Novares DELMIA 생산 계획과 일정을 활용합니다.
Novares는 전 세계 자동차 산업의 요구 사항을 충족하는 포괄적인 솔루션 공급업체입니다.
우리는 계속 진화합니다. 자동차 산업에서 시장은 매우 빠르게 변화합니다. 우리는 모로코, 슬로바키아, 루마니아 및 중국에 새로운 공장을 설치하여 유기적인 성장 단계에 있습니다. DELMIA 솔루션은 우리가 배치할 공장 전체 DNA의 일부가 될 것입니다.
고급 플라스틱 사출 기술을 사용하여 Novares는 사용하기 쉽고 인체공학적이며 경제적인 현재와 미래 자동차에 내장될 하이테크 제품을 설계합니다. 전문 지식은 컴포넌트의 설계, 제조 및 조립과 고급 시스템의 통합을 포함합니다. 항상 자동차 제조업체에 더 많은 가치를 제공하도록 설계된 이 솔루션은 운동학, 메카트로닉스 및 여러 기능을 사용하는 복잡한 메커니즘을 갖추고 있습니다.
Novares 그룹은 차량의 자율성과 연결성 요구 사항을 충족하는 사출 플라스틱 부품을 설계, 개발 및 제조합니다. 그룹의 사업 운영은 엔진, 내외부 차체 범위를 포괄하며 복잡한 시스템과 메커니즘을 포함합니다. Novares는 Peugeot-Citroën, Dongfeng, Renault-Nissan-Dacia, Ford, Fiat Chrysler, Toyota, General Motors, Jaguar Land Rover, BMW, SAIC 및 Volkswagen과 같은 제조업체와 Yanfeng Johnson Controls, Faurecia, IAC, Continental 및 Visteon과 같은 공급업체에 자동차 장비를 제공하는 세계적인 리더로 자리잡고 있습니다. 2016년 프랑스에 본사를 두고 있는 Novares 그룹은 12억 유로의 조정 수익을 올렸습니다.
매우 다양한 공정을 위한 7가지 제품 라인
- 엔진 구성요소 (물, 오일 및 공기 처리, 음향 및 공기역학 관리 및 탱크)
- 베젤 및 클러스터(라디오 및 공조 어셈블리, 계기판)
- 통풍구 및 장식용 트림 (모든 유형의 통풍구, 조명 여부, 장식 부품 및 컵 홀더와 같은 작은 메커니즘)
- 인테리어 및 차체 트림(트렁크 트림, 대시보드 컴포넌트, 루프 콘솔 및 휠 아치 플레어링, 음향 및 공기 역학적 부품 및 블랙 파츠)
- 핸들(내부, 외부 및 연료 도어)
- 외부 페인트 및 표면(페인트 및 장식 부품, 블랙 파츠, 루프 바)
- E-파워트레인 부품 (전기 및 냉각 시스템) 이러한 제품 라인에 따라 프로세스가 매우 다릅니다.
DELMIA Production Planning & Scheduling 솔루션은 Novares 제조 제약 조건에 대한 응답입니다.
Novares는 역동적이고 경쟁적이며 끊임없이 변화하는 자동차 시장-보다 광범위한 다양성과 SKU, 증가한 세분화와 복잡한 흐름-에서 운영됩니다. “시장 요구 사항과 고객 요구 사항을 넘어서는 컴포넌트와 시스템의 성능을 향상시키는 민첩성, 응답성, 고객 서비스 역량은 우리 비즈니스와 그룹 성장에 있어 매우 중요합니다. 우리의 목표는 공장에서 생산을 보다 잘 관리하고, 린(Lean) 제조 원칙으로 재고를 최소화하려는 고객의 실질적인 요구에 보다 잘 대응하는 것입니다. DELMIA의 구현은 이러한 맥락에서 완벽하게 들어맞습니다.”라고 Frédéric Marcotte는 말합니다.
제조의 관점에서: “Master Production Scheduling은 특히 고객 수요의 수준 측정과 전방의 확실성을 개선하기 위한 우리의 역량 관리에 필수적인 연결 고리입니다. 우리는 또한 제품과 프로세스의 다양성과 관련된 복잡성을 고려해야 합니다. 각 제품에는 특정 프로세스가 필요합니다. 공장은 이러한 모든 제품과 프로세스를 새로운 고객 요구 사항에 빠르게 적응할 수 있는 이기종 제조 환경에 통합해야 합니다.”
