Stadler Rail
European railcar manufacturer Stadler Rail needed to ensure the crashworthiness of a new bi-level passenger car (KISS) and the performance of its crash module.
In the early 20th century, a strange spectator sport flourished in America: train crashing. They were so popular that one man, Joe “Head-on” Connolly, staged 73 crashes (destroying 146 trains) between 1896 and 1932 at state fairs and other large venues.
Those days are long gone. Engineers (the design kind, not the train-drivers) who want to observe a crash can run perfectly safe, highly accurate virtual collisions on a computer screen.
While designing a new rail car, the engineers have a significant need for simulation in order to best address safety questions. In the event of a crash will the welds hold, particularly if the train is in its later years of service? Will the passenger portion of the coach retain its shape? Also important: Will the internal components and assemblies of the passenger area remain in place and be relatively undeformed?
Stadler Rail, headquartered in Bussnang, Switzerland, has been answering these questions (with and without simulation) for over 70 years. In the process, they’ve designed and built tailor-made trains, regional, tram, meter-gauge and even bi-level trains. In recent years, they put that expertise to work designing a double-decker commuter train, the KISS (KISS is a German acronym that means “comfortable innovative speedy suburban train”). The train runs at speeds up to 200 km/hr. (124+ mph) and is a workhorse for train lines in Switzerland and Austria.
As with all transportation designs, keeping weight light is an important goal. (“Light weight” is relative—each six-car train weighs 297 tons. To ensure strength at the same time, the car body is made from 35 hollow, large-scale aluminum extrusions joined with an incredible number of MIG welds. Friction stir welds are applied for the intermediate floor. “There are about 12,000 meters of welds in a railcar,” says Dr. Alois Starlinger, Head of Structural Analysis, Testing, and Vehicle Authorization at Stadler Rail. “Under those circumstances, weld performance is every bit as vital for safety as that of the extrusions themselves.”
Crash Energy Management, or CEM, is an extensive part of product development for a new train design. It is guided by a number of different European rail safety standards, most notably “Crashworthiness requirements for railway vehicle bodies (EN 1527).” A significant portion of those standards defines what portions of a design should be proven out with simulation and how to do it.
Central to that process at Stadler is Abaqus, the finite element analysis (FEA) application from SIMULIA, the Dassault Systèmes 3DEXPERIENCE technology. “Stadler has used Abaqus for over 10 years for these sorts of simulations,” Dr. Starlinger says.
MAKING A MODEL
When Stadler first began using Abaqus, FEA models in general were far more narrow in what they could analyze. A decade of advances in computing hardware and software has led to the current generation of extremely detailed yet highly efficient models. The KISS railcar model used over 3 million elements and had 12 million degrees of freedom (Figure 1). A typical element length represented just 25 millimeters of the 25-meter car, affording a close-up look at load effects throughout. The aluminum extrusions, welds, milled parts, and even fasteners (over 1000 bolts and rivets) are represented. “We paid special attention to defining element density and mesh quality,” Dr. Starlinger says, “in order to fully optimize the simulation’s capture of stress gradients.”
Abaqus enabled us to reduce product development times for the KISS cars while retaining high quality and safety.
The model was used for static analyses, in Abaqus/Standard, of 45 different global load cases examining the passenger area, the car coupler, and buckling and vibration modes. An important goal was to check whether the car design would withstand the given load conditions or would deform unacceptably. “The largest effort for development and certification of the KISS train was the stage of calculating and evaluating these load cases,” says Dr. Starlinger.
The most important case was an impact load of 1500 kN on the coupler joining the rail cars. It was specified by a safety standard (EN 12663-1) that states the railcar must sustain such an impact with minimal deformation. Running their analysis, Stadler engineers found little to no deformation in the coupler, and the other static analyses were positive as well (Figure 1).
