Plastic Technologies, Inc.
Realistic simulation with Abaqus has enabled PTI to reduce development costs, achieved faster time to market for its customers, and improve design and production troubleshooting and diagnoses.
With PET (polyethylene terephthalate) firmly ensconced as the material of choice for plastic container manufacturers, the focus has shifted to designing lighter-weight versions of current packaging to wring costs out of the equation and quench consumers’ thirst for more sustainable products.
Although PET has been around for more than 40 years, advances in resin technology and conversion equipment have aided manufacturers’ lightweighting efforts as they try to improve their environmental profile. Research conducted in 2010 for the International Bottled Water Association (IBWA) found that the average gram weight of a 16.9 oz. single-serve water bottle had shrunk by 32.5% over the prior eight years1. While the predominant current weight of 500ml PET water bottles in the United States is now as light as 8 grams (g), new launches are trying to squeeze that down even further.
Yet zeroing in on the optimal design that can offset lightweight material composition with a structure that still meets stringent performance requirements is no easy matter. In fact, it’s a delicate balancing act that has sent brand owners, bottle manufacturers, resin and machine manufacturers scrambling to embrace innovative design processes that can help them achieve their goals.
At Plastic Technologies Inc. (PTI), a leader in plastic package design services, the go-to practice is simulation-led design that combines an in-house virtual-prototyping tool with finite element analysis from Dassault Systèmes’ realistic simulation application SIMULIA, a key component of the Perfect Package Industry Solution. Simulation enables the PTI design team to greatly reduce the amount of time and resources.
PTI has a broad swath of clients ranging from consumer product companies to plastic processors and material suppliers. In a typical year, the firm performs as many as 500 unique design developments and an average of five iterations per design for clients, and it recently capped off its 10,000th bottle design since its inception in 1985. PTI employs state-of-the-art CAD tools, including Dassault Systèmes’ CATIA application, in the development of innovative designs for its customers.
Abaqus is often employed in concert with PTI’s proprietary virtual-prototyping software. This is used to simulate the reheating of preforms, replicate the blow molding of containers and predict the material thickness distribution of associated mechanical properties. The data is then used as input for FEA studies that explore the highly nonlinear deformation of different containers under various types of loading conditions.
Abaqus has become an essential part of PTI’s development process, helping designers address mounting workload pressures by more quickly screening designs, identifying the best lightweighting opportunities, optimizing the production process and identifying root-cause failures.
“Our simulation results help in the development process in multiple ways,” says Sumit Mukherjee, Director, CAE & Simulation at Plastic Technologies. “It helps screen the most promising candidates that are then refined further for optimum performance. It lets us provide critical feedback on what geometric features, material properties and thickness distribution will guarantee better performance and possible lightweighting for existing containers, and it encourages more innovative thinking to facilitate creative, viable solutions.”
Adventures in container performance
PTI has two primary objectives when lightweighting container designs for its customers: to achieve materials savings without greatly affecting structural performance and to enhance both container structure and preform designs to improve the efficiency of material distribution so that each grain of material is maximized.
In one study that explored plastic water bottle performance during lightweighting, PTI used Abaqus in simulations of what happens to top-load strength and/or side-wall rigidity under varying pressures to ensure that a lighter plastic water bottle would not buckle under loading or stacking conditions.
Surprisingly, it was revealed that the top-load strength of a plastic bottle drops nearly in half from 19 lbf (pound force) to 12 lbf as the container is light-weighted from 17g to 14g - critical finding that allowed the company to redirect its design efforts quickly.
The simulated data was physically validated by molding samples at both 17g and 14g, and the predictions were within 90% of the actual observed values.
Abaqus was tapped to explore the orientation and wall thickness of the bottle sidewall to identify the optimal preform dimensions that would result in the desired top load. “Abaqus allows us to incorporate the right loads and boundary conditions along with the time scale of the particular applications,” Mukherjee says. “Going forward, the potential for incorporating the structural dynamics with fluid contact interactions [as is typical of all containers encapsulating a fluid product] is perhaps the single most redeeming feature of Abaqus for us.”
