Şahince Otomotiv
Sheet metal forming company Şahince Otomotiv adopted the 3DEXPERIENCE platform on the cloud to establish a unified environment for all operational processes. The Innovative Modules and Technologies industry solution experience was implemented to support the production of complex products in a multi-discipline setting.
Deep drawn sheet metal parts for automotive OEMs
A typical car includes 300-400 deep drawn components. Deep drawing is a form of sheet metal fabrication that morphs simple flat metal into intricate shapes using dies manufactured to the unique specifications of original equipment manufacturers (OEMs). It’s a fast and cost-effective process that results in parts such as clutch covers, handbrake support brackets, air filter carriers, pistons, and flywheels that are strong and durable.
Sheet metal forming is a competitive industry and success is no small feat. Automotive OEMs demand high quality and low cost – and are often looking for an incredibly fast turnaround of deep drawn items to meet strict production schedules. So, for a machining business like Turkey-based Şahince Otomotiv to be able to list some of the largest commercial vehicle OEMs as its key customers is quite the accomplishment.
Since its establishment in 1980, Şahince Otomotiv is on a mission to stand apart from the competition. According to the company’s general manager Özgür Şahin, this objective is possible thanks to an unwavering commitment to innovation.
For example, the company was one of the first of its kind in Turkey to implement a best-in-class solution to help it advance its design and project management processes. That solution? Dassault Systèmes’ 3DEXPERIENCE platform on the cloud.
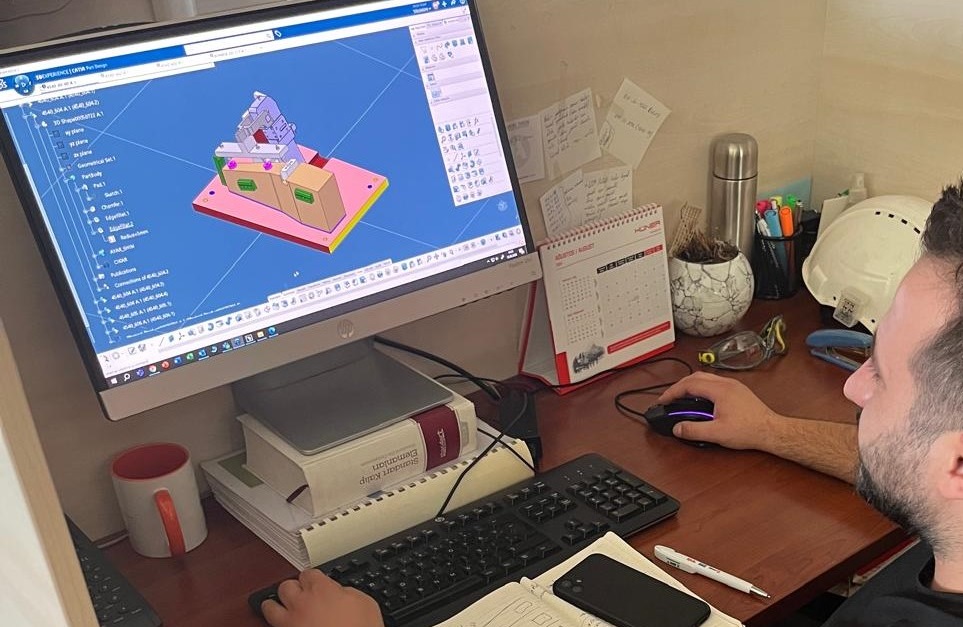
Challenge
Prior to adopting the 3DEXPERIENCE platform on the cloud, Şahince Otomotiv faced several difficulties, largely because of its siloed mode of operation.
Responsible for reviewing OEM product requirements and engineering the dies used for deep drawing components, the design team worked independently from the project management and manufacturing teams. Each employee had their own file-based system. CATIA V5 design files were stored locally on designers’ computers and multiple spreadsheets were used for project management. A separate manufacturing execution system (MES) was used, but there was no integration with design, and no easy way to implement automotive-specific industry-standard practices such as advanced product quality planning (APQP).
