Sunreef Yachts
Sunreef Yachts uses Dassault Systèmes’ applications for design and realistic simulation to optimize the engineering processes of their highly customized luxury catamarans.
Addressing new sailing experiences
Creating a company to manufacture luxury catamarans on the belief that features such as living space, high-quality materials and ergonomics were preferred by many clients over speed and power was a gamble. However, Sunreef Yachts’ founder Francis Lapp was convinced there was a market for these vessels alongside the more customary yacht. “When I founded Sunreef Yachts in 2002, privately-owned luxury catamarans were nonexistent,” Lapp said. “But I sensed that tastes had evolved. Many yacht owners come to Sunreef because they want to switch from a mono-hull vessel to a catamaran because a catamaran is more stable due to its double hull. Moreover, it can provide a more ample living space providing a better sense of conviviality and community than narrower, longer yachts,” Lapp said.
“And Luxury,” Lapp continued, “is also to be able to go where yachts cannot go. By this, I mean sailing around the world with a catamaran is feasible, whereas with a yacht, even a big yacht, it’s not always the case because of the yacht’s instability and lack of autonomy. In effect, a catamaran has more autonomy because there is less hull friction in the water, so less drag and better fuel consumption. Just think, on an 18-meter catamaran, we can cross the Atlantic Ocean on one full tank of fuel. This is not necessarily possible with a 40 or 50-meter classic yacht.”
Thanks to SIMULIA XFlow, we can test several scenarios— different shapes, wind speed, sea conditions—and get our results quickly to come up with an attractive shape for optimum seaworthiness and fuel consumption.
A feeling of trust and cooperation
The company’s high-end luxury products are built for the world’s most demanding and discerning customers. They expect a product delivering the best in design, safety and luxury. Combining fresh design, seaworthiness and customization, as well as other important aspects such as energy efficiency, reliability and high performance, is not an easy task. All this has to be factored in when new model design starts, and understanding the hull plays a crucial role. Building confidence, therefore, is vital for Sunreef Yachts. “Coming up with an appealing, easily customizable and seaworthy product is only possible when you have a powerful tool for design and simulation. It’s critical for our customers that we virtually verify the 3D design model of the vessel,” Piotr Hinczewski, design office director at Sunreef Yachts, said. “The shape of the hull depends on many small details, which we can modify to achieve different aspects, like high energy efficiency or high speed in the case of a motor boat, while still being easy to navigate,” he continued. “However, all these details need to be taken into account in the design and illustrated as the design progresses.”
To achieve this, Sunreef Yachts implemented Dassault Systèmes SOLIDWORKS® design applications and SIMULIA® XFlow to digitally simulate and verify the vessel’s seaworthiness before finalizing a design. “We perform computational fluid dynamics analyses with SIMULIA XFlow to see how the boat will behave. And if we want to investigate a new design idea, we develop the concept in SIMULIA XFlow, which checks the boat’s aerodynamics and hydrodynamics through digital simulations,” he said.
”To correctly design or tune the propulsion system, we need the hull resistance curve which can be derived from XFlow. This defines the power required to propel the yacht, including both hydrodynamic and air resistance for various speeds and environmental conditions. With this information, we can choose the correct engine, match up the best propellers and select the sail plan, as the software can simulate close to real yacht conditions. For example, for a 40-foot motor boat with a high-performing engine, we need a shape that will allow us to go fast. On the contrary, with a 60-foot sailboat speed may not be as important, so the hull shape will be completely different compared to the 40-foot powerboat. Thanks to SIMULIA XFlow, we can test several scenarios—different shapes, speeds, sea conditions—and get our results quickly. Based on the results, we come up with an attractive shape for optimum seaworthiness and fuel consumption. And if the client wants to install a new feature, we need to make sure it doesn’t adversely impact the boat’s speed or navigability,” Hinczewski explained.
