POSCO A&C
POSCO A&C chose the 3DEXPERIENCE platform to implement a smart construction process. They created a construction virtual twin using the industry solution experience Construction Excellence, enabling optimized construction project management to improve productivity while decreasing costs.
Construction virtual twins add a new dimension
By setting up a virtual reality (VR) space to visualize its construction management solution, Korean architectural services company POSCO A&C is pushing the boundaries of what’s possible in its field with construction virtual twins.
On one of its recent projects at the Gwangyang Steelworks furnace site in South Korea, the firm used VR to simulate driving routes for truck drivers. The huge trucks that transport steel products and hot melted steel on its premises were not easy to maneuver. “We found that we were able to virtually drive safely on the roads within our plants at a speed limit of 40km/h,” said Byun Sungjin, senior manager of plant construction management at POSCO A&C.
VR also allows key stakeholders to visualize the construction site in real-time to intuitively identify deficiencies, accurately reflect the intentions of mutual stakeholders, and establish alternative measures. “We now organize many VR review meetings for visual collaboration between stakeholders, and CATIA’s 3D capabilities perform really well. In fact, the visual effect of CATIA is highly praised by our important visitors – it can be very impressive. That’s why a VR space is now permanently installed in the BIM room of the main design office and construction site,” Sungjin said.
POSCO A&C’s new approach is based on the 3DEXPERIENCE platform. “The 3DEXPERIENCE platform builds the foundation of our Smart Construction Management (CM) Platform,” said Lim Seokgon, head of plant construction management at POSCO A&C. The resulting Smart CM Platform® is a collaborative, digital system used for practical construction tasks including 3D modeling, simulation, VR capabilities and design changes.
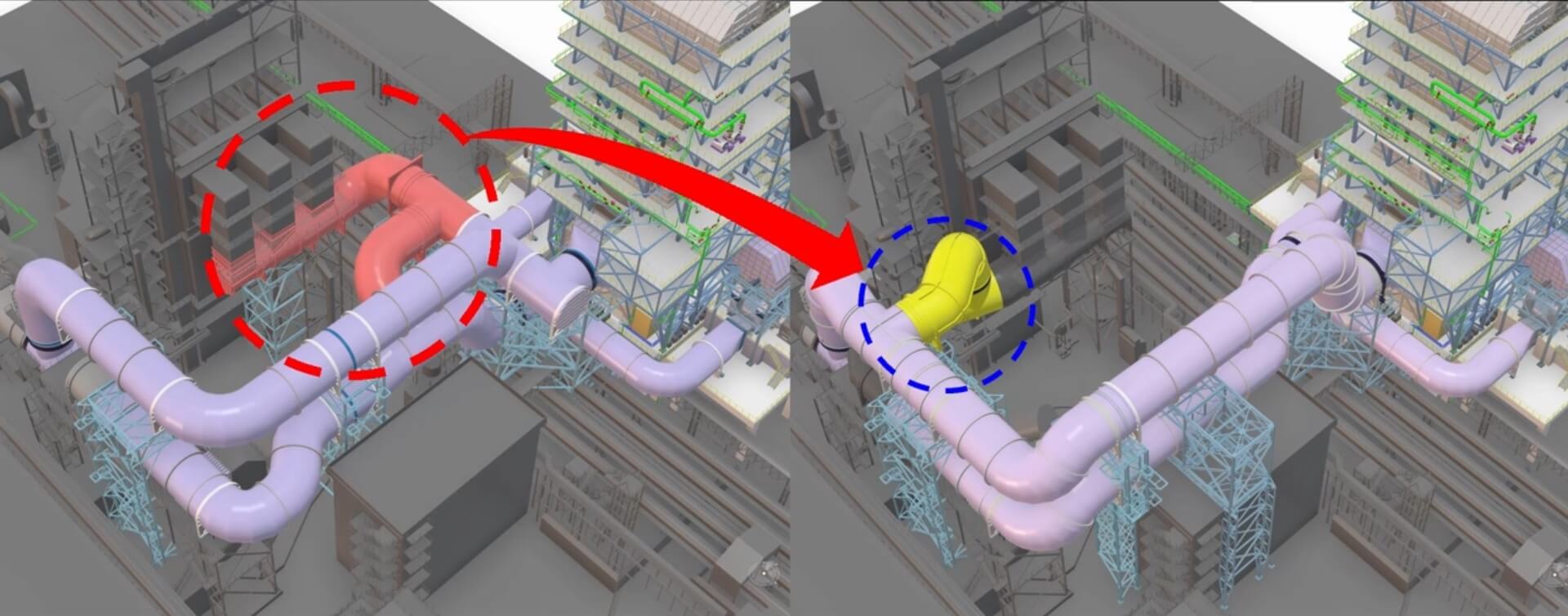
Building on success
POSCO A&C introduced the 3DEXPERIENCE platform in 2018. “Virtual twin technology really appealed to us,” said Seokgon. “We wanted to pursue digital innovation. Managing large amounts of data that comes from 3D modeling was challenging and it was also getting expensive. We realized we needed a unified platform approach instead.”
