Life-saving seatbelts with 3D simulation
Did you know, you’re twice as likely to die in a crash if you don’t wear a seatbelt? Seatbelts are one of the most critical pieces of safety equipment in a car – they have saved more lives than every other safety measure combined, according to a study by the United States’ National Highway Traffic Safety Administration.
It’s no wonder, then, that South Korean seatbelt manufacturer Samsong describes itself as a ‘life-saving company’, supplying seatbelts, along with other safety devices, to global automotive companies including General Motors, Hyundai Motor Company, Kia, Renault Group, Ford, Audi, Volkswagen, and SsangYong.
Historically, Samsong has developed its products using a heavily customized product lifecycle management (PLM) system. However, maintaining and updating this system was time- and resource-intensive, making it exceedingly costly.
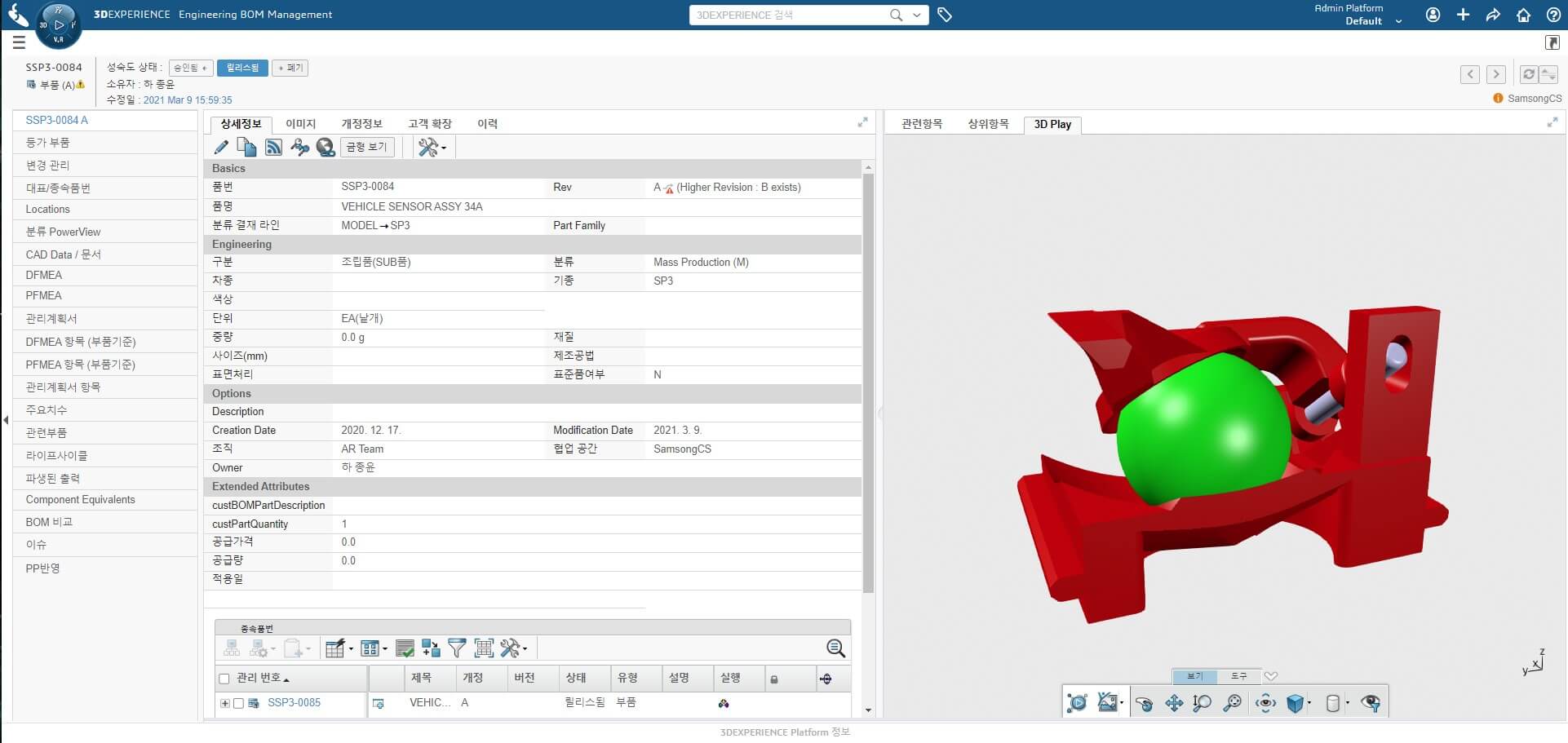
Challenge
Samsong required effective simulation capabilities – its existing system only allowed it to perform offline-centric analysis. With no connection between design data and related information, it was difficult to understand the status of an entire task – which meant duplicated work. Its system also lacked compatibility with CATIA, Samsong’s 3D design solution of choice, which it used to collaborate with customers.