DELMIA Production planning & Scheduling 구현의 주요 목표
Marcotte에 따르면 팀은 새 솔루션에서 다음과 같은 6개의 주요 목표를 확인했습니다:
- 생산 제약 조건에 따라 개발되기 때문에 현실적이고 실행 가능한 일정을 생성할 수 있어야 합니다: “우리는 다른 표준 솔루션을 사용합니다. 따라서 일정의 신뢰성을 높일 수 있는 도구가 필요했습니다.”
- 보다 안정적인 리드 타임으로 길어진 수평 스케줄링 수립: “자재 및 부품 공급을 검토하고 개선하여 전체 공급망, 특히 공급업체에 대한 이러한 수준의 신뢰성을 확장하려면 며칠에서 몇 주가 소요됩니다(재고 감소, 재고 부족 감소, 예외 선적 감소).”
- 자동화된 단일 루프 계산을 통한 시간 절약: "우리는 지루하고 동기화되지 않은 단계를 피하고 계획에 관련된 모든 사람들의 시간을 절약하기 위해 계산이 완전히 자동화되기를 원했습니다." 확보된 시간은 중기역량 계획 분석을 위한 리소스를 할당하는 데 사용됩니다.
- 스케줄에 대한 조감도 확보 만일의 경우 작업 주문을 시뮬레이션하고 재조정하는 기능: “올바른 결정을 내립니다.”
- 제약을 고려하여 전환 시간을 최적화할 수 있습니다.
- 일정을 생성하는 데 필요한 핵심성과지표(KPI), 플래그 및 경고를 통해 정보를 중앙 집중화하고 공유하는 데 사용할 수 있는 완전한 도구를 갖춥니다.. "모든 사람이 공유하는 단일 도구 및 단일 정보 소스."
DELMIA Production planning & Scheduling를 통해 기록된 주요 이점
• 시각화 개선. 이 도구는 매우 시각적이어서 의사 결정을 용이하게 합니다. "우리가 보유했던 것과 비교할 때 의사 결정이 훨씬 빠르고 효율적이라는 것은 의심의 여지가 없습니다."
• 스케줄 제작에 소요되는 시간을 절약하고 기대감을 높였습니다. 단기 일정 관리에 소요되는 시간을 절약하여 중기 일정에 더 많은 시간을 할애할 수 있습니다.
•대체 자원 관리.대체 시스템을 관리하는 데 사용할 수 있습니다: "사출 금형은 여러 장비에 장착할 수 있으며 이러한 제약 조건을 시스템에 직접 통합할 수 있어 효율성이 높아졌습니다."
• 모든 사람을 위한 단일 벤치마크 시스템. 고유한 시스템이 여러 도구를 대체합니다.
• 구성 가능한 플래그 및 알림. 일정이 개발되는 동안 신뢰할 수 있는 실시간 플래그 및 알림.
• 우발 상황 및 제약에 대한 대응. 작업량을 평준화하고 더 많은 기대를 가지고 작업할 수 있는 능력은 자동차 생산에서 빈번하게 발생하는 비상 사태와 예측할 수 없는 상황을 통제할수 있게 해줍니다.
솔루션은 1년이 조금 넘는 기간 동안 전 세계 18개 공장에서 출시되었습니다.
프로젝트 시기, 범위 및 배포 방법론
2014년 말 컨셉 증명이 완료된 후 18개 공장에서 비교적 짧은 시간 내에 DELMIA Production Planning & 을 구현하기로 결정되었습니다. 핵심 모델은 2015년 1분기에 구축되었으며 롤아웃은 2015년 4월부터 매월 동시에 실행되었습니다. “범위는 다소 글로벌하지만 중국, 인도, 유럽 및 멕시코의 공장을 포함합니다. “이러한 국제적 맥락에서 성숙도, 문화와 조직은 매우 상이하며 이것이 프로젝트 구현의 핵심 기능 중 하나입니다.”라고 Frédéric Marcotte는 말합니다.
