Peugeot Sport
Building the new PEUGEOT 9X8 Hybrid Hypercar from scratch, Peugeot Sport adopted the 3DEXPERIENCE platform on the cloud with SIMULIA PowerFLOW to gain aerodynamic performance while saving significant time, money and resources in the process. Partnering with Dassault Systèmes, the company used the Sustainable Multi-functional Vehicle industry solution experience through a Virtual Twin as a Service approach.
(Photo © Peugeot Sport)
Pushing creative limits in Peugeot 9X8 hypercar
When it comes to racing hypercars, speed and aerodynamics go hand in hand. The more aerodynamic the car, the faster it goes. And on the straights of the 24 Hours of Le Mans circuit in France, drivers in the 2023 top-class hypercar field clocked well over 330km per hour. Among the contenders battling for the podium was Peugeot Sport, which made its long-awaited return to Le Mans with the PEUGEOT 9X8 Hybrid Hypercar. Turning heads on and off the track with its striking design, the 9X8 combines innovative aerodynamics and styling to give the car its unique, sleek silhouette.
In many ways, the 9X8 represents what’s possible when you combine creative freedom and advanced technology. New regulations allowed Peugeot Sport’s engineers to think outside of the box when it came to achieving the hypercar’s specified performance levels, allowing them to focus on smart aerodynamics on the car. Critically, they were able to test and verify every aspect of their bold concept in the virtual world first, saving significant time, money and resources. Before so much as a single component of the car was physically made, the 9X8 existed in the 3DEXPERIENCE® platform’s virtual environment, where engineers harnessed its sophisticated design and computational fluid dynamics (CFD) simulation capabilities to fine-tune their ideas and define the car’s major characteristics.
“Typically, when you design a race car, there is no compromise between performance and style,” said Olivier Jansonnie, technical director at Peugeot Sport. “The new Le Mans Hypercar (LMH) regulations limit performance, so once we met those targets, we were freed up to focus on aesthetics, resulting in a distinctive and beautiful race car. The 9X8 is a careful balance between engineering and design, creativity and technical know-how, largely due to the power and flexibility of the 3DEXPERIENCE platform. A digital-first approach allowed us to adopt an entirely new mindset and create something we’ve never done before.”
00:07 - 00:15
Nico Muller, Pilot, Team TotalEnergies:
I always feel privileged to drive cars like the 9X8 with the atmosphere, the spectators around the circuit, it's amazing.
00:18 - 00:25
Olivier Jansonnie, Technical Director, Peugeot Sport:
We have cars that reach maximum speeds of around 340 km/h. So in this type of vehicle, the role of aerodynamics is very important.
00:26 - 00:34
Yann Le Fur, Head of Design Office, Peugeot Sport:
The SIMULIA cloud on the 3DEXPERIENCE platform has been essential for us. It allows us to work much faster and also motivates the teams.
00:42 - 01:05
Olivier Jansonnie, Technical Director, Peugeot Sport:
The 9X8 is PEUGEOT's Hypercar that complies with the FIA Hypercar regulations currently in place in the World Endurance Championship. This regulation is quite innovative. It gives what we call a performance window - the minimum and maximum level of aerodynamic performance. At the end, cars are evaluated in the same wind tunnel. It's extremely expensive, so we try to prepare all of the work ahead of time using digital simulation which is cheaper and more flexible.
01:08 - 01:23
Thomas Orlier, Mechanical Designer, Peugeot Sport:
The major challenges in the 9X8 design are mainly linked to the discipline itself. These vehicles go at extreme speeds. Also, the schedule is relatively tight since we have to respect the championship timing.
01:24 - 01:37
Olivier Jansonnie, Technical Director, Peugeot Sport:
We use CATIA for the mechanical and surface design. We also use [SIMULIA] Simpack for digital simulation, which is very important for us. And then, on this project, particularly for the aerodynamic aspect, we use 3DEXPERIENCE with [SIMULIA] PowerFLOW on the cloud.
01:39 - 01:54
Yann Le Fur, Head of Design Office, Peugeot Sport:
We use Dassault Systèmes solutions every day. We create the virtual vehicle with it, and all the workshops can access this model. It enables us to work on the same data without duplication and reduces the risk of error. This is the key to success for us.