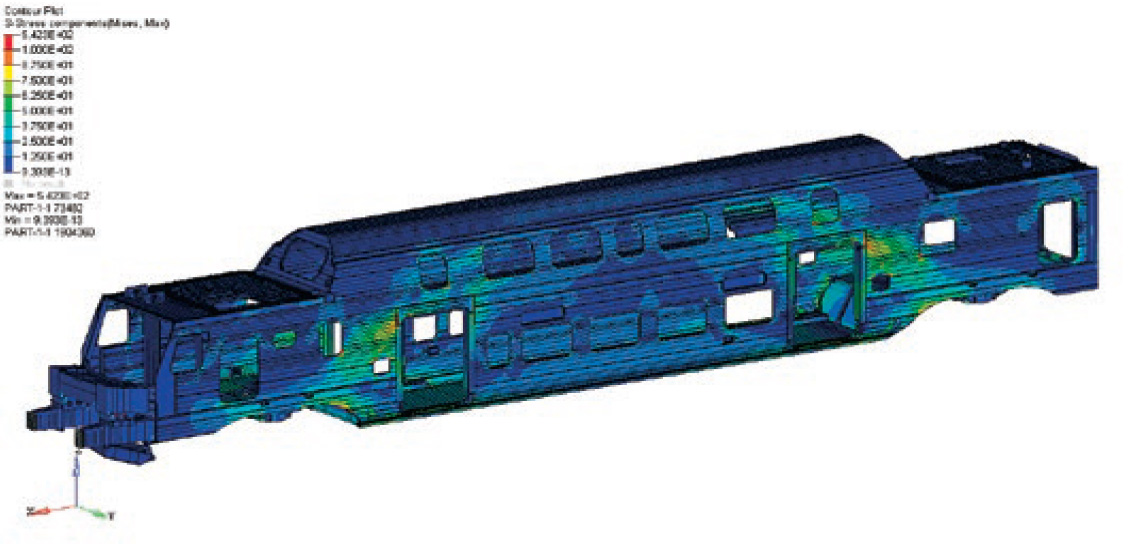
FIGHTING FATIGUE
Once the static analysis was complete, engineers evaluated the Abaqus FEA results using the fatigue strength postprocessor FEMFAT from Magna. Fatigue loads for weld examination included damper forces between the car body and the bogie (the wheel, axle and frame assembly, often called a “truck” in the U.S.), traction and braking loads and acceleration loads in all major directions. “Fatigue effect on the welds is quite important,” Dr. Starlinger says, “since the aluminum welds have a lower fatigue strength than the base materials of the extrusions building the car body.” Fatigue stretch data were drawn from the International Institute of Welding (IIW) recommendations and the German FKM guideline.
“We used the notch-stress approach for the fatigue evaluation,” Dr. Starlinger says. “It gave us insight into the life of the most critical part of the weld for all load cases.” The fatigue software cycled the welds through the projected 40-year operating conditions and lifespan of the railcar, providing the load collective (total load of the car), along with specifics about notch-weld stresses. “The static and fatigue analyses we made gave us a high degree of confidence in how the car would perform,” Dr. Starlinger says.
But some large questions remained: How would the individual features of the car—in particular, the crash module—perform in the event of an impact?
