- Germany-based technology supplier’s employee cafeterias at all sites have been closed since March 2020 due to the COVID-19 pandemic
- SIMULIA applications powered by the 3DEXPERIENCE platform enabled GEA to examine how aerosols can spread within the cafeteria at its largest site in Oelde and visualize safety scenarios
- Simulation revealed unexpected insights into potential virus concentration that will help GEA implement strategies to ensure employee health and safety
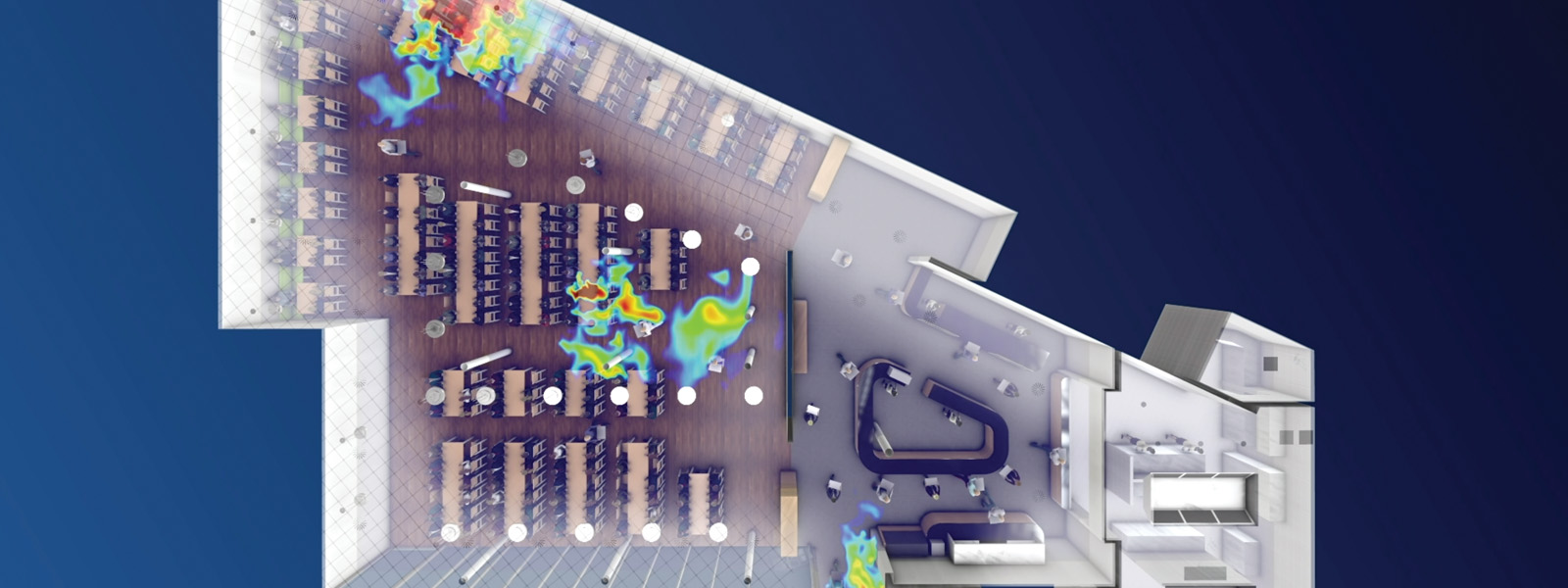
VELIZY-VILLACOUBLAY, France — September 22, 2020 — Dassault Systèmes (Euronext Paris: #13065, DSY.PA) today announced that GEA, one of the world’s largest technology suppliers for food processing and a wide range of other industries, used SIMULIA applications powered by the 3DEXPERIENCE platform to simulate the airflow in its Oelde, Germany employee cafeteria, which has been closed since March 2020 due to the COVID-19 pandemic, and gain insights on how to safely reopen it for 1,900 employees.
Understanding that the coronavirus can spread through droplets in the air, GEA wanted to examine the spread of aerosols in its cafeteria and visualize different safety scenarios as part of its “Back to Work” initiative to fully reopen all sites. It worked with Dassault Systèmes to build a 3D virtual twin of the cafeteria with parameters that included people infected with the virus coughing and sneezing, to simulate particle flow behavior throughout the space. GEA was able to experience how the virus could spread through the air as well as contaminate surfaces like plates, trays and tables. The virtual twin also revealed unexpected areas of high virus concentration.
