Prodomax
Prodomax leverages DELMIA simulation and virtual twin capabilities to support a new approach to planning, validating and optimizing customers’ production lines.
With the addition of DELMIA and our highly skilled robotics simulation team, we’re delivering new systems that meet our customers’ evolving needs faster than ever before.
Challenge
Based in Canada, Prodomax designs customized automotive-part manufacturing lines. As customers demand faster project turnarounds and request simulations in their specifications, Prodomax sought an industry-leading simulation solution to test and integrate robots virtually ahead of installation.
Solution
Prodomax selected Dassault Systèmes’ Digital Equipment Continuity industry solution on the 3DEXPERIENCE platform. Through this solution, Prodomax leverages DELMIA to simulate robotics within the context of each customer’s plants, covering robot reach limitations and tooling interferences. Prodomax also uses SOLIDWORKS to design tooling that is used in their automated lines. These simulation and virtual twin capabilities support a new approach to planning, validating and optimizing customers’ production lines.
Benefits
DELMIA allows Prodomax to test and integrate robots virtually to improve the accuracy of tool designs and robot placement, and optimize cycle times. Engineers benefit from rich robotic simulation capabilities to work efficiently and solve potential issues ahead of physical installation on the shop floor so that production lines get up and running as quickly as possible.
Simulating Robotics in a Virtual Plant
Robotics and automation have already reshaped factories and production lines, helping to boost manufacturing efficiency, increase output and enhance overall product quality. More recently, companies are turning to robot and process simulation to further optimize plant layouts – testing first in the virtual world to improve their designs and accelerate cycle times.
One company doing this to great effect is Prodomax. The Ontario, Canada-based company designs and engineers turnkey automated manufacturing solutions for original equipment manufacturers (OEMs) and Tier 1 automotive manufacturers. Day-to-day, Prodomax’s engineering team problem-solves all manner of scenarios to integrate the latest robotics into their customers’ lines. By introducing DELMIA’s rich simulation capabilities into their toolkit, they now validate line setups before committing to installing each physical production line or cell. This helps them to work faster, more easily meet customers’ increasingly complex requirements and reduce the amount of floor space used.
Recently, for example, Prodomax was commissioned to develop a new cradle line. The team built it in DELMIA, including all welding and material handling paths and operator stations. Simulation helped them test different designs and determine the minimum height requirements and placement for a mezzanine level. By recreating the physical conditions of the customer plant in the virtual environment, they made sure all robots and equipment operated within safe limits.
“We virtually tested the welding paths and checked the operation of all the robots together to identify robot zone problems such as timing issues,” said Steve St. Onge, senior robotics technician at Prodomax. “DELMIA allowed us to virtually verify our entire process. Even when the line went onsite and the customer wanted to add new equipment, we could check within the simulation that the existing robots could move around that equipment. Once these types of installations are on the floor and in the customers plants, there’s a very limited amount of downtime. You’ve got to get it right the first time and simulation has been a big game changer for making that happen.”
Flexible and Scalable Simulation Solution
Prodomax selected DELMIA for its powerful simulation capabilities and flexibility. The company also valued the fact it has no limitations on project size and it covers most common manufacturing processes.
“DELMIA offers support for different types of welding,” said Jakub Garai, manager of Controls, Electrical Design, Fluid Power and Robotics at Prodomax. “It has proven to be a really scalable product.”
One of the key reasons for embracing simulation is to meet its customers’ growing demands. Many customers now put simulation requests in their specifications, covering everything from static simulations and interference checks to cycle-time analysis and validation.
“We’re now capable of performing all those tasks and everything in between using DELMIA,” Garai said.
Dassault Systèmes and its technology partner Aventec have become part of the Prodomax team. They helped to overcome initial hurdles to make sure the DELMIA implementation was successful. Today, they remain in constant communication to further improve the software.
“Aventec integrated themselves with Prodomax and our processes and procedures,” Garai said. “Knowing how we operate allowed them to tailor the training to make it as effective as possible for our entire team. This has really paid off as when we have a new addition to the team, they are up-to-speed a lot quicker than they would have been in the past.”