01:55 - 02:13
Nico Muller, Pilot, Team TotalEnergies:
Aerodynamics greatly affects the car's behavior. The correlation between simulations from the engineers and what we feel on the track is really very good. If an engineer says: "OK, this is the window where the car is most efficient," then it's really the case in reality.
02:13 - 02:26
Olivier Jansonnie, Technical Director, Peugeot Sport:
When the car is high, when it's low, when it pitches forward or backward, when it rolls in corners, the aerodynamic parameters change. We model that and we get to see which areas of the car are working well, which ones are not, and we can see defects, and that automatically generates ideas.
02:26 - 02:37
Yann Le Fur, Head of Design Office, Peugeot Sport:
Another advantage of [SIMULIA] PowerFLOW for CFD is to be able to run CFD simulations several times a day. So we have a constant evolution of the shape. CFD also allows us to stabilize the models.
02:38 - 02:53
Olivier Jansonnie, Technical Director, Peugeot Sport:
The partnership with Dassault Systèmes ultimately allowed us to quickly start a project from scratch without having to go through an entire learning phase. We had powerful tools that we already knew. In conclusion, we managed to achieve technical excellence while meeting deadlines, keeping our schedule, and lowering our costs.
New racing regulations spur digital-led design
The 9X8 adheres to the latest LMH rulebook, which welcomes design and technical diversity while leveling the playing field and keeping costs in check through performance windows. Controlling performance outcomes rather than setting rigid design and aerodynamic constraints gave Peugeot Sport the opportunity to be more liberal in its creative process.
“We quickly realized that reaching the level of performance wasn’t such a big challenge, and it opened up a new way of working,” Jansonnie said. “Our aspiration is to promote electric mobility and technology with the 9X8, and ensure the car fully represents the PEUGEOT brand.”
To meet the specified LMH performance windows, every competing hypercar also had to be tested and approved (homologated) in the same wind tunnel facility in Switzerland. It meant that Peugeot Sport needed to develop more of the car virtually, using CAD and simulation tools rather than relying on physical testing.
“It was very clear that developing small-scale physical prototypes and going into the wind tunnel was not the right solution for us,” Jansonnie said. “We decided to go for a digital approach that was much more flexible and allowed for broader changes on the car. This was a key driver for partnering with Dassault Systèmes and embracing the latest simulation capabilities of SIMULIA on the 3DEXPERIENCE platform. We needed to speed up our development process and run advanced aerodynamics simulations so we could explore more design options.”
Time in the wind tunnel is expensive. In a well-organized session, we’d plan to test three underfloors, which we’d have to design and build, taking around three months in total. Using SIMULIA on 3DEXPERIENCE through the Virtual Twin as a Service, we can do the same types of analysis in a single day. It’s a huge time and cost saving.
Teaming up with simulation experts
PEUGEOT is no stranger to Dassault Systèmes solutions. The company is a long-term user of its CATIA design application for the development of all cars across the group. It also has previous experience working with SIMULIA PowerFLOW technology for CFD and SIMULIA Simpack for multibody simulation. However, with only a matter of months to develop the ultimate endurance racer, Peugeot Sport needed advanced aerodynamics expertise.
“We were convinced by the capabilities of SIMULIA and knew it would be the best solution to develop the aerodynamics of the car,” Jansonnie said. “However, it had been eight years since we’d last done endurance racing, so we were starting completely afresh and we had no time to assemble and skill up a new aero team. Dassault Systèmes brought us the expertise we needed with a Virtual Twin as a Service approach.”
This is a true partnership. Dassault Systèmes’ simulation experts are very much part of the PEUGEOT design team and are directly involved in the daily development of the 9X8. Bringing their experience and expertise to the table, they helped to guide the car’s aerodynamic design, set the wind tunnel sessions and define the car’s future development plan.
“SIMULIA technology is extremely performant, but the methodologies and people using the app are just as important,” Jansonnie said. “You can waste a lot of time if you don’t know how to use it properly. With Dassault Systèmes’ support, from the first day of the project, we could start extracting results from the simulations.”