This disjointed environment made collaboration difficult and hampered productivity. Multiple inefficient processes led to errors and a duplication of effort. Something needed to change.
By leveraging the 3DEXPERIENCE platform on the cloud, we have transformed the way our company operates. We are now working 30% faster. Our state-of-the-art approach will reinforce our leading position in the sector and help us continue to deliver innovative customer-oriented solutions.
Solution
Şahince Otomotiv chose to transition to the 3DEXPERIENCE platform to establish a unified environment for all its operations. Within the platform, Şahince Otomotiv could leverage CATIA for 3D design and ENOVIA for project and data management. It could also integrate the platform with its existing MES.
Since Şahince Otomotiv chose the cloud-based version of the 3DEXPERIENCE platform, implementation was fast and straightforward. Local Dassault Systèmes partner Cadem Digital, which was involved in Şahince Otomotiv’s initial CATIA V5 implementation, helped to customize the solution by mapping the company’s key processes, before commencing onboarding. Cadem also provided two days of training focused on demonstrating the new capabilities of CATIA on 3DEXPERIENCE and the new engineering process workflow.
Benefits
Şahince Otomotiv now has a cutting-edge, integrated cloud-based environment providing a single digital thread across all disciplines. All teams can securely access the same data, eliminating communication silos for seamless collaboration.
