PT United Tractors Pandu Engineering
PT United Tractors Pandu Engineering in Indonesia is the largest heavy equipment engineering and manufacturing company for the energy logistics business. As the number of products produced continues to grow, the company started using the 3DEXPERIENCE platform to improve existing internal processes such as digitizing the design process, eliminating data duplication and ensuring employees work with the latest version of the truth.
Sustainable innovator
As energy logistics businesses navigate an energy-constrained, low-carbon future, they must evolve their supply chains to match, relying on high-quality innovative heavy equipment technology to operate more efficiently, effectively and sustainably.
For more than 37 years, PT United Tractors Pandu Engineering (UTPE), a subsidiary of the PT United Tractors TBK Group in Indonesia, has supplied critical equipment required by the energy logistics sector. As one of the largest suppliers of heavy machinery to energy logistics businesses, it is valued by its customers for its ability to design custom products, its manufacturing flexibility and the after-sales service guarantees it offers.
The company has built a strong reputation on its ability to combine manufacturing and engineering systems with highly advanced technology that enables it to create heavy machinery products that are reliable, productive, environmentally friendly, fast and delivered on time. All of this is in accordance with its company mission to provide sustainable value to its customers and outstanding product and service quality to achieve sustainable productivity and growth.
Unsurprisingly, then, adopting and developing cutting-edge technology is critical to the business’s future.
“Technology plays a key role in our company’s development, helping us to handle the many custom product design requests from our customers in a very short timeframe,” said Annas F. Habibie, design engineering department head at UTPE. “We realized that we can only achieve this by using reliable design tools.”
A natural choice
For many years, the company used design software to handle its product development, but until recently has suffered from an inability to centralize its data storage.
“This resulted in component files not being managed properly, yielding duplication of modeling, long search times, difficulties in tidying up revised drawings and inconsistent design revisions which led to errors,” said Annas.
UTPE turned to its Indonesian technology partner and Dassault Systèmes software reseller PT Citrathirza Anugerahjaya (PT Citra) to propose a solution centered around the following drivers:
- Speed up product design to build more custom products
- Improve data management to better handle the growing number of product variants and components being manufactured
- Synchronize CAD-based part number data with actual data in the company’s SAP enterprise resource planning (ERP) system
- Minimize the delivery of information errors that occur during the design phase to the production stage
- Better serve the demands of the marketing department.
Critically, the solution UTPE selected needed to integrate seamlessly with its existing design software and ERP system. As a long-term user of Dassault Systèmes solutions, in many ways it made sense for UTPE to expand its use of the software. PT Citra carried out a thorough evaluation of the company’s needs and recommended the 3DEXPERIENCE® platform.
The biggest business impact of the 3DEXPERIENCE platform is felt primarily in the engineering division. In particular, it helps them keep pace with the marketing division, which sells products that are custom designed, but mass produced.
Speeding up design
As UTPE seeks out new ways to speed up product development and production while continuing to handle its customers’ unique requirements, it knew it needed to simplify its design process by allowing designers and engineers to reuse existing designs, collaborate effectively on changes and have a better oversight of the company’s growing components and parts library.
“The 3DEXPERIENCE platform helps engineers design products faster and more accurately, because it has a centralized data center that makes it easier for them to pull up the components they need,” Annas said.
Using SOLIDWORKS 3D CAD software and ENOVIA for collaborative innovation on the 3DEXPERIENCE platform, design changes are easier to handle now, too.
“We have started using SOLIDWORKS design software for the process of designing trailer products and managing the solid modeling data using ENOVIA,” Annas said. “The most effective and useful feature in SOLIDWORKS is that we can now handle design modifications quickly using existing design references through top-down techniques. This approach speeds up the design process as the reference fields and lines drawn out in the sketch process are able to keep up with any changes as further modifications are made.”
Today, engineers can keep up with customer demand and even have more time to work on higher-value activities within the company, such as focusing on developing new innovative products and sharing high-quality 3D images with the marketing department to boost ongoing sales. “The biggest business impact of the 3DEXPERIENCE platform is felt primarily in the engineering division,” Annas said. “In particular, it helps them keep pace with the marketing division, which sells products that are custom designed, but mass produced.”
