YURI
German microgravity start-up YURI is on a mission to make microgravity research accessible to all industries. To take customers’ research ideas and scientific requirements and translate them into engineering specifications for hardware makers, YURI is taking advantage of the Reinvent The Sky industry solution experience on the 3DEXPERIENCE platform to build its hardware and handle all space experiments.
Unlocking the benefits of microgravity
In Australia, scientists are exploring how cancer cells behave in the absence of gravity. A team at the University of Technology Sydney’s (UTS) School of Biomedical Engineering put ovarian, breast, nose and lung cancer cells into a microgravity simulator and found that 80 to 90% of the cells died within 24 hours. To validate their findings, they have partnered with microgravity experiment specialist YURI to send the cancer cells to the International Space Station (ISS) to study them in true microgravity. Soon, the cancer cells will be transported in YURI’s special cell biology experiment hardware to ISS on the SpaceX CRS-21 mission. It’s one of the first of many exciting projects for YURI as it brings microgravity experiments within reach of more research organizations worldwide.
Microgravity is an environment where gravity does not act or seem to act on an object or thing, making it feel weightless. There are numerous ways of creating microgravity or freefall conditions, such as using drop towers, parabolic flights and sending objects up to orbital space platforms such as the ISS. Scientists are particularly interested in exploring how biological and physical systems behave in the absence of gravity to improve our understanding of diseases and their treatments.
“The problem on earth is that gravity is permanently acting on the test object,” said Philipp Schulien, chief technology officer and co-founder at YURI. “If, for example, cells are tested in a petri dish, they are two-dimensional on the bottom and are flat, but in the body the cells are three-dimensional structures and this can only be recreated by trying to switch off the gravity factor. On the ISS you can create larger clumps of cells, spheroids, which then also have other properties. We also do crystallization experiments, growing crystals under weightlessness to make them more much defined and uniform, which leads to better functionalities such as in fiber optic cables.”
We’re a high-tech start-up so it’s important to have high-tech software, it made perfect sense for us to adopt the 3DEXPERIENCE platform on cloud.
Bringing microgravity within reach
Until recently, sending an experiment to the ISS was extremely cost prohibitive, but thanks to YURI and its hardware, built using the 3DEXPERIENCE® platform, it’s now possible to send an experiment to the ISS for as little as €95,000.
Launched by a team of aerospace engineers in Germany, YURI was set up to make access to microgravity experimentation simpler, quicker and more affordable. YURI’s founders believe that microgravity experiments hold enormous potential for the pharmaceutical, biotech, advanced materials and electronics industries and want to make this kind of research widely accessible. The company handles all aspects of a mission, including working with clients to define their experiment setup, choosing the most suitable, cost-effective and time-effective combination of experiment hardware and microgravity platform, booking a launch and handling all of the safety and logistics considerations.
“Our mission is to make microgravity research available to everyone,” said Mark Kugel, co-founder and chief commercial officer at YURI. “We’re all experienced in this field and have been involved in numerous microgravity payloads for the ISS, so we had seen the problems scientists face in terms of cost and access and wanted to find a better way.”
Central to YURI’s success is its ability to build its hardware using modular blocks and reuse its designs and knowledge, going from ideation stage to experiment launch within a matter of months. This approach also helps to keep costs under control and enables organizations like UTS to access microgravity for the first time.
“We’ve built up a modular approach which allows us to reuse parts,” Kugel said. “This is a huge cost saver as we don’t have to develop everything from scratch. It means we can bring microgravity within the reach of smaller organizations with limited budgets that previously would have been priced out of the market. We’re faster too. Our record of getting an experiment into space is four months, which is around three times faster than anybody else. And because we don’t own any expensive assets in space ourselves, we’re able to work with the agencies and choose the cheapest option for our clients. We’re cost- and time-effective.”
YURI handles its entire hardware development process on the 3DEXPERIENCE platform, which it has used since it launched in 2019.
“We’re a high-tech start-up, so it’s important to have hightech software,” Kugel said. “CATIA is the most popular design system used in aerospace, so it made perfect sense for us to adopt the 3DEXPERIENCE platform on cloud with its design application.”
