Soosan Heavy Industries. Co., Ltd
The company selected the 3DEXPERIENCE platform and its Single Source for Speed industry solution experience for design, collaborative innovation and project management.
INDUSTRY HEAVYWEIGHT SEEKS TOP POSITION
Soosan Heavy Industries is the largest industrial equipment manufacturer in Korea and recognized as one of the world’s leading manufacturers of hydraulic breakers, demolition attachments, crawler drills and truck mounted cranes. The company is headquartered in Korea, and has branch offices in the US, China, the Netherlands and Dubai. With more than 70% of its total sales generated in overseas markets, Soosan Heavy Industries is accelerating its efforts to develop core technologies with the aim of becoming one of the world’s top three equipment manufacturers. Soosan Heavy Industries plans to reinforce its R&D efforts to deliver cutting-edge products that will allow it to gain a competitive advantage over other major industry players.
INTUITIVE SYSTEM REDUCES LEARNING CURVE
“As Dassault Systèmes already has many customers in various industries, we knew we could rely on its solutions for our development,” said Jae-sang Cho, executive director at R&D Center, Soosan Heavy Industries. “We visited companies from similar industries that use Dassault Systèmes applications, and found them suitable for what we wanted to achieve. We, therefore, adopted the 3DEXPERIENCE® platform and its Single Source For Speed industry solution experience to improve our product development processes and equipment quality. Rich & Time, a Dassault Systèmes’ business partner performed a proof of concept whose results convinced Soosan Heavy Industries to select the Dassault Systèmes’ solution. The partner also implemented and tailored the solution to our needs. Their responsive support and training helped secure the successful use of Single Source For Speed at Soosan Heavy Industries. In effect, thanks to Dassault Systèmes’ training program, it took approximately one month to learn the different functions. With their new skills, our engineers can perform tasks that are far more extensive than what they could do in the past. The system is so intuitive, the learning curve is definitely not very steep,” he said.
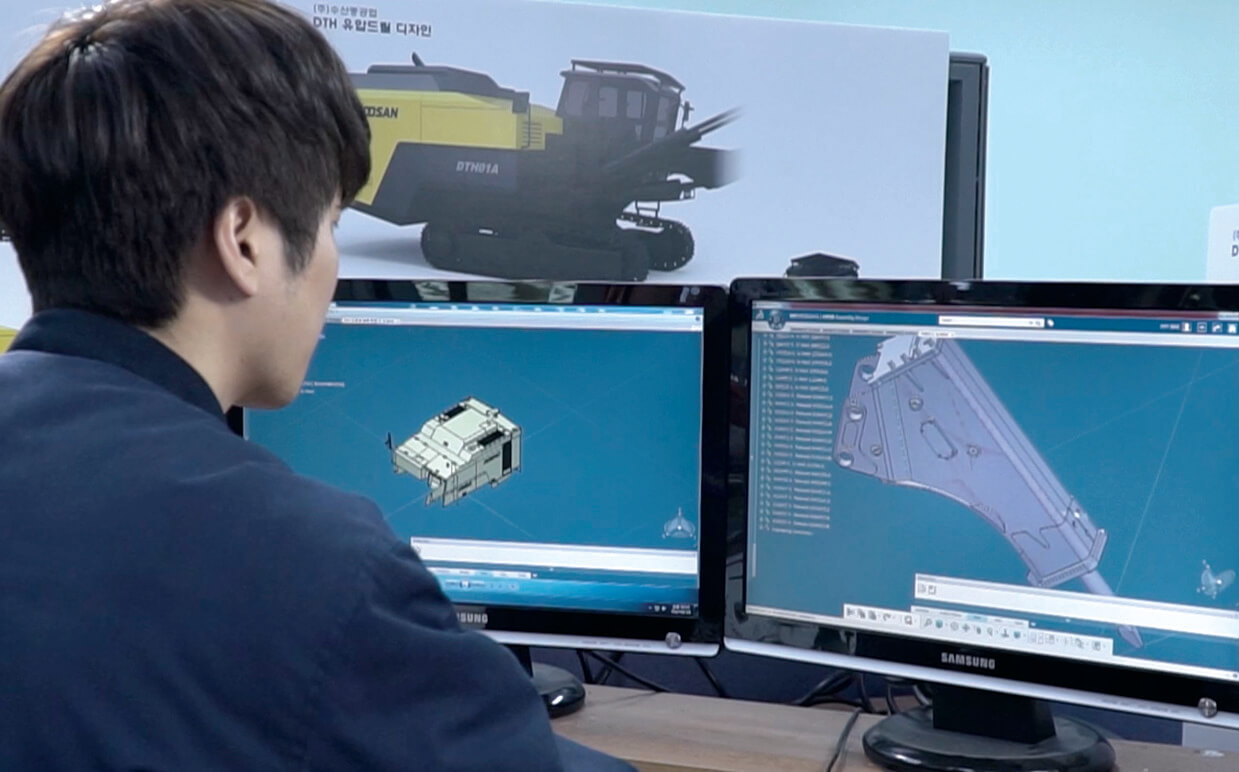
IMPROVED PERFORMANCE, REDUCED DEVELOPMENT COSTS, SHORTER TIME TO MARKET
