Lean Manufacturing: Better Manufacturing Visibility, Lower Operational Costs
With Lean manufacturing, businesses can drive long-term growth by adopting a mindset of continuous improvement.
Why Does Lean Require a Change in Mindset?
Lean manufacturing addresses one of the most prevalent byproducts of any supply chain: Waste. This selling point has gained a deeper significance in our post-pandemic world, as manufacturers look for ways to become more resilient, improve their operational efficiencies, cut costs and reduce the impact of disruptions.
While supply chains are under pressure to become more optimized and efficient, manufacturers are trying to achieve this in various ways, from cutting waste to improving collaboration and optimizing costs.
Lean production methods such as just-in-time production (JIT) and autonomation have helped manufacturers improve the efficiency of their operations, to varying degrees of success. Increased efficiency translates into more profitability and higher quality products for consumers and consistent on time, in full (OTIF) delivery levels.
Make Lean Work for You
Overcome your operational challenges and make Lean work for you. Watch our exclusive webinar and find out how you can leverage the virtual world to improve collaboration and drive sustained manufacturing excellence.
Unfortunately, the current way of working for many companies impedes their ability to achieve continuity, particularly during times of extreme disruption. This can lead to inefficiencies, ultimately resulting in value being left on the table.
Some of the existing challenges that stand in the way of Lean thinking include:
Organizational barriers
Top-down processes disempower and stifle teams that could otherwise add more value. As a result, teams lack good working relationships and tend to work in siloes. They also often lack the structure and learned behaviors to analyze problems, identify waste and ensure corrective actions are assigned.
Lack of outcome-oriented structures and processes
Many teams are disconnected; when they meet, their time is often wasted, lacking focus on what is important. Information is also disparate and not presented in a way that can steer discourse towards the desired outcome.
What Makes a Lean Initiative Successful?
Despite its popularity and wide adoption among businesses, not all implementation of Lean principles achieve the same success rate. The average success rate of Lean initiatives is less than 10%. Why is there such a wide gap between expectations and reality?
From our experience of empowering our customers with the 3DEXPERIENCE® platform, Lean initiatives deliver on the promised value when the following criteria are fulfilled:
Continuous enforcement of service improvements
Lean initiatives succeed when its enforcement is embedded directly into the manufacturing processes through automated directed manufacturing, reviews and signoffs. Employees can then be guided through new procedures, reinforcing new behaviors until they become habits. Stakeholders must also provide the proper resources and support towards implementing a Lean initiative that will stand the test of time.
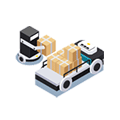
Complete visibility of the supply chain
Manufacturers must have access to digital platforms that provide enterprise-wide visibility and management. It should cover all aspects of production, including quality, compliance and maintenance. Real-time visibility of operations enables quick decision-making and improves overall operational control. This capability is essential when dealing with critical disruptions to the supply chain.
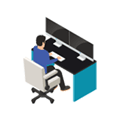
Measurable metrics
Measuring the right key performance indicators is essential to successful continuous improvement initiatives. These metrics need to be standardized in its definition, measurement and reporting, so they mean the same thing across every shop floor in the enterprise. Some of the more common measurable metrics include capacity and availability, labor efficiency, quality, inventory turns and value-add time. Investing in these metrics at the beginning of the implementation process will pay dividends down the line.
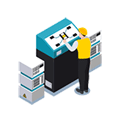
Implementing Lean With the 3DEXPERIENCE Platform
Our customers report immediate benefits by fulfilling these criteria through the 3DEXPERIENCE platform.
"More than 85% of teams feel more involved, engaged and have better access to information."
These benefits lead to:
- More operational problems solved
- Increased innovation and ideation
- Improvement opportunities in every meeting
Manufacturers can also continuously monitor and verify the enforcement of Lean initiatives, empowering teams to embrace constant improvement as a standard operating procedure.
With the 3DEXPERIENCE platform, our customers can take a highly detailed and methodological examination of their business practices and streamline local plant floor processes and material flow across the enterprise. As a result, they can reduce operating, recall and warrants costs, achieve lower inventory levels and hit a lower cost-to-quality ratio.
There is now a powerful and intuitive way to put Lean principles into action at every opportunity; it's time to design supply chains for efficiency and success — with the 3DEXPERIENCE platform.
Read our top articles on Operational Optimization
Explore our Industry Solution Experiences
Learn more about how our industry solutions can help you to achieve your professional ambition and business objectives