Using CATIA on 3DEXPERIENCE, engineers have standardized die design practices while benefiting from the application’s smart component capabilities to reduce repetitive tasks. As a result, design productivity has increased and errors have reduced.
Thanks to ENOVIA, project management happens right within the platform and is based on the most up-to-date information. Spreadsheets are now a thing of the past.
By integrating the platform with its MES, Şahince Otomotiv has also introduced APQP protocols into the manufacturing process and is driving quality improvements as a result.
Overall, since design, project management, manufacturing and governance processes are connected, Şahince Otomotiv estimates that its teams are working around 30% faster.
Impressed with the results so far, the company is keen to leverage more of the platform’s capabilities. For example, it is exploring the possibility of digitalizing its failure modes and effects analysis (FMEA) to systematically identify potential failure points in the die design and deep drawing process, thereby further embodying the principles of APQP.
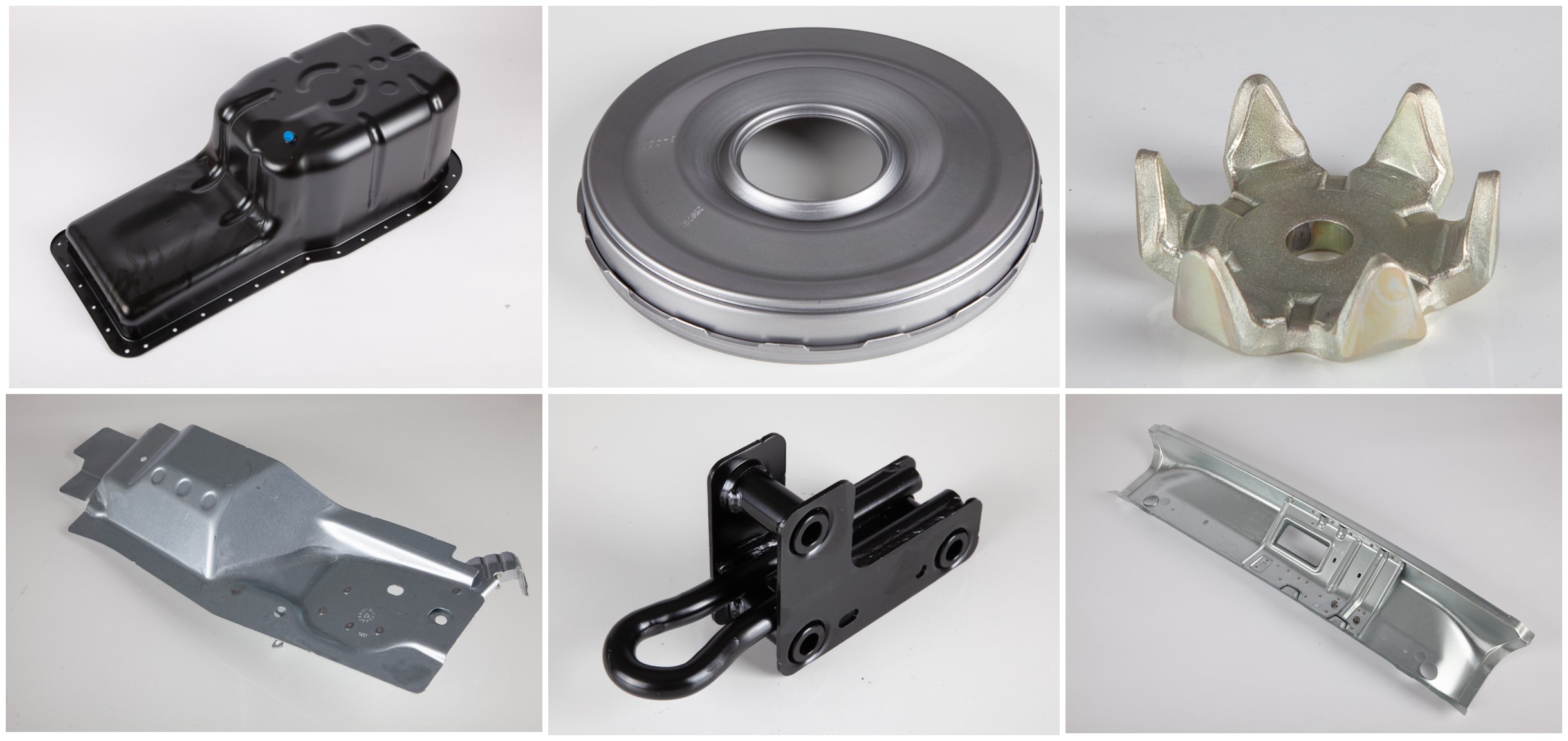
Discover more about the Innovative Modules & Technologies industry solution experience.
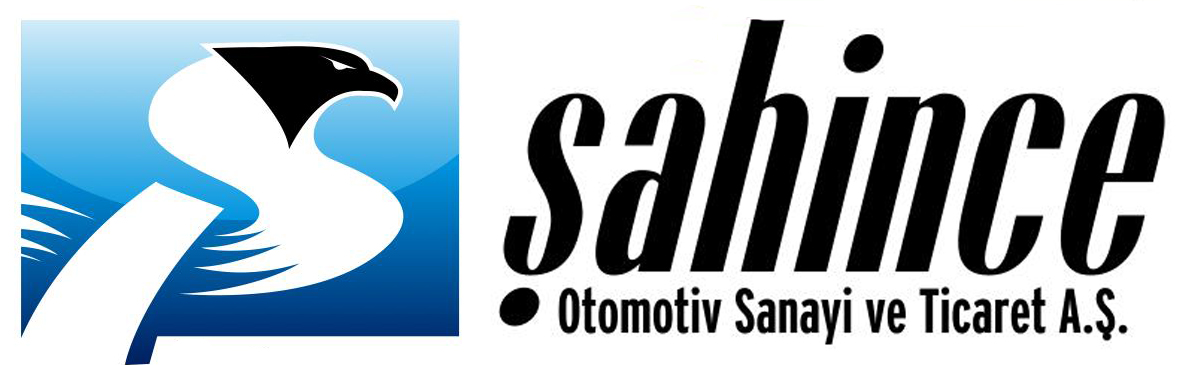
Focus on Şahince Otomotiv
Sheet metal forming company Şahince Otomotiv is a pioneer in its industry, with a deep-rooted history in the automotive sector. Operating from Bursa in Turkey, it prides itself on its customer-oriented approach and uncompromising commitment to quality. Always with an eye on the future, the company attaches great importance to research and development to continuously increase the quality of products and services.