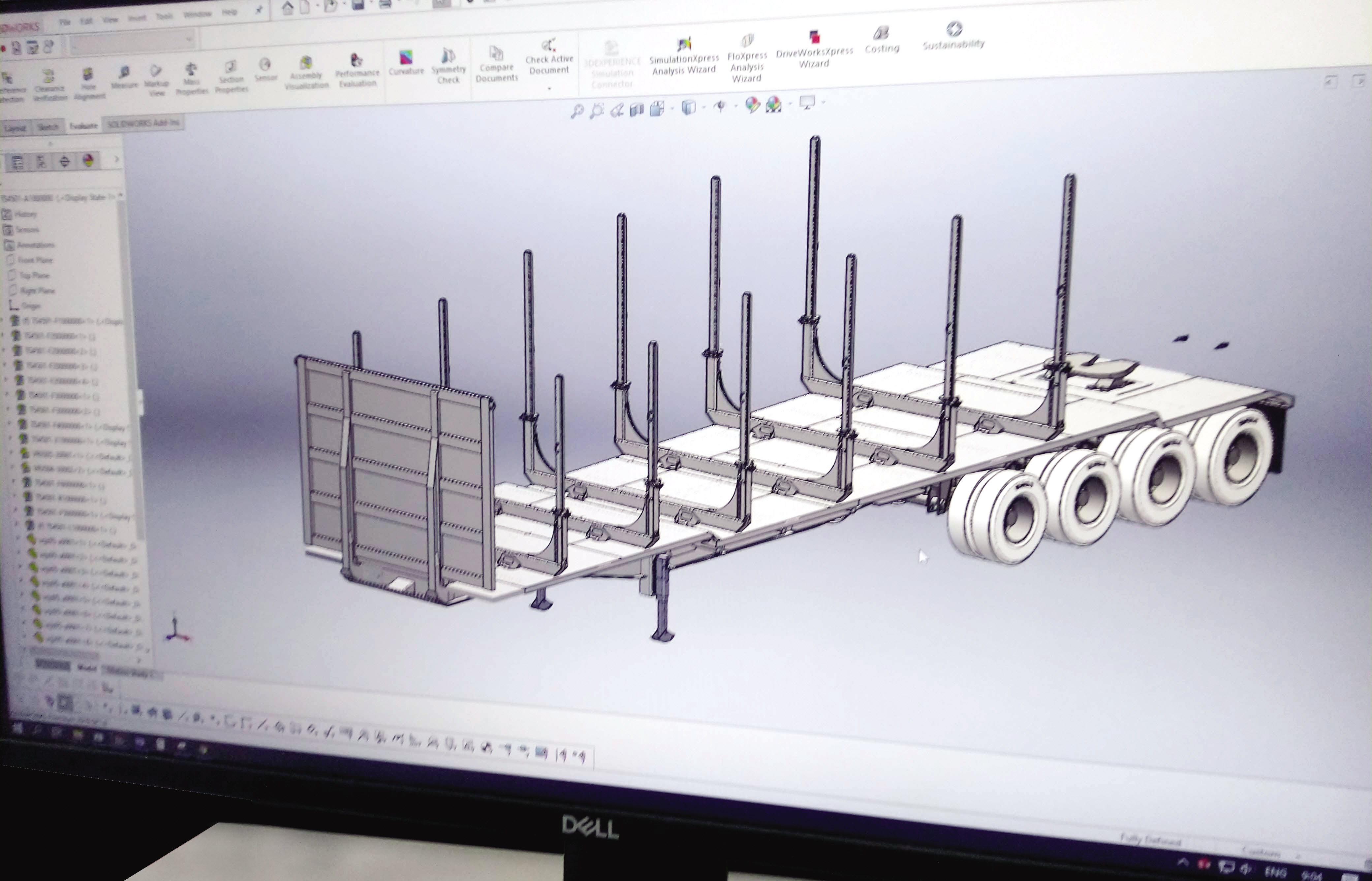
Data clarity
With ENOVIA, UTPE has a centralized database that enables it to efficiently share information company wide, reuse designs, easily search for components and collaborate across disciplines as design modifications arise.
Getting a better handle of its growing components library, which encompasses bulk material, hydraulic, mechanical and running gear and adapter fitting components, was a key goal for the company. Backed by ENOVIA collaboration software, engineers can now access the information they need at the right moments, both to develop new designs and handle design modifications throughout the product development process.