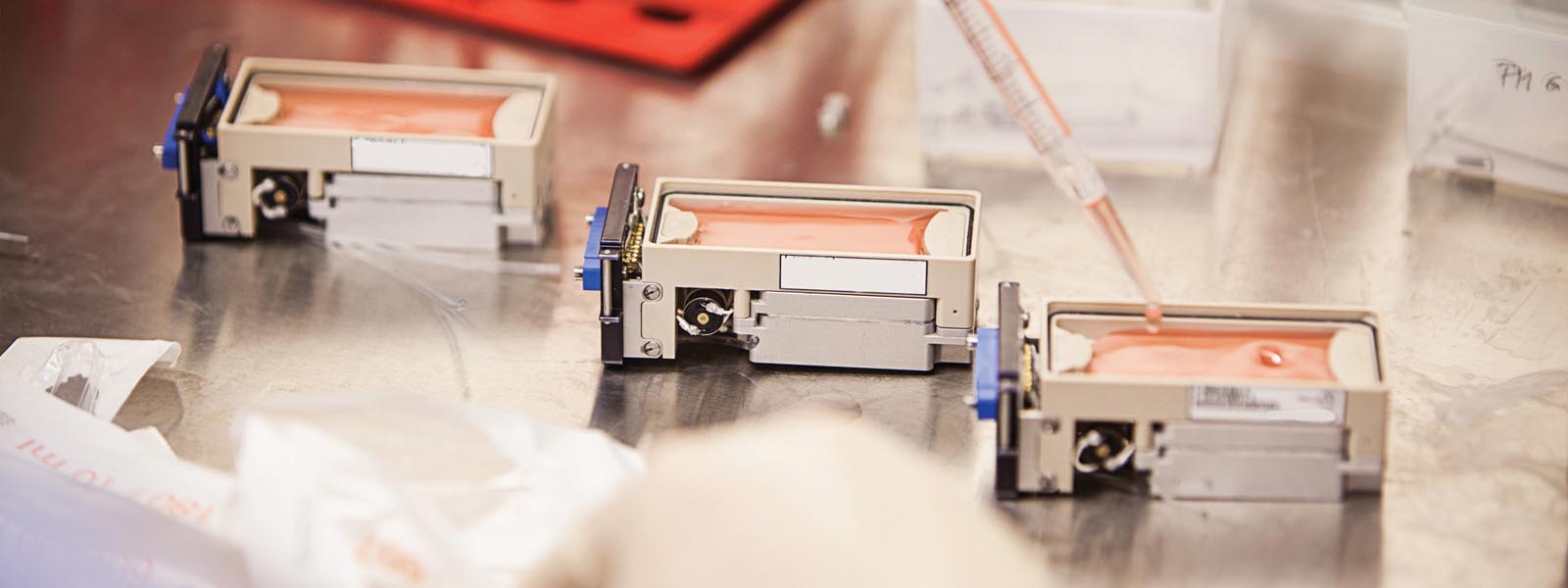
Developing specialized hardware in 3D
All of YURI’s hardware is designed on the 3DEXPERIENCE platform, taking advantage of 3D architectures to develop both standard and customized experiment containers and modules.
“There are a number of research facilities on the ISS and we provide boxes that fit into those facilities, which have certain standards we must meet,” Kugel said. “The most common is the standard cube form factor (10x10x10cm), but there are others such as the 80x50x30mm cuboid. Each box must be light, completely secure and biocompatible.”
These small modular containers are designed in minute detail, with each inner shell custom designed for individual use cases, such as cell cultures, plants or aquatic systems.
“These small form factors must meet standard dimensions and weight requirements, and are designed for specific use cases,” Schulien said. “Our clients come up with a research idea, have scientific requirements such as temperature and volumes, and we then translate this in the 3DEXPERIENCE platform into a design and engineering specifications for our machine builders.”
During the initial design phase, YURI’s engineers use CATIA to express ideas into understandable formats that can be easily shared and communicated. Designing in 3D, they can share concept proposals with clients and clearly visualize how the hardware will look and operate. Serving as an authoritative source of truth, ENOVIA on the 3DEXPERIENCE platform keeps track of design changes, helping to prevent re-work further down the product development lifecycle.
“If I make a modification, then my drafting from the start changes directly too,” said Lukas Trautwein, design engineer at YURI. “Everything is connected. Another big advantage to working with 3D models is that I don’t have to start at zero when I’m working on a new hardware concept. I can easily combine different parts and components, building up modules to quickly create a product that meets our clients’ specific requirements.”
All of this helps YURI to stay on track with tight mission timeframes and ensure each experiment is ready for launch. “Deadlines must be adhered to, so our goal is to be as quick as possible,” Trautwein said. “It’s also in the interest of our customers to complete the design stage early so they can start the experiment and test and tailor their setup.”
Of course, we checked data security, especially as our business is offering space experiments. We need control over where data is stored, preferably on servers in Europe, and this is a given with the 3DEXPERIENCE on cloud.
