豊電子工業
日本のラインビルダーである豊電子工業は、顧客向けに設計したシステムが物理的な試運転を開始する前に正しく効率的に稼働していることを確認するために、ダッソー・システムズの3DEXPERIENCEプラットフォーム・オン・ザ・クラウドと業界ソリューションの経験豊富なデジタル・エクイップメント・コンティニュイティを選択しました。
ロボットによる自動生産ラインの立上げをバーチャルコミッショニングで効率化
最新の生産現場に一歩足を踏み入れると、溶接や組み立てから、マテリアルハンドリングや製品梱包まで、あらゆる種類の作業が様々なロボットにより自動生産ラインで行われているのを目にするでしょう。
しかし、自動化された生産ラインからメーカーが最大限の効果を得るにはどうすればよいでしょうか?答えのひとつは、日本の豊電子工業のようなラインビルダーに専門知識を求めることです。
同社代表取締役社長の盛田高史氏は「豊電子工業は1964年にメカトロニクス技術会社として設立されました」と語ります。「1979年には、日本でいち早く産業用ロボットシステムの分野に参入しました。それ以来、私たちはトータルシステムインテグレーターへと進化してきました。目標は、システムインテグレーターとして世界一になることです」
豊電子工業は、自動車、航空宇宙、防衛関連の企業やOEMなどを含む顧客の生産ラインにおいて、産業用ロボットシステムをどのように適用するかの検討を行っています。そして、しばしばIoT(モノのインターネット)技術の助けを借りて、そのラインの工程を最適化する最善の方法を考察します。現在までに、豊電子工業は40ヵ国以上の顧客に20,000以上のロボットシステムを納入しました。
豊電子工業 先進技術部部長 兼 加工技術開発室室長の松尾大介氏は次のように述べます。「お客様のご要望や仕様を綿密に検討した後に、生産工程を自動化するために、大手ロボットメーカーの産業用ロボットを用いたロボットシステムを含む、最も効果的な生産ラインを設計します。設備を現場に運び、正しく機能することを確認してお客様にお引渡しすることが、最後の段階となります」
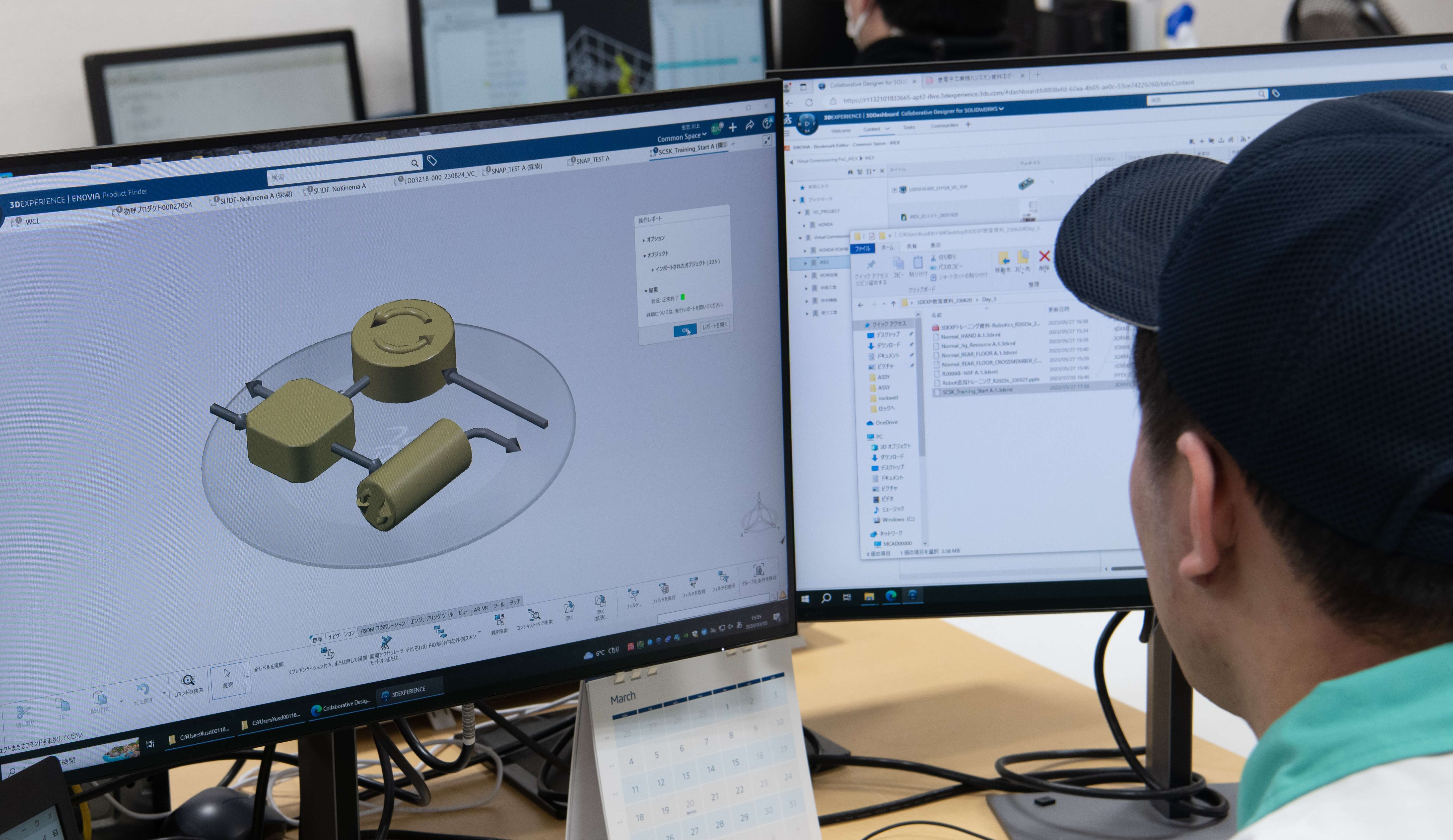
より迅速、よりシームレスなプロセスの必要性
競争が激化する市場において、豊電子工業は、顧客のロボットによる自動生産ラインのコンポーネントをチェック、テスト、検証するエンジニアリングプロセスであるコミッショニング(試運転)を迅速かつ効率的に行う必要があります。
一般的に、コミッショニングの段階は煩雑であり、プロジェクト遅延の原因の最大70%を占める可能性があります。かつては、豊電子工業はこの問題に直面していました。設計とコミッショニングの作業が別々に行われていたからです。
