University Hassan First
Simulation enables restoration workers to fine-tune repair materials in advance, match the physical properties of legacy materials and avoid potential damage to important architectural structures.
Overall, I’ve found that simulation motivates the students to work harder, and Abaqus is a wonderful tool for this.
The urge to become an engineer hits many people early on in life. Dr. Hicham Fihri-Fassi first felt the call as a young high school student. “I’ve always liked to innovate, and engineering enabled me to do just that,” he says. Dr. Fassi has since taken those teenage ambitions and made an impressive career of them—today he serves as professor of mechanical engineering at Morocco’s University Hassan First, and is a member of the Faculty of Sciences and Technologies in Settat (FSTS).
True to his drive for innovation, he’s also responsible for establishing a new research and innovation center at the university, pulling together interested experts from various industrial companies to promote the use of mechanical simulation and other engineering tools, informing and educating his students in the process.
Dr. Fassi is also very focused on the wealth of architectural and archaeological sites in the surrounding area, and has become a strong advocate of preserving them. One of the tools he uses for this work is Abaqus FEA software from SIMULIA, the Dassault Systèmes brand for realistic simulation.
Delicate matters
“Masonry buildings constructed centuries or even millennia ago were created using ancient techniques and questionable materials,” Dr. Fassi says. Add to this the deleterious effects of weather, wind, and war, and the results are poor mechanical properties and unpredictable structural integrity - what appears to be a sturdy tower or minaret may be as fragile as a house of cards. “Unfortunately,” says Dr. Fassi, “repairing these historic structures is not a simple matter.”
Restoration projects usually focus on the replacement of damaged bricks and stones. Worn mortar—the rocky glue that holds the building together—is scraped away to a depth of several centimeters so that new material can be put in its place, a practice known as repointing.
The marriage between modern masonry and centuries-old mortar and brick is not always a happy one, however. “Because contemporary mortars are substantially stronger and more rigid than those used by the ancients, so-called ‘stress shielding’ may occur after installation,” says Dr. Fassi. “This phenomenon can cause compressive stresses to form between block joints.” The result can be cracking and even crushing of the legacy brick and mortar adjacent to the newly repaired surfaces, ultimately causing more harm than good to the original structure.
That’s where Dr. Fassi’s innovative mindset has come into play. Recognizing the problems encountered during restoration of historic buildings, he began researching ways to reduce the negative effects of stress shielding several years ago. One of his first tasks was collection of legacy material to perform baseline physical and mechanical testing. But he soon found that extraction of sufficient material for analysis can be a roadblock when dealing with sensitive archaeological sites.
So Dr. Fassi turned to simulation to help solve the problem.
“One of the challenges of architectural preservation is the incompatibility between legacy masonry and the stronger, more reliable mortar and bricks available today,” he says. “We’re conscious that there are multiple natural phenomena - humidity, temperature, static gravity, etc. - that affect all buildings, but the issue of incompatibility between materials is of particular importance with ancient restored buildings. For this reason we focused our first study on incompatibility due to initial incorrect choice of material. Later we can study the effect of other phenomena.”
In the case of restoration, he says, “We have seen that partial replacement of mortar joints must be accomplished through careful attention to mechanical and aesthetic considerations, taking care to avoid further degradation. Abaqus allows us to model a wide range of replacement materials without disrupting delicate structures, and plays a critical role in the restoration of these important heritage buildings.”
Measuring the minaret
One of these buildings is Al Masjid al Aadam, a mosque in the coastal city of Safi, three hours southwest by automobile from Casablanca on the eastern shore of the Atlantic Ocean. Originally constructed in 1471 AD by the city founder, Moulay Ali Ben Moussa Ben Rached El Alami, the mosque has been partially destroyed and rebuilt several times over the centuries, and most recently repaired in 1807.
Dr. Fassi and his team chose Al Masjid al Aadam as a starting point for their research due to its historical significance as a center of Islamic worship and scientific teachings, and because the building represented the masonry work typical of the Moroccan area.
Dr. Fassi began his data collection with a translational cutting analysis, a destructive testing method common in the petroleum industry but one used rarely in architectural mechanics. Small samples of stone are collected from a representative area of the restoration site and placed into a machine tool, which then scrapes away thin layers of the subject material using a diamond coated cutter, thus determining its Modulus of Elasticity (MOE). Another testing method employs pulses of ultrasonic sound to measure material density and composition.
