武蔵精密工業株式会社
日本の自動車部品メーカーである武蔵精密工業は、電気自動車向けの次世代パワートレインを開発しています。製品開発期間の短縮に加えて、新たな複雑性に対応するシミュレーションを導入し、品質の高い製品を低コストで継続的に納入する必要がありました。
パワートレインの再考
自動車部品メーカーの武蔵精密工業は、電気自動車がやがて従来のガソリン車に代わって主流になることを察知し、それが現実となった時のために準備を進めています。同社の目標は、業界トップの座を維持し、ムサシ・ブランドのスローガンである「Power to Value」を実現させる、現世代と次世代のそれぞれの自動車に最適化された、ユニークで革新的なパワートレインを開発することです。
武蔵精密工業 社長の大塚浩史氏は、次のように述べています。「自動車は大変革期と言われていますが、電動化やコネクテッドといった流れの中で、車そのもの、部品そのものも変わっていきます。例えば(ガソリン車の)『トランスミッション』のような領域が少なくなっていく一方、電動自動車のモーター部分には、減速機をはじめ、我々の得意とするギア・ユニットが必ず付いてきます。電動化の時代にあわせて、我々の得意なトランスミッションであったり、ギアであったり、そういう世界で技を磨いて世界一の会社になりたいと思っています」
同社は電動自動車向けに最適化された新しい世代のパワートレイン部品を開発するまたとない機会を得て、成功に向けて舵を切りました。
同氏は次のように述べています。「電動自動車では『回生ブレーキ』といって、車が停まるときにエネルギーを回収します。電動自動車向けには、そういったギアに求められる強度要件も、だいぶ変わってきます。同じ形をしたギアでも、電動化の時代に向けた新しい歯車の技術が求められており、そういった開発にも懸命に取り組んでいます」
静粛性の高い電気自動車の開発に押されて内燃エンジンからの代替が進む中、同社は自社部品が持つ潜在的な特性を見直し、騒音と重量という2つの大きな課題を克服しなければなりません。
同氏は次のように述べています。「我々の研究開発テーマとしては、音のしない静粛性の高いギアを作ることがあげられます。今の電動自動車は、バッテリーの関係もあって非常に重いのですが、これを小型・軽量化していくための技術は、ますます需要が高まってきます」
競争力を維持して社内の研究開発機能を強化するために、同社は提携や買収を通じて世界に進出しています。同時にデジタル変革も進めており、同社のグローバル研究開発と製品データの合理化と統合、業務効率の改善、製品開発の加速を実現しようとしています。それを達成させるには、ダッソー・システムズの3DEXPERIENCE® プラットフォームの実装が非常に重要でした。同氏は次のように述べています。「3DEXPERIENCEプラットフォームのような統合的なシステムというのが必須要件だと思いますね。我々のお客さまが使われるようなシミュレーションのソフトウェアだったり、あるいはお客様がナレッジや技術を集約されるプラットフォームと親和性の高いものが、我々の側にも必要です。そういう意味で、プラットフォーム上に社内の知見を集積しつつ、お客様と効率よく連携し、お客様と接点を深めていきたいと思います」
