Valmet
With 3DLean, Valmet improved collaboration and transformed their meetings to improve performance while ensuring their meeting practices aligned with corporate targets.
DELMIA 3DLean was the first solution that made it possible for us to have interactive discussions, supported by a clear agenda for the meeting and an action log, which stores and follows up on agreed actions. As soon as we deployed 3DLean, I noticed an immediate
benefit.
The challenge
Valmet, a global developer and supplier of process technologies, automation and services for the pulp, paper and energy industries, wanted to evolve its networked global production environment and support employees with modern working practices. To sustain its competitive advantage, the company sought an online meeting and collaboration tool that would support multi-site meetings, integrate with digital data sources, deliver strong action management and ensure all tasks and supporting data are readily available after each meeting.
The solution
The company’s Board and Paper Business unit implemented DELMIA 3DLean on the 3DEXPERIENCE platform to improve collaboration and transform its meetings and follow-up processes, empowering teams to improve their performance and ensure their meeting practices align with corporate targets. Valmet’s teams use the digital visual management board and intuitive shared environment on the cloud to support their meetings, and make decisions and manage actions guided by rich content and Lean principles.
The benefits
DELMIA 3DLean is enabling positive change in Valmet’s daily management processes, giving management better visibility of their operations and Lean practices, and empowering teams to run more efficiently. Now, both office and shop floor workers clearly understand their goals and leave each meeting with a clear view of actions and who is responsible for them. Meetings end on time with all topics covered, team members are more engaged and willing to contribute ideas and
content, and problems are more easily identified and quickly resolved.
Driving automation and innovation in pulp, paper and energy
Organizational agility and a lean mindset have been the driving force of Valmet’s product development strategy throughout its 220-year history. In that time, the company has adapted constantly to the ever-changing requirements of the paper, pulp and energy industries. Today, Valmet is one of the world’s leading providers of process technologies, automation and services to these sectors.
As the company rises to the challenges of the digital era and pursues new sustainability targets, its innovation efforts remain focused on helping customers use their resources more efficiently. Through the Industrial Internet and digitalization, for example, it is capturing opportunities to improve the support it provides for hundreds of machines around the world and using real-world operating data to enhance future designs.
Not only is Valmet committed to helping its customers embrace technology to achieve resource efficiencies, but the company is also underway with its own digital transformation to improve the way it operates. As part of this, it has implemented the advanced meeting and collaboration tool DELMIA 3DLean on the 3DEXPERIENCE® platform.
From paper to digital meetings
DELMIA 3DLean is a web-based meeting tool that provides the framework for Valmet to foster collaboration and boost team performance. It’s designed to promote a Lean culture, harmonize shop floor processes and improve company-wide quality. During meetings, it helps to keep all team members focused and allow them identify and solve issues before they turn into bigger problems through clear communication and the ability to visualize rich 3D content and data.
“We had looked into using a digital tool for this kind of thing before, but they only worked with static data,” said Ari Linsuri, Director of Sales and Operations Planning at Valmet’s Board and Paper business.
Linsuri’s Sales and Operations Planning team is responsible for managing customer deliveries and optimizing resource capacity. Distributed over two sites, it oversees Valmet’s Project Delivery process, which ensures all machine sections and parts produced by different sources across different regions are delivered to customers at precisely the right time for assembly. The team previously used to write on paper and a whiteboard during its daily update meetings, but Linsuri wanted to find a better way of noting down and sharing information.
“The majority of our team usually works in one open-plan office,” Linsuri said. “Every morning, when I came into the office, I’d ask how everyone is getting on and those conversations helped to inform what was happening across the team and highlight any issues we may face. But I realized that it would be useful if the rest of the team members also had access to this information. We moved to short, daily meetings and I wrote the agenda up on the whiteboard and made notes. But sometimes there was too much to discuss,
we missed information or did not write important tasks down. And meetings often overran.”
Valmet made the decision to implement DELMIA 3DLean to not only ensure meetings were more productive, but also to support its workforce with digital tools that promoted more efficient ways of working.
Keeping the global S&OP team informed
With DELMIA 3DLean and its visual management board, Linsuri is able to ensure meetings stay focused, cover all points on the agenda and stay within the allotted time. He uses the tool to plan his meetings effectively.
“The way 3DLean is set up is that the screen is divided into different meeting boards and each has its own agenda,” Linsuri said. “For example, on Monday we pull up the sales projects on the screen and we can see all items on the agenda related to that area. It helps me remember what we need to handle and is always updated with the latest information. We have a clear agenda to follow and can assign tasks to team members as we go.”
With a clear view of the meeting format, team members are now more willing to actively engage. “3DLean is easy to use, so when we are in front of this screen, I can ask individual team members to take over and run different parts of the meeting,” Linsuri said. “It helps to get everyone involved and makes our meetings much more fluid and dynamic.”