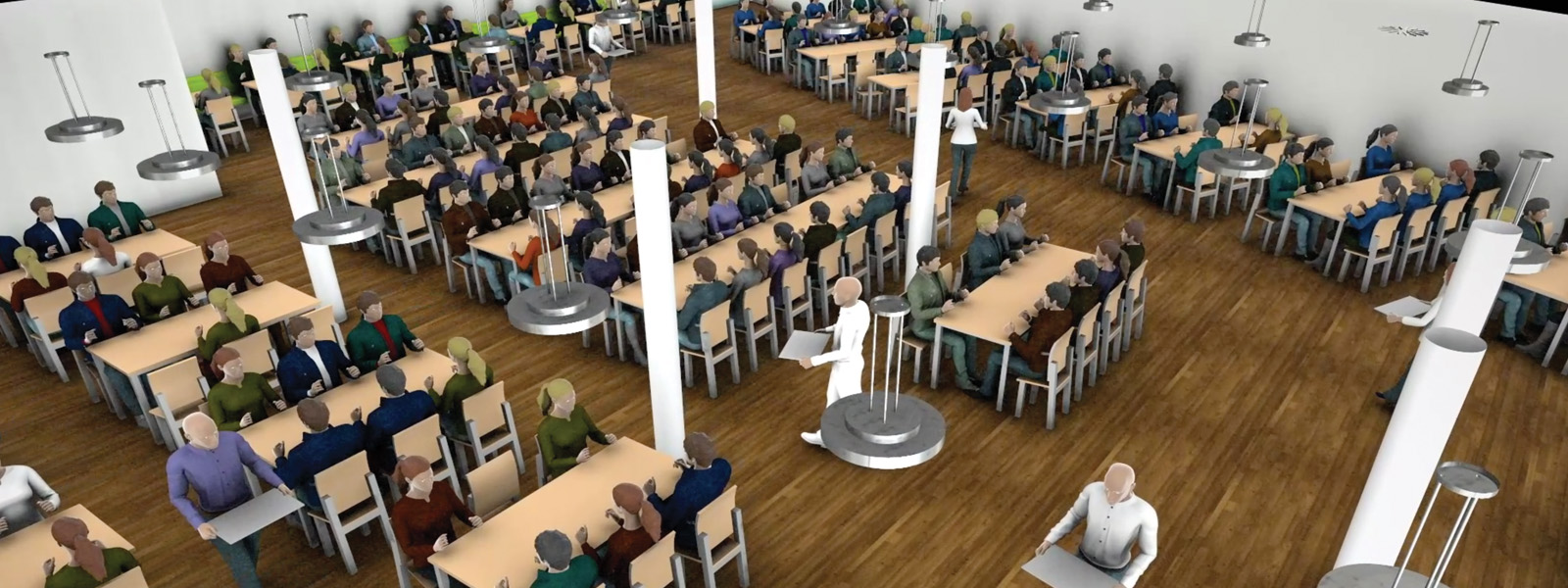
GEA is now using the simulation results to identify and implement an effective risk management strategy for a safer cafeteria environment. This includes altering entrances, exits and seating layouts, separating the cafeteria’s kitchen from its catering area, modifying the ventilation system, and adopting additional safety measures that protect kitchen staff.
“Simulation provided us with a valuable learning experience and will play a major role in our decision-making as we plan to reopen our cafeteria, which is an important gathering space for all our employees,” said Erich Nitzsche, Vice President Engineering Standards & Services, GEA. “The results from our collaboration with Dassault Systèmes exceeded our expectations and showed a different story from what we were expecting. Thanks to simulation, we can be more purposeful in our thinking as we solve problems to ensure the health and safety of our employees and reduce the negative impacts on our business. Selecting Dassault Systèmes was a winning initiative for us.”
GEA plans to share videos showing the simulation results to employees, to clearly communicate why and how new measures were taken, and technology’s role in this strategy.
“Virtual worlds revolutionize our relationship with knowledge and open up tremendous possibilities,” said Klaus Löckel, Managing Director, EUROCENTRAL, Dassault Systèmes. “Our SIMULIA applications reveal the invisible by representing the time and space of a behavior that evolves in its environment. GEA can understand and act on this behavior in response to the coronavirus crisis with a program that prioritizes employee well-being.”
About Dassault Systèmes
Dassault Systèmes is a catalyst for human progress. Since 1981, the company has pioneered virtual worlds to improve real life for consumers, patients and citizens. With Dassault Systèmes’ 3DEXPERIENCE platform, 350,000 customers of all sizes, in all industries, can collaborate, imagine and create sustainable innovations that drive meaningful impact. For more information, visit: https://www.3ds.com