「以前は、作図者はたくさんの工程を思い描かなければなりませんでした」と松尾氏は語ります。「ロボットシステムの機械設計は当時、メーカーのデータを用いて当社がSOLIDWORKSで作図していました。しかし、このデータに間違いがあると、リワークや手戻りが頻発しました。また、ロボットの動作プログラムをチェックするためには、それをサードパーティのソフトウェアにエクスポートする必要があり、シームレスとは言えませんでした」
豊電子工業は、バーチャルコミッショニングを可能にし、より広範なデジタルトランスフォーメーションのビジョン達成に役立つ新しいアプローチが必要だと気づきました。 豊電子工業は、すでにダッソー・システムズのCADソフトウェアであるSOLIDWORKSを使用していたため、3DEXPERIENCEプラットフォーム・オン・ザ・クラウドと、プラットフォームを基盤として運用できるアプリケーションやソリューションで補完することにしました。
松尾氏は「SOLIDWORKSのデータも含め、すべてのデータを一元管理できるのが3DEXPERIENCEプラットフォームだと理解しました」と述べます。「これは私たちにとって大きな変化をもたらします。すべての検討業務のプロセスをより短期間で完了させることができ、納期を短縮できるのです」
バーチャルツイン・エクスペリエンスによって、コミッショニング作業を設計作業そのものに組み込むことができます。これにより、今まで見過ごされてきた初期の設計上の不具合を取り除き、結果として手戻りを減らすことができます
ロボットによる自動生産ラインを検証するための、一元化されたソリューション
豊電子工業は今では、顧客の製造現場に実際の設備を設置する前に、その実現性を検証することができる3DEXPERIENCEプラットフォーム上のDELMIAにより、ロボットによる自動生産ラインのバーチャルコミッショニングを実現しています。 以前は、ラインが完全に組み立てられるまで、タクトタイム(顧客の需要を満たすために必要な生産速度)を決定することができませんでした。そのため、現場での手戻りが増え、納期が遅れることがありました。
「バーチャルツイン・エクスペリエンスによって、コミッショニング作業を設計作業そのものに組み込むことができます」と松尾氏は述べます。「3Dのモデリングをしながら、複数のロボットを含むシステム全体の包括的な動作チェックを行うことができます。これにより、今まで見過ごされてきた初期の設計上の不具合を取り除き、結果として手戻りを減らすことができます」
クラウドベースのコラボレーション
