Sandvik Coromant
By combining Sandvik machining expertise and DELMIA advanced functions, the company is able to deliver an optimized 3DEXPERIENCE Twin to its customers on the 3DEXPERIENCE platform.
Our customers come to us with major challenges relating to machine processing, time constraints and increasingly stringent specifications.
World leader in machine processing solutions
Sandvik Coromant, part of the global industrial engineering group of Sandvik, leads the way in tools manufacturing, machine processing solutions, knowledge and expertise. The company creates industry standards and simulates the innovations demanded by the metallurgy industry, now and for the future. Its training materials, significant investments in R&D and close partnerships with customers allow the company to develop machine processing technologies that modify, shape and drive forward the future of the industry. Sandvik Coromant also offers digital machine processing solutions, from design to machine processing analysis, using connected software and tools that support planning and digital manufacturing. Sandvik Coromant holds more than 3100 patents worldwide, employs more than 7900 people and operates in 150 countries.
Challenge
Customers face many challenges within the aerospace industry: increasing production rates, reducing cycle times, optimizing manufacturing costs, embedding subcontractors, working with materials that are increasingly difficult to machine process, and dealing with increasingly demanding specifications.
Solution
The DELMIA Digital Manufacturing solution simulates machining processes in a virtual setting before they are brought into the real world, embedding concentric tool paths in particular.
Advantages
- Program the tool path, simulating the removal of material and integration within the whole machine
- Simulate machine processing of a component or part before the production phase
- Provide accurate data for cutting times and machine processing costs in advance
- Deploy concentric technology across a large number of machine processing cycles
- Reduce cycle times by up to 40%
- Increase the service life of the cutting tool
- Avoid tool breakage
- Tailor the solution to different materials: stainless steel, aluminum, Inconel, titanium
From design to production: A dedicated team and a tailored solution
Specialist teams within the Sandvik Coromant organization assist the industrial sectors in supporting clients with their projects. Antonio Igreja, Manager of Customized Solutions Aerospace Hub Europe at Sandvik Coromant, leads a team of project engineers who are specialists in the aviation industry, a sector where orders often represent several years of production, and where stakeholders are looking to make improvements in productivity in order to accelerate production rates. "We want to support our customers as a partner, rather than just a supplier of cutting tools, offering them solutions that are perfectly tailored to their requirements," explains Antonio Igreja.
"Our customers are major workgivers, and their subcontractors manufacture engines and structural components. In the 1980s, the aerospace industry began designing aircraft using Dassault Systèmes CATIA solutions. That's why their partners and then subcontractors were naturally led to invest in DELMIA solutions," Antonio Igreja adds. This ensures the end-to-end consistency of data and processes, from design to manufacturing. What's more, Sandvik Coromant is able to capitalize on DELMIA's developments and inputs to showcase its own machine processing solutions, which integrate perfectly with the means of production and the production environment available to customers.
