Viking Range Corporation
Cooking up culinary excellence with DS PLM
CATIA automates design of custom products
In the past, an engineer might spend a month on engineering documentation for the retro-style steel cabinetry produced by Viking Range’s St. Charles Cabinetry Division. Leveraging CATIA for knowledge-based design, Viking developed a Cabinet Configurator that automatically generates design geometry and manufacturing documentation for custom cabinets in minutes. The configurator is allowing Viking to engineer an average of 50 items per day, compared to 5-7 items per day manually.
Once the intelligent templates are created, designer Troy McDaniel simply enters the job’s key engineering parameters. The software automatically designs the cabinetry and generates all of the documentation, from bills of material to manufacturing drawings. It also generates the geometry used to create computer numerical control (CNC) programs to produce the cabinetry on a laser-cutting machine
“Because they’re steel, there’s no room for error with these cabinets,” McDaniel says. “They must fit precisely, and the configurator gives us that.”
Viking Commercial design engineers, meanwhile, use CATIA for part design, drafting, sheet metal design, product assembly, lineup assembly, suite assembly and electrical design. “CATIA’s 3D design and parametric capabilities allow faster development time and greater accuracy, along with the flexibility to easily create other sizes and configurations,” says Eric Deng, director of operations for Viking Commercial. “CATIA also helps facilitate communications with marketing and industrial design groups during the early development phase and enables quicker prototype confirmation.”
ENOVIA SmarTeam provides the discipline that keeps everyone on the same page and eliminates any excuses for making mistakes.
ENOVIA SmarTeam helps accelerate innovation
Almost every Viking product development process involves numerous engineering change notices (ECNs). In the past, ECNs were reviewed through a complex manual process lasting a month or more. “I sometimes had engineering change orders stacked up on my desk so high that I could barely see over them,” says Sheila Taylor, engineering technical information coordinator.
Because the system was paper-based, changes often remained invisible to manufacturing and purchasing until they were nearly ready to implement, raising the risk of making or buying soon-to-be-obsolete parts. The risk of working with outdated paper documents led to additional confusion.
Leveraging ENOVIA SmarTeam, Viking developed an automated workflow process that delivers ECNs to each approver electronically, with reminders when due dates approach. Documenting every step in the change order process, including who made the change, when, and why, takes just seconds. Taylor knows immediately which ECNs are at risk of falling behind – and her desk is no longer buried in paper.
ENOVIA SmarTeam also helps teams on opposite coasts stay in synch. “It provides a systematic and consistent flow of communications and approvals between California and Mississippi among all departments including engineering, production, purchasing, quality control, service and industrial design,” Deng says. “ENOVIA SmarTeam makes it easy to share drawings, BOMs, and deviations, and increases visibility at all levels, from users to management.”
Dan Lyvers, vice president of engineering, observes that consistency is critical to quality. “Each of our engineering teams had developed its own individual processes and standards, which had grown up around its people and products but which were not conducive to doing business as a single entity. ENOVIA SmarTeam provides the information infrastructure that gives everyone access to parts designed by other teams and delivers common processes built on proven best practices.”
Our CATIA-based cabinet configurator enables us to design and build all-steel cabinetry in approximately 50% of the time it would take otherwise.
Improved efficiency for greater innovation
ENOVIA SmarTeam workflow has dramatically reduced the time required to complete ECNs, the processes that drive innovation at Viking. The average time required to process an ECN was cut from 25-30 days in the past to five or six days now, and doubled the number of ECNs that can be completed in any given month.
“The increased speed with which we are able to process ECNs reduces the time required to get new products and improvements to existing products to our customers,” says Neil Littell, CAD/PLM Administrator, Viking Range. “The automated workflow also saves our engineers and designers time that they use to investigate new concepts and innovative designs.”
We selected ENOVIA SmarTeam and CATIA because Dassault Systèmes shares our vision of continuously growing and striving to be the best of the best.
Saving engineering cost and time
ENOVIA SmarTeam has helped reduce time to market and engineering costs by making it easy for engineers to find and reuse existing component designs rather than design them again. For example, Viking Commercial developed a line of more than 500 modular products and more than 250 accessories from scratch in less than two years, with parts that can be mixed and matched to deliver thousands of customer-specific configurations. “With CATIA, we can offer flexibilities in modular customization superior to our competitors,” Deng says.
ENOVIA SmarTeam also enables Viking to leverage best practices from one area across the entire organization.
ENOVIA SmarTeam makes it easy to share drawings, BOMs, and deviations and increases visibility at all levels, from users to management.
Ensuring everything is built to the latest specification
Viking Range’s Manufacturing and Purchasing departments access design documents and work instructions exclusively through ENOVIA SmarTeam. The instant anything changes,
the database and all related documents are updated immediately. This approach has saved approximately $250,000 by eliminating the production of parts based on outdated documentation, a risk with the previous paper-based approach. ENOVIA SmarTeam also ensures that teams from Mississippi to California all work from consistent, up-to-date data.
Our vision is to integrate the entire company with ENOVIA SmarTeam to drive innovation, eliminate wasted time and promote best practices throughout all of our business processes.
Future
Viking plans to leverage ENOVIA SmarTeam’s modularity and implementation methodology to replicate its successes throughout the company, gradually expanding functionality in line with users’ experience and expertise. CATIA, too, will be extended across the company’s divisions to reduce time to market and engineering costs, primarily by leveraging knowledge-based design and improved sheet metal design capabilities.
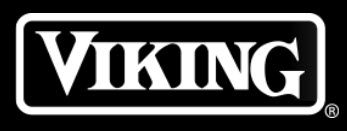
Focus on Viking Range Corporation
Viking Range Corporation introduced professional-quality cooking to the home when its first range shipped in 1987. The company’s passion for perfection is relentless. For example, the Viking simmer burner works at such low temperatures it can melt every chocolate chip on a paper plate without damaging the plate. “We provide not just appliances, but a complete epicurean experience,” explains Brian Waldrop, the company’s chief financial officer. In the process, Viking sparked a renaissance in its historic hometown of Greenwood, Mississippi, USA, renovating historic buildings for its offices and opening a hotel, restaurants and a world-class cooking school visited by renowned chefs from Jacques Pepin to Emeril Lagasse.
For more information
http://www.vikingrange.com