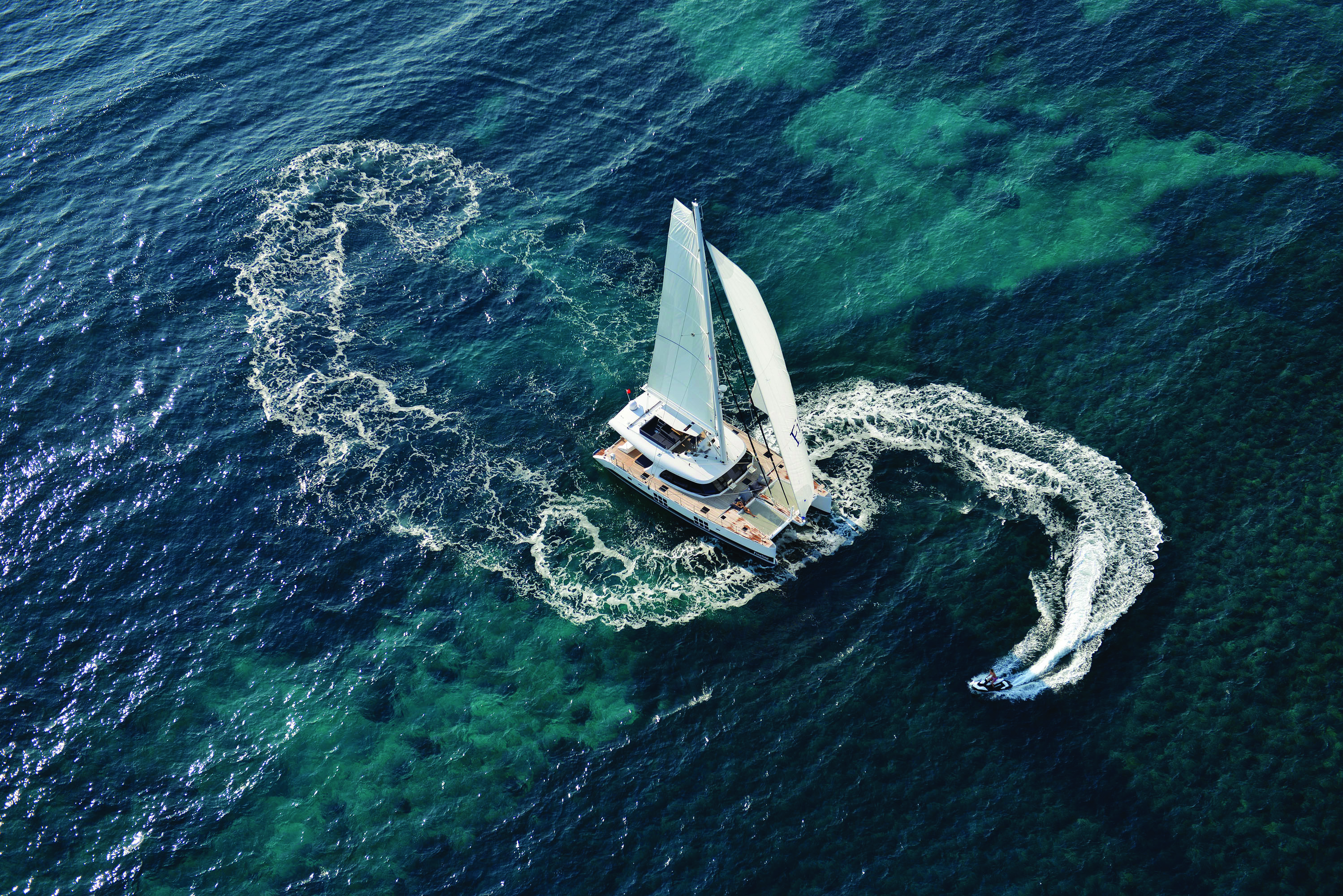
Breakthrough in shape optimization
Sunreef Yachts are very comfortable boats and include high-end luxury equipment. Consequently, much attention is given to weight. In order to meet the desired performance, shape optimization is a key success factor for achieving the best hydrodynamics and energy efficiency and leads to a better understanding in terms of engine choice, fuel efficiency and possible sail options.
According to Michal Krula, hull designer and CFD specialist at Sunreef Yachts, “shape optimization is crucial because it enables us to make our boats appealing and seaworthy.” The specific simulation capabilities that started in the automotive and aerospace industries offer a big advantage for Sunreef Yachts. “It allows us to avoid physical prototyping and testing that would require having a test pool for our boats. I think it’s a breakthrough in fluid dynamics and simulation. We don’t need physical testing, which is costly and time-consuming. We sit at our computer and simulate all possible real-world scenarios or conditions to understand the behavior of each boat model,” Krula said.
Our response time has considerably improved—to build a 74-foot boat takes us 3 ½ months compared to 6–7 months in the past.
Krula explained, “We need to virtually test the 3D design against sea conditions, such as how waves and currents affect the performance and energy consumption at different speed levels, or how the outside temperature and wind influence the behavior of the boat, or how much the wind drags the boat and how the boat reacts under different sailing situations. We, therefore, begin by defining what we want to achieve, for example reducing water drag for the hull. We then prepare the models, play with the different parameters, such as different wave heights, wave lengths and wind speeds, get the results from XFlow, such as where the drag increases, and optimize the hull in the places where XFlow tells us there is room for improvement. We can run endless simulations because XFlow is so fast.”
