Trier University of Applied Sciences
Trier University of Applied Sciences delivers an industry-focused curriculum where students at the Department of Engineering acquire the fundamental concepts of the 3DEXPERIENCE platform on the cloud in a hands-on learning environment. For Project HAMLET, Students used the platform to transform medical imaging data from a CT scan into a realistic 3D-printed model of a skull, handling all aspects of the product development process within the platform.
We’re very much oriented towards what the big players use. The 3DEXPERIENCE platform is such an advanced interdisciplinary solution and gives students a complete, end to end view of the product development lifecycle of strategic projects.
Modular skull model transforms neurosurgery training
At the Barmherzige Brüder Hospital in Trier, Germany, medical students and junior residents hone their skills in manual surgical procedures on a skull without a human or cadaver in sight. Instead they work on a 3D-printed model, where they can practice milling and punching the skull bone and carrying out procedures like craniotomies, burr holes, biopsies and computer assisted techniques.
This 3D-printed model is the result of an innovative project by students on Mechanical Engineering and Sports and Rehabilitation Technology courses at Trier University of Applied Sciences. Anne Meier and Lena Pitz, both sports and rehabilitation technology students, worked on the project ‘HAMLET’ (Haptic Applications for Medical Learning, Experimenting and Teaching) in various learning modules and picked up three prizes on behalf of the team at the Rhineland-Palatinate ideas competition for their groundbreaking work. The team was celebrated for making an excellent and creative contribution to the field of medical training through their engineering studies.
The university they attend, also a 3DEXPERIENCE Center of Excellence, is renowned for its industry-focused, hands-on curriculum. There, students like Meier and Pitz are equipped with the transferable skills to think outside the box. What was particularly special about Project HAMLET was that it bridged the gap between mechanical engineering and medical engineering, growing from an idea between the university and hospital to help medical students progress with their neurosurgical studies and perform basic training scenarios like brain tumor biopsies in an innovative, cost effective and sustainable way.
“We attach great importance to project-based teaching and encourage students to engage in solving real-world problems,” said Michael Hoffmann, head of the lab “Digital Product Development and Manufacturing” (LDPF) in the Department of Engineering at Trier University of Applied Sciences.
Being able to quickly create patient-specific models could be an additional way to improve patient outcomes and minimize surgical risk.
Project-based approach to learning
Trier University of Applied Sciences has a long-standing partnership with Dassault Systèmes, through which students gain full access to the 3DEXPERIENCE platform on the cloud to support their studies. One of the main reasons the 3DEXPERIENCE platform is Trier UAS’s technology of choice is to give students access to the same tools they are likely to use in their future careers. This equips them with the skills they need once they graduate and prepares them better for the working world.
“We’re very much oriented towards what the big players use,” Hoffmann said. “The 3DEXPERIENCE platform is such an advanced interdisciplinary solution and gives students a complete, end to end view of the product development lifecycle of strategic projects. Students learn to use the system but also apply strategic and methodical working methods. We also value the fact that it’s cloud based so that students can access the platform at university or at home and continue their studies wherever they are.”
Hoffmann and his colleagues deliver comprehensive courses to help the students master the 3DEXPERIENCE platform’s rich functionality and project-based approach. Within the first semester, they cover basic functionality, including part and assembly design. From there, students progress to more advanced applications so they can pursue more complex projects like HAMLET.
“Supported by the 3DEXPERIENCE platform, we’re able to deliver solution and process-led teaching and advance these types of technology transfer initiatives,” Hoffmann said. “Our students are given all the tools they need to be creative and see their ideas through to finished products, which repeatedly find their way into industrial applications or startups.”
“It took one semester to find my way around the 3DEXPERIENCE platform,” Pitz added. “Then, we had the freedom to experiment on our own for Project HAMLET, which is when I began to grasp how big and powerful it is.”