Critically, anyone in the team can revisit the virtual meeting board to check the latest updates. So, even if they miss a particular meeting, they can still access the information they need and get up to speed quickly.
“Everyone in the team has a personal login to the system, so they can read the notes and see which tasks have been added to their responsibilities,” Linsuri said.
Tracking key tasks on the shop floor
As DELMIA 3DLean is gradually rolled out across the company, more teams beyond the office are benefiting from the new digital meeting approach, including Valmet’s workshops.
“We use 3DLean in our meetings to monitor our production status,” said Kyösti Häkkinen, workshop manager at Valmet, overseeing more than 60 employees on the shop floor. “It gives our meetings structure and we can update it as we go so we don’t forget any important issues, such as a safety issue.”
DELMIA 3DLean helps the workshop track tasks against key performance indicators (KPIs) and resolve production issues early on.
“We used to juggle all kinds of issues and now you take each KPI and follow up on it easily,” Häkkinen said. “3DLean allows us to see the bigger picture, and from that we can identify potential problems and take action. By having this kind of system, we keep everyone in the team updated as to what is going on.”
The workshops run several meetings per week, all with different agendas supported by 3DLean. They find the action log feature in DELMIA 3DLean particularly valuable. “At the beginning of every meeting, we check the action log and at the end we check it again and identify any new actions we must prioritize,” said Anssi Puttonen, workshop manager at Valmet, overseeing 100 employees on the shop floor.
“These action logs help us to find all the agreed actions from different meetings in one place. It’s all there and the takeaway actions are available for everyone to see. The ability to follow up on tasks and issues is really helpful.” — Anssi Puttonen, Workshop Manager, Valmet
Puttonen has noticed that because meetings are now much more focused, they now generally take half the time compared to before.
“Our meetings are shorter,” he said. “Before, we tried to solve all issues in a single meeting, but now we’re able to delegate issues and follow up on actions in a considered manner rather than trying to do everything upfront. Meetings are more structured and efficient. They used to last around 90 minutes, but now they only take 45 minutes."
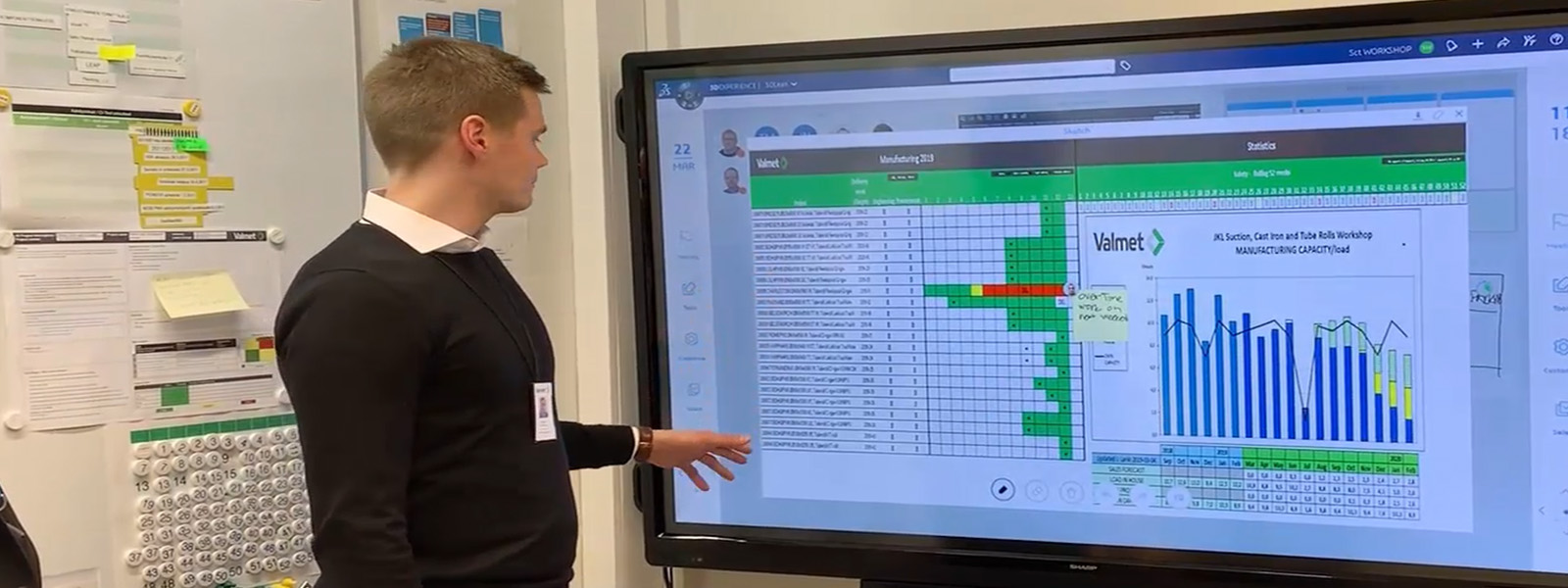
Supporting remote working during a pandemic
Even when Valmet’s teams switched fully to remote working during the COVID-19 pandemic, DELMIA 3DLean helped to keep daily meetings running smoothly online.