With this in mind, POSCO A&C began to explore use cases from the big global software companies. “We analyzed how the various market offerings could help us leverage virtual twins to contribute to the construction of a plant; to reduce construction period, and increase worker productivity and worker safety; and to prevent construction obstacles by replicating real-life environments,” Seokgon said. “We found the 3DEXPERIENCE platform could help in all three scenarios. It would allow us to freely link all construction information, such as 3D design and 3D models, simulations, documents and processes – in one place.”
Having a 3D virtual model of the process has helped us shorten the construction period by more than 15 days.
A new way of collaborating
The platform accumulates all information and data generated during the construction lifecycle including that related to planning, design, construction and safety, to create an environment where all stakeholders involved in the project can review details and engage in real time.
This is a significant departure from POSCO A&C’s previous system. “We had a file-based management system, where all documents were stored and managed on the individual PCs of ordering companies, designers, construction project managers and suppliers,” said Seokgon. “This was inefficient and prone to errors, especially around information delivery.”
Adapting to the new platform was challenging as users were unfamiliar with the new approach and methodology. However, thanks to Dassault Systèmes' systematic platform education and meticulous technical support, users learned quickly. “We needed step-by-step training from the most basic to advanced functions of the 3DEXPERIENCE platform. We learned how to use the platform with ENOVIA, to create 3D modeling of facilities with CATIA and to implement simulations and construction schedules according to structural conditions of construction equipment with DELMIA,” Sungjin said.
Before long, the company was experiencing significant benefits, especially when it came to collaboration. “The plant construction period is short because of the complexity of processes and facilities, and the parallel operation. So, it’s important to collaborate quickly within a given time,” said Sungjin. “The Smart CM platform facilitates online collaboration between key stakeholders including designers, contractors, partners, supervisors and purchasers – through the entire planning to maintenance life cycle. It helps project stakeholders understand and make decisions in real time without unnecessary meetings and face-to-face reports. It also improves design performance by preventing conflicts, faulty design and omissions, providing building information modelling (BIM) data to the maintenance stage.”
ENOVIA on the 3DEXPERIENCE platform has proven to be particularly advantageous with its project management capabilities. Notices, suggestions and cooperation are realized through communities in 3DSwYm, Dassault Systèmes’ social innovation application.
“Construction project management can be successfully completed only when various stakeholders collaborate efficiently based on comprehensive management technologies such as process, quality, cost, safety, measurement and licensing,” Sungjin said. “The Smart CM platform includes a dashboard of widget features that can actively utilize ENOVIA’s collaboration and 3D model management capabilities. The platform supports a multi-CAD environment and can integrate different components from different suppliers. This allows us to optimize construction project management and makes it easy for stakeholders to intuitively understand and apply on projects.”
ENOVIA’s Gantt function is also used to review and edit project schedules in a graphical way. “We can link processes, costs and 3D models for each task,” Sung-jin said. “We also use the Gantt Chart during our daily meetings to monitor the progress in real time.”
Efficiency has also improved, because the various stakeholders participating in a construction project can now use the Smart CM platform to handle most aspects of their work. “It’s not uncommon for various problems to occur simultaneously at the construction site,” Sungjin said. “The use of integrated information is important to solve these problems. We can make quick and reasonable decisions on issues occurring in the field, minimizing delays. What’s more, because there is now a standardized work format for process, quality and safety management in the system, stakeholders can enjoy consistent performance and don’t have to spend time collecting and verifying scattered information.”
