How DFXenhances product development
Design for Excellence, (also known as DFX or Design for X), is a systematic method of applying certain principles and criteria to ensure quality during the product design stage. In this article, we explain exactly how the DFX methodology works, look at the different types of DFX, and analyze why DFX is such a crucial part of the product development process.
What is Design for Excellence - DFX?
The Design for Excellence methodology involves systematically scrutinizing every aspect of the product development process from the design stages to the manufacturing phase. With every task they undertake, stakeholders must strive towards achieving a clear objective. In this way DFX helps to eliminate errors, reduce waste, and ensures efficiency and quality throughout the entire development process.
The X in DFX stands for Excellence, but this concept can cover any number of parameters. X can represent any objective that a design team wishes to accomplish. You can, for example, Design for Manufacturability, for Reliability, Quality, Sustainability, or Ease of Assembly. You can even substitute X with a more precise goal, such as Design for Kickstarter. Whatever parameter you set for X will provide your team with a clear objective to focus on.
Discover the DFX solutions from Dassault Systèmes
Achieving your design goals requires more than just the right DFX methodology. You also need the right CAD and project management tools. Here are the Dassault Systèmes solutions available on our Store.
How and where does the term DFX appear?
The first time the terms Design for Excellence and DFX were formally used and recorded was in 1990. Remarkably, two different authors wrote two different papers and submitted them to two different industry bodies at the same time.
The terms Design for Excellence and DFX first appeared in two papers submitted to the Keys Conference and the AT&T Technological journal respectively. Even more surprisingly, it seems that the two authors were not aware of each other at the time they wrote and submitted the papers.
This shows that the design and manufacturing industries were both independently moving toward the philosophy of DFX. With the adoption of Lean manufacturing and Lean management techniques becoming more widespread throughout the 1980s, the development of DFX as a concept was inevitable.
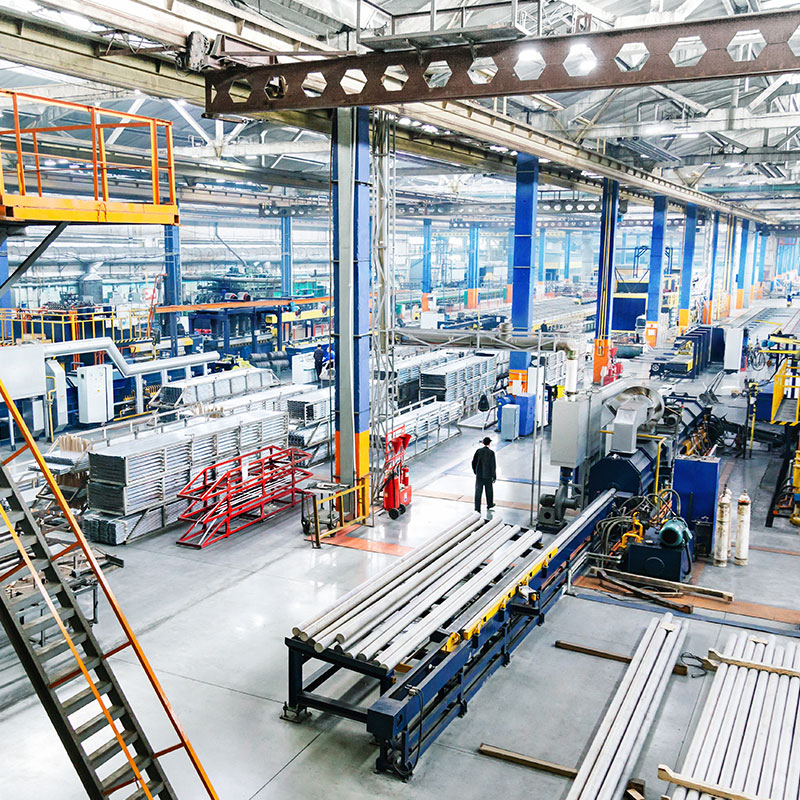
What is the difference between the traditional product development process and DFX?
The DFX methodology represents a complete break from traditional methods used in product development and manufacturing. Historically, using a traditional approach the design team is separated from the manufacturing process and the supply chain. Using a DFX methodology, stakeholders at all stages are required to communicate, collaborate, and cooperate to achieve the goal of X.
Looking at how the traditional engineering process is different from a DFX process can shed some light on why so many companies are now choosing to implement Design for Excellence systems.
