SABELT
Sabelt, a leading global manufacturer of car seats, seat belts and motorsport products for racing activities, uses Bid to Win on the 3DEXPERIENCE platform. They became a digital-first company with true agility and were able to halve the time it takes to develop new products.
Developing safer, greener car seats
Many years of research and development go into the seat and harnesses that help to keep racing car drivers safe behind the wheel. When they have an accident, their seat belt and webbings must remain intact and functional to both withstand the impact of the collision and then unfasten without jamming to get the driver out fast. It’s why seven out of ten Formula One teams choose seat belts from Sabelt, a leading global manufacturer of car seats, seat belts and motorsport products.
The Italian brand is synonymous with the highest levels of safety in the world of supercars and motorsport, and works closely with the world’s top car manufacturers, including Abarth, Alfa Romeo, Alpine, Aston Martin, Ferrari, Jaguar, Maserati and McLaren. Since the company was founded in 1972, it has invested heavily in improving the performance and safety of its products, and today, carries out rigorous tests at its advanced internal dynamic test laboratory.
Through its Carbogreen project, which started in 2019, Sabelt also is on a mission to evolve into a low environmental impact manufacturer. It plans to launch a new line of seats within the next two to eight years to suit the specific characteristics of battery-powered cars and support the shift towards ecofriendly mobility solutions. The company is researching the processes and materials to combine efficiency and lightness for a “green” reinforced seat structure using new generation chemical and recycled plastics, including natural flax and basalt fibers, recycled carbon fibers, thermoplastic resins and recycled polymers. All accumulated knowledge is managed on the 3DEXPERIENCE® platform, which Sabelt implemented as part of its long-term digital strategy.
“As we explore the different materials that have enough structural performance in order for us to use less carbon fiber, we can check and manage all of this in the 3DEXPERIENCE platform,” said Roberto Marengo, chief technology officer at Sabelt. “We have all the information related to the materials we currently use, such as glass fiber and carbon fiber within our database on the platform. We’re integrating all the findings and material characteristics from our Carbogreen project, too. When we plan to go to market with our environmentally friendly product line, all the material, selection criteria and characterizations will already be there in the platform.”
The 3DEXPERIENCE platform brought us order and helped to avoid any confusion in the product development process.
Driven by innovation
As Sabelt continues its transition from a high-tech company with an artisan approach to a high-tech company with an industrial structure, it knows it must invest in the latest technologies to not only run its operations more efficiently, but support its customers more effectively, too. Every decision is driven by the company’s unyielding drive to innovate.
“Innovation starts with us,” Marengo said. “We chose the 3DEXPERIENCE platform to eliminate paper-based processes across our business and gain a 360-degree view of all the information we need to innovate. It supports us to take the documentation requests from our customers, ensure product quality, manage changes, approve modifications and release CAD data in the proper way, all managed entirely on the platform.”
Sabelt worked with Italian CAD and product lifecycle management (PLM) technology specialist and Dassault Systèmes business partner ABEX Italia to roll out the platform across its business.
“Without ABEX we could not have implemented the system,” Marengo said. “The team there has been our right arm, supporting us to integrate the 3DEXPERIENCE platform into our business. We’ve worked with them for many years; we know their capabilities and they understand us. If you ever need to discuss anything, the link between us both works very well. When you introduce a new, sophisticated platform like this, you discover there are some new things you’ll be able to do and there are some processes you need to change to work better. We’re working with ABEX continually to take full advantage of the platform for our business, and we’re beginning to see real results. If we are not prepared to change, we don’t progress; there is no innovation.”
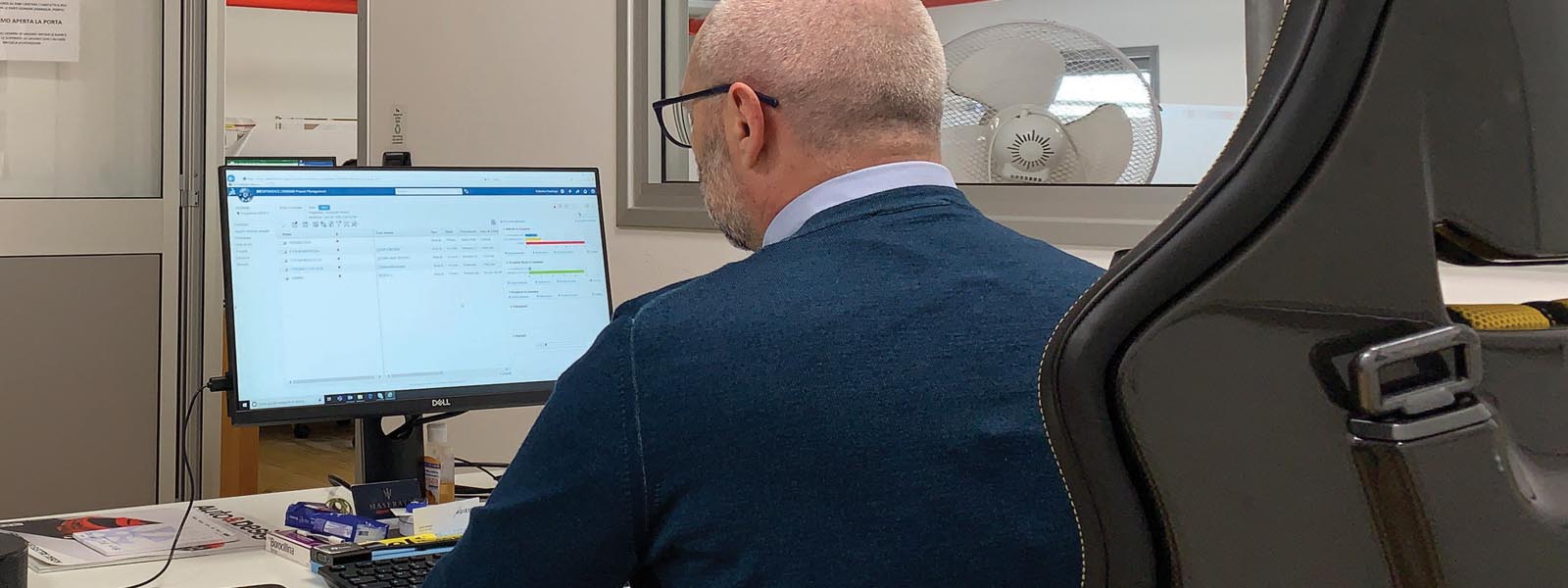