「プラットフォームというのは、それなくしては競争力にものすごく差が出てしまうので、当社にとって3DEXPERIENCEプラットフォームは必須アイテムです。世界できちっと戦って勝ち抜いていけるような会社を目指していくには、そういった必須アイテムをどれだけ使いこなせるかという、そういう観点が必要だと思います」
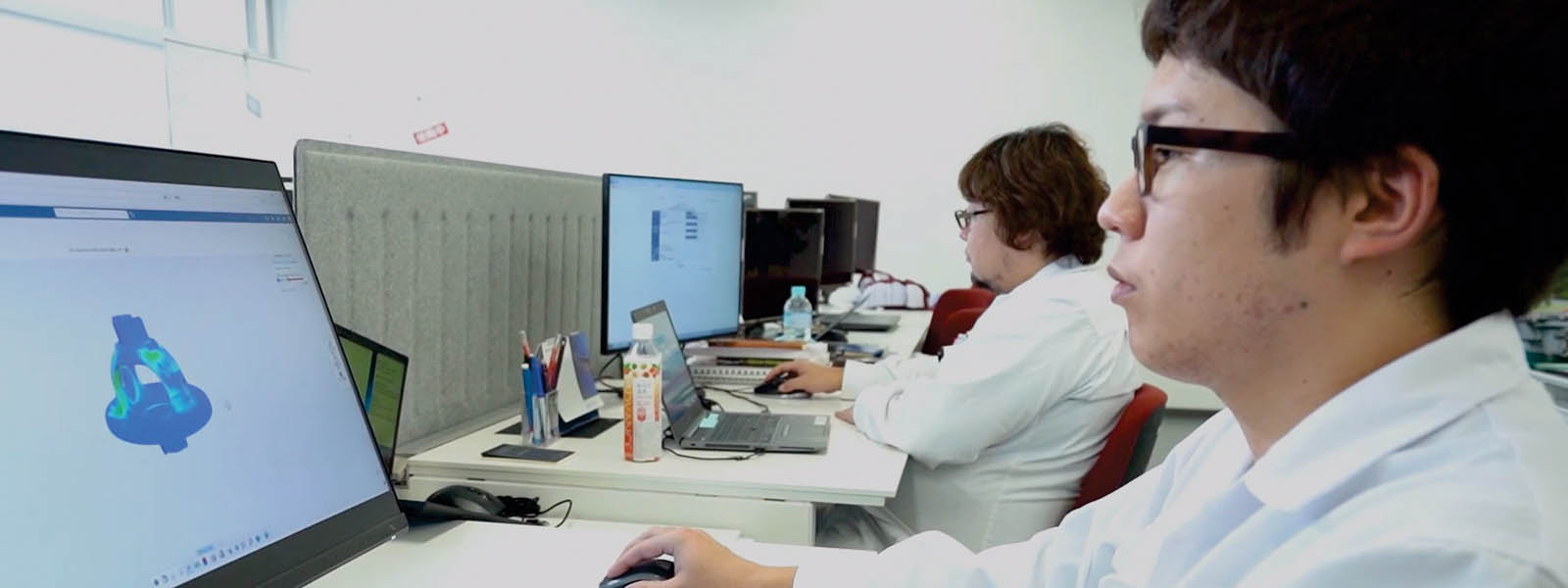
ナレッジベースの一元管理
3DEXPERIENCEプラットフォームを実装するまで、同社の研究開発と設計の能力は担当者個々人の専門知識に依存しており、社内全体のナレッジ共有など不可能でした。
大塚氏は次のように語っています。「技術は時間と共に属人性が高くなっていきます。10年選手と新入社員では、当然知見の差があるわけです。したがって、それぞれの人間が経験の中で蓄積してきたものを、いかに『見える化』して共有できるか、に常に興味があります。我々は、グローバルの開発チームのつながりを強化する方法も見つけなければなりません。そうするには、今までの電話やメールではなくて、いわゆるシステムとして、個々人の深い知識をちゃんと見えるようにしながら、メンバー間を横断的につなげていかなければなりません」
同社は、3DEXPERIENCEプラットフォーム上にこうした重要なナレッジを取り込み、社内チーム全体で広く共有していきます。そうすることで社内の専門知識を強化できるだけでなく、コラボレーションの効果をあげることもできます。
大塚氏は次のように話しています。「開発ひとつとっても、日本、アメリカ、中国など様々な所が関わってきます。これらを横につなげていくイメージです」
ナレッジベースを統一することで、同社のチームは今ではそれぞれの専門知識を蓄積しながら、革新的な製品の開発に専念できるようになります。
「本業では、『技を磨いて突き抜ける』ということをやっていますけど、せっかく新しいテクノロジーが出てきているので、我々が持っているものと、新しいテクノロジーの双方を生かした新しい事業に挑戦をしていきます。イノベーションは、異質のものどうしの掛け合わせから生まれるからです」(大塚氏)
武蔵精密工業 研究開発部 CAE研究グループのマネージャー佐久間敬哲氏は、次のように付け加えています。「今までの業務は、どちらかというと属人的な部分が多かったのです。3DEXPERIENCEプラットフォームでは、製品開発プロセスの上流における要求仕様から、それをどうやって製品機能に落とし込んだかという部分までをプラットフォーム上に全て保管することによって、知識を集約していきます。それが、今後のイノベーションにつながるデータベースとして活躍すると考えております」
テンプレートを作成してベストプラクティスを記録するプラットフォームの機能により、今ではプロセスも社内全体で標準化されています。
佐久間氏は次のように述べています。「3DEXPERIENCEプラットフォーム上のENOVIAアプリケーションでプロジェクトを管理し、業務をテンプレート化することにより、『抜け漏れ』がなくなります。設計の業務に関しては、それまでは複数の業務フローがありツールも分かれていましたが、それらを3DEXPERIENCEに一本化することで、設計者とCAE担当者が連携して情報共有が進み、業務効率が上が