“The 3DEXPERIENCE platform shortens the time it takes for engineers to search for the components they need,” Annas said. “It also helps engineers work effectively as design revisions arise as it flags all areas of the design that are affected as well as its implications further down the supply chain so that they can keep an accurate status update, reduce errors and manufacture products on time.”
Synchronized CAD and BOM
One of the key reasons UTPE chose the 3DEXPERIENCE platform was because of its ability to integrate seamlessly with the company’s existing multiple CAD software environments and ERP system.
Using SOLIDWORKS and ENOVIA, UTPE has the ability to synchronize information between its CAD software and ERP, and automatically generate the engineering bill of materials (EBOM) and manufacturing bill of materials (MBOM). What was previously a time-consuming manual process is now a fast, efficient experience as engineers know exactly what components and how many they require straight from their CAD drawings. Designers can also see which components are already available for use, leading to design and material efficiencies.
“The 3DEXPERIENCE platform is able to facilitate project management as the MBOM can be generated automatically, processing the material list data right from the CAD,” Annas said. “The process of sorting the type of material used can also be done on the platform, helping to speed up and improve the accuracy of component calculations and groupings. This process is much better than before we implemented the 3DEXPERIENCE platform when the component calculation process was carried out manually by reviewing each assembly drawing.”
UTPE is now looking at a paperless future as it continues to automate and digitalize its design-to-manufacturing processes—a critical part of its sustainability strategy which is deep rooted in its long-term goal to care for society and the environment.
“We believe that we can save costs by reducing our use of paper,” Annas said. “We have already reduced the number of working drawings we need to produce, and we can now go paperless all the way through to the workshop.”
Long-term benefits
UTPE’s decision to implement the 3DEXPERIENCE platform was a bold move. While the company was fully invested in the solution from the start, migrating its entire design, parts and components library to the new platform was a time-intensive task. However, UTPE believes that their efforts have already paid off.
“We believe that UTPE will now continue to be able to compete in the global market because upstream of our business chain we are equipped with software that is able to process data faster, more accurately and can be accessed all the way up to the workshop level.”
Throughout the implementation and beyond, PT Citra supported UTPE to get the most value from its software, helping the company with customizations and training. UTPE trusts in Dassault Systèmes as a long-term technology partner too.
“The data management solutions offered from Dassault Systèmes are ideally suited to our needs,” Annas said. “Our relationship with them is very good; the system implementation was carried out professionally and responsibly.”
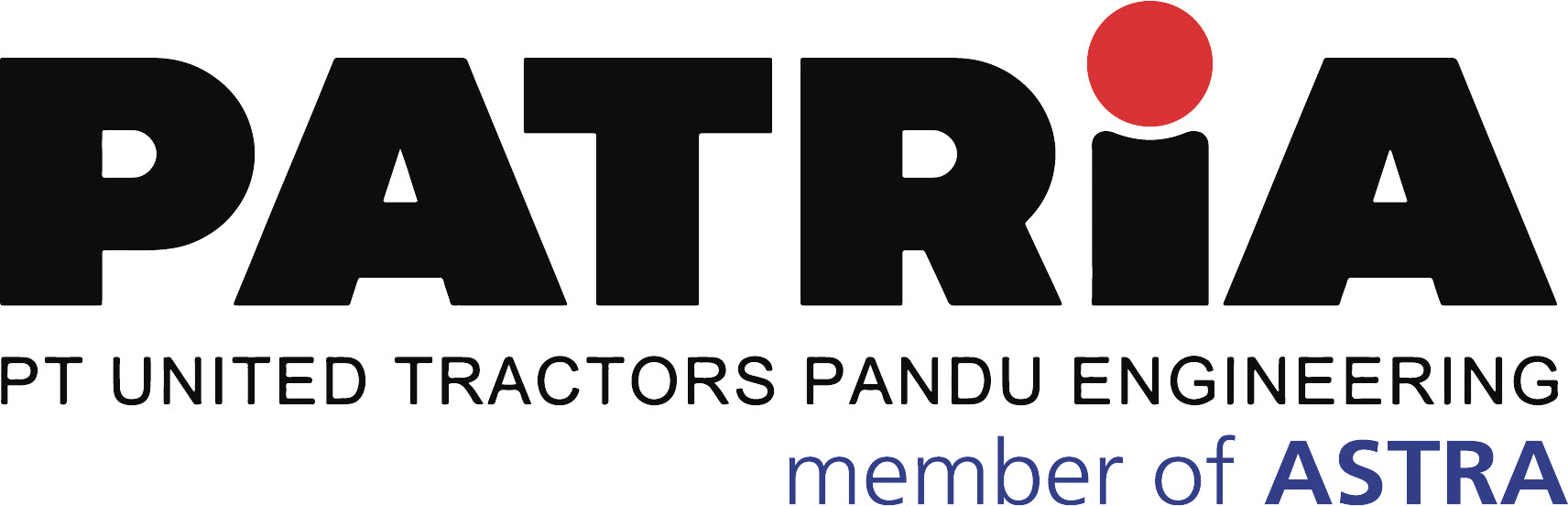
Focus on PT United Tractors Pandu Engineering
PT United Tractors Pandu Engineering is one of Indonesia’s leading manufacturers of heavy equipment for the industrial, maritime and energy sectors. The company was founded in 1983 and operates through its brand name PATRiA, providing its customers with a full lifecycle service from design innovation to aftersales support.