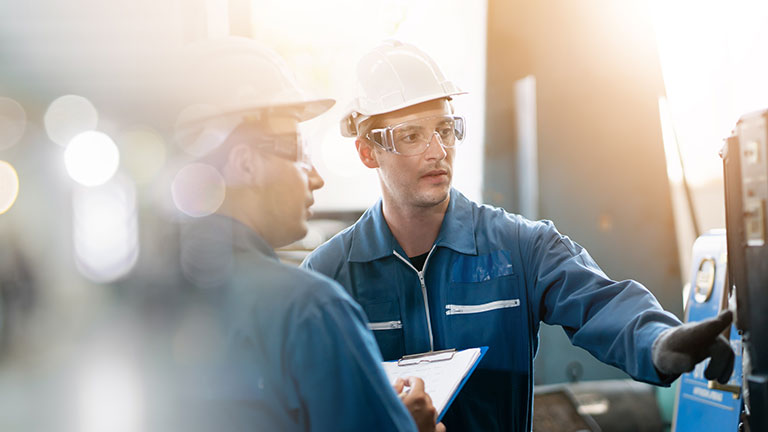
The traditional engineering process
The traditional engineering process begins with identifying a problem by observations, surveying, experimentation, or a mixture of all three. The team will then research the problem and try to come up with solutions. The solutions are evaluated and the most optimum solution is selected.
The design is then made based on this option. A prototype is created which is then put through various tests to ensure it can solve the original problem. Refinements and improvements are made before the product is released for production.
How does DFX work and how the process differs from the traditional engineering process
The traditional engineering process is a linear progression from one step to another. In a traditional process, issues are detected after a design has been made. DFX aims to reduce waste by eliminating problems as they occur. DFX concentrates on resolving issues during the design stage, not afterward.
With DFX methods, simulations are used instead of physical prototype tests. Design iterations are done before production is set in motion. While traditional engineering processes require the use of several tools, DFX seeks to use as few tools as possible.
With a traditional engineering design, functional requirements are paramount. Using DFX methods, the product life cycle is the main focus. DFX also allows for collaboration between teams at every stage of the process.
The design team needs to communicate and collaborate with suppliers and manufacturers during the initial stages of the process to ensure that the optimum design is reached with as few iterations as possible.
DFX can greatly reduce time to market, eliminates waste, and improves productivity. DFX uses Lean manufacturing and design thinking to focus on continuous improvement. This leads to better employee engagement across all levels, encourages supplier collaboration, and enhances product usability, product safety, and, ultimately, customer satisfaction.
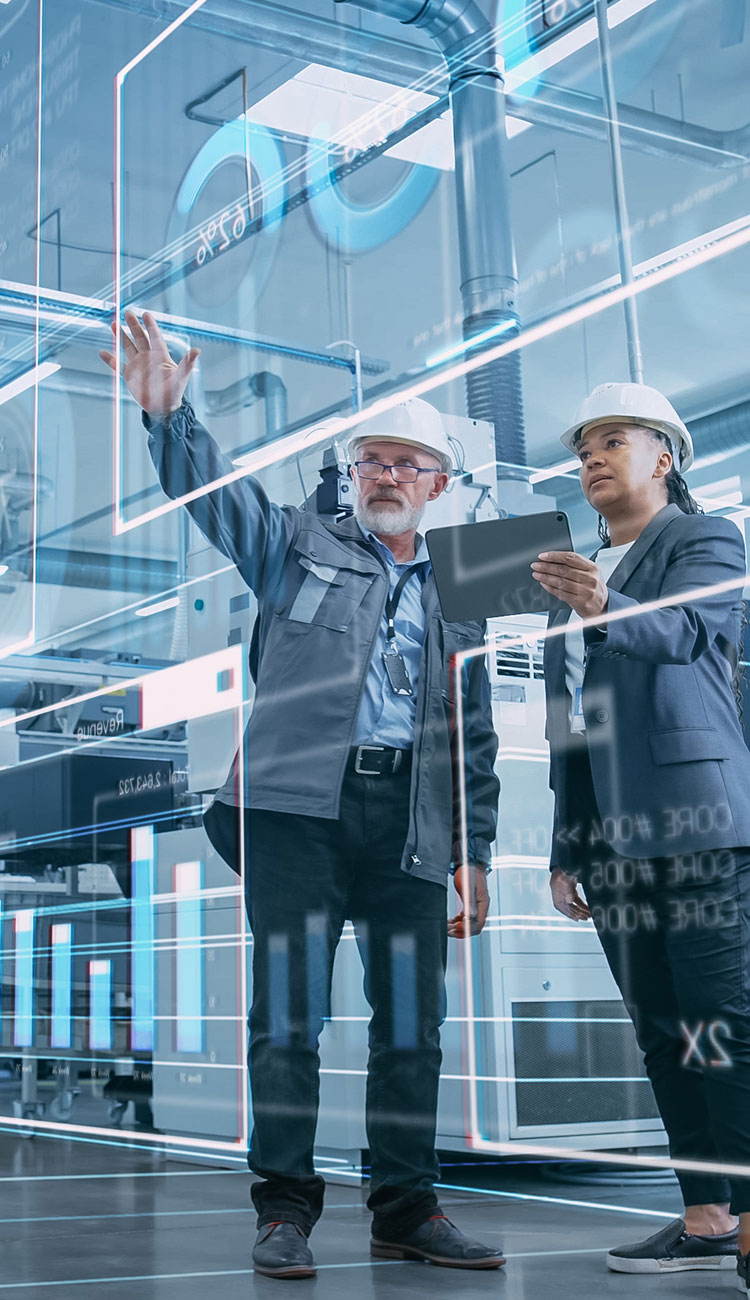
The different types of DFX methodologies
As we noted before, the X objective in DFX can be set as any type of parameter that you like. DFX acts as a general philosophy that can be used to enhance productivity, eliminate waste, reduce environmental impact, lower costs, and enhance the robustness, safety, and overall quality of a product.