“The pandemic changed how we used the tool,” Linsuri said. “Until then, we used it in front of everyone on a big screen. But when we had to work remotely, we started to share it virtually and we could configure it ourselves to meet our evolving needs without IT support. It’s really flexible. Before, when we had a couple of team members working in another location, we found it difficult to organize their participation. Now, we’ve discovered how to use 3DLean when you have meetings in different locations. Going forward, we will take a hybrid approach and be able to include both people working in the office and remotely. In many ways, the pandemic has forced us to develop faster and adopt new ways of working.”
Collaborative thinking, sustainable future
Valmet’s Sales and Operations Planning team was the first in the company to go live with DELMIA 3DLean and now the company is beginning to see greater benefits as more departments embrace the tool.
“Now other teams across the company are also using it, we can begin to send action tickets and share messages across departments,” Linsuri said. “It will really help to improve cross-team collaboration and bring even greater transparency to the way we run our business, giving management full oversight of our Lean processes.”
As the company continues to deliver on its vision of becoming a global champion in serving its customers, and acts on its mission to convert renewable resources into sustainable results, digital tools like 3DLean will help the company stay focused on achieving its goals.
“Through digitalization, we are boosting employee engagement and developing the best talent to support the workforce of the future,” Linsuri said. “3DLean empowers us to build better team relationships, support flexible working and drive continuous improvements across our business, all within a digital, lean framework.”
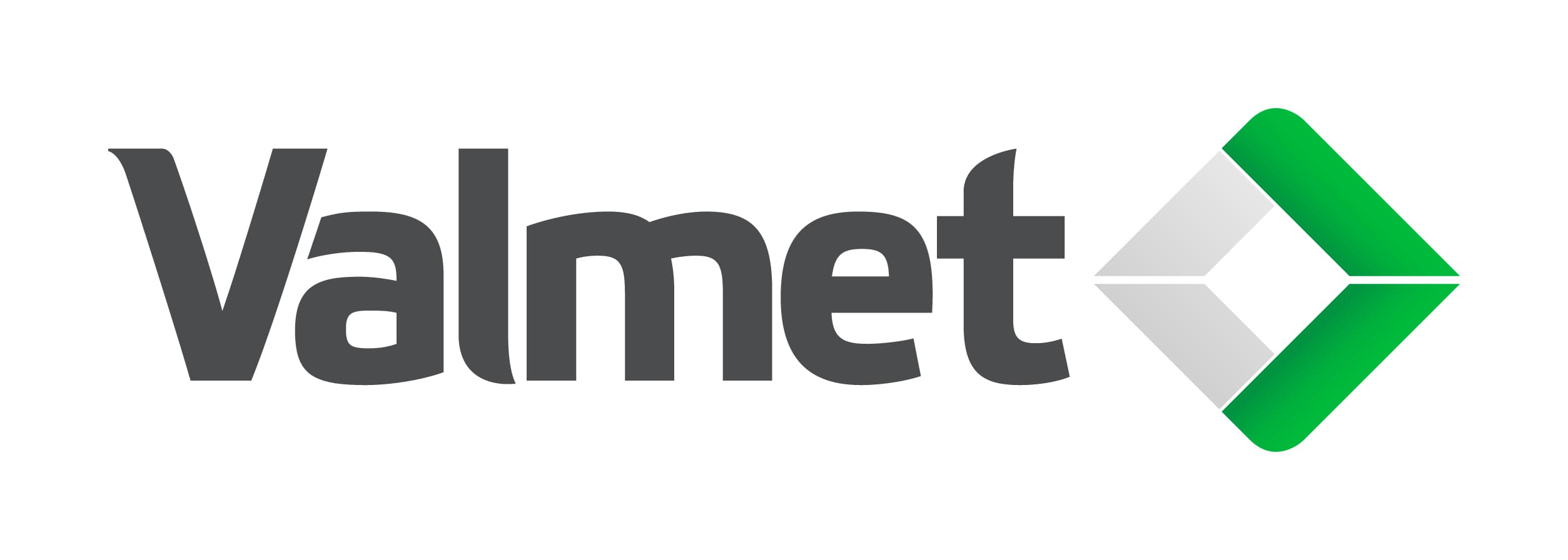
Focus on Valmet
Valmet is the leading global developer and supplier of process technologies, automation and services for the pulp, paper and energy industries. Headquartered in Finland, the company aims to be the global champion in serving its customers. It has more than 14,000 professionals around the world, all committed to moving its customers’ performance forward, every day.
For more information: www.valmet.com