With the help of the 3DEXPERIENCE platform in the cloud, Meier and Pitz transformed anonymised clinical medical image data from a CT scan into a 3D model. This formed the basis for the realistic, modular 3D-printed skull, which can be used to practise neurosurgical procedures.
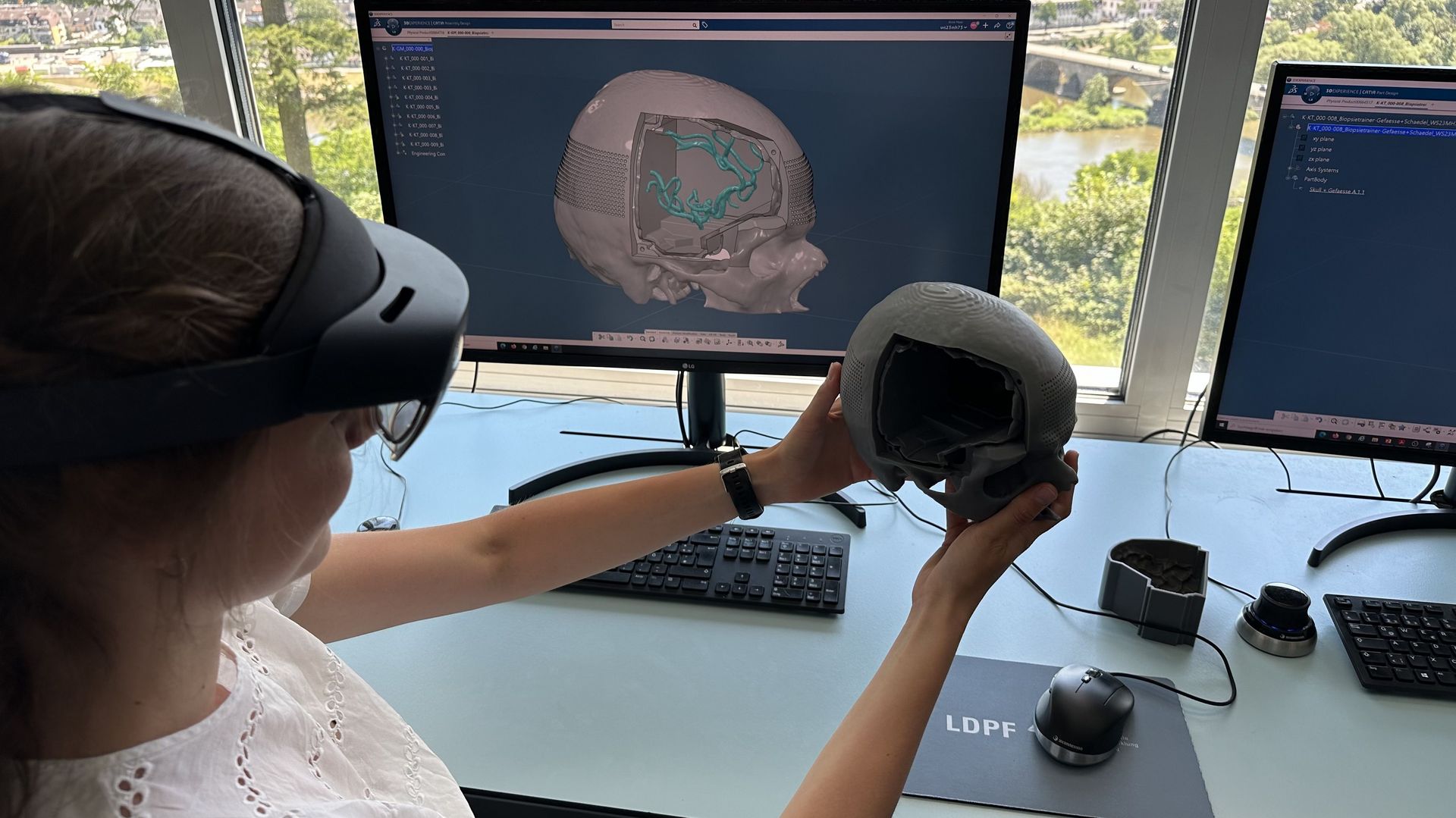
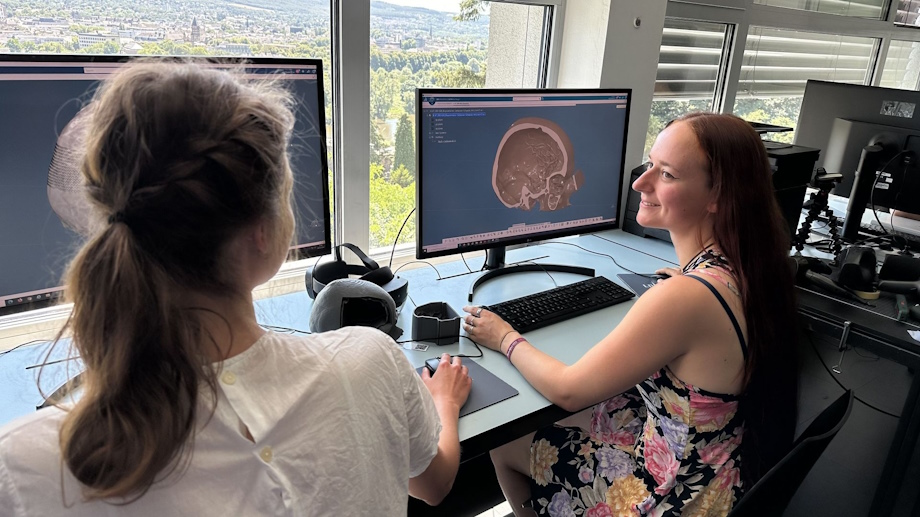
CT scan data forms basis of 3D printed skull
Using the 3DEXPERIENCE platform on the cloud, Meier and Pitz transformed anonymized, clinical medical imaging data from a CT scan into a 3D model. This formed the basis of the realistic 3D printed modular skull that could be used to practice neurosurgery procedures, even in combination with advanced multimodal MRI (magnetic resonance imaging) data.
“We received DICOM (medical) data from the hospital and transformed it into a 3D-CAD model in the 3DEXPERIENCE platform,” Meier said. “After we prepared the data, we developed the assembly design for the components that would make up the modular 3D printed skull with interchangeable components.”
The final skull is made of a combination of the 3D printed model and materials including composites, latex, silicon and gelatin to resemble the anatomy of the skull and brain adapted to the training task. Throughout the project, the students communicated closely with the hospital’s neurosurgery department to share ideas, receive feedback and make sure the model met its specific needs. All collaboration was handled on the 3DEXPERIENCE platform.
“We used the 3DEXPERIENCE platform to create a solid that we could print, and we experimented a lot with different materials so it felt like real bone,” Pitz said.
“When we had an idea about a material we could use it for the design of a particular component, we could build and test it in the platform and share the digital model,” Meier added. “It was invaluable being able to connect directly with the hospital and have people from multiple disciplines working together.”
When we had an idea about a material we could use it for the design of a particular component, we could build and test it in the platform and share the digital model. It was invaluable being able to connect directly with the hospital and have people from multiple disciplines working together.
Modular design reduces costs of surgical training
Even using models for training can be very cost and material intensive. Students at medical school use the same surgical instrumentation and tools in the training experience as they would in real surgery, so inevitably end up drilling and cutting through material. That’s why the 3D printed model needed to be designed with interchangeable components so that it wouldn’t need to be replaced in its entirety after every procedure.
“The skull itself is the most costly and time-consuming part to print, so we focused on creating modular parts around it that could easily be renewed and wouldn’t be as expensive to replace,” Pitz said. “We used the collaborative lifecycle management functionality in the 3DEXPERIENCE platform to test and refine each part and keep track of every iteration. The team did the project over a period of 18 months across different modules in our studies, so it was invaluable being able to manage and keep a record of everything we did in the platform.”