Combining speed and customization
Sabelt designs and makes every seat and seatbelt in collaboration with its clients, the car manufacturers, according to their specific needs. For any given client, Sabelt could be managing and developing hundreds of different parts for a multitude of car models. While the company already handled all its design and modelling processes in CATIA, it needed the data and project management capabilities in ENOVIA on the 3DEXPERIENCE platform to handle this complexity, streamline product development and keep tight project schedules on track.
“We manage a lot of different product with different personalization,” Marengo said. “Everything is customized and the biggest challenge we have is to respect the timing and launch everything on time. We decided to introduce ENOVIA, because with the short timeframes we are working within, we cannot make mistakes. The 3DEXPERIENCE platform brought us order and helped to avoid any confusion in the product development process.”
Sabelt mapped its entire internal product development methodology, the Sabelt Development System, to ENOVIA.
“The Sabelt Development System methodology provides a whole series of phases and approvals to allow the progress of each project, up to production,” Marengo said. “By managing all of this through ENOVIA, we improved the structure and order of our activities. For each project, the system guides us through a stage-gate model, supports us to manage the approval processes, keeping track of all information and decisions made at each step.”
One of the biggest advantages of this approach is that Sabelt can now work even closer with the customer to satisfy all their requirements and check manufacturing feasibility fast.
“We enter all customer requirements for each product into the platform and if they want to make a change, we can quickly demonstrate whether something is possible or not,” Marengo said. “Or if they give us another document, we can easily substitute it in the platform and make sure we’re working with the latest information.”
As Sabelt improves the customer experience, its efforts also translate into substantial time savings in the product development process.
“With the platform, we have seen a 25 to 30% reduction in the time it takes to produce a product, from the first specification we receive all the way through to production,” Marengo said. “We’ve also seen a significant improvement in terms of reducing mistakes. Now, we know we’re working with the most up-to-date version of the CAD data, so when we go to make a physical model, we can be sure it’s the right version. This equates to time and cost savings.”
We have seen a 25 to 30% reduction in the time it takes to produce a product.
Connected product development
The 3DEXPERIENCE platform supports Sabelt to connect all the dots across the product development lifecycle, from CAD and bill of materials (BOM), through to enterprise resource planning.
“It helps us to fulfill a lot of requirements,” Marengo said. “We can now put the eBOM data directly into our ERP system. Before, we had to do it manually. The platform is an instrument for us to achieve a truly connected product development process. From the planning phase all the way through to the manufacturing BOM and beyond, we can now manage all the data in a single environment.”
Because Sabelt now has full visibility across the business, it is able to flag and mitigate quality issues early, before they lead to bigger problems further down the supply chain.
“If quality control highlights an issue with a pin, for example, in case it doesn’t fit very well in a port, then they can immediately check on the platform if the pin is compliant with the original drawing or not,” Marengo said. “This is a big advantage. It allows us to discover if the pin is correct and there is an issue with the design, or that the pin is incorrect and the issue is with the supplier. We can identify the problem straight away and notify all relevant stakeholders. Then we can approve a modification directly with an electronic signature, and the issue cycle is closed and we release a new component.”
Full traceability leads to improved product quality and safety. “The platform ensures we’re working with the latest revision, while maintaining the entire version history,” Marengo said. “It also notifies all members of the project team that a new version of CAD data exists, eliminating the first cause of errors. From a standards perspective, we have full traceability and all the documentation to support regulatory compliance.”