Using the 3DEXPERIENCE platform, Soosan Heavy Industries can verify product performance and defects in advance in a digital environment, reducing the need for physical prototypes that can amount to a few hundred million Korean Won (tens of thousands of US dollars). “Therefore, we dramatically reduce development costs,” Jae-sang Cho said. “Moreover, since defects are detected early during digital simulations, we also reduce time to market.”
Jae-sang Cho continued: “When we introduced Single Source for Speed, our objective was to reduce the overall development timeline by 30%. We, in fact, reduced the development cycle by even more than we originally planned. In the past, it took about two and a half years to develop a custom-made product. Thanks to Single Source for Speed, we managed to reduce it to about one and a half years, a savings of about 40%. In addition to this, since design data is capitalized for future projects, the development period is expected to shorten even more,” he said.
When Soosan Heavy Industries worked with other CAD software for its design activities, it took a long time to read and write data due to performance problems. “With the 3DEXPERIENCE platform, these problems have disappeared,” Jae-sang Cho said. “Now, we can quickly and precisely create complex designs and display several digital models simultaneously to compare them.”
The 3DEXPERIENCE platform is the foundation to transform Soosan Heavy Industries into a champion of industrial equipment manufacturing.
REINFORCING COLLABORATION
Currently, about 50 people are using the 3DEXPERIENCE platform in three departments, i.e. breakers, cranes and drills. “Before adopting Single Source for Speed, engineers had trouble collaborating on designs because nobody knew if they were working on the latest version of a design,” Jaesang Cho said. “This introduced errors and delayed design completion. Now that we use a single platform to access our information we can update the designs as changes are made by individual departments. Thanks to concurrent design, we improve the speed and accuracy of our work. Moreover, as we are working with the latest up-to-date data, we avoid wasting time correcting errors. For now, this collaboration is only available within the company; our aim is to allow our suppliers to access the 3DEXPERIENCE platform to perform design activities for manufacturing preparation,” he explained.