Both parties constantly share data and feedback with each other through the 3DEXPERIENCE platform on the cloud. For a racing team traveling a great deal, secure cloud-based access to data on the go has proven critical.
“The interface is easy to use and understand, so we can scan through the simulation results and access the information we need,” Jansonnie said. “It’s very convenient to access any results directly in the cloud and have remote meetings. It’s also important to note that the project launch coincided with the COVID-19 pandemic, so we started everything virtually. It was a big test for the system.”
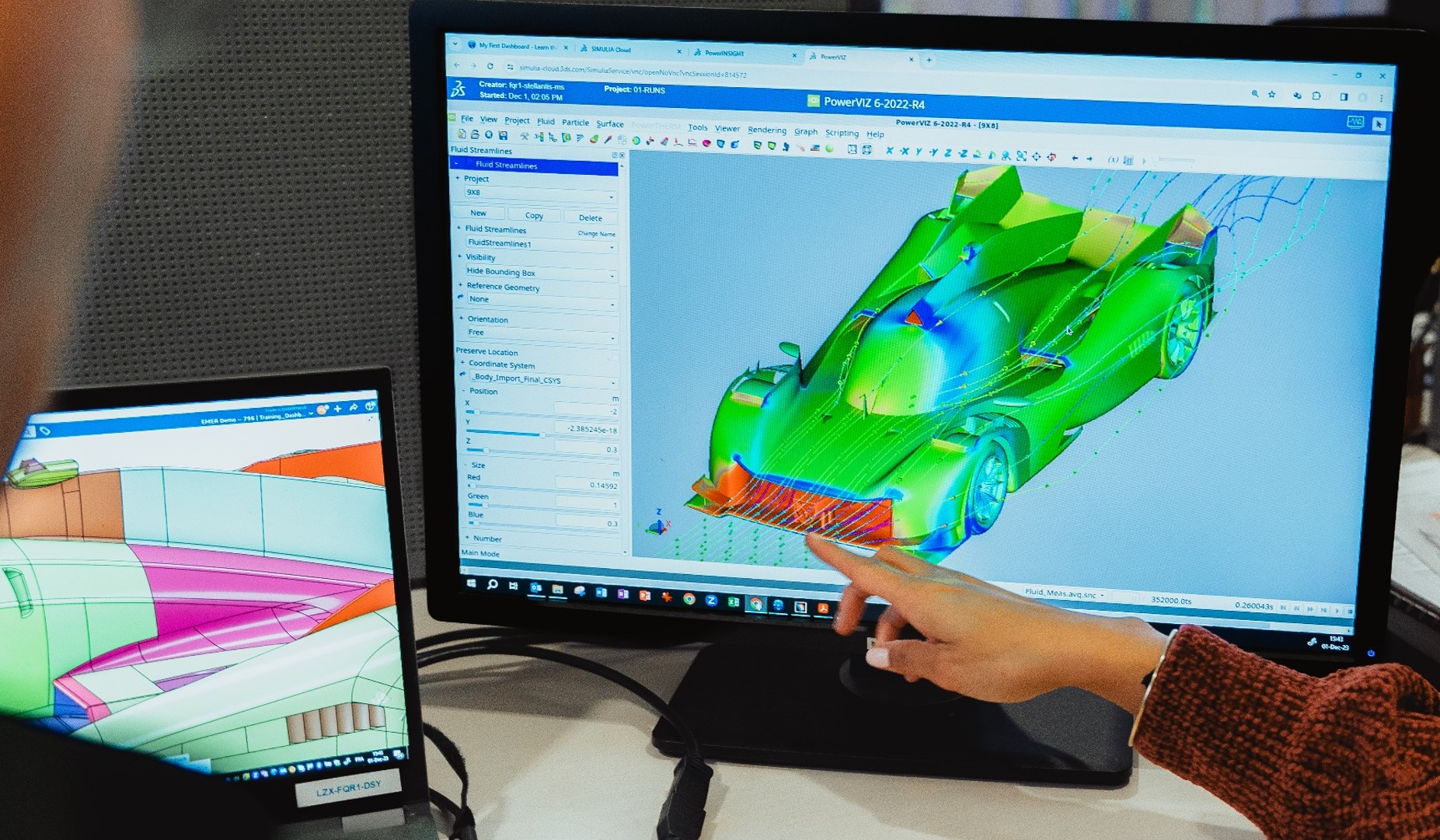
Validating aerodynamic performance through simulation
Unlike previous regulations which limited what competitors could do with the car’s aerodynamics, the new LMH rules gave Peugeot Sport the opportunity to focus more on the car’s underfloor. With this setup, air travels through tunnels and is squeezed at the point closest to the ground to generate downforce. A certain level of downforce must be reached to be in the performance window and the rear wing usually helps with that.
