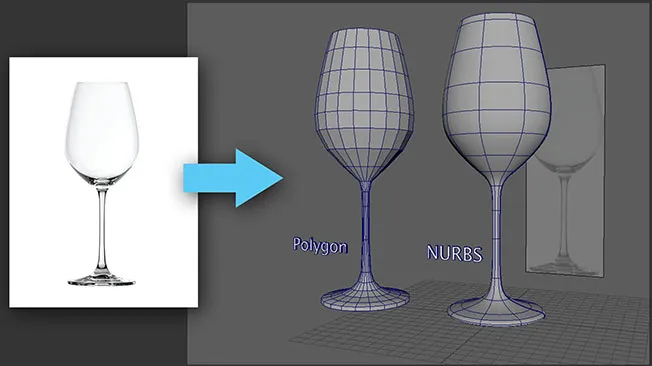
Polygonal modeling
The function of this software is to generate 3D structures using basic units called tris (triangles) and polys (polygons), which are two-dimensional shapes defined by their vertices and edges. This type of software is particularly suitable for situations where exactness or precision is not a primary concern.
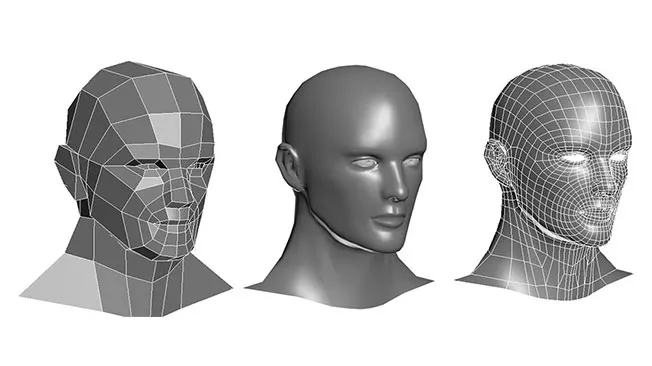
Subdivision modeling
In subdivision modeling, a designer will cut the polygons in a model down into even smaller numbers of components. This allows the designer to add more detail to a model and makes it appear smoother.
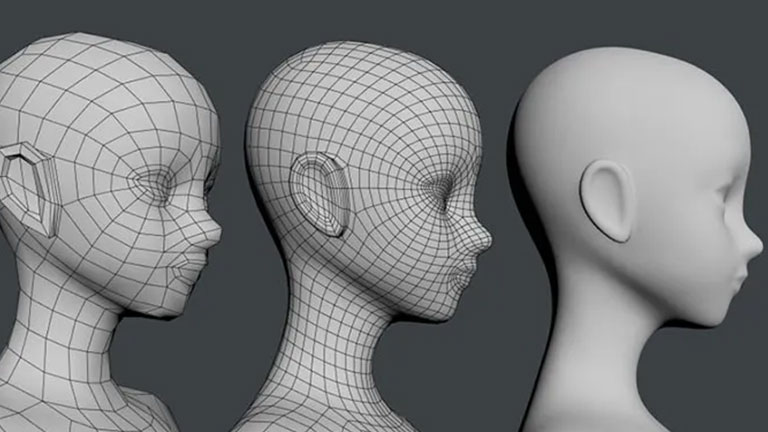
Implicit modeling
Implicit modeling is a feature where the software itself will define the dimensions of an object using mathematical equations. Implicit modeling can be used to save time when creating highly complex shapes.
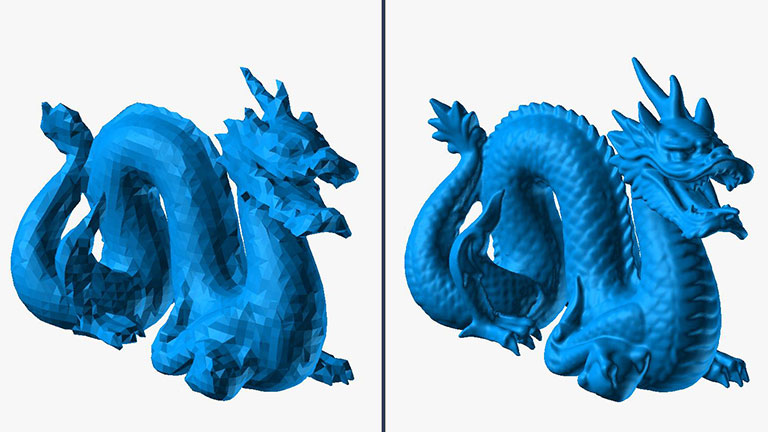
Browse all the Dassault Systèmes store applications
We feature in our store some of our best software to design, collaborate and innovate throughout the entire product lifecycle.