Procedures such as brain tumour biopsies are highly structured, and using the 3D model, students can learn the essential steps to performing surgery with neuronavigation systems, including planning, determining a safe approach, opening the skull and using technical equipment.
Realistic experience for neurosurgical specialty training
In many cases, digital models and virtual reality training cannot yet replace the act of physically practicing on a human specimen, especially when it comes to getting a real sense of how it feels doing these technical procedures. Yet the escalating cost of cadavers, not to mention the issue of acquiring, transporting, preserving and disposing of them, demands a more affordable and sustainable approach. Dr. Marcus Mehlitz, deputy head of the Brain Tumor Center and senior consultant in the department of neurosurgery and pediatric neurosurgery at Barmherzige Brüder Hospital, found the simulated experience with the 3D printed model offered a realistic representation of how neurosurgery procedures play out in the operating theater.
“Cadaver specimen are still the gold standard for the training of advanced surgical skills, yet the use of the 3D model exposed the same handling problems we see in the operating theatre by less experienced surgeons,” Mehlitz said. “It’s proving a safer and more affordable approach to medical education that provides a similar experience to traditional cadavers. Through this project, we wanted to explore the potential of using 3D printed models to apply anatomical knowledge in a specific training scenario, again and again. Becoming a surgeon is all about repetition and being able to practice in a non-pressured setting like this really makes a difference.”
We used the 3DEXPERIENCE platform to create a solid that we could print, and we experimented a lot with different materials so it felt like real bone. With the collaborative lifecycle management functionality in the 3DEXPERIENCE platform, we could test and refine each part and keep track of every iteration.
From education to personalized patient treatment
Procedures like brain tumor biopsies are very structured and students can learn the essential steps to perform surgery with neuronavigation systems, including planning, defining a safe approach, opening the skull and using technical equipment. Offering realistic simulated training helps to show medical students exactly what it will be like to be a neurosurgeon and supports junior residents with more advanced procedures. Many value the opportunity to learn in this way and the neurosurgical program for medical students receives excellent evaluation results because of this.
“To capture the attention of the brightest and manual gifted minds, you have to deliver first-hand experiences to show what neurosurgery is all about,” Mehlitz said. “With limited financial resources, we’re able to do exactly that and deliver fun, interactive workshops.”
“The most interesting and exciting part of this project was having the opportunity to visit the hospital and see what we’d created in action,” Meier added. “It was so cool to see how our model was being used in a realistic simulated surgery session.”
Work is now underway to add new features to the 3D printed model, such as monitoring pathways of the brain, and support other training scenarios. Beyond training and clinical research, it is hoped that projects like this might be used in the future to support even more personalized patient treatment and interventions.
“Augmented reality will be a standard technique in surgical treatment and training within the next decade,” Mehlitz said. “Being able to quickly create patient-specific models could be an additional way to improve patient outcomes and minimize surgical risk.”
More about Project HAMLET
Project HAMLET won three awards in the Rhineland-Palatinate 2024 ideas competition, funded by the Rhineland-Palatinate Ministry of Economic Affairs, Transport, Agriculture and Viticulture in Germany. The team accepted the special medical prize, the Trier regional prize, and picked up first place in the state prize.
For more information: HAMLET

Focus on Trier University of Applied Sciences
Trier University of Applied Sciences stands for practice-oriented learning, forward-looking research and teaching. It is a place of innovation, artistic and scientific work. With around 7,000 students, it is one of the largest universities of applied sciences in Rhineland-Palatinate, located in the immediate vicinity of Luxembourg and France.
Within the university’s Laboratory for Digital Product Development and Manufacturing in the Department of Engineering, students are shown how to use modern cloud-based product lifecycle management systems and adopt interdisciplinary engineering processes, covering design, development, simulation, production, disposal and recycling of sustainable products.
For more information: https://hochschule-trier.de/en