Cloud-first start-up success
YURI worked with local Dassault Systèmes business partner CENIT to implement the 3DEXPERIENCE platform. “They negotiated the package for us and helped us choose the best setup for our business requirements,” Kugel said. “We have a really good connection with the CENIT team and they guided us through the entire implementation. Even now if we have any issues, they are on hand to help.”
Many of the team had used CATIA in previous roles and were impressed by the new user interface in CATIA on the 3DEXPERIENCE platform on cloud. “It made sense for us to start directly in the cloud-based platform and get hold of all the rich functionality we needed,” Trautwein said. “Having used different CAD systems before, I found the jump to CATIA on the 3DEXPERIENCE platform a real step up. The new design is even more user-friendly.”
YURI decided a cloud implementation was an ideal fit for its business requirements, particularly in terms of the flexible access and scalability it delivers. Before going ahead, the team checked that Dassault Systèmes’ cloud offering aligned with its data security needs.
“Of course, we checked data security, especially as our business is offering space experiments and these can fall into different categories,” Schulien said. “We need control over where data is stored, preferably on servers in Europe, and this is a given with the 3DEXPERIENCE on cloud.”
Today, YURI’s engineers benefit from the ability to access the platform online from wherever they are regardless of the device, and know they are working with and sharing the latest data and designs. “I can easily access all the applications I need and work on all the components and share them securely with colleagues, which would not be the case if file-based work and data was stored locally,” Trautwein said. “In terms of speed and access to the applications on cloud, nothing changes when we’re working from home. And should there be a failure or malfunction, the permanent storage mechanism of the cloud keeps data safe,” he added.
Thanks to the cloud, YURI is always working with the most up-to-date version of the software and benefiting from access to the latest functionality. “Managing updates is super easy and ensures that everyone works in the same way using the most current release,” Trautwein said. “The update runs smoothly in the background and allows me to carry out other tasks such as managing my emails, without impacting my productivity.”
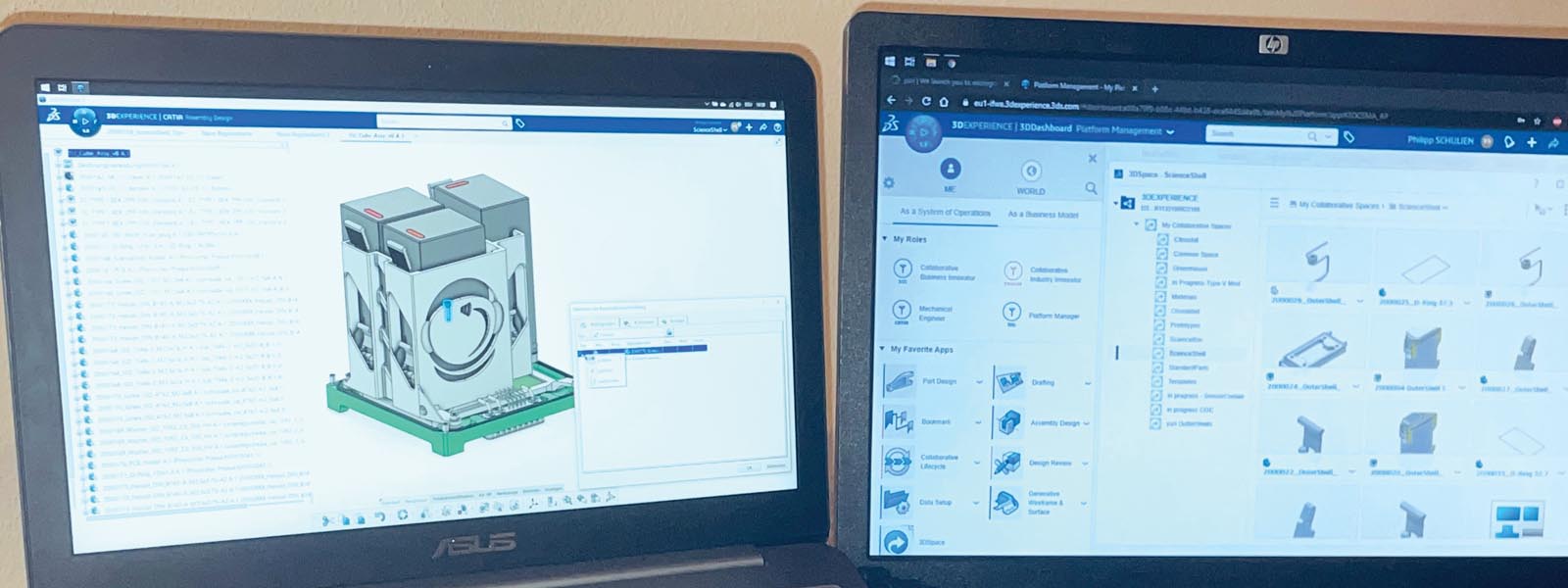
No limits
As YURI continues to grow its business and bring more unique and diverse experiments to microgravity, it’s confident that its technology platform will support its ongoing needs.