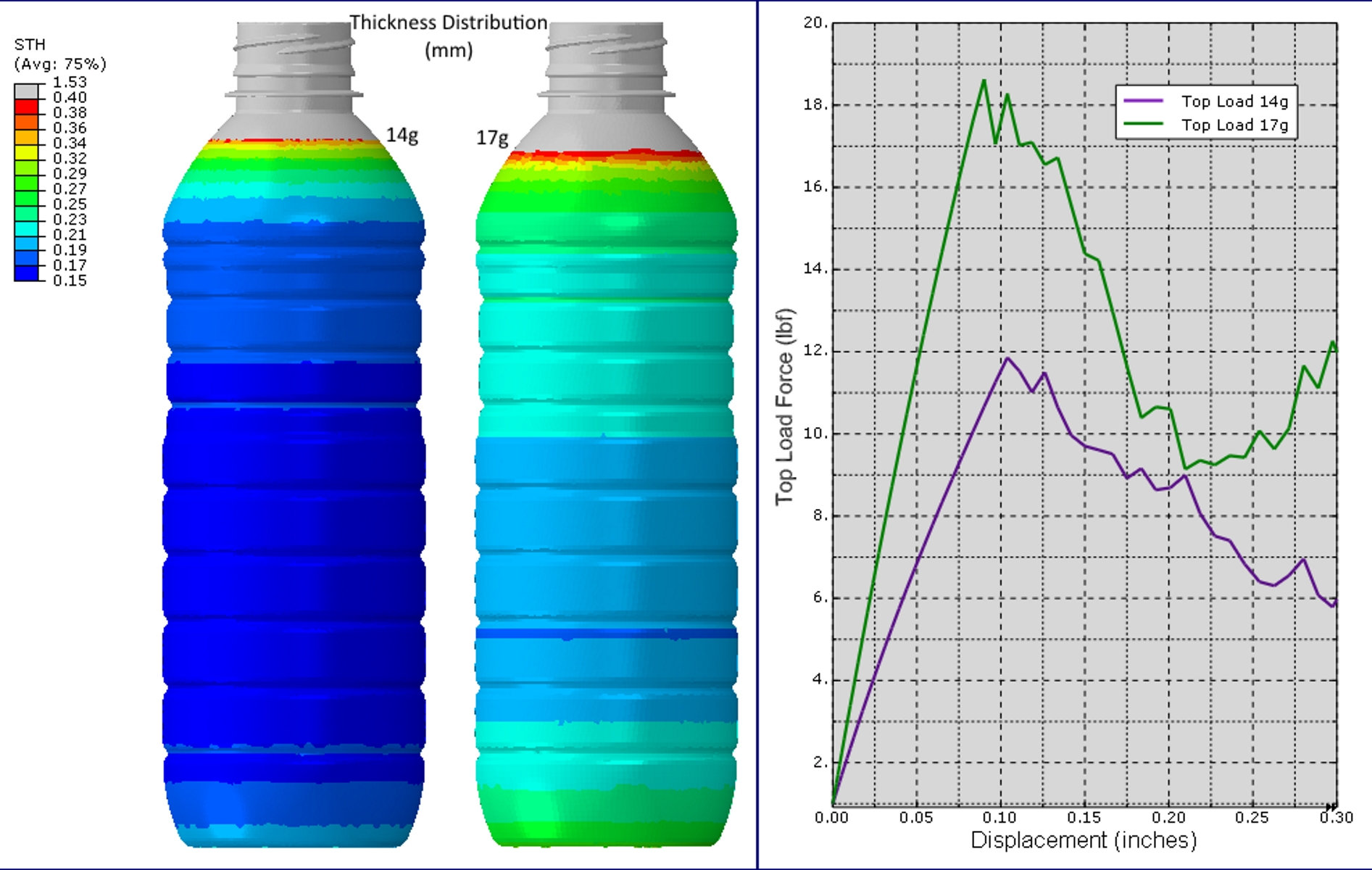
If new package designs can be simulated before any samples are made, bottle and preform design iterations happen more quickly and cheaply, speeding up the entire design chain and resulting in quicker time to market.