To balance the car aerodynamically, the rules permit the use of a single adjustable aerodynamic device (AAD), fitted to either the front or the rear. However, there are a huge number of variants in between.
“Through simulation, we could evaluate an unlimited number of options for the AAD system,” Jansonnie said. “A digital approach meant we could try out very diverse concepts and have answers in a matter of days or weeks. For example, the car’s front splitter can vary in height and shape. Designing, building and testing multiple physical front splitters is too costly, but totally possible in the virtual world.”
Peugeot Sport and Dassault Systèmes have now run over 3,000 CFD simulations using SIMULIA PowerFLOW to develop and refine the 9X8. Building prototypes and testing them in the wind tunnel usually takes a vast amount of time and resources. Peugeot Sport found the digital approach faster and more cost effective.
“Time in the wind tunnel is expensive,” Jansonnie said. “In a very well-organized session, we’d plan to test three underfloors, which we’d have to design and build, taking around three months in total. Using SIMULIA and the Virtual Twin as a Service, we can do the same types of analysis in a single day. It’s a huge time and cost saving. When we go to the wind tunnel, we can use the digital simulation results to understand the physics behind what’s happening in real life.”
“We can constantly test and evolve the shape in a way that wouldn’t be possible if we relied on the wind tunnel alone,” added Yann Le Fur, head of the design office at Peugeot Sport. “The CFD simulations also allow us to stabilize models and be really consistent; we can test them in a uniform way.”
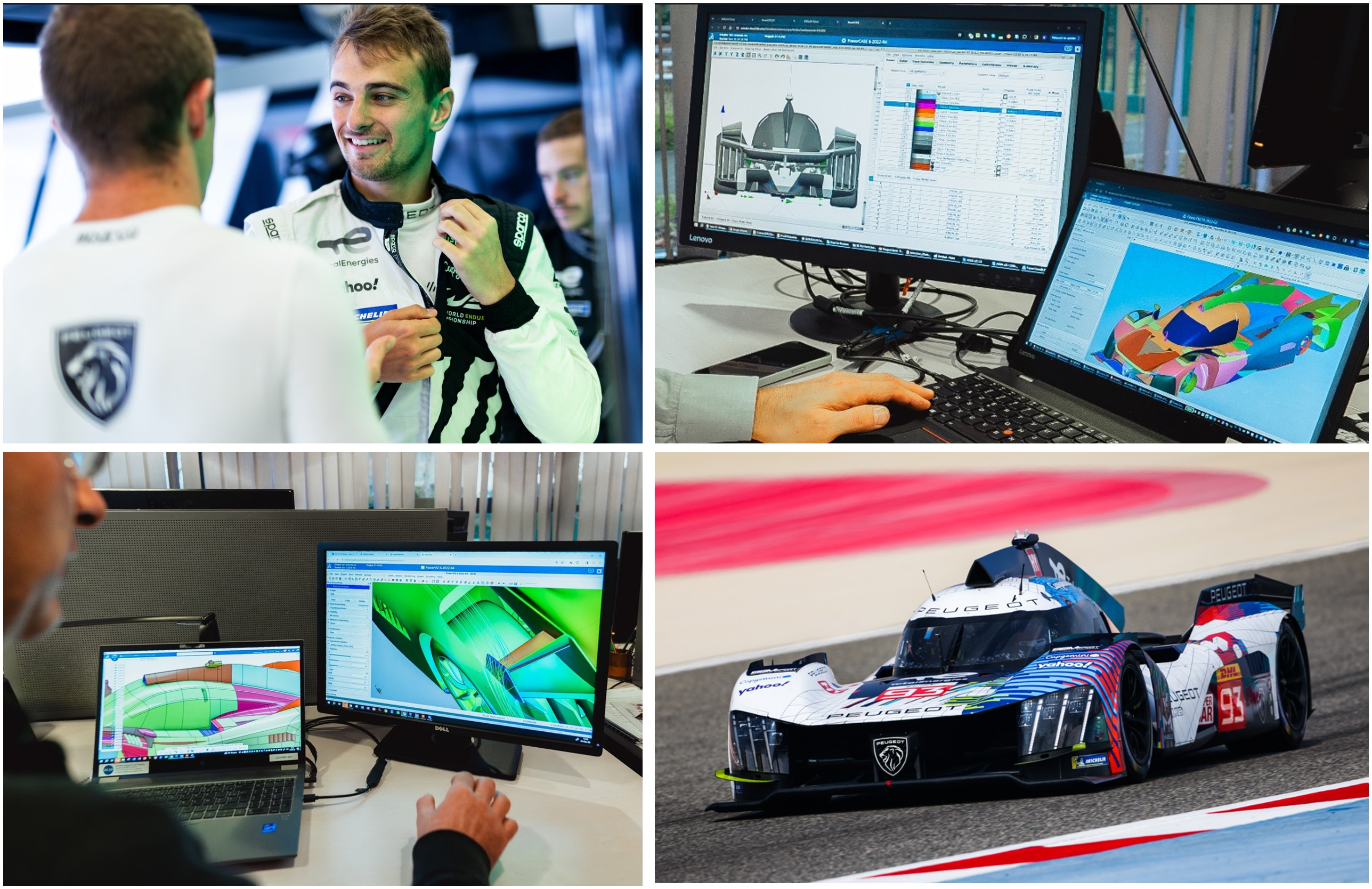
Continuous feedback loop
Because of the seamless connectivity between CATIA and SIMULIA in the 3DEXPERIENCE platform, the team was able to easily act on simulation results and reflect them back into the design of the car – an approach widely referred to in the industry as MODSIM (modeling and simulation).