For more information: https://sahince.com.tr
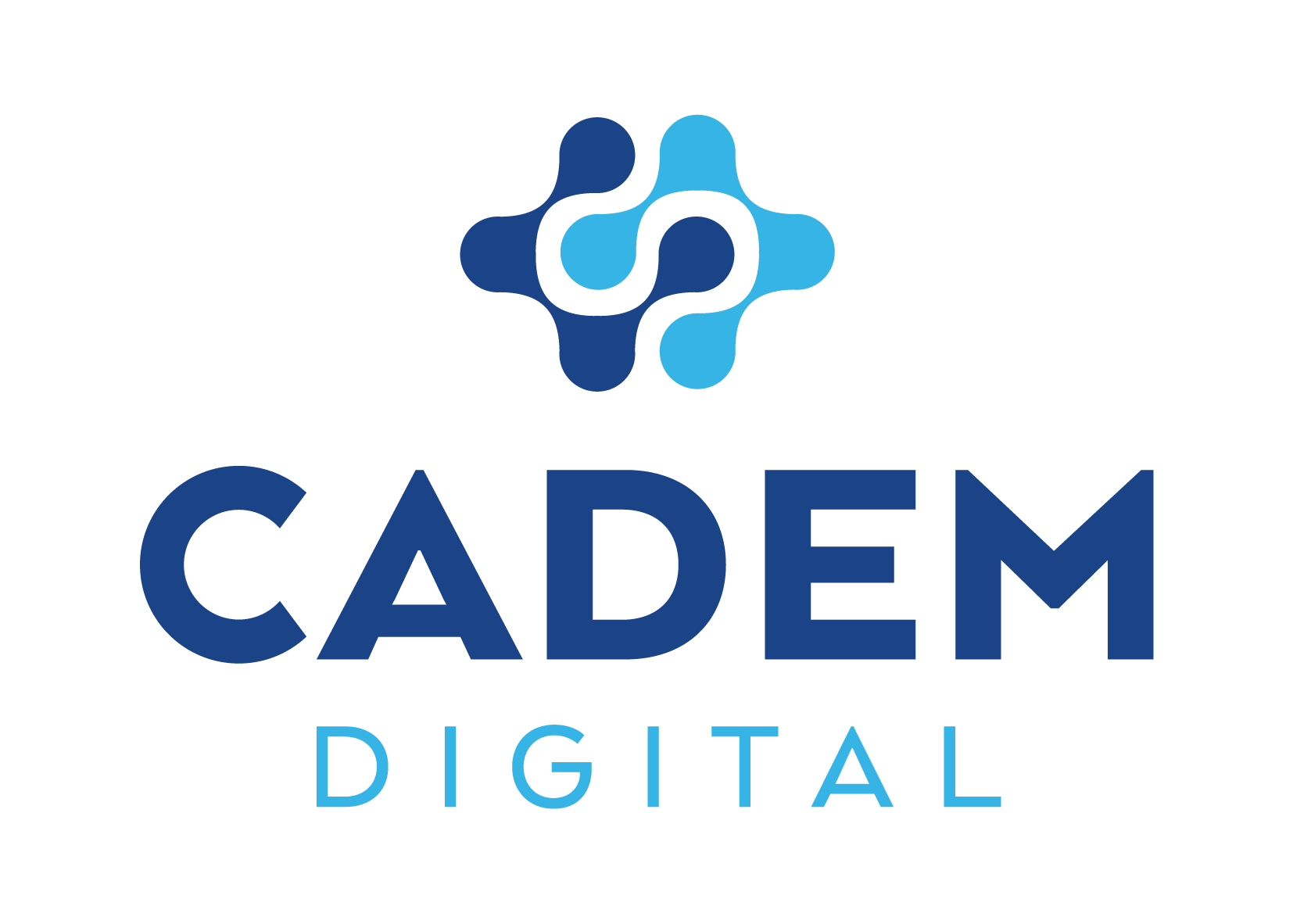
Focus on Cadem Digital
Operating in digital transformation since 1998, Cadem Digital offers PLM and 3DEXPERIENCE Platform solutions to provide its customers with improved speed and productivity across the full product development lifecycle. It provides innovative, integrated technologies in industrial manufacturing processes primarily for the automotive industry along with aviation, defense and machinery. Cadem Digital is a reliable, experienced and innovative solution partner in the digital transformation journey of brands in the process of creating their future, empowered by its experience and expertise in digitalization, technology, education and innovation in the industry.