Stelweld
Polish Stelweld is shaping the future of metal fabrication with its latest welding techniques and adopted the 3DEXPERIENCE platform to refine its production processes. With the Digital Equipment Continuity industry solution experience, the company can create a seamless workflow and has the ability to simulate and virtually test product designs, helping them to meet customer demands faster while maintaining high quality standards.
By integrating Dassault Systèmes’ latest software solutions combined with our cutting-edge machinery, we can continue to scale and add new functionality as we need it to improve our processes and redefine what’s possible in the metal fabrication industry.
Innovation meets quality in metal fabrication
From its state-of-the-art research and development (R&D) center in Jelcz-Laskowice, Poland, Stelweld is shaping the future of metal fabrication. Inside, 3D scanners, machines and devices for: static and fatigue test, Charpy impact test, hardness test, microscope, laser cutting machines, milling centers and robotic welding systems are busy at work creating and rigorously testing metal products. This hub of creativity and technical excellence is a proving ground for the latest welding techniques and advanced manufacturing processes.
Every year, Stelweld transforms around 12,000 tons of steel into critical components such as bus axle frames, wheel loader frames, railway steel structures, lifting booms and fuel tanks. Innovation is a philosophy embedded in every weld and cut as the company develops new production methods to meet the evolving demands of the heavy mobile machinery and transportation industries. Robotic welding systems with double-arm configurations drive faster, more controlled manufacturing. Offline welding preparation and programming further enhance efficiency, while advanced inspection machinery guarantees flawless results.
Technology plays a pivotal role in Stelweld’s innovation journey as it continually enhances its expertise and in-house engineering capabilities. Initially relying on a legacy CAD solution, Stelweld sought more advanced capabilities and transitioned to a modern, scalable technology platform to unify its modeling, simulation, project management, and process management functions. Dassault Systèmes’ 3DEXPERIENCE platform proved the ideal solution, integrating CATIA for advanced design, SIMULIA for simulation and analysis, and ENOVIA for product lifecycle management. This holistic digital ecosystem supports a seamless transition from part design to production, reducing waste, improving process and product quality, and accelerating development timelines along the way.
“Our goal is to set new benchmarks in quality and efficiency,” said Sławomir Karwala, design and technology director at Stelweld. “By integrating Dassault Systèmes’ latest software solutions combined with our cutting-edge machinery, we can continue to scale and add new functionality as we need it to improve our processes and redefine what’s possible in the metal fabrication industry.”
An insight into the different production processes at Stelweld:
Saving time and resources in metal manufacturing
As a production services provider, Stelweld’s main role is to manufacture products according to the specifications provided by its customers. To devise more effective and economical production solutions, the R&D and design teams are involved early in the product development process.
“We can help to shape the design to make it more efficient from the onset, while adhering to the highest quality standards,” Karwala said. “CATIA allows for faster and more precise collaboration with customers, who often use the same CAD software.”
Stelweld uses CATIA to prepare production documentation, such as 3D models for cutting, and drawings for bending, machining, and assembly. It then generates the bill of materials, translating all customer documentation into internal requirements for production. Using 3D models is advantageous because designers can collaborate on the same model simultaneously and work more productively.
“Multiple designers can work on the same assembly or structure, which wasn’t as seamless with our previous software,” said Daniel Gwóźdź, chief designer deputy and 3DEXPERIENCE platform implementation project leader at Stelweld. “It allows us to prepare documentation for large and complex assemblies in a shorter amount of time.”
The advantages extend beyond effective collaboration. Within the 3DEXPERIENCE platform, Stelweld refines every detail before production begins, such as reducing the weight of a part or trying an alternative welding technique to help keep energy consumption and raw material usage as low as possible.
“This approach reduces material thickness without compromising safety, reduces energy used during production, and shortens delivery times by avoiding unnecessary steps,” said Marek Cwenar, director of the R&D center at Stelweld.
This new project management approach has completely changed how we operate, and we’re just scratching the surface of its potential.
Simulation reduces physical prototypes and optimizes production
Virtual testing allows Stelweld to predict product performance and verify production processes, cutting down on the need for physical prototyping and saving both time and resources. Using SIMULIA, the company is able to simulate operational conditions such as load-bearing capacities, vibration and fatigue resistance, corrosion and wear for the products it makes and predict outcomes, such as stress points.
“We use SIMULIA for calculations related to tools, rotators, and lifting equipment,” Karwala said. “For example, we verified the fatigue life of a product for a customer through simulation, then confirmed its accuracy with real tests.”
Moving forward, Stelweld is exploring the thermal deformation analysis capabilities within SIMULIA. Simulating these conditions will help to prepare fixtures and shape parts before defining production processes, allowing engineers to better anticipate and control how heat affects metal in the welding process.