“The cloud platform is the best and most flexible solution for us, especially as it gives us the option to add more functionality as our requirements change and grow, without any disruption to our business,” Kugel said. “We can add new apps safe in the knowledge that we won’t need to purchase additional hardware. Everything we need resides on one platform.”

Focus on YURI
Founded in 2019 by a team of space engineers, YURI enables research in microgravity for any industry. The German company develops fully automated mini labs the size of a wallet and launches them for customers to the ISS, on orbital and suborbital spacecraft, on parabolic flights and on drop towers. The unique environment of microgravity is especially valuable in the life sciences, as human tissue grows in three dimensions and drug discovery can be improved. The name YURI is a tribute to the first human in space, YURI Gagarin.
For more information: www.YURIgravity.com
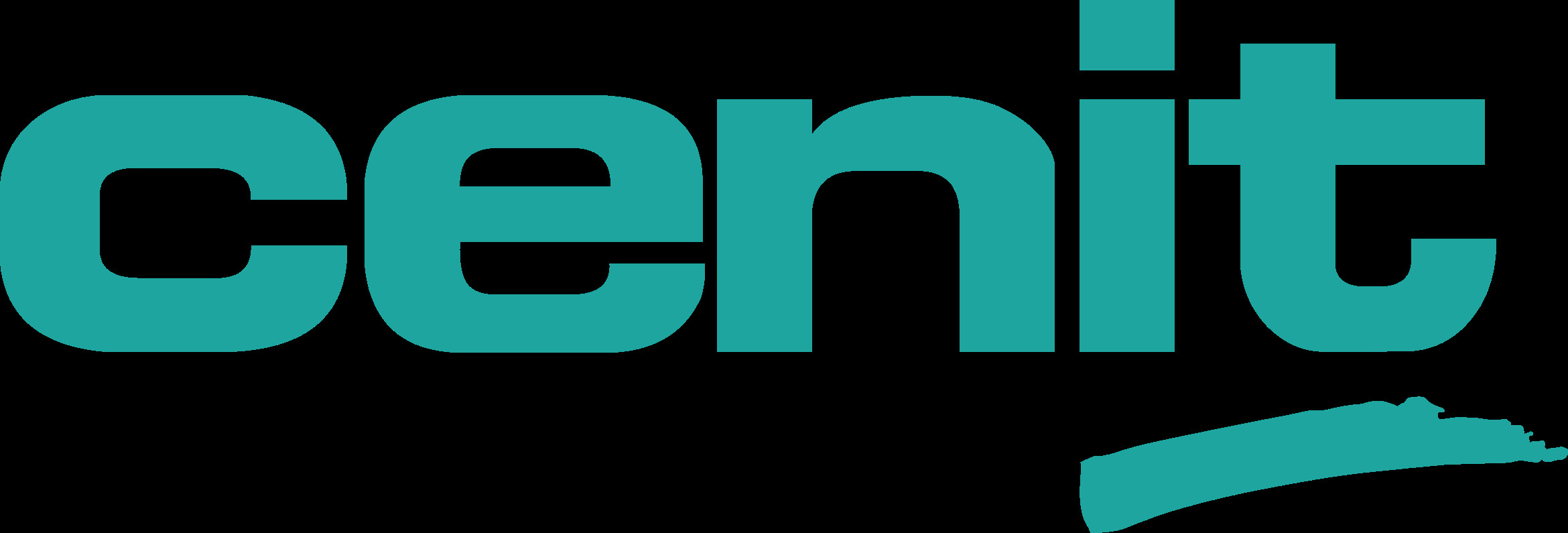
Focus on CENIT
CENIT empowers sustainable digitalization. Our solutions are based on innovative technologies in product lifecycle management, the digital factory and enterprise information management. CENIT consultants provide customers with end-to-end advice to ensure that solutions are implemented with an understanding of the entire value chain. With a holistic approach and based on trusted partnerships, CENIT takes responsibility for solutions on behalf of our clients. CENIT has been helping prestigious customers in key industries to gain competitive advantages for over 30 years.
For more Information: http://www.cenit.com/