Experts have written papers outlining 48 different ways to implement DFX methodologies. We’ll now take a short look at some of the most common DFX approaches.
What are the benefits of DFX for businesses and consumers?
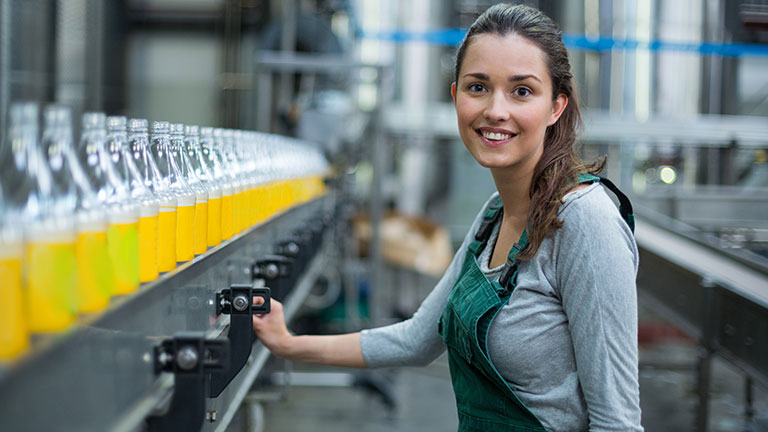
DFX approaches have considerable benefits for both companies and customers. By reducing waste and focusing on efficiency at every stage, companies can shorten the time to market and concentrate on fulfilling customer needs.
This results in higher quality products that are available sooner, have less impact on the environment, are safer, more robust, and are tailored to deliver exactly what the customer expects of them. DFX techniques also ensure regulatory compliance which enhances quality, reduces warranty costs, and prevents product recalls.
Browse all the Dassault Systèmes store applications
We feature in our store some of our best software to design, collaborate and innovate throughout the entire product lifecycle.
Content related to DFX
What is the connection between DFX and Lean Six Sigma?
Lean Six Sigma is a team-based Lean management technique. Like all Lean techniques, Six Sigma aims to eliminate waste and enhance efficiency. It focuses on achieving optimal output quality by reducing product defects.
Lean Six Sigma concepts can be built into a DFX methodology. This approach is known as the Design for Six Sigma method or DFSS. DFSS uses a range of statistical tools to determine what the needs of customers are and what the goals of the business are. Using DFSS, customer needs must be considered when making any decision at any stage of the product development process.
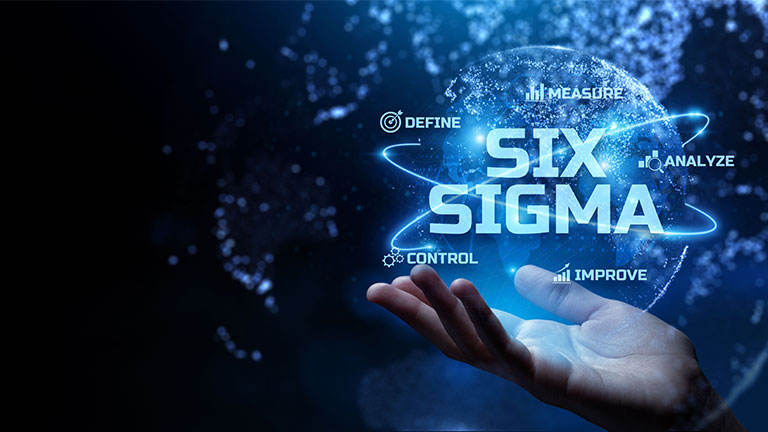
DFX - Conclusion & Perspectives
Creating a quality product that is efficient, reliable, and durable requires a deliberate and methodical approach to the design phase. Design for Excellence, or DFX, is a methodology that was developed to specifically address the issues of waste involved in traditional engineering processes.