“Aventec provided us with full-time support on ‘live’ projects, which was invaluable as we modified our processes and learned to use the tool while still ensuring we delivered our projects on time,” added Lenka Cernova-Cerrato, senior process engineer at Prodomax.
One of the key advantages of DELMIA is that you can have multiple robot manufacturers in the same work cell. We can swap out different robots and get new code to the people on the floor.
Validating Robot Behavior Ahead of Installation
Because DELMIA supports all major robot brands, Prodomax easily switches between different robots when configuring a line to determine which robots are best suited for each task.
“One of the key advantages of DELMIA is that you can have multiple robot manufacturers in the same work cell,” St. Onge said. “We can swap out different robots and get new code to the people on the floor.”
This functionality allows Prodomax to efficiently test robots in different configurations and scenarios to improve overall design accuracy.
“In the past, we'd install items where we believed they should go based on static studies and then we found later on that it was not the best place for that robot to be and we had to move things around,” Garai said.
Within the virtual plant, Prodomax’s engineers identify robot reach limitations, tooling interferences and see how robots operate together. They can study tooling orientations and virtually test tool kinematics, such as tooling clamp motion, sequencing robots and seeing how different stations interact with one another. Simulating all these elements makes it easier to refine their machine designs, leading to a smoother and faster installation process on the shop floor.
“Our goal was to have zero rework on the physical floor at the installation stage, and since we started using DELMIA we have not had to move a single robot due to engineering errors,” Cernova-Cerrato said. “Before, we carried out static reach studies, but we were not able to visualize the robot paths. DELMIA enables us to go through all the motions of the robots and optimize their placement.”
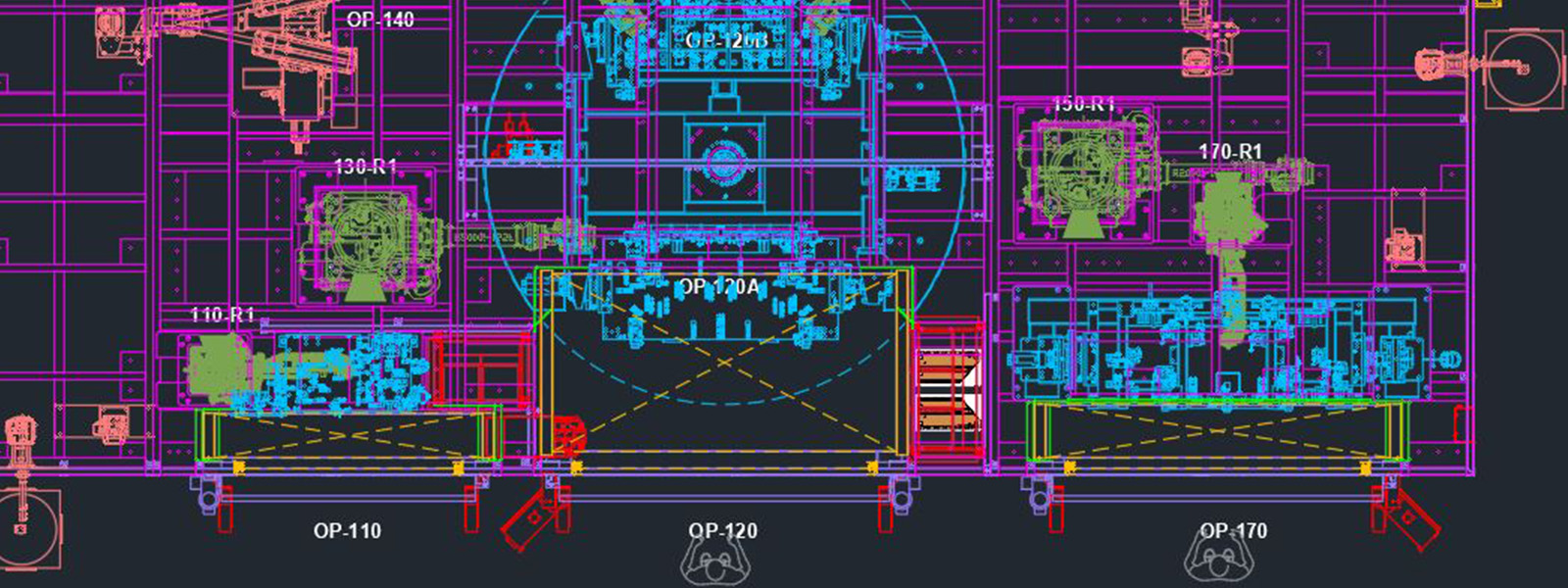
Collaborative, Efficient Engineering Approach
Prodomax now works more efficiently as different team members within the simulation department can access all the information they need and see the parts and machines they are developing within the context of the same line model. All data is stored centrally in ENOVIA on the 3DEXPERIENCE platform.