Content related to surface modeling
What is surface modeling used for?
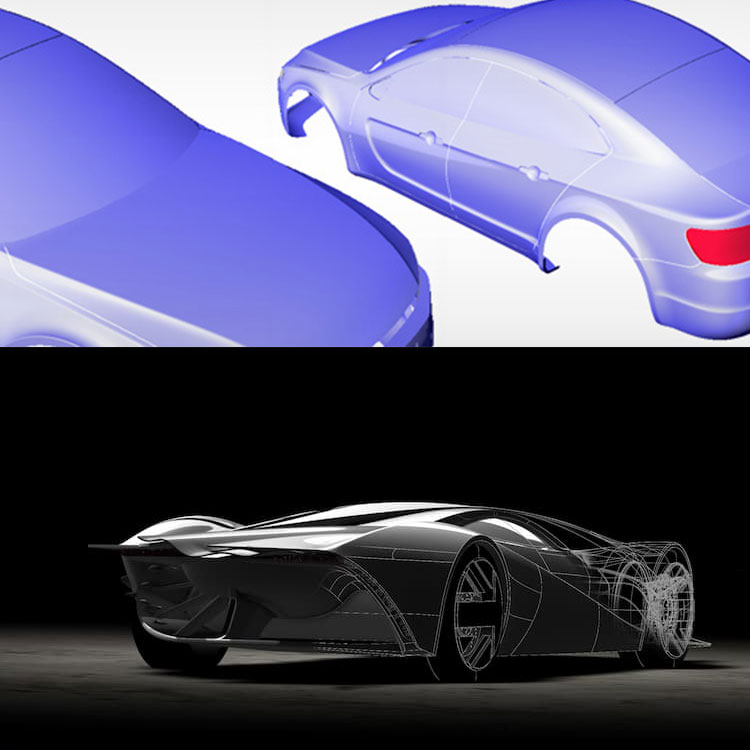
Surface modeling is widely used for product development and industrial design purposes. The freeform nature of surface modeling allows designers to create highly detailed representations of proposed products without having to build physical prototypes. Design faults can be analyzed and identified before a product reaches the manufacturing stage.
Automotive design uses surface modeling techniques to create what is known as Class A surfaces. The complex curvatures of automotive bodies can only be replicated in digital form using surface modeling techniques.
Aerospace design also requires complex curvatures and free-flowing shapes. Many aircraft designers use subdivision modeling methods to create aerodynamic configurations.
Surface modeling is widely used in the architecture and construction industries to provide realistic depictions of what proposed building projects will look like. As in the automotive and aerospace industries, architects use surface modeling techniques to design thin-walled structures.
Surface modeling is also a vital part of medical imaging. By constructing a surface model, researchers can track the progress of a disease and analyze the outcome of various treatment options.
What are the most common surface modeling techniques?
Several techniques are used in surface modeling software to create 3D models. Many of these techniques are automated commands.
What are the benefits of surface modeling?
Surface modeling allows for the creation of highly complex and lifelike organic shapes that would be difficult or impossible to create with solid modeling techniques. This feature has made it an invaluable tool for creating realistic models of objects for visualization. For this reason, you often find surface models used in product presentations as well as characters in video games and animations.
The malleability and freeform aspects of surface modeling make it ideal for creating ergonomic designs that fit the human body. It is often used for medical purposes such as designing dental implants or prosthetic limbs.