DFX aims to provide a method where you can optimize your products during the initial stages of their development. Using the DFX methodology means that you can avoid having to make expensive and time-consuming changes during pre-production or even at the post-production stage.
Implementing a DFX system requires a significant change of mindset within a company. All team members across all levels must communicate and collaborate at every stage of the product development process. Achieving DFX goals also requires the use of sophisticated CAD software and technology.
Why choose Dassault Systèmes for your DFX needs?
Enhance collaboration with the 3DEXPERIENCE Platform
Achieving the goals of DFX requires employees across all levels of a company to be in constant communication. With today’s fragmented remote working models, this can be difficult to achieve. The 3DEXPERIENCE is a cloud based digital environment where colleagues can collaborate and work together securely and safely.
Easily accessible using any type of internet-enabled device, the 3DEXPERIENCE Platform allows team members to share and store files or work on projects simultaneously at anytime, anywhere on the planet.
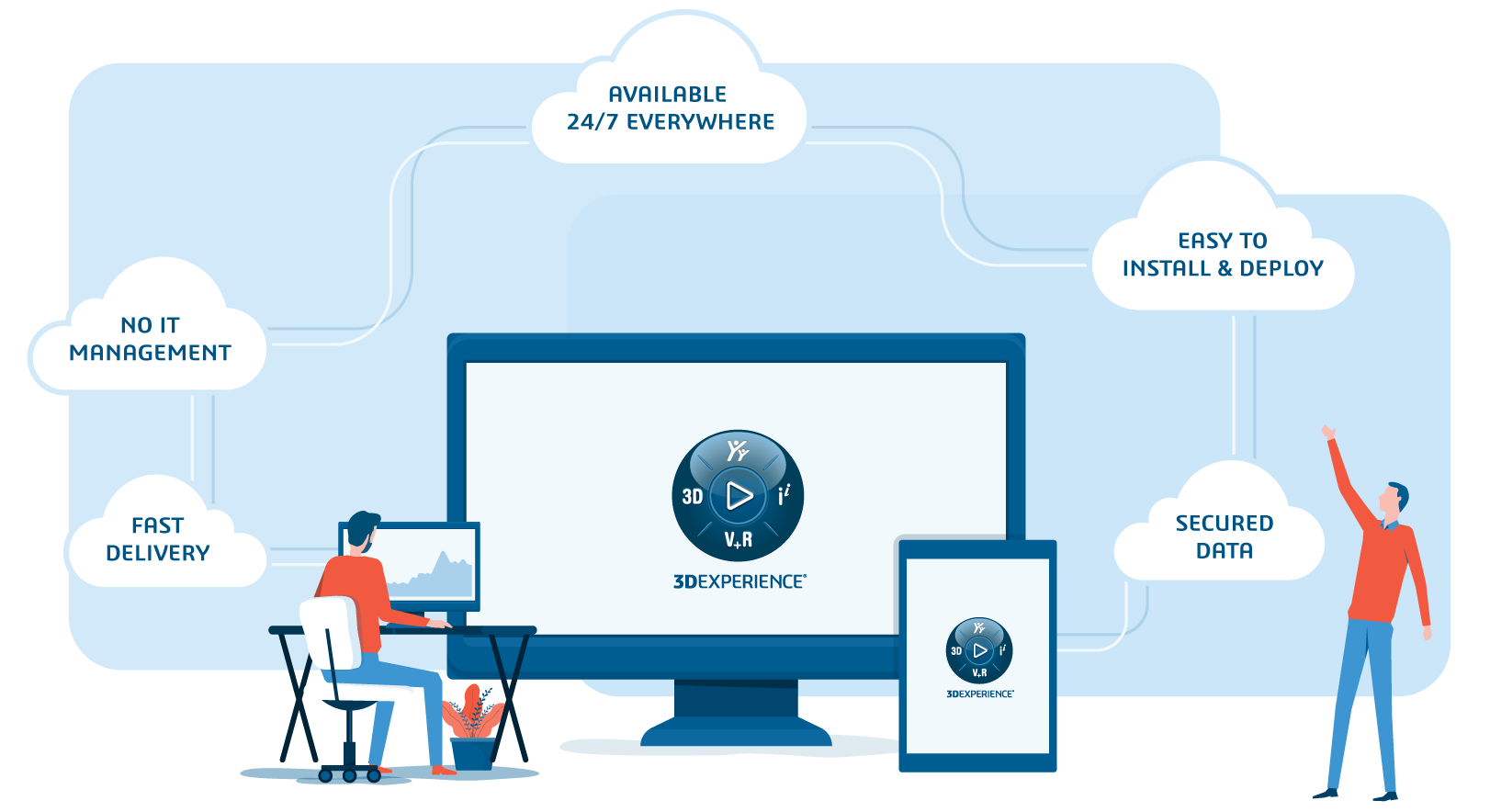
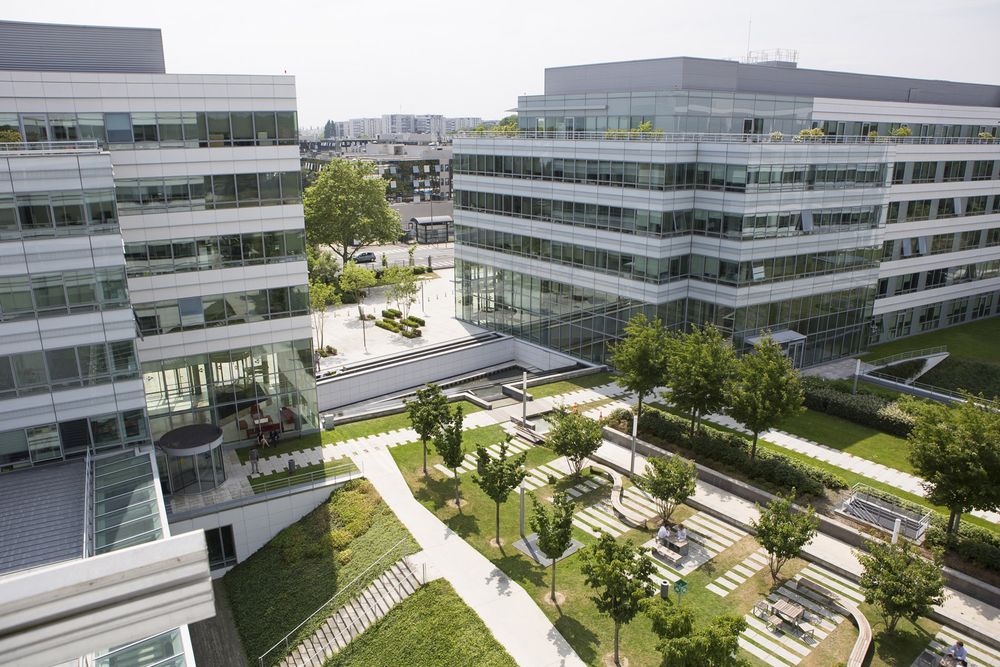
More than 40 years of experience
Partner with a developer that has the expertise and the experience to help you reach and exceed your goals. Dassault Systèmes has been providing companies across a wide range of industry sectors with powerful, innovative, and effective CAD and PLM tools for more than four decades.
From our beginnings in the French aerospace industry, we are now a multinational company known for developing cutting-edge software. We take pride in providing the exact tools which managers, designers, and engineers need. With Dassault Systèmes, you can discover better ways to create and innovate. Explore our roles today.
Explore inspiring content