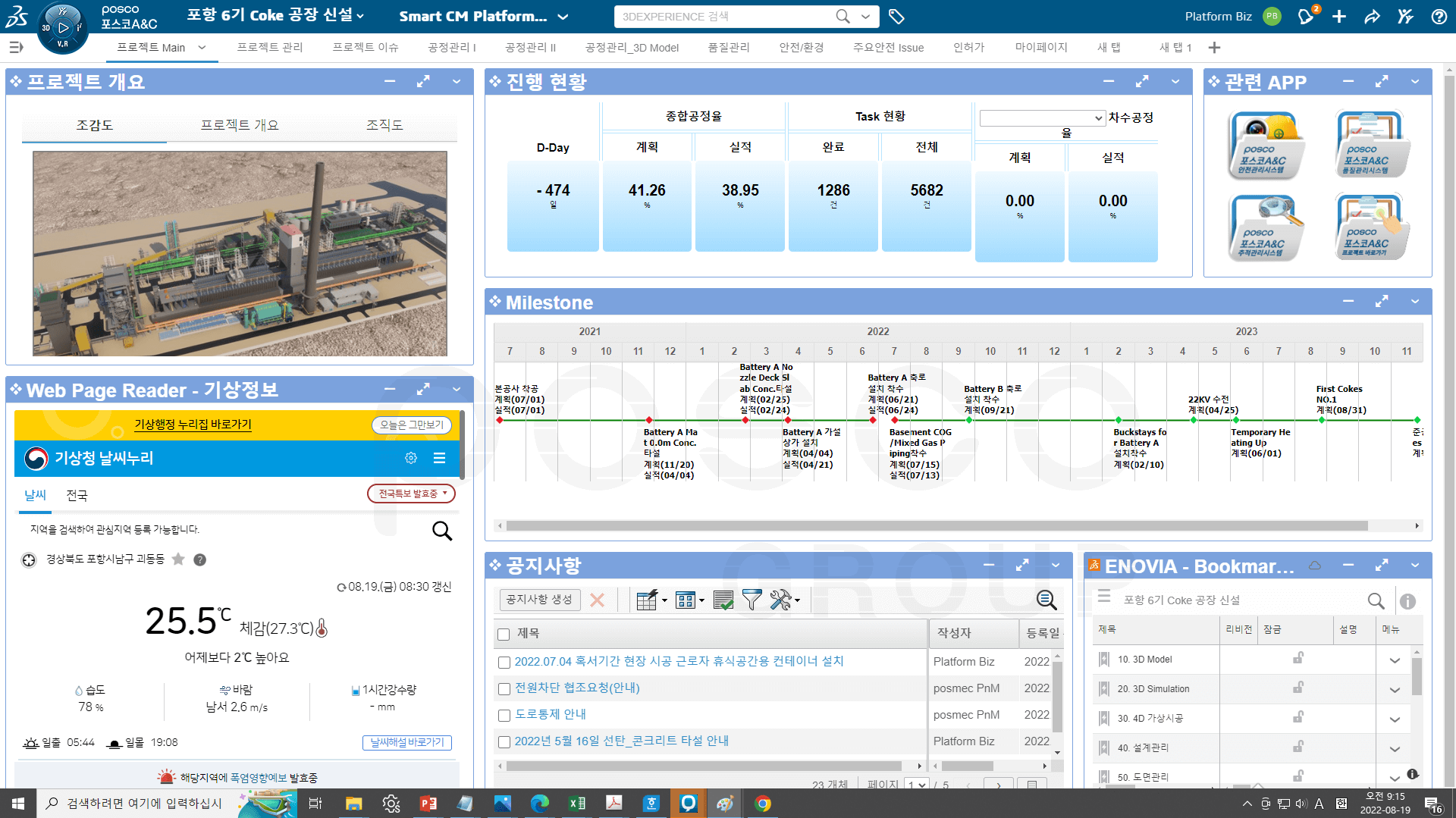
Using a construction virtual twin to install a large duct
Virtual twin simulation revealed how it was possible to install large duct measuring
in length
in height
in diameter
Compatibility comes as standard
Before the implementation, the team at POSCO A&C was struggling with compatibility issues since they used various applications to generate 3D models for each project. These issues are now consigned to the past.
“Most projects in steel plants require the participation of a large number of experts, including civil engineering, construction, machinery, electrical communications and firefighting. Irregular design data from various sources must be entered, converted and utilized in one platform for integrated construction management,” Sungjin said. “Using the CATIA 3D Design application in our Smart CM platform has allowed us to input and manage a large amount of unspecified design data and we can now integrate the 3D designs of each contributing partner in one 3D master model. It is highly efficient because it can be used for ENOVIA and DELMIA by utilizing data stored in cloud servers.”
CATIA also supports the multiple CAD environments of POSCO A&C’s various designers. “This was essential for integrated project management,” Sungjin said. “There are not many CAD solutions out there that can manage design data received from multiple complex unspecified designers.”
The solution came into its own on the firm’s repair project at Gwangyang Steelworks in South Korea. “The 3D model we created for this job consisted of about 3,000 products and more than three million parts,” said Sungjin. “It was a large-scale plant construction project with more than 50 designers participating. CATIA was essential for the integrated management of such large-scale modeling into a single file.