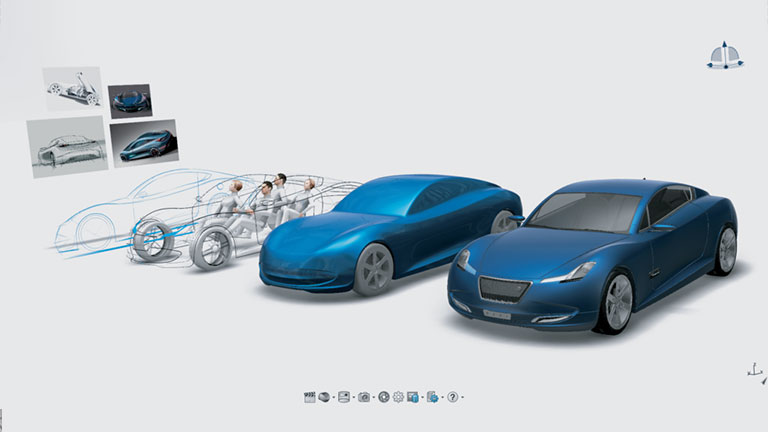
What are the drawbacks of surface modeling?
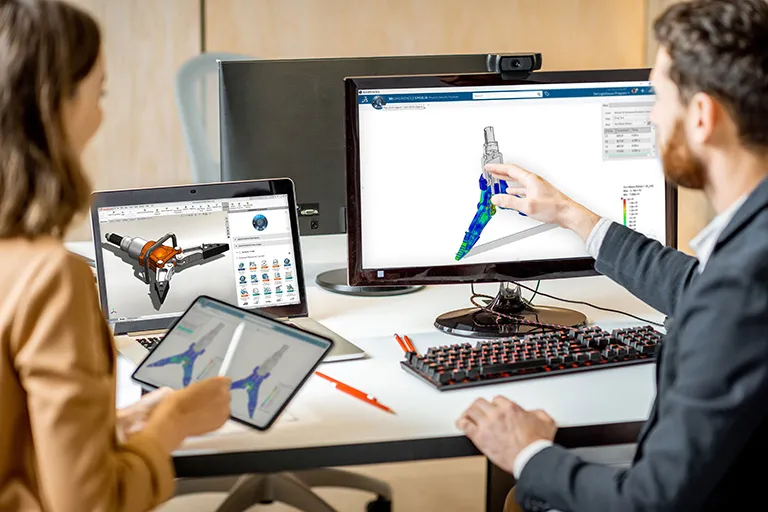
Surface modeling is not without its drawbacks and limitations. The complexity of surface modeling techniques and the high cost of surface modeling software can make it resource intensive and put it out of the reach of students.
Surface models cannot be split to show internal workings. They lack the internal structure and details necessary for manufacturing. So, while a surface model can be used for a basic presentation, it is not suitable as a guide for engineers.
Surface models are also quite difficult to modify or update once they have been created.
Explore Dassault Systèmes solutions
Discover the powerful browser-based modeling solutions from Dassault Systèmes. You can design whatever you wish, wherever you are with 3DEXPERIENCE.
Connecting data & people to foster innovation
The 3DEXPERIENCE platform on the cloud gives you access to a various set of applications that allow you to design, simulate, inform and collaborate on a project.
What is hybrid modeling?
Often, a designer finds that using just one modeling technique will not give them the results that they need. In such a case, a designer must use what is known as hybrid modeling.
Hybrid modeling is a technique where a designer will combine both solid molding and surface modeling techniques to create a 3D model. It can be used to create incredibly complex shapes that would not be achievable using either solid modeling or surface modeling methods alone. Hybrid modeling often involves sophisticated artificial intelligence and machine learning elements. Hybrid models are used in a range of advanced fields, such as robotics and natural language processing.
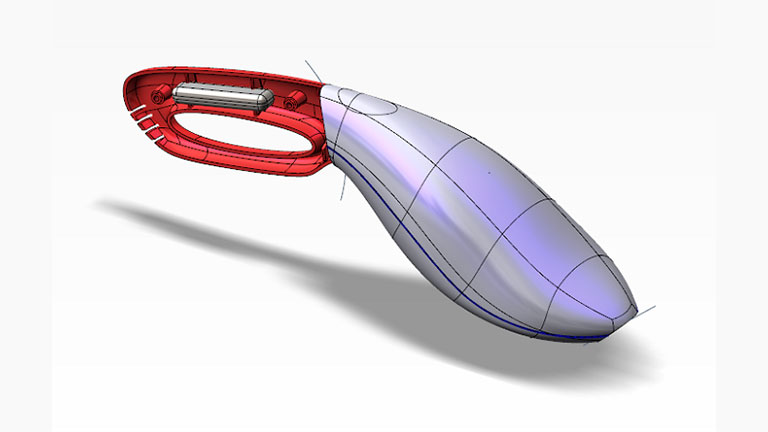
Surface modeling - Conclusion & Perspectives
Surface modeling is a highly valuable tool with a broad range of applications, from product design to architecture to art and entertainment. By using surface modeling techniques, designers can create lifelike shapes with highly complex organic curves and lines.