“It’s very easy to collaborate and spread the workload,” St. Onge said. “We are all aware of the machine’s footprint and where our boundaries are. For example, welding torches take up a lot of volume. With DELMIA, we can create torch clouds, determine where we need the welds to be and then export that CAD data to our design department, which uses SOLIDWORKS, so they can put the tooling around our torch clouds and see interferences very quickly.”
The ability to automatically roll out design changes and create design and robot program templates also boosts productivity.
“Say we want to change a tip dresser through a line, all we need to do is amend that one piece of CAD and it automatically updates every instance within the machine,” St. Onge said. “We can also create function templates in DELMIA that we can use in other projects to save time.”
Aventec provided us with full-time support on ‘live’ projects, which was invaluable as we modified our processes and learned to use the tool while still ensuring we delivered our projects on time.
Faster Commissioning, Satisfied Customers
Today, the time between powering on and running a production line is greatly reduced now that Prodomax simulates the system ahead of time. This helps the company to meet its customers’ ever-tightening schedules and come up with optimized production solutions that lead to significant efficiencies on the shop floor.
“The timelines to build new lines are constantly being compressed; sometimes we have only a few weeks to get a line up and running,” Cernova-Cerrato said. “DELMIA allows us to create downloadable offline programs which we can transfer directly to our robots to carry-out cycle analysis and robot utilization.”
This new approach improves how Prodomax communicates with its manufacturing customers too, allowing them to virtually see and verify a new line well ahead of physical installation.
“At the design stage, we now are able to present a 3D tool visualization to the customer showing robot interactions and interactive animations,” Cernova-Cerrato said. “This has greatly enhanced how we communicate with our customers, giving us a professional edge.”
Looking to the future, Prodomax plans to continue using DELMIA to achieve greater efficiencies across its internal design and engineering processes. Through simulation, it innovates at speed without compromising on the high levels of quality that its automotive customers expect.
“With the addition of DELMIA and our highly skilled robotics simulation team, we’re delivering new systems that meet our customers’ evolving needs faster than ever before,” Garai said. “Now, we’re looking into areas where we can save even more time, such as virtual commissioning and PLC code generation.”