POSCO A&C also uses the DELMIA application to review mechanical constraints of construction equipment and construction site conditions by simulating different construction layouts and making tweaks to improve site use efficiency.
“We can test our ideas quickly and easily to verify construction feasibility and take action on potential issues in advance by presenting an optimal construction plan through the reconstruction of construction units,” Sungjin said. “For example, we had to install a large duct at a Pohang plant. The duct was made up of 12 parts, and measured 300m in length and 40m in height, with a diameter of six meters. Our simulations of the site made us realize that we did not have the space or resources to assemble it on site – in fact it would have been dangerous to attempt to do so. Instead we assembled it off-site, and then maneuvered it into position using a crane – the position of which we had also simulated. Having a 3D virtual model of the process has helped us shorten the construction period by more than 15 days.”
In addition, since the construction equipment on site is implemented as designed through DELMIA, POSCO A&C can check any interference with surrounding facilities to prevent on-site accidents, and specify the installation of temporary safety facilities in advance if necessary.
These aren’t the only benefits. “By integrating various heterogeneous CAD systems into the platform and building a common 3D model, we are able to virtually discover or simulate problems in maintenance, operation and construction,” Sungjin said.
Construction business management through Smart CM Platform®, which is based on the 3DEXPERIENCE platform, has significantly reduced construction period and amount of manpower. This has led to increases in productivity, quality and construction safety.
Tangible results for future business
Overall, Seokgon believes the 3DEXPERIENCE platform has resulted in far greater benefits than they could ever have anticipated. “Construction business management through Smart CM Platform®, which is based on the 3DEXPERIENCE platform, has significantly reduced construction period and amount of manpower. This has led to increases in productivity, quality and construction safety. We are now able to simulate and tackle qualitative effects such as timely project completion,” he said. “Recently, we used 3D Review in CATIA to improve the design of a NOx (nitrogen oxide) reduction system before installing it in our Sintering Plant. We then optimized construction plans through DELMIA, leading to greatly improved productivity and decreased construction costs by 9% or $2million (2.4billion South Korean won) within a year.
It’s been so successful, in fact, that POSCO A&C is exploring how it can leverage the technology further in the months and years to come.
“We intend to connect planning, design, purchase and procurement, construction, and maintenance to the Smart CM platform,” Seokgon said. “When designing before construction, we hope to use virtual construction in 4D, connect it with a smart tracking system to manage the process, and create various electronic manuals to become a partner in the construction industry that helps the client achieve innovative operational production.”
The company also hopes to expand its business to provide construction maintenance, a move which can be achieved more easily thanks to the 3DEXPERIENCE platform. “With many facilities in domestic manufacturing plants now reaching 20 to 30 years of age, maintenance costs are expected to increase sharply, as in the case of other advanced countries,” Seokgon said. “Therefore, it is necessary to develop a technology that can evaluate the aging of facilities and predict the future.
Discover more about the Construction Excellence industry solution experience.
Discover additional insights from a DELMIA user.
00:00 – 01:23
Lim Seokgon, Head of Plant Construction Management, POSCO A&C:
Working with a virtual twin of our plant construction is key in helping us verify, improve, and complete projects on time. We’ve significantly increased work productivity by eliminating many possible risks, and reducing construction cost by $2 million USD or 9%, within a year. POSCO A&C offers various architectural services. We needed to simplify and systemize projects so that workers can easily understand. Creating a safe work environment is our top priority, and compliance eco-friendliness, and carbon reduction are also important to us. To achieve our mission, we needed a data-based integrated construction management platform. We saw the potential of the 3DEXPERIENCE platform and decided to use it as a foundation to build our Smart Construction Management Platform.
01:24 – 02:56
Bjun Sungjin, Senior Manager of Plant Construction Management, POSCO A&C:
We now manage every project on the 3DEXPERIENCE platform and ENOVIA’s project management is very intuitive, and the graphical view makes it easy to review projects. We use CATIA to create all 3D models and to integrate the 3D designs of each contributing partner. The platform supports multiple CAD environments, solving past compatibility issues. CATIA is essential for the integrated management of large-scale modeling projects like the Gwangyang Steelworks repair project. The 3D model had more than 3,000 products and more than three million parts and we managed all in a single source of truth. And to review mechanical constraints of construction equipment and site conditions before the actual construction starts, we use DELMIA. For example, we had to install a large duct at our Pohang plant. Our site simulations showed potential danger there was insufficient space and resources to assemble it on site. Instead, we assembled it off-site, and then maneuvered it with a crane, into a position that we’ve found through simulation. Doing this virtually in 3D has helped to enhance worker safety and shorten the construction period by more than 15 days.