っていくことを期待します」
同社のさまざまな部門や拠点で働く設計者とエンジニアは、今ではプラットフォームを介して効果的に作業を進めることができ、製品開発サイクル全体を通して効率的な連携が可能になります。
同氏は次のようにも語っています。「今までは他グループの進捗が全く把握できないこともありました。プラットフォームでプロジェクトを管理し画面上で進捗が『見える化』され、他グループとの密接にやりとりできるようになります。また、プラットフォームが要求管理に有効だということもわかりました。顧客がどれぐらいのものを求めているのかというのも、グループで共有することで、互いにやるべきことが見えるようになってきています。3DEXPERIENCEプラットフォームにプロジェクトを管理させることで、情報の共有を進めて、開発の進捗状況などを確認していきます
武蔵精密工業 研究開発部 CAE研究グループの小杉優太氏は、次のように付け加えています。「研究開発グループ全体で、正確なデータを用いるという取り組みができるようになりましたので、これまで以上に他のグループとの協業が進んでいくのではないかと感じています」
デジタルによる設計検証
武蔵精密工業が3DEXPERIENCEプラットフォームを選択した主な理由の1つに、このプラットフォームが、各担当者が使い慣れているCAEツールに対応していることが挙げられます。業務とツールを連携させることは、分析だけに限らず、プロジェクトの分野全体にわたる管理体制も強化することにつながります。それは、時代の先を行く新しい製品を開発する同社にとって非常に重要なことです。
小杉氏は次のように述べています。「プロジェクト管理などのアプリケーションを用いて、他のメンバーの仕事を把握するほか、解析アプリケーションを使って、製品の構造解析などをしております。3DEXPERIENCEプラットフォームで一番気に入っている点は、設計データと解析データなどの紐づけができる点だと感じています」
すべてのシステムが単一のプラットフォームから起動するため、設計部門からのデータの共有、それを用いる解析業務がシームレスに連携できるようになります。
同氏は次のように述べています「今まではファイルサーバーを用いてデータの受け渡しをしていたのですが、プロジェクト管理機能のみならず、3DEXPERIENCEプラットフォーム上でデータの受け渡しもできるようになります。その点が大変うれしい機能であったと感じています。
3DEXPERIENCEプラットフォーム上で、設計・エンジニアリング向けアプリケーションのCATIA、リアリスティック・シミュレーションのSIMULIAを使用することで、設計者とエンジニアはプロセスのどの段階でも新しい製品設計に変更を加えることができ、仮想テストやシミュレーションを活用して詳細な部品検証を行い、内径のねじれ、曲げ剛性、負荷分散、応力場、金属疲労の安全要因などの情報を確認することもできます。これらアプリケーションの活用により、物理的なプロトタイプやテストのニーズを削減することで、開発プロセスを加速できます。