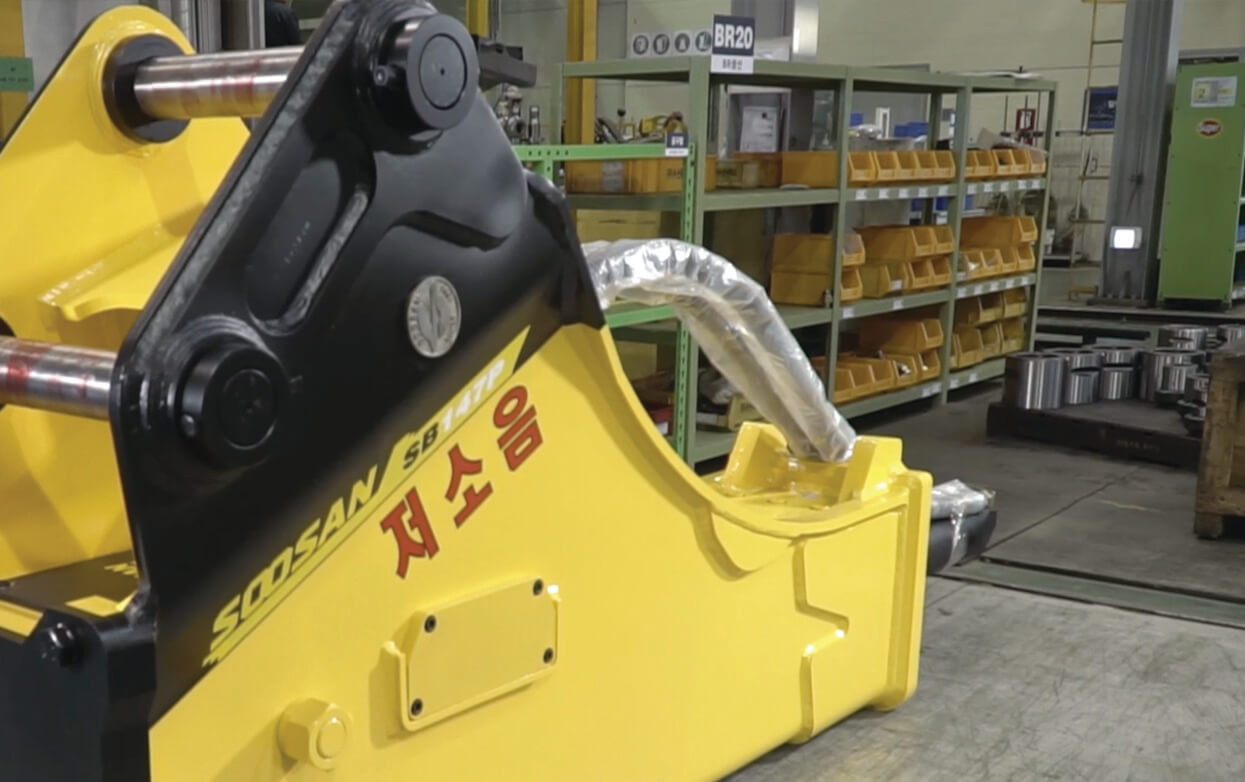
BETTER PERFORMANCE IMPROVES WORK EFFICIENCY
Soosan declared its new vision in 2014 to become one of the top three industrial equipment providers in the world. ”To implement this vision, we participated in the World Class 300 projects, a government initiative to support mediumsized companies,” Jae-sang Cho said. As a result, Soosan Heavy Industries is making it its top priority to improve R&D skills. ”Our company continuously invests to hire outstanding researchers, provide continuous education, and create an efficient development environment with technologies like the 3DEXPERIENCE platform. This will lay the foundation to transform Soosan Heavy Industries into a champion of industrial equipment manufacturing,” he said.
Development time was reduced by about 40% with Single Source For Speed, and expected to reduce even more in a short time
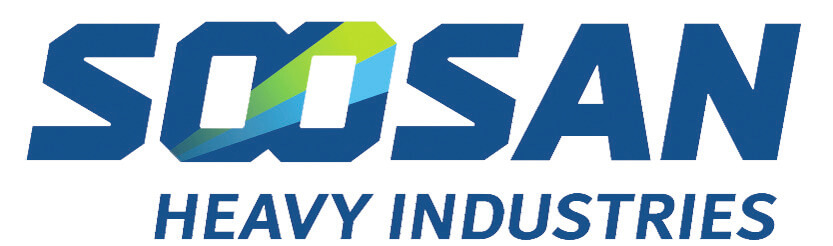
Focus on Soosan Heavy Industries. Co., Ltd
Industrial equipment manufacturer
Products: industrial equipment (breakers, cranes and drills)
Employees: 214
Headquarters: Jeongmunsongsan-ro, Songsan-ri, Yanggammyeon, Hwaseong-si, Gyeonggi-do, Republic of Korea
For more information www.soosan.co.kr
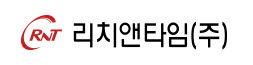
Focus on Rich & Time
Korea-based Rich & Time has provided IT services for over 15 years and has been certified as an excellent and growing enterprise four years in a row. The team comprises IT infrastructure and PLM services experts with years of combined experience. Rich & Time also ensures competitiveness by investing in R&D to continually to provide a greater variety and wide range of services, based on business areas and IT needs.