Design challenges come in all shapes and sizes
PTI also studied top-load and side-load performance of oval and other non-round containers to determine the different outcomes produced by different preform heating methods during the blow-molding process. In this case, PTI engineers learned that the “preferential heating” method is the preferred option for oval-shaped containers as it resulted in a more uniform weight distribution with better empty and filled topload strength.
“This ability to analyze different container shapes and preform designs in a relatively short time meant a wider variety of design features could be rapidly evaluated while providing a good learning tool for future design recommendations,” Mukherjee says. “This opens the door for evaluating more creative concepts that may fall outside of the scope of the previously prototyped concepts and allows for the development of more robust designs much more rapidly.”
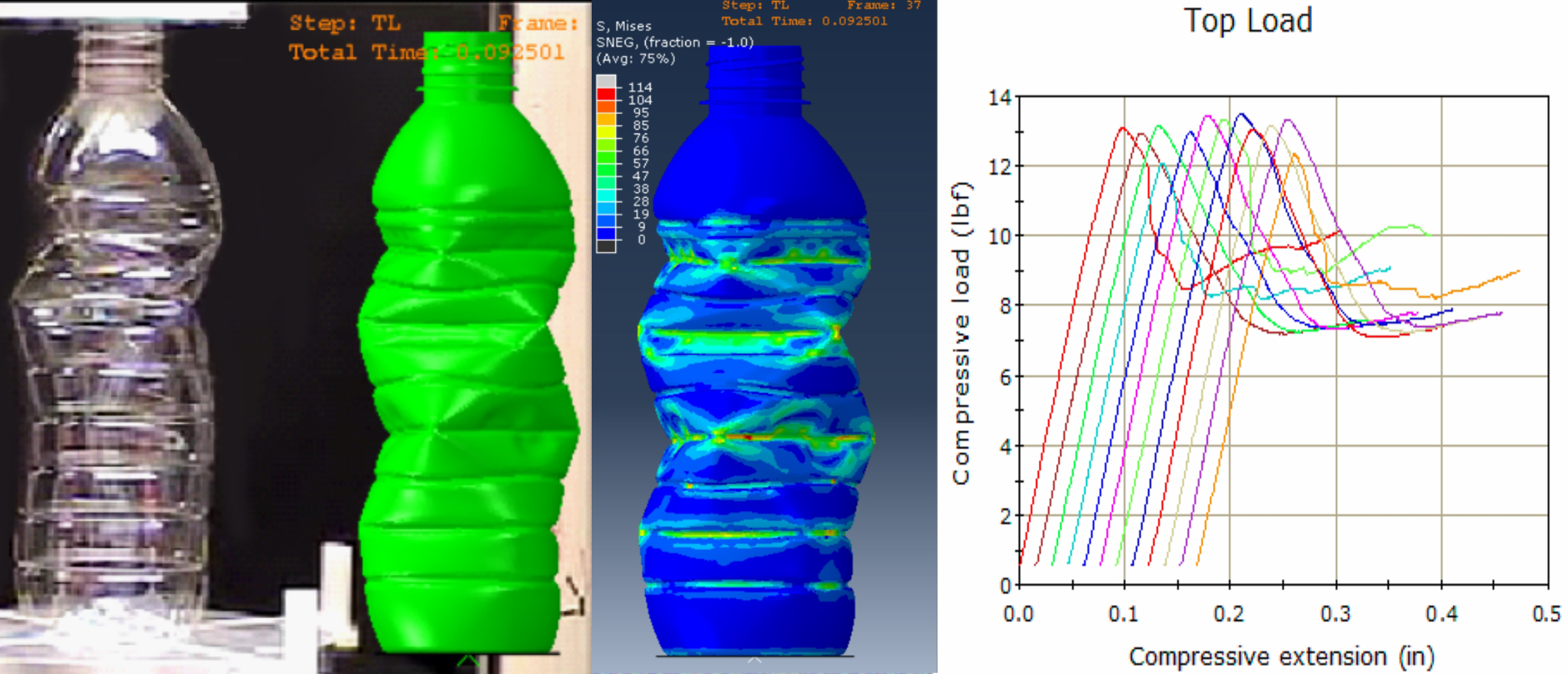
Going beyond lightweighting
Abaqus FEA is not only facilitating PTI’s lightweighting efforts, it also plays a role in other areas of the design-and-build workflow, including optimizing a more complex blow-molding process and aiding in ongoing efforts to identify and fix product failures.
