Wichita State University
National Institute for Aviation Research (NIAR) at Wichita State University (WSU) partnered with Dassault Systèmes’ to create the first 3DEXPERIENCE Center as part of its newly created Innovation Campus with the 3DEXPERIENCE platform at its heart.
Empowering tomorrow's workforce
Innovation not only begins with a good idea, it also needs an environment to nurture and mature the idea until it becomes a viable, marketable product. Providing this optimal environment is the driving force behind Wichita State University’s (WSU) Innovation Campus in Wichita, Kansas.
“Our ambition is to expose students to industry-related projects that provide them with learning that is not traditionally found in a text book,” said John Tomblin, WSU vice president for research and technology transfer and executive director of the National Institute for Aviation Research (NIAR), an aviation research center of WSU that integrates business, government and university entities in cooperative efforts to advance aviation technology. “We aim to be a model for applied learning and an economic driver for the community – where students can transition back and forth between the academic world and industry to work on real-world projects while they’re in school.”
Dassault Systèmes partnered with NIAR at WSU to open the 3DEXPERIENCE® Center at the Innovation Campus to promote the use of new technologies such as additive manufacturing, Multi-Robotic Advanced Manufacturing (MRAM) and the development of new engineered materials that will shape the aviation industry in the years to come. “To prepare the engineers of the future, we need to start familiarizing students with emerging technologies that employers will soon be using,” Tomblin said.
Shawn Ehrstein, director of emerging technologies and CAD/ CAM at WSU-NIAR, adds that many aerospace companies use 3DEXPERIENCE technologies to develop their aircraft; and those companies prefer to hire students that already have experience working with these technologies rather than spending up to two years training new employees. Consequently, they welcome the opportunity to collaborate with students on reallife projects that use advanced technologies like virtual product development and prototyping, immersive 3D environments, simulation, robotics and certification.
“In the 3DEXPERIENCE Center, students can go from concept to development and manufacturing – all made possible with the 3DEXPERIENCE platform,” Tomblin said. “We focus on four pillars here at the 3DEXPERIENCE Center. They are advanced materials or how to get the newest materials into the latest products. The second is using simulation tools to solve those problems. Next, there’s automation or how we can do things differently in advanced manufacturing and finally, certification or how we can certify those products. Dassault Systèmes is the perfect partner because their platform excels in each of these domains. It elevates what we can do in these areas to advance innovation in the future.”
The 3DEXPERIENCE platform allows us to put our requirements in early and to track those requirements to obtain up-to-date statistics based on live data. Managers know exactly where projects are at any point in time and can detect and correct issues before they become showstoppers.
Building an unmanned aerial system
The first fully collaborative project at the 3DEXPERIENCE Center is an unmanned aerial system (UAS), or drone, designed to handle multiple missions including search and rescue. The UAS was entirely designed and manufactured using Dassault Systèmes’ 3DEXPERIENCE platform and its Aerospace & Defense industry solutions.
“The goal of the UAS project is to take a fairly complicated system and build it using the 3DEXPERIENCE platform,” said Ryan Benyshek, lead designer of a team comprised of WSU engineering students and Dassault Systèmes experts. “It is a learning experience that enables us to familiarize ourselves with the tools, and to have a good understanding of the issues we will deal with in real-world projects like this. Students see that from an initial concept to test flight, everything can be done on the 3DEXPERIENCE platform. It’s a rewarding experience to have something go from requirements to full-fledged flight.”
“We chose the 3DEXPERIENCE platform for this project because it was an all-encompassing product,” Ehrstein added. “We were able to drive our different activities here without having to deal with data translations and switching from one system to another. It’s a true integrated, enterprise-wide system.”