By collating these results, Dr. Fassi was able to determine the material property values expected in the mosque, and use that data to build numerical simulation models of the stress-shielding phenomenon in Abaqus FEA.
The study considered a restoration scenario at the front face of the mosque’s minaret, a tower measuring 21 m (68.9 ft.) tall. A mortar replacement depth of 2 cm (0.787 in) was applied, which was the assumed average depth for repointing such a structure. Using Abaqus to vary the grout density parameters, Dr. Fassi simulated stress shielding using MOE values between 1 to 30 times those of the joint materials encountered in the
minaret, and 40 to 120 times the measured block values. He also applied anticipated load values for the structure based on calculations of its height and mass.
Dr. Fassi’s approach produced a number of useful results, including a “worst case” simulation that highlighted the stress shielding that might occur under extreme conditions. This offered researchers a unique view into previously invisible and lengthy structural deterioration. The results from Abaqus clearly support the damage observed by field workers in restored heritage buildings, and presented Dr. Fassi and his collaborators with graphic representations of the rise in compressive stresses as masonry MOE values increased.
The failure mode of the surrounding block was made visible as well, further confirming the need for carefully selected restoration materials that have mechanical properties compatible with heritage masonry. Considering the cost of failure incurred through traditional trial-and-error restoration that was approached, it’s obvious that Dr. Fassi’s work is an important contribution to the science of architectural repair.
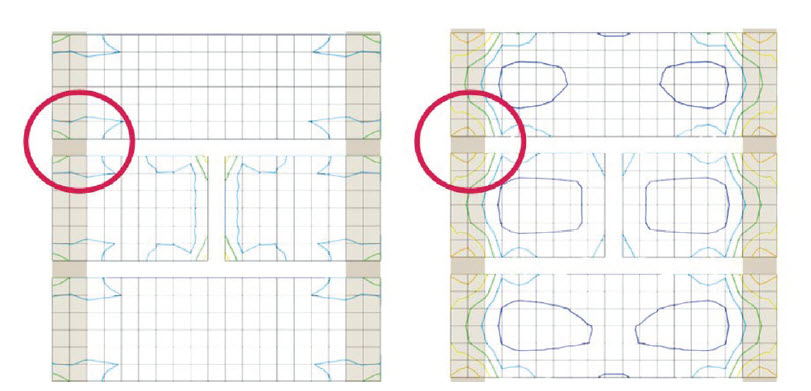
Simulation benefits both work and life
Dr. Fassi has been using Abaqus since 2008, and says it helps him create more designs in less time as well as greatly simplify the validation of such designs.
“It’s a very flexible software program,” he says. “I’ve been able to take on new projects without having to use physical materials, something that reduces costs and is far more efficient: what once took me four or more hours to simulate can now be done in 15 minutes. I’m happy to say that simulation helps a great deal with my work-life balance.”
This last point is especially important to Dr. Fassi, who enjoys nature, hiking, and spending time with his wife and three children, two of whom followed their father’s love of art and painting, choosing architecture as their career paths.
His students enjoy Abaqus as well. Dr. Fassi says they can progress in their simulation skills at their own pace, with little assistance from him or the other professors at the university. “They are able to integrate Abaqus with our MATLAB [the scientific programming language] environment to create perfectly complete meshes on their own,” he says. “Overall, I’ve found that simulation motivates the students to work harder, and Abaqus is a wonderful tool for this.”
Despite his impressive accomplishments thus far, Dr. Fassi is just getting started. He presented his findings at the 2015 Simulia Community Conference in Berlin, and returned to Morocco to continue his research on heritage building restoration. As part of this next step, he and his team explored other options for simulation software, but found Abaqus to be the most complete solution for nonlinear analysis such as this. They are now using Abaqus along with CATIA and SolidWorks for a broader spectrum of projects, including a scooter design
and even 3D printing.
Now Dr. Fassi and his team are developing a search for local, natural materials that can be used in restoration, and a new numerical model involving plasticity and contact with friction.“Abaqus helps reduce risk to valuable structures in Morocco and elsewhere,” says Dr. Fassi. “Because we can quickly simulate the effect of various building materials, we are able to assist in the development of practical tools and restoration standards. It’s very encouraging for the future preservation of our architectural heritage around the world.”