Besides that, the company realized that virtual simulation opens many possibilities, like thinking outside the box to test unusual ideas. “We can create abstract shapes and simulate them any way we want. For example, we can test hulls that are unconventional or try different stabilizers. I can say we’ve increased our power of innovation. It actually increases our imagination in the design process and helps us make the right decisions. I can even say it’s a revolutionary way to design boats,” Krula said.
With SIMULIA XFlow, we can run endless simulations; we can create abstract shapes and simulate them any way we want—a revolutionary way to design boats.
Multi-disciplinary collaboration
Another advantage is the fact that the different departments use SOLIDWORKS for design. “Once the correct design is created in SOLIDWORKS, all disciplines, such as the construction department, the electrical, hydraulic and mechanical systems departments, as well as the engineers working on interior design, all share and work on the same model,” Hinczewski said. “It’s easier to coordinate all of the systems, interior or construction elements, enabling them to avoid clashes that will cause production or assembly problems later on. Moreover, documentation is right the first time. There is no need to make revisions because designs have changed along the way. It’s automatically updated as the design progresses,” he said.
Sunreef Yachts can now run realistic simulation scenarios in a fast loop to know quickly how to improve hydrodynamics and aerodynamics, and ensure that they can accomplish all aspects of safety while meeting speed expectations and energy efficiency. Prior to using SIMULIA XFlow, Sunreef would outsource simulation to a third-party, but now can perform these analyses in house, check the results immediately and make corrections to the design in SOLIDWORKS right away. “Our response time has considerably improved,” Lapp said. “Before it took us 6–7 months to build a 74-foot boat; today an 80-foot vessel takes us 3 ½ months.”
Francis Lapp said there is a market for large 50 to 60 meter catamarans as well, which are also ecologically-friendly with electric or solar-powered engines and eco-friendly furnishings. “We are currently experimenting with a revolutionary solar panel that will be directly integrated in the hull or mast,” Lapp said. “Our future, therefore, involves intensive use of high performing SOLIDWORKS and SIMULIA XFlow applications, because we are planning to build these bigger boats,” Hinczewski said. “They are key to our future development.” Instead of simply selling boats, Sunreef Yachts aims to promote a philosophy that provides its clients with an exceptional sailing experience, ample living areas and quality after-sales services. “We build close relationships between the shipyard and client because it creates an overall sense of family and that is our trademark,” Lapp concluded.
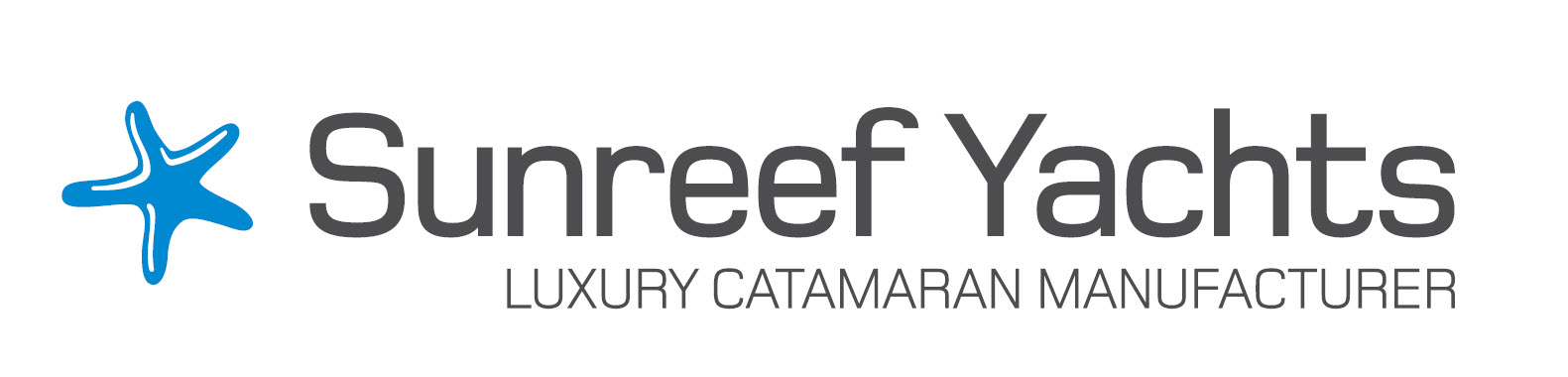
Focus on Sunreef Yachts
Sunreef Yachts is a world-leading manufacturer of custom-made luxury catamarans.
Products: Power and sailing catamarans and yachts
Employees: ~700 (2019)
Headquarters: Gdansk, Poland
For more information www.sunreef-yachts.com