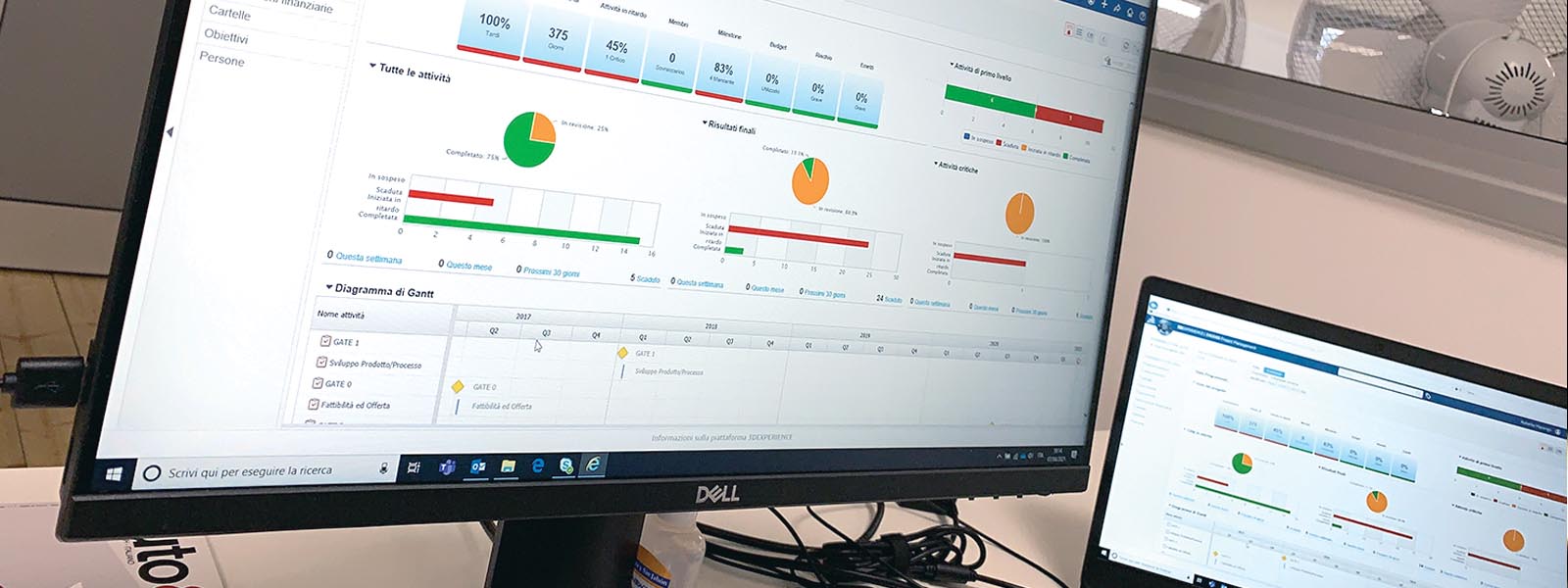
Real-time project updates
Every morning, Marengo opens ENOVIA on the platform to see the live status of all projects in a single dashboard.
“I can monitor everything in real time and compare the plan with the status and immediately identify any critical or late activities,” he explained. “Inside the project structure, I can see the level of completion for each task and every document connected to that project can be reviewed. I can switch to the GANTT view, where the activities are located inside a calendar view and all the dependencies are highlighted. Through 3DCompass, I can also view, rotate, zoom, section and review 3D data without going into the CAD tool. I don’t need a CATIA license to review the 3D design of a particular seat.”
Sabelt currently has more than 40 users on the platform and plans to add more in the coming months.
“Feedback from the engineers and project managers about the platform has been really positive,” Marengo said. “It has completely transformed the way they work and they are seeing the benefits the platform brings to our business. We’ve improved our approach and the mood is changing.”
Exploring composites
As Sabelt forges ahead with its Carbogreen project, the platform will play a key role in helping the company to develop more ecofriendly, sustainable products.
“We want to continue to push innovation,” Marengo said. “Going from the older version of CATIA to the 3DEXPERIENCE platform, we’re able to take advantage of more sophisticated composites functionality. It’s a challenging material to manage, but we set the standard for putting composites into car seats and now we want to go further with our technology.”
Sabelt records all fiber options, orientations and stacking sequences in ENOVIA to determine the best materials and approaches for its next-generation products.
“We are entering a whole series of data on composite materials in our ENOVIA library,” Marengo said. “This allows us through the composites module to define exactly which and how many layers of fiber are needed to make the back of a seat, for example, so that it exceeds the required safety performance. We can then make modifications directly in CATIA and put out a new release. We have the know-how and skills to go further and the platform supports us to innovate with confidence.”

Focus on Sabelt
Sabelt is a global leader in the development and manufacturing of original equipment car seats, seat belts and motorsport products for racing activities. Founded in 1972, the company started as a manufacturer of safety seatbelts for original equipment. Over the years, the company consolidated and developed an extensive knowledge of buckle systems, seat belts, seats for racing and supercars and complex retention systems.
For more information: www.sabelt.com

Focus on ABEX Italia
Founded in 1995, ABEX Italia is a specialist in CAD, CAE, CAM and CIM technology implementations and a Platinum Partner of Dassault Systèmes. The company is committed to bringing organizational solutions and specialized software tools to R&D and industrialization processes using innovative methodologies to help companies achieve the best results.