Products: Forklifts, trailers, trucks, tippers, logging trailers and forks, concrete mixers, tankers, hydraulic pumping units and spare parts.
Headquarters: Cikarang, Indonesia
For more information: http://www.patria.co.id/
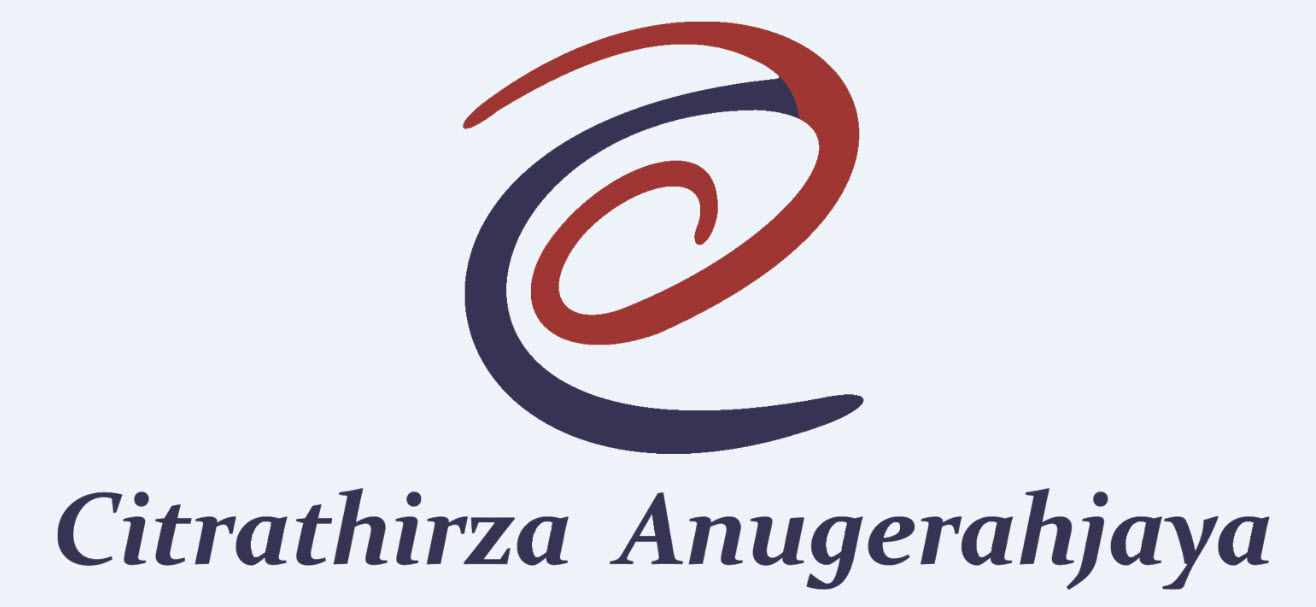
Focus on PT Citrathirza Anugerahjaya
PT Citra in Indonesia is a Dassault Systèmes reseller established with the goal of delivering end-to-end business solutions covering CAD, CAM, CAE, product data management and digital manufacturing. The company has a strong and experienced team committed to understanding customers’ needs, proposing suitable and scalable solutions, and handling installation, training and support, covering industries including automotive, consumer products, electronics, mold and dies, and heavy machinery. Customer satisfaction is PT Citra’s main focus when doing business.
For more information: http://www.caj.co.id/