豊電子工業は、POWER'BYのアプリケーションを使用して、SOLIDWORKSで作成した設計図面を3DEXPERIENCEプラットフォームに接続し、現在は、物理モデルのシミュレーションを3DEXPERIENCE プラットフォーム上のCATIA 1D-CAE機能を用いて行っています。今後は、CADと設計部品表(EBOM)をリンクし、ENOVIA の製品ライフサイクル管理 (PLM)とデータ管理の機能を用いることで変更や問題の見直しの際のコラボレーションを促進する予定です。
すべてのデータがクラウドベースの単一のプラットフォームに保存されるため、豊電子工業はプラットフォーム上で顧客と直接コラボレーションでき、データをセキュアな方法で共有、管理できます。したがって、現地で生産ラインをチェックするためにチームが出張する必要性も減ります。
松尾氏は「クラウドでデータを一元管理することが強力なコラボレーション機能を実現し、大きな変化をもたらします」と述べます。「会社としてより効果的に協力し合えるということです。インターネットを通じてつながることで、異なる場所にいながら同じ情報を得られるのです。この効率的な作業方法がもたらす結果として、私たちは20~30%の時間短縮を見込んでいます」
3DEXPERIENCEプラットフォーム・オン・ザ・クラウドを使うことで、稼働時間も向上しています。豊電子工業 SI技術部 生技検証室の大竹光彦氏は「かつて、ファイルベースのシステムを使っていた時は、あるプロジェクトから別のプロジェクトにデータをコピーすることがよくありました」と述べます。「コピーされたデータリンクが時々壊れ、生産ラインをテストするときに問題を起こしたり、時には故障して止まったりすることもありました。クラウドになった今、私たちはシングルソースの情報が手に入ります。正確なデータにアクセスできるので、業務がより円滑に進みます。データのストレージへのアクセスや読み込み・書き込み速度も格段に速くなりました」
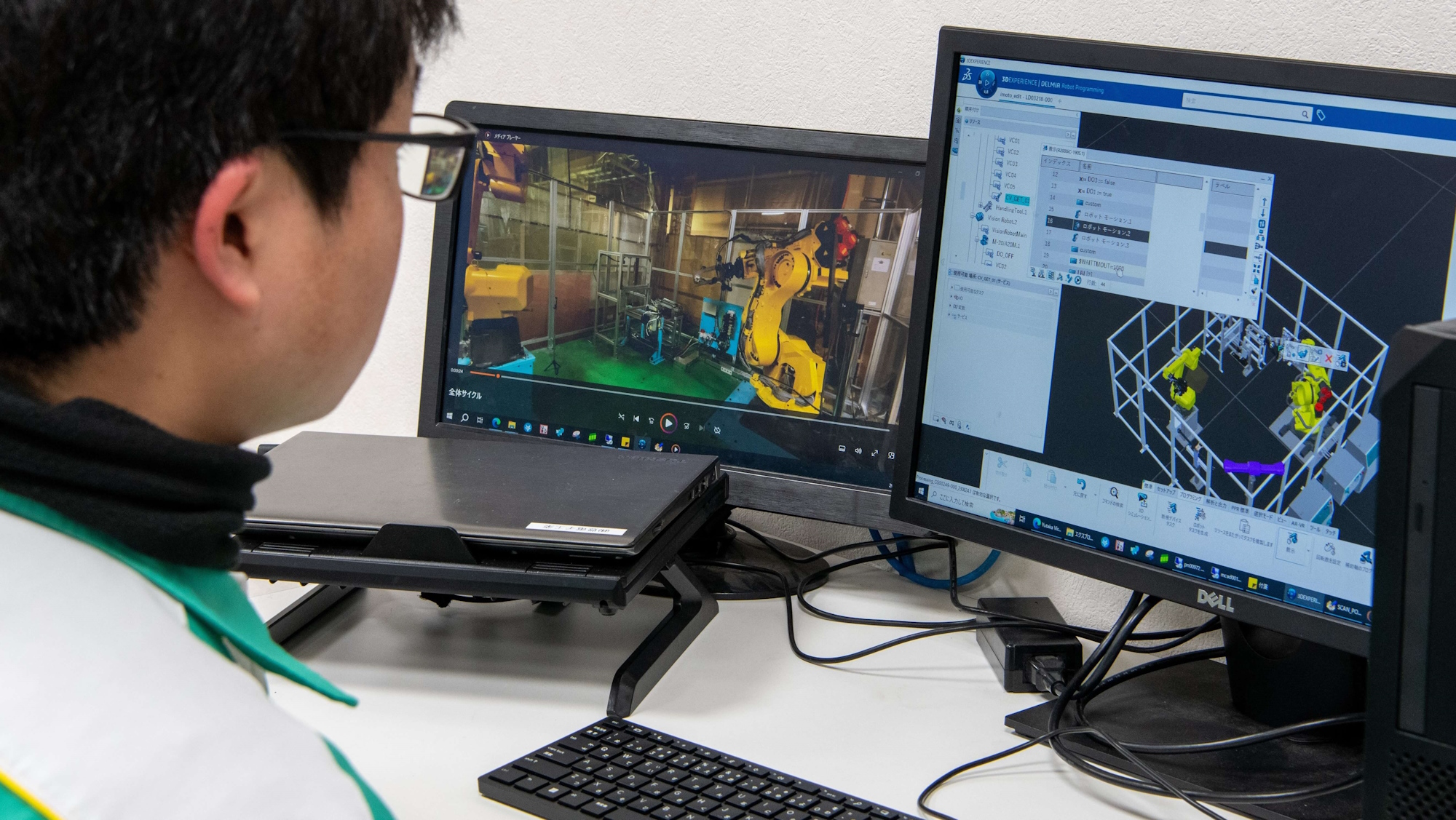
バーチャルコミッショニングの実践
3DEXPERIENCEプラットフォーム・オン・ザ・クラウドのバーチャルコミッショニング機能を活用する最初の機会は、iREX2023(International Robot Exhibition2023)で訪れました。その展示会で豊電子工業は、ロボットによる生産工程の将来性をデモンストレーションするためのラインを作成しました。バーチャルコミッショニング無しでは、セットアップに丸一日かかったかもしれません。しかし、最初にロボットのデジタルレプリカを作成し、その動作とインテグレーションをシミュレーションすることで、設置には4時間しかかかりませんでした。