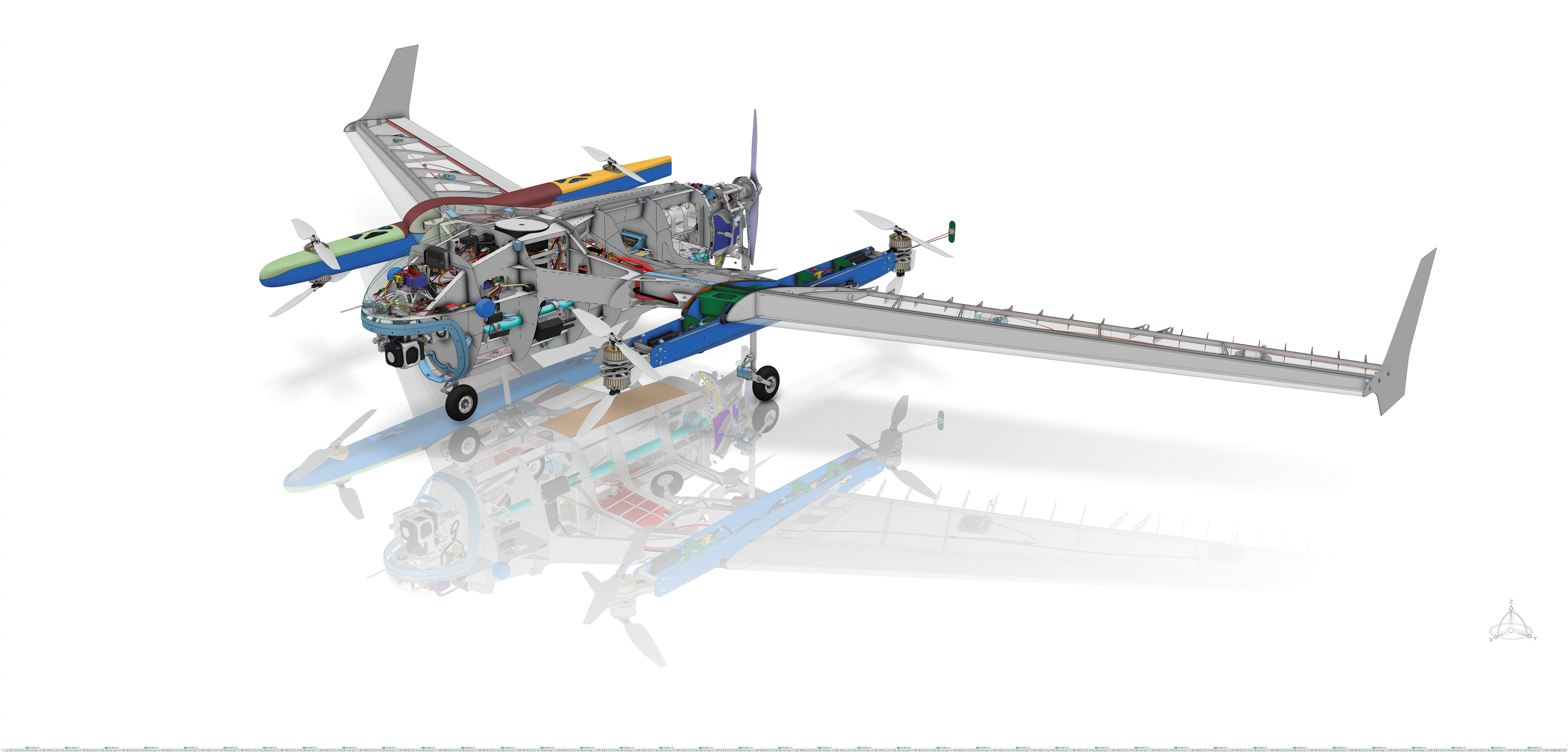
Composite design and virtual simulation
The UAS is almost entirely made of composite materials and by delivering a comprehensive set of dedicated process-oriented applications, the 3DEXPERIENCE platform allows students to efficiently manage composite design on complex surfaces.
“Designing a full aircraft structure in composites, including the skin, its external and internal structures, and the tooling is challenging,” Benyshek said. “Parts that are too complex to create in composites were 3D printed. Dassault Systèmes’ applications provides us with a virtual framework for assembly and manufacturing that allows us to quickly validate our tooling and systems, and to greatly reduce the amount of tooling features and jigs required to assemble the drone. In essence, a digital pre-validation enables us to get our designs right the first time.”
One of the UAS’s distinctive characteristics is its modular architecture. “Our UAS is a bit non-conventional because we have a modular design,” Ehrstein said. “Not only can it be a CTOL (conventional takeoff and landing) only or a VTOL (vertical takeoff and landing) aircraft, but we can add/remove wings, add/remove pylon engines, and switch configurations in the field, which is fairly unique. Although we are not the only ones doing this, it certainly is not the norm in UAS design.”
Ehrstein also spoke about specifications and their impact on the design. “The main concern that everyone has in any air-type ship is weight. Our UAS must be 12 feet (approx. 3.6 meters) in length and weigh under 55 pounds (25 kilograms), which is a challenging combination,” he said. “The 3DEXPERIENCE platform is very useful in this respect because we are able to start from the beginning with the requirements, log them into the system and keep track of our compliance as we go along. Moreover, we don’t have to worry about exchanging data or someone working on outdated files because everyone has access to one single source of information that they follow all the way from requirements to planning, to system and structural development, analysis, manufacturing, assembly and test. It’s all integrated in one platform.”
The team used CATIA Generative Design Engineering (GDE) to optimize the UAS Gimbal assembly for the cameras. Generative Design allows topology optimization and CAD reconstruction on a unified platform. Using GDE, the team reduced the vehicle weight allowing 15 to 30 minutes of additional flight per battery charge. Without GDE, multiple software tools would be needed, some of which are not compatible, making data translation a lengthy and inaccurate process that impacts quality.
