Nyrstar
Solving a metals and mining puzzle in seven countries.
The Customer
Nyrstar is a global multi-metals business, with a market leading position in zinc and lead. It has growing positions in other base and precious metals, which are essential resources that fuel rapid urbanization and industrialization, and its mining and smelting operations are located in Europe, North America and Australia.
The Challenge
Nyrstar, which previously concentrated its operations in Europe, began to experience a steep increase in operational complexity when it acquired mines in North and South America – and hence a large change in feed mix. The different production sites owned by Nyrstar have different characteristics, which make some sites better at, or even uniquely capable of, extracting certain metals from the input materials. Across these production sites, the unique complexities of each location involved many feedback loops and multi-period time optimization requirements to run efficiently.
Then, one of Nyrstar’s major suppliers in Australia was about to be depleted. Instead of getting its raw materials from one supplier, it now had to contend with sourcing materials from many smaller mines. This already complex operation was further exacerbated by the vastly different time zones Nyrstar’s operations are located in, which spanned from Australia to the western coast of Canada. These complexities presented a serious computational challenge.
Furthermore, its key metal, zinc, underwent volatile price swings that made planning an uncertain endeavor. This situation added more demands to the already variable nature of the business.
All of these challenges were handled by a spreadsheet system coupled with an optimizer model, but it proved too much to bear for the system.
First, the spreadsheet system was good enough when Nyrstar was still mostly supplied from a single big mine. However, when that mine was depleted and supplies were being delivered from many smaller mines, the puzzle size increased drastically and surpassed the capabilities of the system.
Second, the system could only handle single-period optimization, where the consumption for one full year was optimized and then disaggregated evenly over twelve months. As aforementioned, the business of Nyrstar is variable by nature, and thus a single-period plan was insufficient for the company. Over time, different production mixes which should have been run were not, and the system could not capture this. As a result, there were many deviations in the plan that created a loss in value to the tune of millions of Euro annually.
Third, there was a lack of visibility of information across different planning teams as the many spreadsheets in the system did not contain accurate and up-to-date information.
The Choice
Nyrstar needed a better solution than a spreadsheet system. It needed a solution that was very agile, efficient and, in this particular case, had to fulfil a payback period of three months. Nyrstar’s search for an answer saw it shortlist of potential vendors across the globe. It kept a stringent list of requirements for things that needed urgent attention:
- Vast improvements to computing power were needed to run various scenarios quickly, especially in case of sudden supply disruptions, and this was something that exceeded their present capabilities.
- Nyrstar needed a solution that would be able to accommodate the SAP integration. An integration with SAP was critical to maintain a consistent, single authoritative source of information that would be used throughout its operations as well as be included the value-in-use decisions in the future. It would also improve treasury’s forecasting ability for inbound materials.
- Nyrstar needed proven technology, which was critical to avoid lengthy learning periods. The business case focused at first on early avoiding incorrect allocations and unnecessary spot purchases that were traced back to the use of spreadsheets instead of a more robust system.
In the end, DELMIA Quintiq edged out the competition as other solutions were not proven technology or were too complex. Instead, DELMIA Quintiq provided the ability to handle complex calculations quickly, was proven technology in various industries the world over, and was cost-effective for the task at hand.
The task at hand was elaborate, as it involved the buying of raw materials at the mines, selecting the best input mix at all production facilities and deciding where to further treat intermediate products or to sell them. It also had to take into consideration the complex feedback loops and multi-period time optimizations involving different production sites.
DELMIA Quintiq presented itself as the top choice for Nyrstar as it had proven technology and the experience providing solutions to industries that operate internationally. Moreover, DELMIA Quintiq was able to solve Nyrstar’s enterprise resource planning (ERP) deficiencies by immediately and seamlessly integrating its solution with Nyrstar’s choice ERP, SAP.