Surface models do not need to follow the strict geometric parameters of solid models, so a designer can let their imagination run free. The push-and-pull sculpting quality of surface modeling allows for enhanced design freedom.
When used in conjunction with solid modeling techniques, surface modeling enables the creation of incredibly complex 3D models. Advances in medicine, science, and engineering have all been made possible by the use of hybrid modeling techniques that combine the precision of solid models with the fluidity of surface modeling.
Mastering the complexities of surface modeling in CAD is an essential skill for any budding designer or engineer. Becoming proficient in 3D surface modeling requires the most advanced and intuitive surface modeling solutions available.
Why choose Dassault Systèmes for your surface modeling needs?
Experience real design freedom with the 3D Experience Platform
In today’s highly digitized world, professional designers need the flexibility to work from any corner of the globe at a moment’s notice. Traditional CAD software simply does not allow for this level of freedom. The 3DEXPERIENCE Platform gives designers and engineers the ability to work on designs and collaborate with colleagues at any time, on any type of device, anywhere in the world.
Powered by the latest cloud computing technology, the 3DEXPERIENCE Platform provides a digital environment where users can share and store files and communicate with clients and co-workers safely and securely.
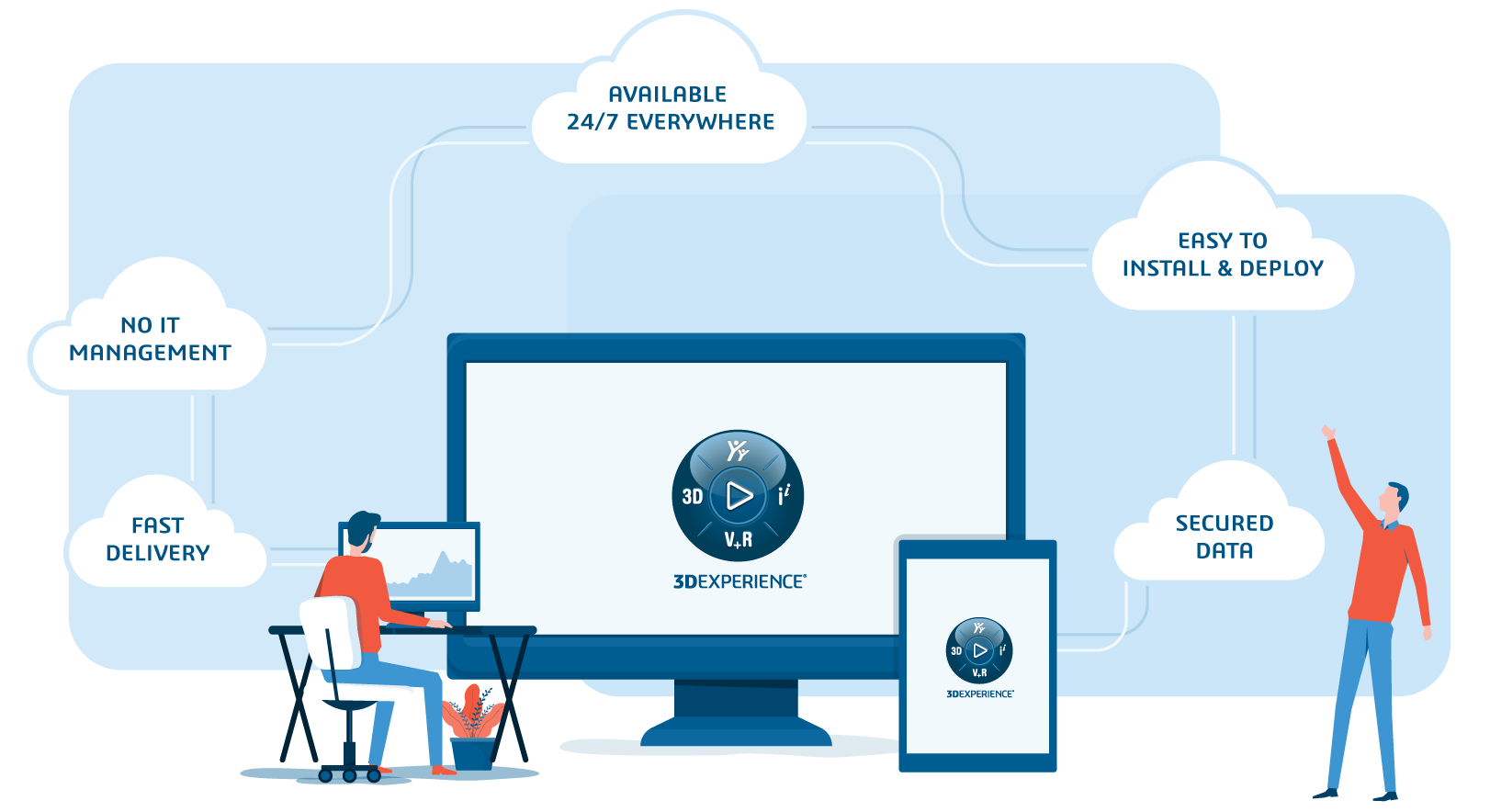
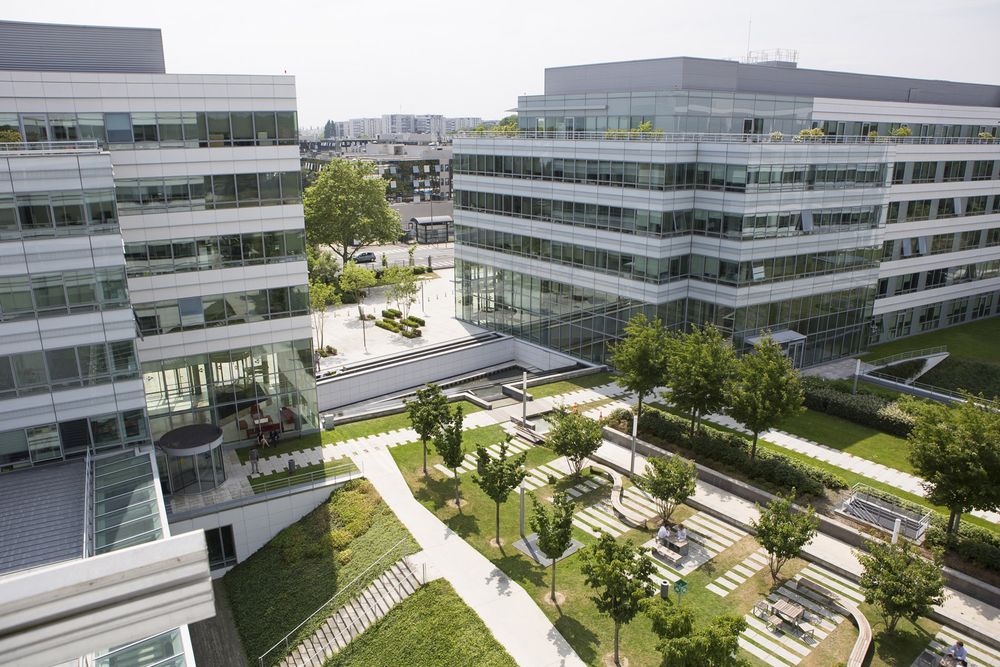
CAD expertise and experience you can rely on
Dassault Systèmes has been at the cutting edge of CAD development for more than four decades. Designers and engineers from sectors as diverse as the construction, automotive, and aerospace industries turn to us for solid modeling and surface modeling solutions they can rely on.
You can discover the entire range of Dassault Systèmes roles via our online store. Explore highly sophisticated, innovative, and intuitive software from 11 different brands. With Dassault Systèmes, you can go beyond expectations and reach new levels of creativity.
Explore inspiring content
Frequently asked Questions
Solid models must be geometrically precise and can depict the inner workings of an object while surface models only show the exterior and do not have to follow set parameters.
No, surface modeling alone is not sufficient to create highly complex shapes with inner workings.
The SOLIDWORKS surfacing roles are used widely throughout many industry sectors to create detailed, realistic 3D surface models.