Samsong realized that an out-of-the-box platform could help it design and simulate products more effectively and affordably. It wanted to create a system-based status report that would allow it to use design data more successfully for component development and process and quality control, which could then expedite decision-making. Samsong also wanted a centralized data repository that could help it accelerate the reuse of parts, designs, specifications, standards, test results and related information for engineering and manufacturing activities.
In addition, Samsong needed to establish a seamless collaboration channel with overseas factories and research institutes to communicate design ideas clearly.
Solution
After a successful proof of concept, Samsong chose Dassault Systèmes’ 3DEXPERIENCE platform along with its Bid to Win industry solution experience, including CATIA for vehicle seatbelt design and to create 3D PDF files to distribute drawings to external partners that are non-CATIA users. It is also using SIMULIA for simulating the strength and tensile force of seatbelt parts, including a simulation process and data management (SPDM) system to manage simulation requests across its entire business, and NETVIBES for standardizing product parts, to increase the reuse rate of parts.
Through the 3DEXPERIENCE platform, we have been able to secure a data-based collaboration space that enables more effective cooperation between our internal teams, and with external stakeholders such as research institutes. This gives us more free time to focus on product development. We will continue to further our use of the 3DEXPERIENCE platform – it’s a powerful tool for us to help strengthen our competitiveness.
Benefits
Quickly implementing the 3DEXPERIENCE platform right out of the box meant Samsong’s needs were met immediately, without any customization.
With the platform now connecting different disciplines, Samsong can improve project efficiency. ENOVIA’s product data management (PDM) and PLM capabilities enable instant access to information to make more effective decisions. Any team member can have an instant view into a project’s status. This not only reduces work hours, it ensures faster progress and improves R&D work quality, and also facilitates better interdepartmental collaboration.
Using an SPDM system, Samsong has established integrated simulation management based on a virtual verification environment. This enables the company to standardize and automate the simulation process and manage the association of simulation data and related information across the entire business.
Having the 3DEXPERIENCE platform act as a single repository for all data, including 3D drawings and documents, means all project data is easily accessible using a tag system that allow designers to assign content based on six Ws: who, what, when, where, why and how.
In addition to easier file discovery, Samsong’s designers find that they can share data more effectively. 3D documentation for production, for example, can be generated with 3DVIA and shared with customers who do not use CATIA. All stakeholders can then collaborate using ENOVIA’s 3DPlay widget.
Furthermore, NETVIBES has increased the reuse rate of parts thanks to artificial-intelligence-driven part standardization. This has also enhanced the traceability of the design history for continuous improvement.
Discover more about the Bid to Win industry solution experience.
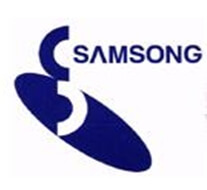
Focus on Samsong
Based in South Korea’s capital city of Seoul, safety device manufacturer Samsong serves several global automotive firms including Hyundai, General Motors, Renault, Kia, Ford, Audi, Volkswagen, and SsangYong. The company’s products include seatbelts, ECU electronic components and infant car seats.
Founded in 1978, and with subsidiaries in China, India, Vietnam, Brazil and the Czech Republic, Samsong employs over 1,900 people.
For more information: http://www.samsong.co.kr
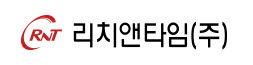
Focus on Rich & Time
Korea-based Rich & Time has provided IT services for over 15 years and has been certified as an excellent and growing enterprise four years in a row. The team comprises IT infrastructure and PLM services experts with years of combined experience. Rich & Time also ensures competitiveness by investing in R&D to continually to provide a greater variety and wide range of services, based on business areas and IT needs.