“By virtually verifying welding stresses and deformations, we can be sure that parts maintain their correct shape after thermal changes,” Cwenar said.
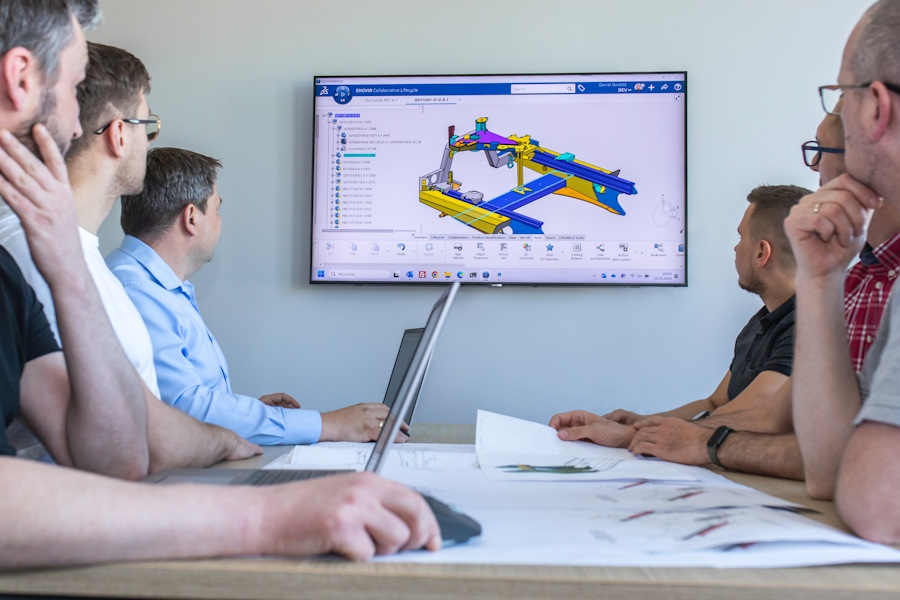
Powerful project management capabilities
Stelweld’s adoption of ENOVIA’s advanced project management tools, achieved with the support of IBS POLAND, has revolutionized its approach to implementation projects planning and execution. The company transitioned from managing every production project using spreadsheets. Now, it uses ENOVIA to create project templates, establish relationships between tasks, and keep track of all potential risks and issues.
Information sharing and productivity has improved too. Before, project files were stored on a server, requiring manual exchanges. Now, the 3DEXPERIENCE platform integrates 3D models, bookmarks, and structured task management to make sure everyone can access the data they need and no tasks are overlooked.
“Access to information is much easier and reporting is streamlined,” Karwala said. “When someone completes a task, it automatically updates next person’s to-do list. This has significantly reduced meeting times and improved overall efficiency. Our new approach to project management feels like upgrading from a bicycle to a high-speed car. The possibilities for optimizing tasks scheduling and resource management are vastly greater.”
Throughout, the partnership with IBS POLAND has been instrumental, helping the welding specialist become familiar with the 3DEXPERIENCE platform and align its processes to the platform’s functionality. This involved an in-depth audit to map out needs and bottlenecks before rethinking workflows for project management. Looking ahead, Stelweld plans to expand its use of the platform by integrating resource management, so it can assign workloads to specific tasks.
“IBS POLAND’s support was exceptional,” Gwóźdź said. “This new project management approach has completely changed how we operate, and we’re just scratching the surface of its potential.”
This approach reduces material thickness without compromising safety, reduces energy used during production, and shortens delivery times by avoiding unnecessary steps.
Continuous improvement in process quality
Stelweld’s steadfast commitment to quality carries through into all aspects of its business. The company is now using the 3DEXPERIENCE platform for advanced product quality planning (APQP) governance. This involves supporting all quality plans and processes, which should ultimately lead to fewer production mistakes and more accurate work instructions, helping to improve the overall quality of the products it makes.
“The platform ensures that all requirements stated in the APQP are reflected in the task sequence,” Cwenar said. “It also simplifies managing tasks such as feasibility studies and coordinating team involvement. Now, everything is organized in a clear structure, which ultimately helps us meet customer expectations.”
Stelweld’s success stems from a commitment to precision, expert engineering support, and unwavering reliability. Backed by the power of Dassault Systèmes’ solutions, it can continue to build on its strong technical expertise in welding and production engineering that attracts globally recognized clients, driving the company’s growth and reinforcing its position as a leading supplier.
“We anticipate significant advantages such as shorter development and industrialization timeframes as we tap into more of the 3DEXPERIENCE platform’s capabilities,” Karwala said. “Working with IBS POLAND and Dassault Systèmes, we look forward to improving our skills and growing our platform usage.”