大竹氏がその例を挙げます。「ロボットのアームが非常に複雑な治具を操作している場合、干渉があるかどうかを3Dのバーチャルモデルで簡単に確認できます。以前なら、ラインが構築されるまでこの種の問題に気づかないこともあり、最初からやり直すこともありました」
このプロジェクトは、現場で試運転が行われる前に顧客のニーズに合わせて、サイクルタイム、スペースのレイアウト、ワークフローを設計することで、豊電子工業がバーチャルツインで提供できる付加価値を実証しました。「現場での組み立て前に、実現性とタクトタイムを事前検証することで、現場でのテストを減らすことができました」と大竹氏は述べます。「その結果、プロトタイピングのリードタイムを50%短縮することができました」
豊電子工業は、ダッソー・システムズのツールの機能をフルに活用することで、オペレーションとデバッグのシステムの可視化をさらに向上させるとともに、ナレッジや過去の学習結果を今後のプロジェクトで再利用できるようになると期待しています。
盛田氏は、豊電子工業の専門知識と3DEXPERIENCEプラットフォームが提供する機能の組み合わせが、市場での地位を強固なものにしたと考えています。「私たちの強みは、あらゆる業界と接点があり、あらゆる産業の生産工程に対して、顧客の要求を取り入れた最新のロボットシステムによる自動化を提案できることです。あらゆる業界でデジタルトランスフォーメーションが進むなか、私たちの強みは変わらないでしょう。弊社はシステムインテグレーターとして、3DEXPERIENCEプラットフォームのような最新のテクノロジーを組み合わせることで、今後も顧客に優れた付加価値を提供していきます」
よくある質問
ロボット導入は生産の自動化の手段として機能し、大小さまざまな企業が、消費財から産業機械まで私たちが目にするあらゆるものを効率的に生産するのに役立っています。人間と機械が一緒に働けるように、協働ロボットを使うことも今や可能になりました。
ロボットによる自動生産は、製品の生産を自動化し、効率性と生産性の向上を実現する方法です。
産業用ロボットは、資材の移動、ピッキングや荷物の積み下ろしなどの繰り返し作業、さらには製品の検査まで行うことができます。
精度、スピード、品質。それが豊電子工業が、自動車や航空宇宙・防衛などの企業向けのロボットによる生産ライン構築における信頼できるエキスパートとして知られる理由です。
代表取締役社長 盛田高史
当社は1964年に創業いたしました。メカトロニクスの技術を基盤として、1979年に国内でいち早く産業用ロボットシステムの分野に参入をいたしました。トータルシステムインテグレーターとして活動をしてまいりました。
先進技術部部長 兼 加工技術開発室室長 松尾大介
ご要望や仕様に合わせて、私共の方で設備の検討、設計、その後、製作に入っていく、ということになります。