“We design with CATIA, generate the surfaces, mesh the model, run the simulation and then bring those results directly back into the design environment,” Jansonnie said. “Within the context of the full structure, we can see which parts are working properly according to the flow. It’s much smoother to exchange ideas.”
Having different design disciplines, such as surface and mechanical design, linked within CATIA supports this iterative process. Working with such high performance materials is a careful balancing act of making sure they’re structurally robust while being as light as possible.
“We’re led by aerodynamics in terms of surface design, and then we have to translate that into feasible mechanical parts, considering their thickness and ability to withstand aerodynamic loads,” said Thomas Orlier, mechanical designer at Peugeot Sport. “Having the entire car represented in a digital model helps us make those informed decisions and be as efficient as possible.”
Everyone involved in the project, including those in the workshop, have the opportunity to view the latest 3D model of the car and give their opinion.
“We want everyone to feel invested in the design of the car, so to be able to consider their ideas and comments is really important,” Le Fur said. “It helps different teams understand how we arrived at certain design decisions and why.”
This continuous engineering loop is also critical for incorporating driver feedback, particularly when it comes to the car’s aerodynamic balance. Engineers must take into account individual driving preferences and find the optimal set up.
“If we have a good balance between the front and rear of the car, it’s much more pleasant to drive,” said Nico Müller, driver at Team Peugeot TotalEnergies. “If we are 2% to 3% too far forward, the car becomes difficult to drive. Too far back and there’s too much understeer. The correlation between the simulations that the engineers use and what we feel on the track is very good. If an engineer says, ‘This is the window where we think the car performs the best,’ that’s the case in reality as well.”