02:57 – 03:33
Lim Seokgon:
POSCO A&C plans to expand its B2B and B2C business by leading digital innovation in the construction industry based on the smart CM platform. In addition, we would like to advance even further and establish ourselves as the leading company in construction business by virtually designing in 4D and using advanced Building Information Modeling. To achieve this, Dassault Systèmes will be the most essential partner.
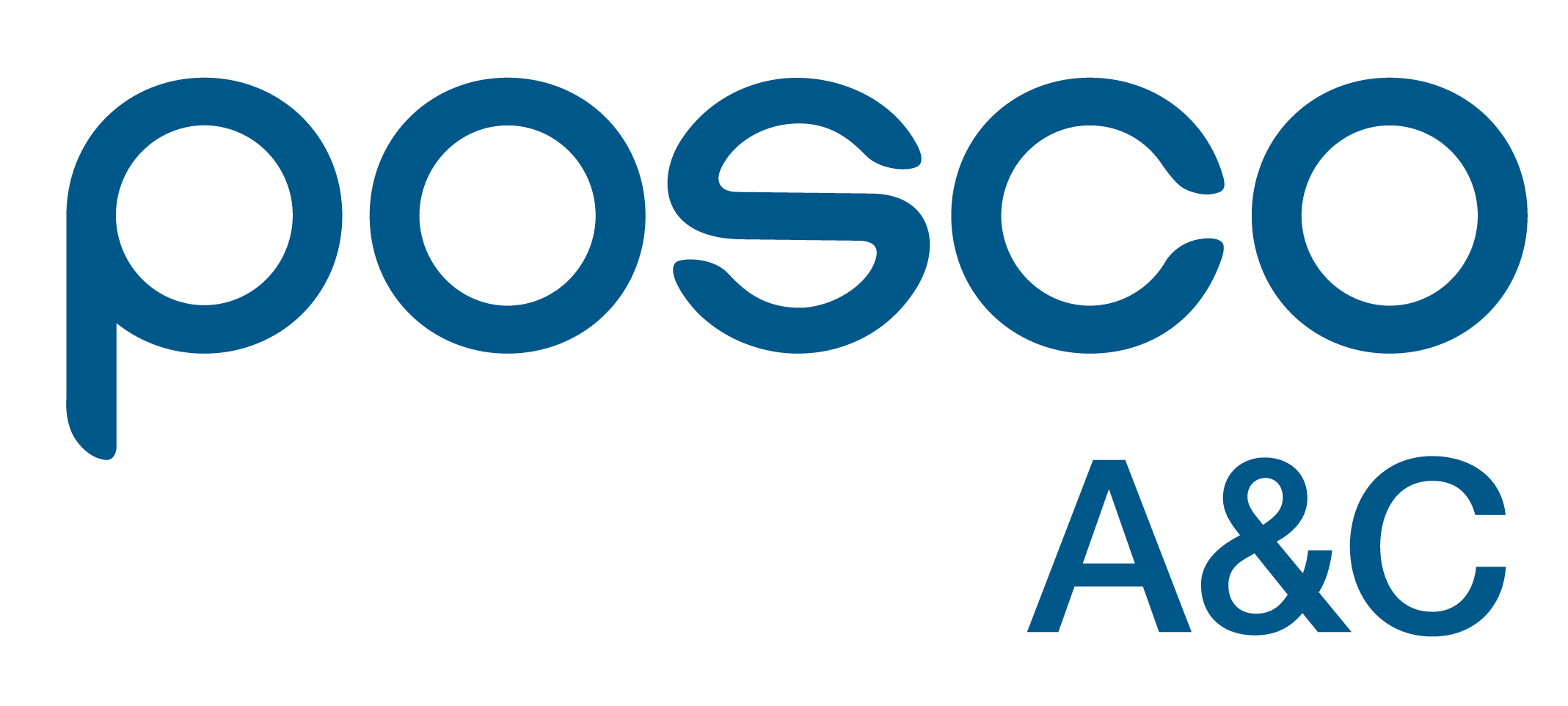
POSCO A&C
POSCO A&C, a division of POSCO Group, is an architectural services company established in 1970 to provide the specialized technologies necessary for the construction of the Pohang Steel Works. The company is equipped to manage a series of architectural processes ranging from planning, design and construction, to supervision and maintenance.
POSCO A&C offers differentiated services including design with technology, architectural construction management, efficient design build and quality improvement. Its Smart CM Platform® is unique in the construction management industry and changes the paradigm of architecture.
For more information: https://www.poscoanc.com/