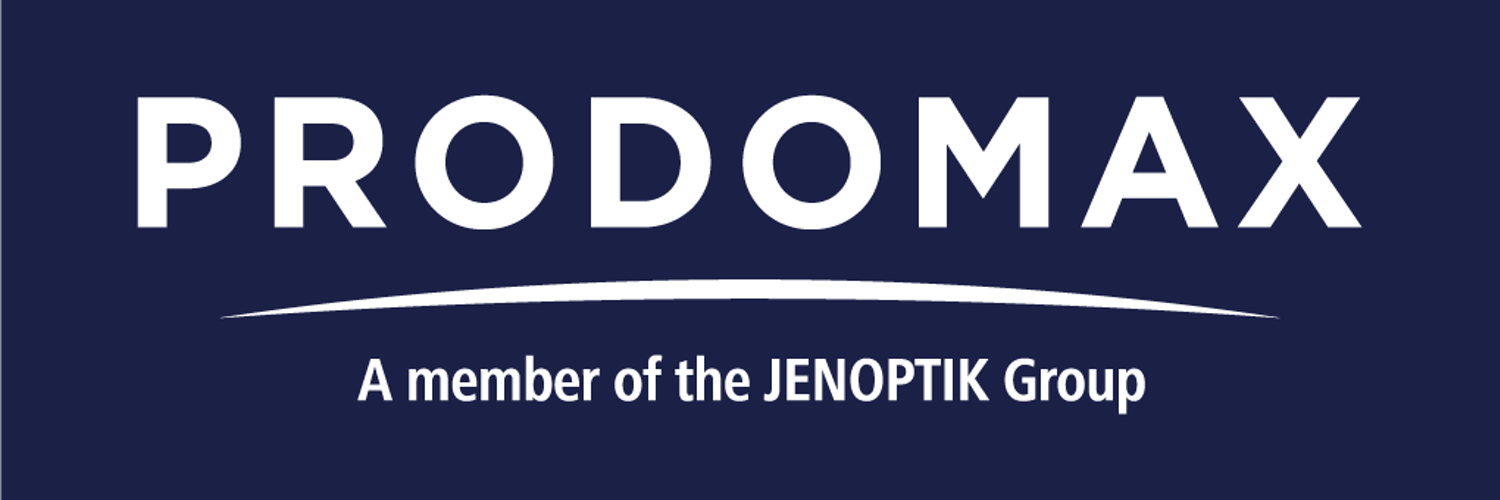
Focus on Prodomax
With over 52 years of automotive experience, Prodomax specializes in the design, engineering, and turnkey integration of automated manufacturing solutions for OEM and Tier 1 automotive manufacturers. Through cutting-edge technology and robust engineering design, the Canadian company strives to deliver the best systems to its customers and meet their unique requirements.
For more information: www.prodomax.com
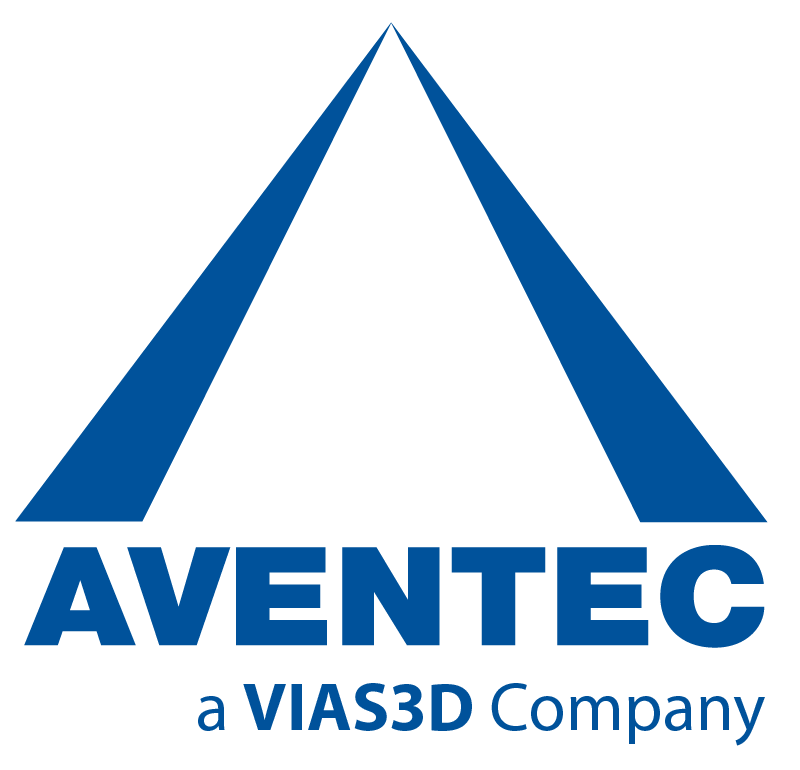
Focus on Aventec
Aventec, based in Canada, provides consulting and training services to automation integrators, robotics integrators and industrial equipment OEMs for CAD design, FEA, CFD, and robotics & plant optimization. The company specializes in CATIA, SIMULIA, DELMIA, ENOVIA and EXALEAD on the 3DEXPERIENCE platform to help engineering and manufacturing companies improve their competitiveness, productivity and profitability.