同氏は次のように述べています。「CATIAの部分に関しては、パラメーターを使って形状をすぐに生成するような仕組みを作っております。そこからシミュレーションの部分につなぐ部分は3DEXPERIENCEを使って、設計者が簡単に解析できるようなシステムを作っています。今までは、形状を変更した際に条件の再設定などの手間がかかっていましたが、3DEXPERIENCEプラットフォームでは、形状を変更した後も、簡単に解析を再実行できます」研究
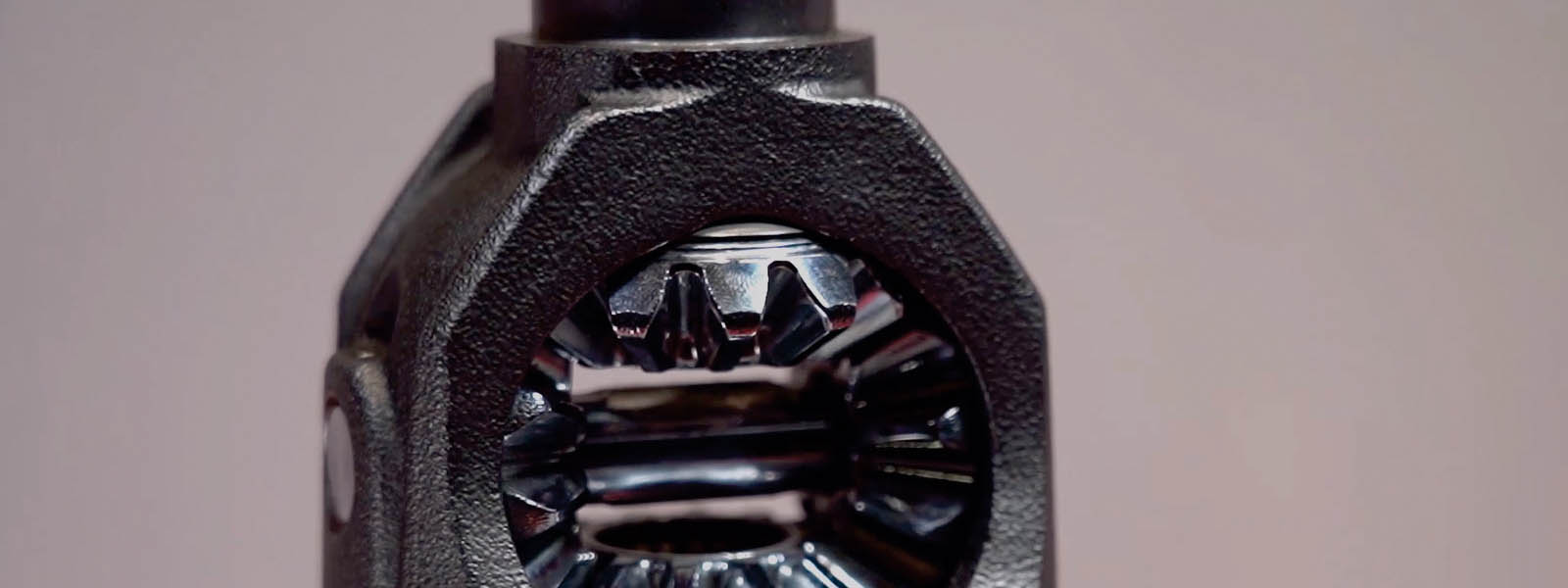
研究開発の加速
3DEXPERIENCEプラットフォームによって、同社は製品開発に集中して取り組み、新しい自動車の製造ライフサイクルがますます短くなっていく中でも、メーカーの要求に遅れることなく素早く対応することができます。
大塚氏は次のように述べています。「これまでは車の開発には約5年、また関連する諸々の技術の仕組みを整えるのには約10年かかるのが通常でした。いったん新車が商品化された時点で、また新しい開発に取り掛かるのが常でしたが、今はテクノロジーの大転換期ですし、ガソリン車と比較して、電動自動車の開発期間は、ざっと半分ぐらいです。そのため関連する技術に掛けていた時間も半減させようと思っているのですが、そのためには非常に速い製品開発プロセスが必要になります」
CADとCAEをシームレスに連動させることで、モデリングやメッシングの自動化に加えて、シミュレーションに基づく設計の最適化が可能になります。つまり、最初から設計し直すという作業はもう過去の話なのです。
大塚氏は次のように述べています。「開発スピードを上げるために、最新のIT活用を非常に重視しています。プロトタイプを作って、それをテストするという、このプロセスが一番長くかかります。これを、最新のテクノロジーを使ってバーチャルテストに置き換えていくことによって、開発期間を短縮する、そういった方向性です」
「 3DEXPERIENCEプラットフォ ームのプロジェクト管理の部分を使い、業務をテンプ
レート化することにより『 抜け漏れ』がなくなります。 」
真のグローバル競争
自動車業界がますます進化していく中、3DEXPERIENCEプラットフォームのような技術プラットフォームは、もはや、あれば良いというレベルではなく、なくてはならないものになっていくだろうと大塚氏は考えています。
同氏は次のように述べています。「バーチャル・モデリングやシミュレーションのテクノロジーなくして、これからの世の中は成立しません。プラットフォームというのは、それなくしては競争力にものすごく差が出てしまうので、当社にとって3DEXPERIENCEプラットフォームは必須アイテムです。世界できちっと戦って勝ち抜いていけるような会社を目指していくには、そういった必須アイテムをどれだけ使いこなせるかという、そういう観点が必要だと思います」
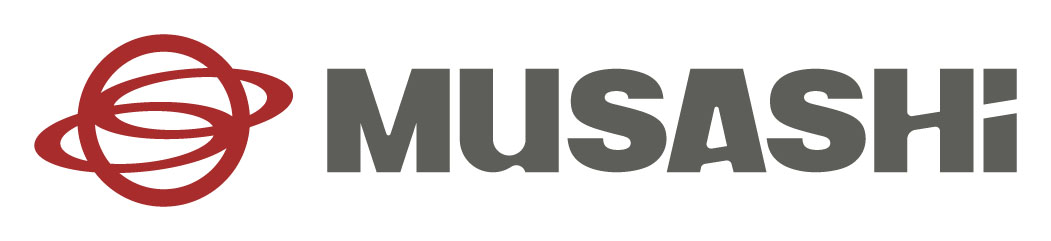
武蔵精密工業について
武蔵精密工業は、世界中のグローバルOEMや一次サプライヤーに自動車・自動二輪用部品を供給するグロ
ーバル・メーカーです。豊橋市に本社を構え、ヨーロッパ、南北アメリカ、中国、東南アジアにわたる14か
国・35拠点で製造を行っています。
製品:自動車用パワートレイン、コンポーネント、変速ギア、カムシャフト、自動二輪用各種駆動部品
詳しくはこちらをご覧ください:www.musashi.co.jp