Frequently asked Questions
DFX methods focus on reducing waste at every stage of the product development process so overall costs are much lower than traditional engineering and manufacturing processes.
DFX increases efficiency and productivity, so products can reach markets in less time and for less cost.
DFX techniques ensure that the main X objective is the focus of every stage of product development and manufacturing process. If X is defined as designing for the circular economy, then stakeholders across all levels will work towards this goal.
Design for Excellence (DFX), also referred to as Design for X, is a variable term in product development where 'X' signifies a multitude of characteristics. These characteristics or traits can include manufacturability, cost, quality, reliability, and more. The 'X' provides flexibility in the product development process, allowing for the optimization of a specific aspect of the design.
The 'X' in DFX could be applied to overall manufacturing processes that produce your products, such as 3D printing, CNC machining, sheet metal, and more. It provides clear targets or objectives, thereby enhancing the power of design in outcomes.
DFX plays a crucial role in optimizing the product development process. Its importance lies in the fact that it offers a systematic approach to improve various aspects of a product - from manufacturing to cost, and from reliability to quality. By focusing on a specific 'X' factor during the design phase, DFX allows for a targeted optimization strategy. This not only enhances product quality but also reduces time-to-market and overall costs. It enables designers to consider factors such as manufacturability, testability, and reliability upfront, thereby avoiding costly redesigns later. Thus, DFX contributes to the creation of high-quality products that meet customer satisfaction while reducing manufacturing and service costs.