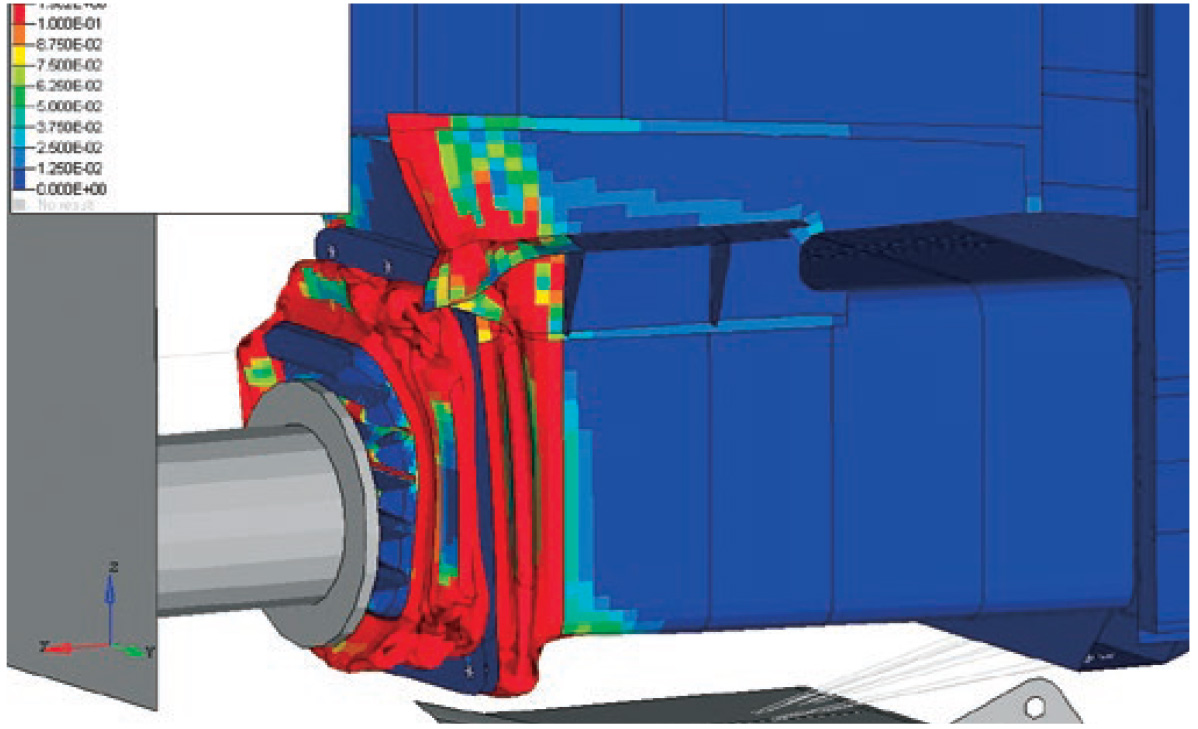
COMBATTING CRASH
Four standard collision scenarios require examination of impact: front-end with an identical train unit, front-end into a buffered rail vehicle, front-end into a heavy obstacle (such as a truck at a road crossing), and impact into a low obstacle on the track. Of all these the most critical is the head-on impact between identical railcars, since it could potentially cause the highest number of injuries as well as the most serious ones. “We performed dynamic crash analyses using Abaqus/Explicit,” says Dr. Starlinger, “on a time line extending from the first collision contact until 0.2 seconds after the impact.”
The analysis focused on the crash module at the front end of the car (Figure 2). This module, a tapered tube with multiple chambers, is designed to absorb energy by plastic buckling sequentially (and predictably) on impact, contributing to the rest of the car retaining its shape and protecting any occupants. The simulation involved materials characteristics and behavior under crash load as well as the deformation of the module. “We’ve been analyzing railcars with Abaqus for more than a decade,” Starlinger says, “and we have extensive physical test data to use along with the results of previous simulations.”
Interior and Equipment Structures.
Interior components and equipment were also evaluated in accordance with safety standards. These included a detailed examination of such items as staircases, seats, toilets, luggage racks, internal doors, and the driver’s seat and desk. In the stair area, for example, the engineers included passenger mass and specific forces at the hand-rails in their analyses. Among the nonlinear phenomena analyzed was behavior of the cantilever beam that fixes a passenger seat to the railcar wall. The engineers modeled the different welded, milled, and forged pieces of the assembly to capture as complete an understanding of the seat beam as possible. Analysis results determined the potential displacement of the seat structure under impact loads, information that provided basic data for defining bolt quality as well as assembly parameters.
Outside of crash analysis, the engineers looked at vibration of key train components during normal operation—for example, a simulation of the constant vibration created by the rotating mass of the compressor engine. This analysis applied a dynamic force within a specific frequency spectrum and explored the effects of fatigue on features of the railcar.