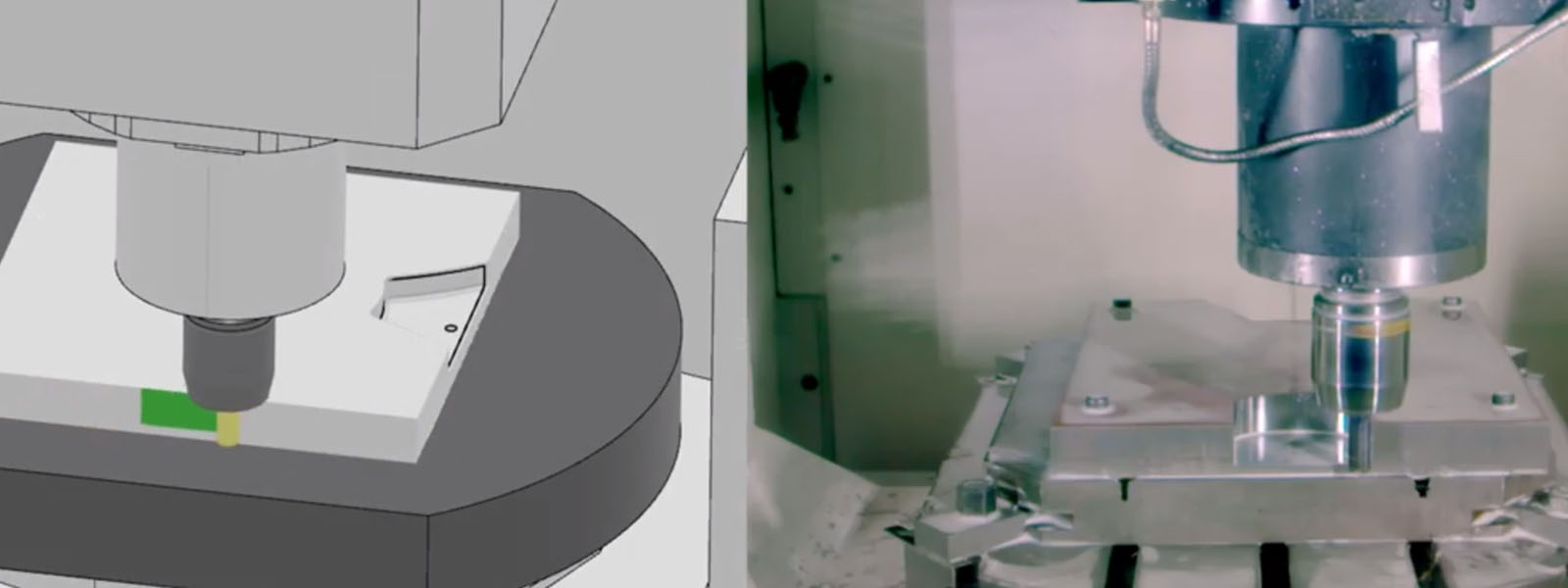
Concentric technology goes one step further
Speeding up production rates, embedding the supply chain… but that's not all: Manufacturing within the aerospace industry faces an additional challenge, owing to the fact that materials are increasingly difficult to machine process. "So the challenges our customers are facing are related to these machine processing constraints, time constraints and increasingly stringent specifications," states Antonio Igreja. To better organize their production processes and therefore maintain throughput, aerospace manufacturers make use of Sandvik Coromant to simulate machine processing strategies for parts, while respecting specifications relating to time, cost and process safety.
"In fact, when they contact us, our customers' two main requests relate to calculating cutting times and costs per unit. To provide them with accurate data, we need powerful simulation tools," he adds. In this particular case, concentric technology allows Sandvik Coromant to push the envelope when it comes to optimization strategies. This machine processing technology is embedded within DELMIA, which brings immediate advantages. "Concentric technology helps us deliver optimized tools to our customers," confirms Salim El Kadaoui, Customized Solutions Aero Project Engineer-Technical Expert at Sandvik Coromant. "Thanks to this technology, the tool has a longer life span and can stay in contact with the material for longer, helping to achieve significant gains in cycle times."
Immediate benefits
"Concentric technology allows low radial engagement to be combined with high axial engagement, which means we can increase cutting parameters," he says. "Higher cutting parameters allow us to reduce cycle times by up to 40%." This technology offers the added benefit of working on a wide variety of materials, such as titanium, stainless steel, Inconel and aluminum. For example, when machine processing titanium, it is possible to triple the cutting speed while doubling the tool life compared to conventional machine processing methods — and in some cases, the tool life can be increased even further. Sandvik Coromant's customers can therefore take immediate advantage of this technology and benefit from safer processes, as cutting tools break less often and machine downtimes are reduced.
DELMIA and Sandvik Coromant, a winning team
In DELMIA, Sandvik Coromant has found a partner that it can rely on in its search for continuous improvement and ongoing innovation. "By combining Sandvik Coromant's machining expertise with the advanced capabilities of DELMIA solutions, we can use a digital clone of our machines, available on the 3DEXPERIENCE platform," Antonio Igreja adds. The development of digital technology is groundbreaking for companies who have to continuously adapt. In this context, both Sandvik Coromant and DELMIA are developing collaboration and training processes with their customers to contribute to technological innovation in the industry.
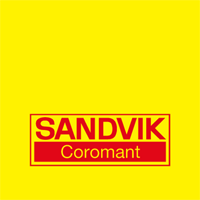
Sandvik Coromant Highlight
Global leader in manufacturing tools and tooling systems for industrial machine processing. Its products are made from cemented carbide and other hard materials such as diamond, cubic boron nitride and special ceramics. Services include both additive and digital manufacturing.
Established in: 1942
Headquarters: Sandviken, Sweden
Find out more: www.sandvik.coromant.com