豊電子工業は現在、3DEXPERIENCEプラットフォーム・オン・ザ・クラウドでバーチャル・コミッショニングを行い、顧客のロボット生産ラインのコンポーネントを、現場での構築前にテスト、検証しています。
先進技術部部長 兼 加工技術開発室室長 松尾大介
3DEXPERIENCEの中で連携をすることによって、データは一元管理されるので、作図したデータが正しいのか間違っているのかということを事前にチェックできるようになりました。これは非常に大きな違いだと思いますし、工数はおそらく減っているだろう、という感覚で私共は作業しております。
このプラットフォームにより、豊電子工業は実現性を事前に検証し
適切な生産率を評価することができます。これにより、実物でのテストが減り、
試作のリードタイが 50% 短縮されました。
先進技術部 加工技術開発室 榊原大樹
これまではロボットのシミュレーションはロボットという感じでやってきたのですが、ロボットの動きやアクチュエータの動き、今回においてはAGV(無人搬送車)の動きなども実機同様の動きを事前に確認することができました。
3Dでバーチャル上であれだけ簡単に見られるというのは強みなことです。
クラウドベースの3DEXPERIENCEプラットフォームにより、豊電子工業は顧客とデータを共有し、迅速、容易にコラボレーションを行うことができます。
代表取締役社長 盛田高史
システムインテグレーターとして、世界中の最新の技術、こういったものを組み合わせて、世の中には存在しない付加価値というものが提供できますし、今後もそれをし続けていきたいと考えております。
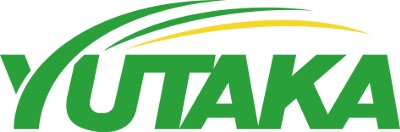
豊電子工業について
株式会社豊電子工業は日本最大級のシステムインテグレーターです。従業員は700人を超え、昼夜を問わず操業している同社は、ロボットシステムや物流制御システムの製造だけでなく、設計前の開発提案から納品後のメンテナンス、アフターサービスまで総合的にサポートしています。豊電子工業は世界7ヵ国に事業拠点を持ち、開発型システムエンジニアリング企業として、高度な技術的専門知識と革新的なアイデアで世界中の顧客を精力的にサポートしています。
詳しくは、ウェブサイトをご覧ください: https://www.ytk-e.com/
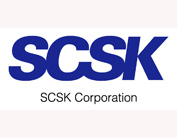
SCSKについて
1969年に設立されたSCSK株式会社は、日本のみならず世界中の企業に幅広いシステムインテグレーションサービスを提供しています。SCSKは、産業、金融、ソリューション、プロダクト・サービス、モビリティの5つの戦略的事業領域にフォーカスし、ITサービス業界における大手を目指します。