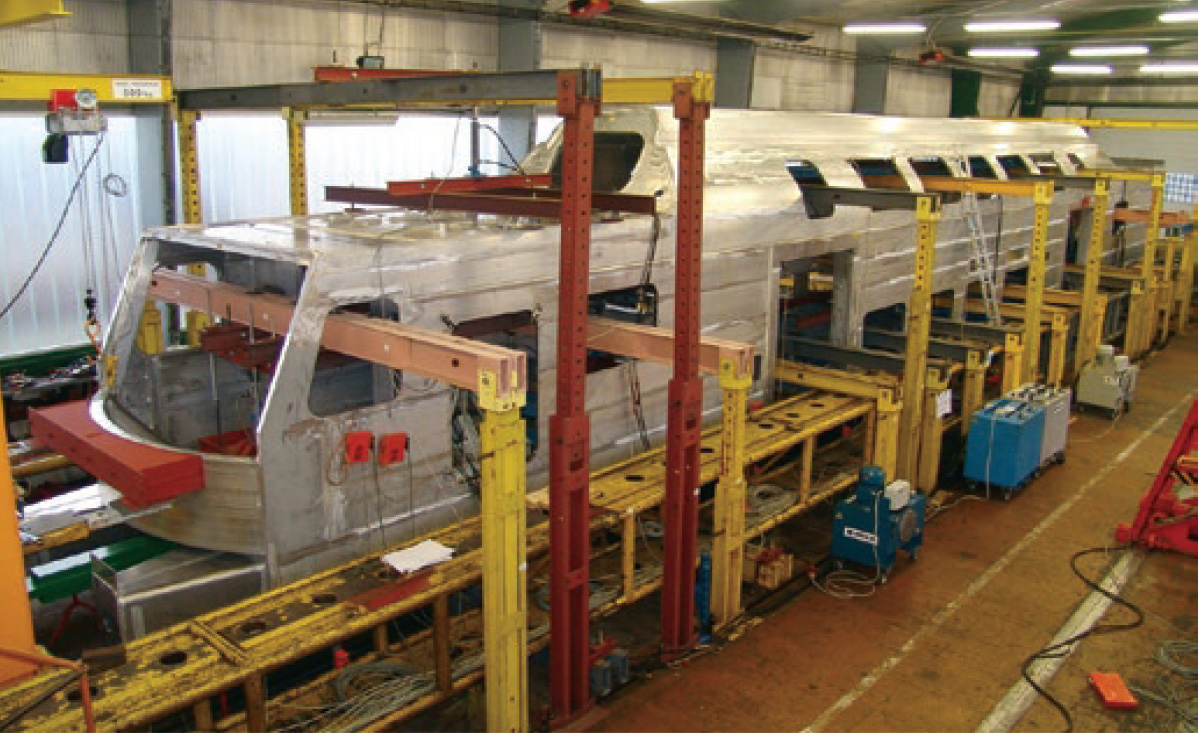
VIEWING VALIDATION
Physical prototyping and testing remain an important part of railcar design. While simulation provides valuable insights into design and helps engineers meet safety standards, there are additional requirements for validation of static and dynamic analyses through physical testing. Tests include applying vertical and longitudinal loads to railcar structures and using hydraulic actuators.
During real-world testing of the KISS car, the main deformations of the full-size railcar body and components were measured and stress levels obtained at over 140 positions via strain gauges. The physical testing showed a close correlation with the FE analyses, and dynamic loading of the crash module also produced results in close agreement with the simulation (Figure 3)
RESULTS ON THE RAILS
Stadler’s simulations confirmed that the KISS railcar design successfully fulfilled all requirements of the European standards. Over 170 multilevel car trains have been ordered, many of which are already in service in Switzerland, Austria, Germany and Luxembourg.
“Abaqus enabled us to reduce product development times for the KISS cars while retaining high quality and safety,” Starlinger said. “We were able to quickly perform a significant number of analysis iterations, enabling us to optimize the railcar structure in terms of weight while still meeting all safety standards. That helped Stadler to meet its stringent time schedule for structural design releases. Up to now, Stadler has kept all contractual deadlines for product delivery to the customer.”