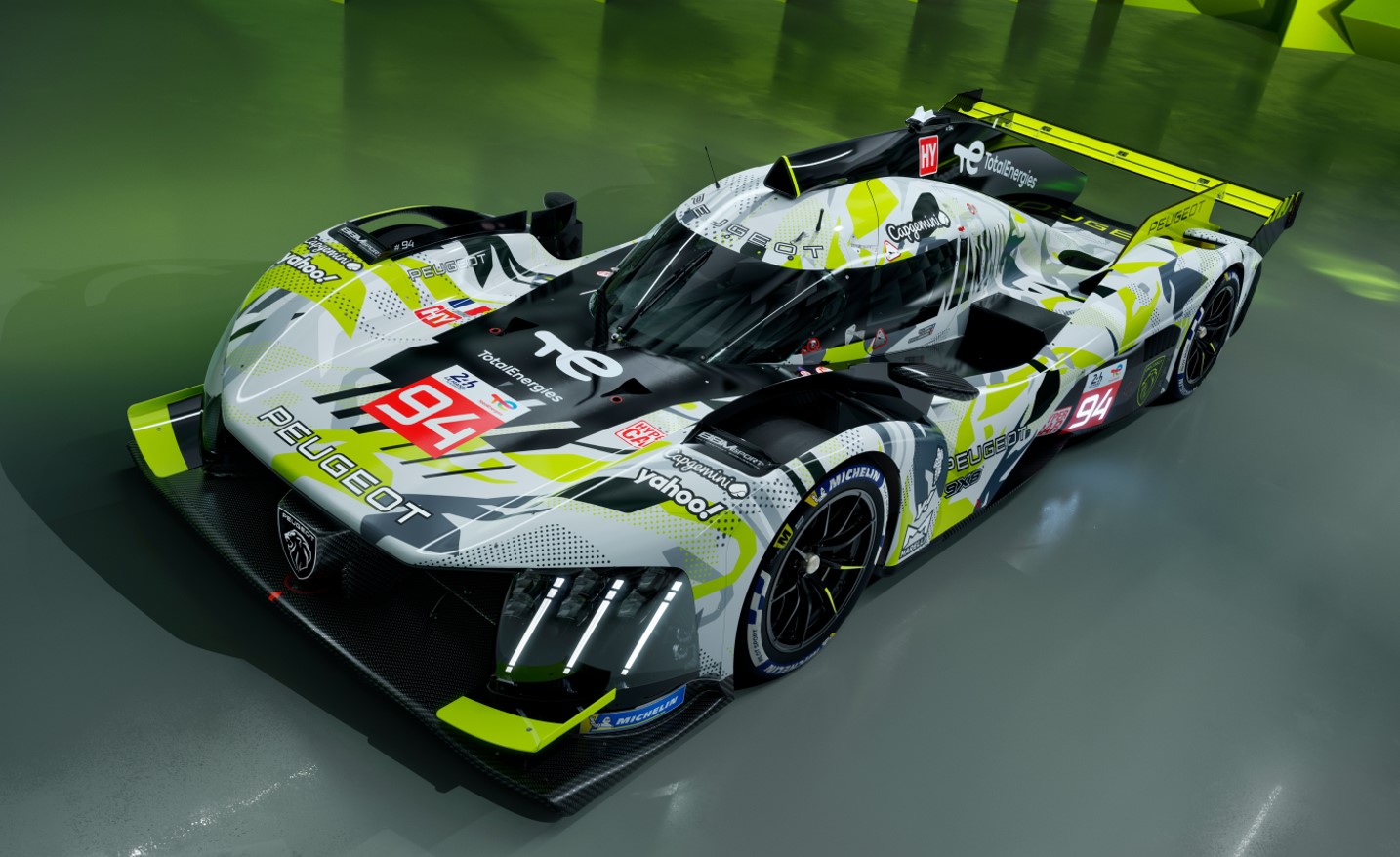
Virtual Twin supports ongoing development
Thanks to the high caliber of its simulation results, Peugeot Sport could accurately test the interaction between different components and systems in the car and be sure of its theoretical performance before physical testing. This virtual representation of the car – known as a virtual twin – served as the basis for creating the first physical full-scale model for testing in the wind tunnel. Now, the 9X8 is clocking miles on the racetrack and feeding back data to the same virtual twin to further enhance performance and guide future development.
“Work is underway on the second generation of the car for 2024, including a new aero kit,” Jansonnie concluded. “We know from experience that aerodynamic development never really stops, so it makes absolute sense to continue with the same people and tools. We really rate SIMULIA and the 3DEXPERIENCE platform’s high performance and flexibility. Within a few weeks, we were fully up and running with the simulations. It was the only way to get this project going quickly. Without this technology and the talented people behind them, the 9X8 wouldn’t have been possible.”