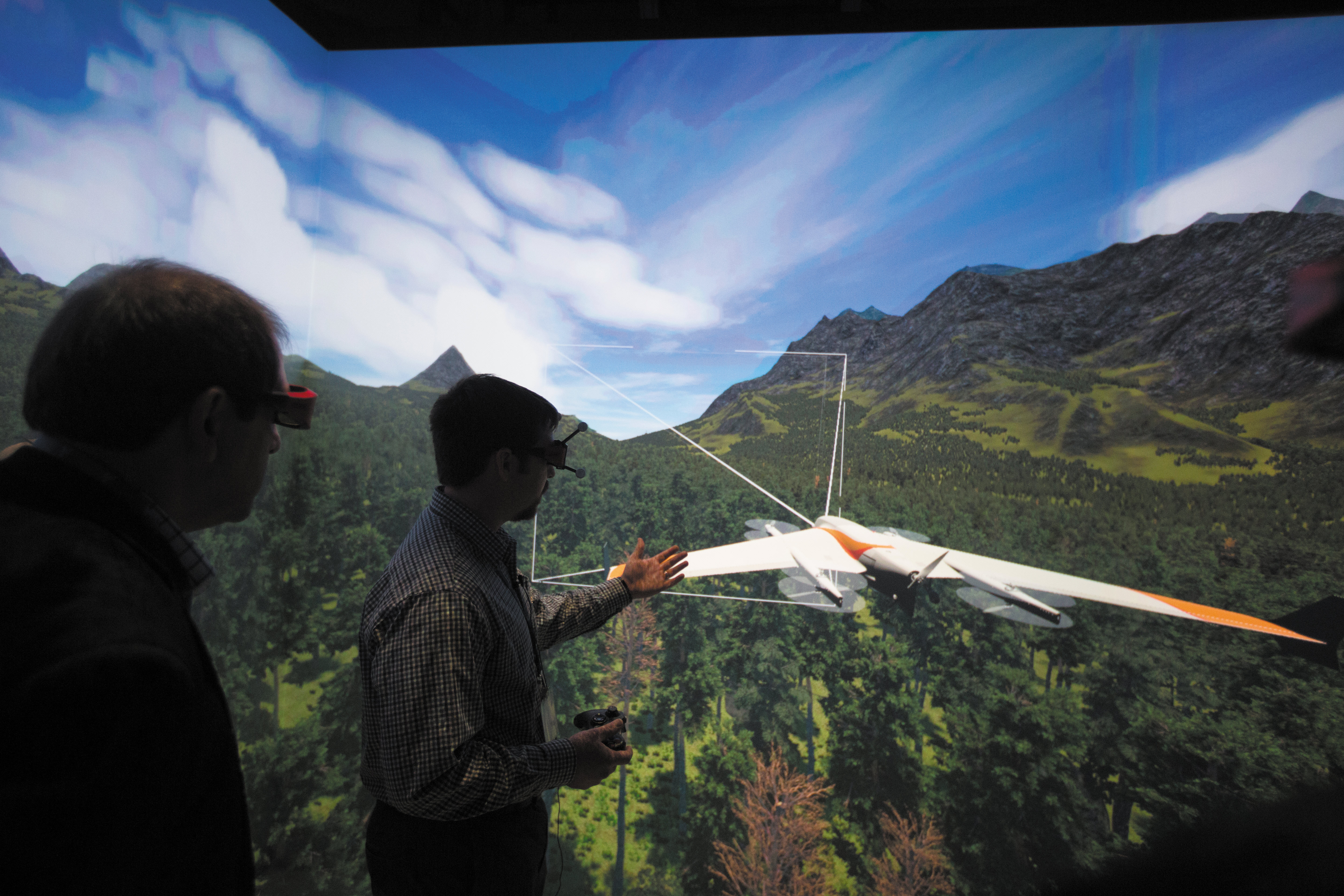
Project planning tools for on-time delivery
The team also defined a development schedule with planning tools from the 3DEXPERIENCE platform to ensure their project remained on track. “One of the challenges we have in industry is getting things done on time,” Ehrstein said. “The 3DEXPERIENCE platform allows us to put our requirements in early and to track those requirements to obtain up-to-date statistics based on live data. Managers know exactly where projects are at any point in time; they can detect issues and head them off before they become showstoppers.”
Digital simulation was another essential feature of the platform that helped the WSU team stay within budget. “Physical tests are expensive because when you start going out there and breaking equipment that costs money to replace,” Ehrstein continued. “So the earlier we can perform thermal and structural analyses in a virtual environment before physically flying it, the more savings we can achieve. Traditionally in the past, a designer would create a design and ‘throw’ it over the wall to the stress team only to discover that it was going down the wrong direction. Reengineering the design at this late stage is a huge effort and not necessarily the most cost-efficient approach. Our focus here is to reduce the development lifecycle by introducing testing and validation as early as possible to make sure we are headed in the right direction.”
The design and simulation applications of the 3DEXPERIENCE platform helped the students reduce development time from what is typically a three-year process to 18 months. “Now, our goal is to reduce that even further to a three- to fourmonth timeframe,” Ehrstein said. “As we get more familiar with the applications, we notice that there are many areas where we can shave time off and do a better job thanks to the full integration capabilities of this platform. I definitely think it’s doable.”
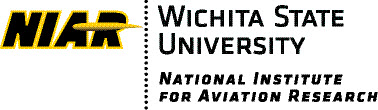
Focus on Wichita State University
A public state university dedicated to being recognized as the model for applied learning and research.
Number of students: 15,000 enrollments per year
Campus: Wichita, Kansas
For more information: www.wichita.edu