이 방법론은 "다른 고객을 통해 이미 효율성과 효과가 입증된" DELMIA 팀과 공동으로 구현되었습니다. 출발점은 사전 공장이 배치할 준비가 되었는지 확인하는 킥 오프 4주 전에 시작되었습니다. 각 공장은 성숙도와 공정 제어 수준이 동일하지 않았습니다. 목표는 BOM 및 제조 범위가 최신 상태인지, 인벤토리는 신뢰할 수 있는 전제 조건을 확인하는 것이었습니다. "일탈이 발견되면 비교적 짧은 일정으로 실행 계획이 실행됩니다."
킥 오프 이후 5~6주에 걸쳐 배포가 완료되었으며 마지막 단계인 사용자 교육, 통합 테스트, 고 라이브(go-live)와 서포트가 현장에서 수행되었습니다. “고전적인 IT 시스템 롤아웃 계획. 순수한 IT 측면(소프트웨어 설치, SAP과의 인터페이스 구성, 테스트)은 IT 팀과 DELMIA 팀이 공동으로 관리합니다. 명심해야 할 중요한 사항은 우리가 전반적으로 5~6주마다 공장을 시작할 수 있는 능력을 갖추고 있다는 점입니다. 결과적으로 롤아웃은 빠르고 효율적입니다.”
이 도구는 우리의 모든 요구와 운영 제약을 충족합니다.
오늘날, 모든 이점들이 잘 드러납니다.
Marcotte는 그룹이 몇 가지 중요한 영역에서 성능이 개선되었다고 보고합니다.
고객 서비스 수준은 그룹 전체에서 98.5%이며, "툴이 설치하기 전에는 결코 100%가 아니었던 공장이 있는데, 이것이 진정한 보너스입니다."라고 덧붙혀 말했습니다 공급자 서비스 수준은 90% 이상입니다. “우리는 더 적은 변경으로 훨씬 더 안정적인 배송 일정과 리드 타임을 발행합니다. 이를 통해 우리는 공급업체의 수요를 평준화하고 결과적으로 공급업체와 공장의 재고 수준을 줄일 수 있습니다.”
공장 생산성 향상: “생산 계획이 현실적이고 실행 가능하기 때문에 예상치 못한 전환을 최소화할 수 있습니다. 모든 산업에서 발생합니다. 미리 계획하지 않으면 그 결과로 인해 고통을 받게 됩니다. 솔루션을 배포한 모든 공장에서 이 영역에 대한 실질적인 절감 효과를 보았습니다."
재고 감소: 평균 재고 수준은 8일입니다. “여기에는 재료, 반제품과 완제품이 포함됩니다. 어떤 경우에는 재고가 30~40% 줄어들어 상당한 절감 효과를 얻을 수 있습니다.” 공장이 고객 요구에 최대한 가깝게 생산하기 때문에 노후화 위험이 감소했습니다. 마지막으로 예외 선적(공장/고객 또는 공급업체/공장)이 대부분 제거되었습니다.