Discover more about the Sustainable Multi-functional Vehicle industry solution experience.
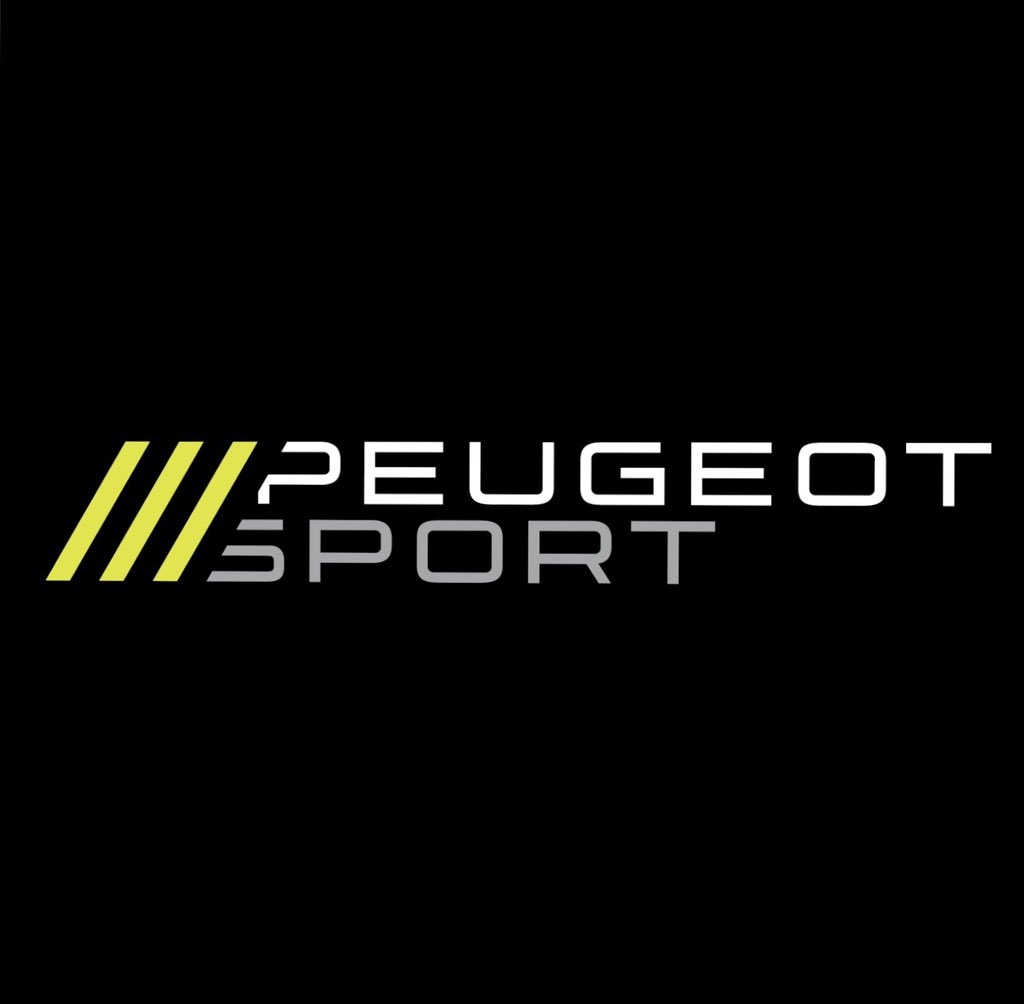
Focus on Peugeot Sport
Founded in 1981, Peugeot Sport is the competition department of the French car manufacturer PEUGEOT. Based in Satory, Versailles, the Peugeot Sport department handles the design and manufacturing of racing cars under the Peugeot Sport Engineered line, which is supported by the new World Endurance Championship (WEC) program. Pushing the limits of innovation, the company has been perfecting its mastery of hybrid-electric technology in competition and on the road for more than 10 years, combining aesthetics and high performance with low emissions.
For more information: https://peugeot-sport.com