Discover more about the Digital Equipment Continuity industry solution experience.
Focus on Stelweld
Stelweld specializes in the production of welded products for industries such as automotive, railway, lifting and handling, and construction equipment. The company follows a systematic approach to its production process, ensuring the highest quality in every product delivered. Stelweld operates in compliance with international quality standards. It offers comprehensive solutions across various stages, from design and prototype production to serial manufacturing, quality control, logistics, and aftersales services.
For more information: www.stelweld.com.pl/en
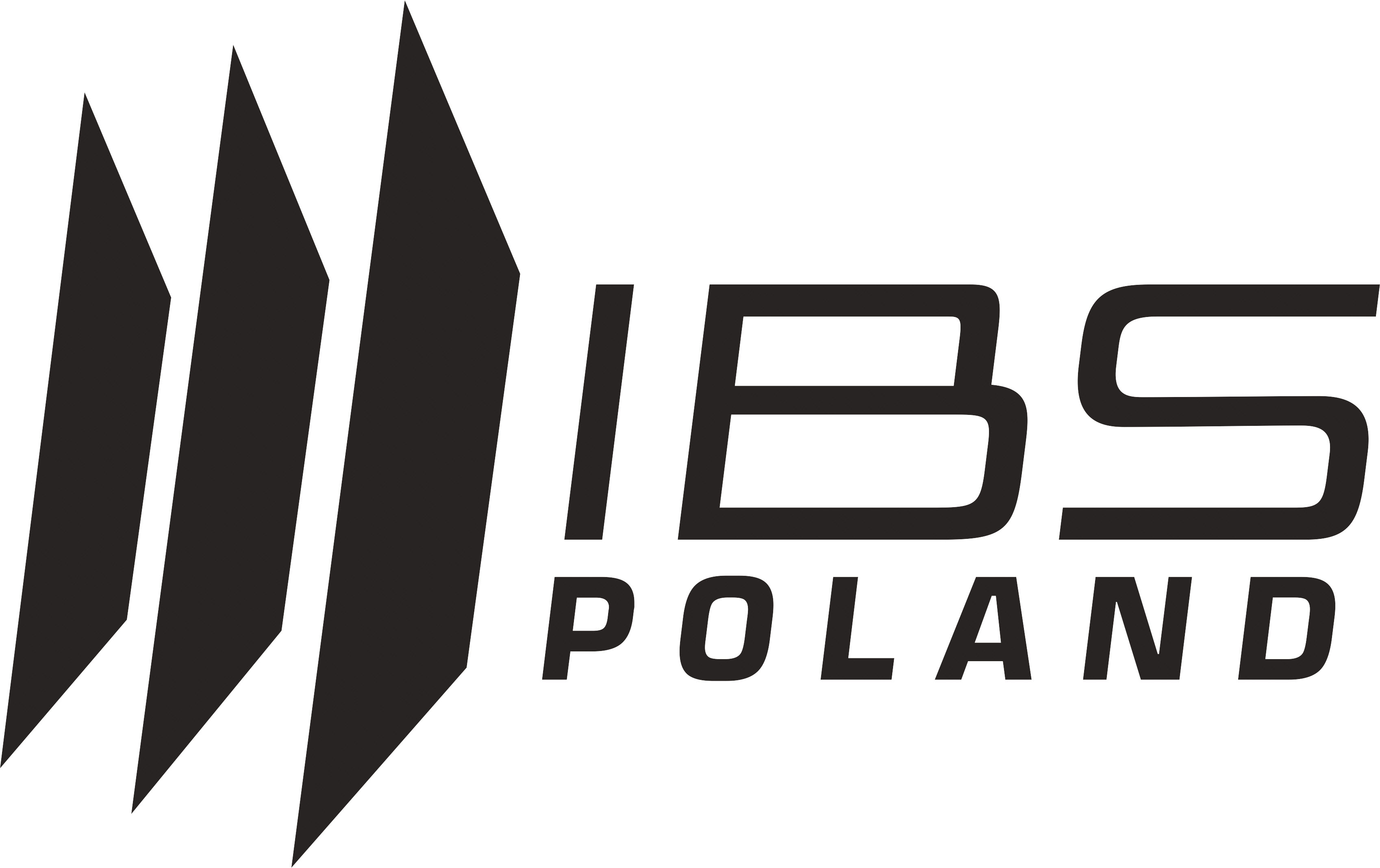
Focus on IBS Poland
Established in 2008, IBS POLAND is dedicated to supporting its customers with process optimization, complete PLM solutions, and engineering and programming services. The company is an accredited provider of Dassault Systèmes solutions and a certified training center, establishing itself as a leader in delivering PLM solutions on the Polish market. The company’s main goal is to add value for customers by optimizing and integrating business processes.