Consider the design and manufacture of wide-mouth PET containers, which are produced via a single-stage blow-molding process as opposed to the conventional two-stage process. The large neck diameter of this class of PET containers requires the single-stage process because the retained heat from injection molding can be harnessed for preform stretching and blow molding. Preform design is particularly critical because there is little room for redistribution of material with this approach. Historically, however, the complexity of the single-stage process has precluded PTI and others from accurately simulating preform design and the actual blow-molding process in a virtual world, continuing a reliance on costly physical prototypes.
Now, building on its success modeling blow-molded wallthickness distribution on round and oval containers, PTI was able to create its first-ever analytical model that addresses these specific challenges, simulating a pure single-stage process on a 116g 3L container that was blow molded without any additional reheat conditioning. By inputting the sidewall thickness and mechanical property outputs from virtual-prototyping software into Abaqus FEA, PTI wanted to predict container top-load resistance, the goal being to zero in on the optimal container size that could hold a kilogram of printer color toner.
PTI’s simulations of this previously hard-to-replicate design and manufacturing process proved to be nearly identical to the results of physical testing. The failure mechanism and deflection at max load were also near mirror images between the simulation and the actual tested bottles. Abaqus’ precise contact algorithms and its ability to efficiently map material properties to individual nodes and elements was instrumental in helping PTI pull off a simulation of this magnitude, Mukherjee says. “We had used other software in the past, but it didn’t meet our needs for large deformation of thin-walled plastic articles with nonlinear material properties.”
Mukherjee notes that having access to all the different solver modules, including structural dynamics and computational fluid dynamics (CFD) in Abaqus, and the option to scale to a higher number of CPUs based on complexity and need, is enabling the team to tackle a wider variety of challenging problems.
Getting to the root of product failures
As packaging becomes an integral part of a company’s brand appeal, new containers are testing current processes and domain expertise, introducing novel challenges in the way of package failures. Yet since quality standards vary from one producer to another, there is no absolute guidance on what constitutes failure.
PTI decided to further evolve its simulation efforts to tackle root-cause failure analysis and, ultimately, improve its quality efforts. Armed with its own virtual-prototyping software tools along with FEA software and M-Rule® models, PTI was able to zero-in on reoccurring failures and resolve them in a fraction of the time and with far fewer resources than were previously required using standard prototype-and-test methods.
In one exercise, engineers tested their new failure-analysis process on a 64-ounce hot-fill juice container, which exhibited bulging in the area of the logo panel on sporadic numbers after being filled. Tracking the errors through the system, PTI determined that the failure sample was being generated during the filling process. Further analysis revealed that material distribution inconsistencies were not the cause of failure, prompting PTI to turn its attention to possible external influences. A thesis emerged that high product temperature coupled with filler pressure spikes was the impetus for the panel failure.
In order for simulation to serve as an effective replacement for the traditional root-cause failure inspection process, PTI had to conduct modeling efforts on a grand scale. The model’s build began with the replication of the material distribution and mechanical properties, but also included reproducing the blow-molding process in a virtual world as well as the physical aspects of the environment, including conveyors and filling heads. Once the information input was complete, PTI conducted numerous simulations to realistically replicate the failure mechanism. With those validated, the team could then use the model as a baseline to compare design iterations that addressed the failure.
As a result of its efforts, PTI was able to rule out heavyweighting the juice container design to a 75g version to address the deformation problem and instead concluded that a geometric modification to redesign the logo panel was the optimal resolution to the problem. This very process of continually modifying designs to eliminate failure is exactly where simulation can save time and money.
“If new package designs can be simulated before any samples are made, bottle and preform design iterations happen more quickly and cheaply, speeding up the entire design chain and resulting in quicker time to market,” says Mukherjee. “A wide variety of design features can be rapidly evaluated, providing a good learning tool for future design recommendations. This opens the door for evaluating more creative concepts that may fall outside the scope of the previously prototyped concepts and allows the development of more robust designs much more rapidly.”