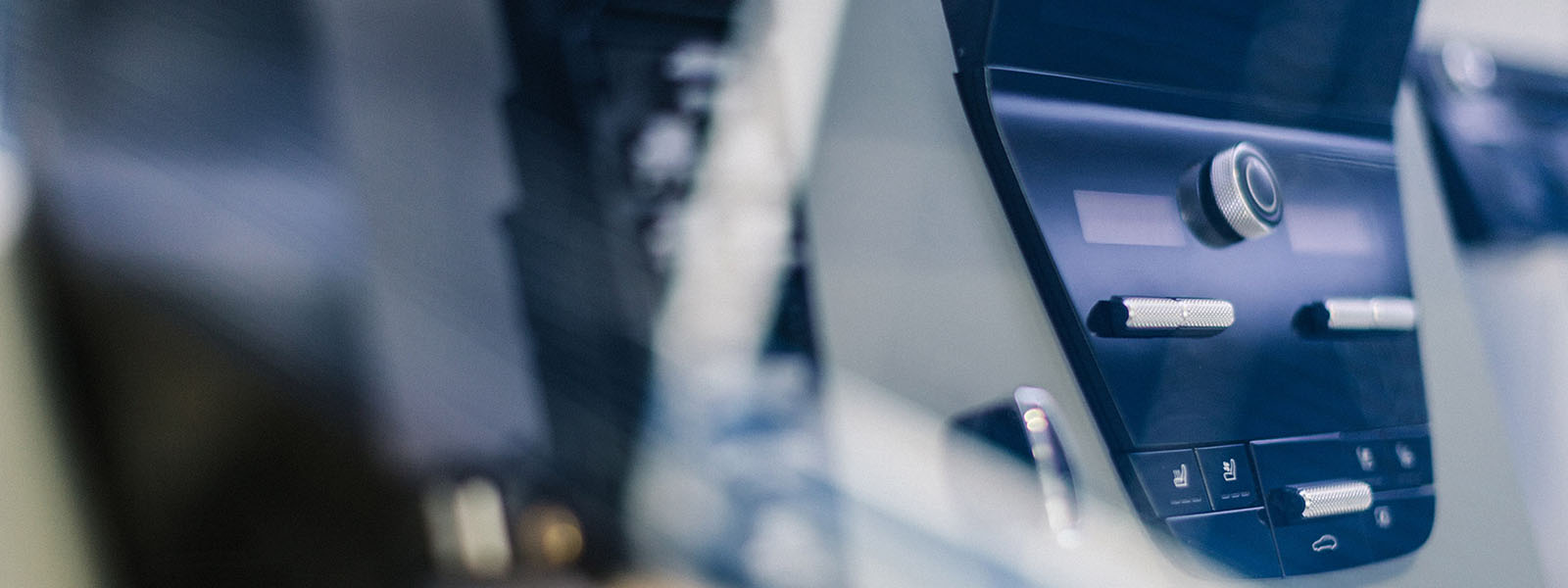
조직적 이익
Marcotte에 따르면 그룹은 여러 영역에서 이익/성과가 개선되었습니다:
- 향상된 팀워크: “DELMIA가 구현되는 동시에 이전에 생산 팀의 일원이었던 생산 기획자는 물류 부서로 옮겨졌습니다."
- 구조화된 커뮤니케이션: "우리는 단일화된 정보 소스를 모두에게 공유합니다.”
- 의사결정 개선, 적은 노력으로 빠른 효과를 거둡니다: “모든 공장에서 물류와 생산 사이의 일일 회의는 최대 30분이면 충분합니다. 모든 것이 명확합니다. 우리는 의사 결정을 재촉하지 않고 자연스럽고 차분하게 하루를 진행합니다.”
- 책임성 향상: "모든 스케줄링은 이전에 책임을 공유했던 단일 역할에 따라 달라집니다."
목표
- Novares 자동차 제조업체 고객을 위해 현실적이고 실행 가능한 납품 스케줄을 생성하고 프로젝트에 대한 360° 조감도를 제공할 수 있습니다.
- Novares 공급업체에서 시작하여 전체 공급망에 대한 요구 사항을 차트로 작성하기 위해 일관성 있고 신뢰할 수 있는 장기적 전망을 갖습니다.
- 정보를 중앙 집중화하고 공유할 수 있는 포괄적인 도구를 보유하고, 다른 작업 문화와 방법을 국제적 맥락으로 수용하는 것이 주요한 프로젝트 기능 중 하나입니다.
솔루션
플라스틱 사출 전문 자동차 공급업체인 Novares는 전 세계 18개 제조 공장에 DELMIA Production Planning 솔루션을 구현했습니다.
이점
- 향상된 성능: 그룹 차원의 고객 서비스 수준 98.5%, 공급업체의 경우 90%
- 공장 생산성을 향상시키는 현실적이고 실행 가능한 생산 계획
- 재고 수준 감소 및 노후화, 예외 선적 제거
- 조직적 이점: 향상된 책임성, 통제력과 예측으로 팀워크가 발전하고 의사 소통이 훨씬 구조화되었으며 의사 결정이 개선되었습니다.

Novares 클로즈 업
제품: 36,000개 이상의 부품 SKU가 있는 19개 제품 세그먼트로 구성된 7개 제품 라인을 포괄하는 솔루션 범위. Novares는 엔진룸 및 자동차 내외장 부품 시장에 포지셔닝하여 매일 15개 이상의 주요 브랜드를 제공하고 70개 이상의 자동차 고객을 보유하며 400개 이상의 차량 모델에 부품을 제공합니다.
본사: Clamart, France
설립: 1955년
직원: 21개국 10,000명의 직원
For more information: www.novaresteam.com