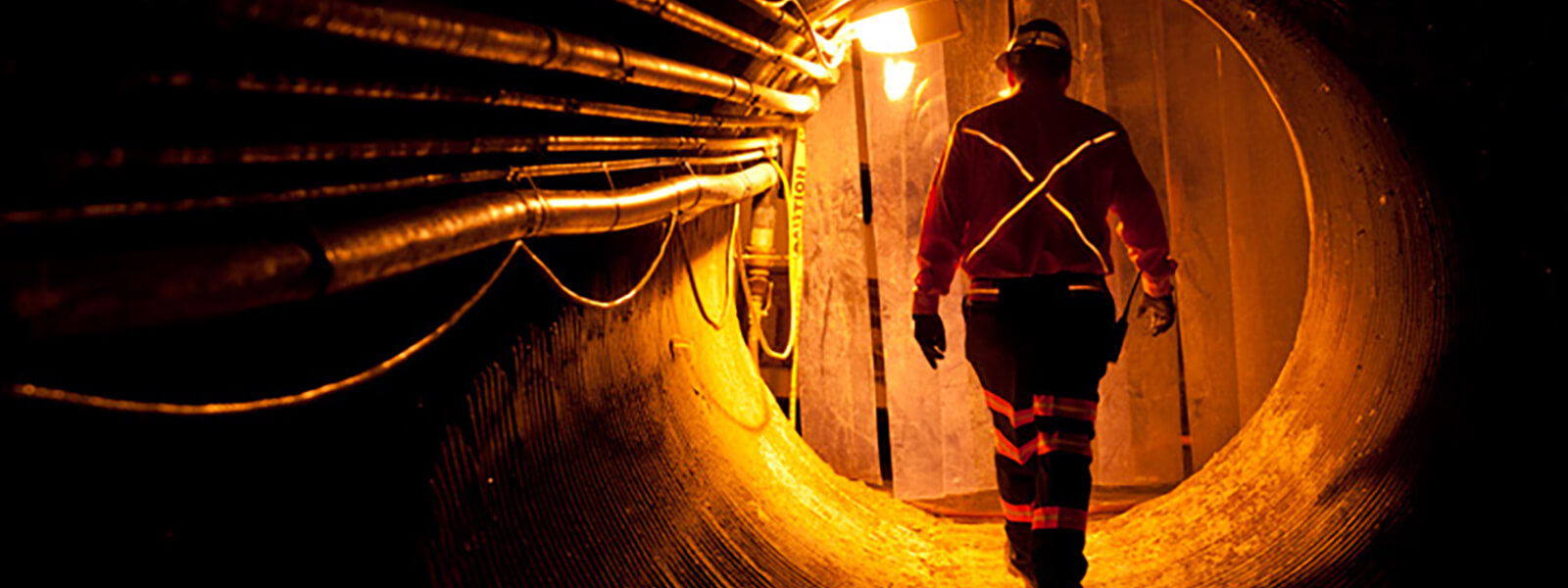
Implementation
The DELMIA Quintiq implementation team recognized the problems it had to solve and decided early on to split implementation of the overall solution into two phases.
Both phases were aimed at maximizing margins by optimizing the availability and cost price of input materials, production site constraints, costs of transportation and the value of the output products with the ability to take estimates of the fluctuating metal prices into account.
The Phase 1 model is used by Nyrstar to plan the actual movement of material, either between multiple mines who supply Nyrstar and the many production sites, or internal flows between these production sites.
The Phase 2 model saw the rolling out of a consumption plan that defines the inputs required at the different production sites. The blending optimizer finds the best mix of input materials for each production site, including the decision on quantity of raw material to purchase, and where to further treat it.
The first site to start using DELMIA Quintiq was the Nyrstar Headquarters in Zürich, Switzerland, where high-level planning decisions that affect the purchasing and material divisions of the company’s various production sites throughout the world.
Nyrstar is currently in the process of rolling out the DELMIA Quintiq application to the other production sites, where the system will also be used to plan day-to-day operations. It will then be used in Europe (three sites), the United States (one site) and Australia (two sites).
The Results
The availability and visibility of planning data was a main concern, which was addressed by the DELMIA Quintiq implementation. DELMIA Quintiq provided a faster and more accurate optimization due to the multi-period optimization, and taking a greater level of detail into account.
Planning discussions are now much easier, since all planners have access to the same input data. As a result, errors had completely disappeared overnight; what was once the daunting prospect of losing millions of Euros annually due to errors was now no longer a concern.
Integration with the SAP system brought certainty and transparency to the company’s operations. Developments and issues along the supply chain could now be picked up and dealt with instantly. What’s more, the sharp increase in computing power afforded by the DELMIA Quintiq solution greatly sped up scenario projections on disruptions; where it once took two days to compute such scenarios, it now only took a couple of hours.
Nyrstar was also able to realize various soft benefits from the implementation. Transparency was added to the flow of high-quality, accurate and fast data and it brought alignment between the commercial and operations teams in Nyrstar. Less time was spent on requesting for more and better data, and the ability of poor data to disrupt the trust and confidence of teams to work together simply disappeared.
In fact, where planners once spent 30 percent of the time planning and 70 percent of the time gathering data, they could now spend 80 percent of the time planning and 20 percent of the time gathering data.
Nyrstar’s treasury management was positively impacted by the implementation and it was able to reap several working capital benefits as a result. The data provided by DELMIA Quintiq’s solutions gave it better control of variable costs as well as its inbound supply chains. Not only was there more data, the quality was also higher, giving the company the ability to well-manage inbound supply chains towards profitability. Also, where once treasury could only forecast its cash flow for the next five to six days, it could now extend that to over six months.
In all, DELMIA Quintiq became a large enabler of Nyrstar’s supply chain improvements. It has also gained the confidence to pursue strategic plans in the future.
Nyrstar Fast Facts
Business: Integrated mining and metals
Headquarters: Zürich, Switzerland
Presence: Seven countries in Europe, Australia and North America (France, Belgium, the Netherlands, Norway, Australia, USA and Canada)
Size: 4,100 employees
Revenue: €3.53 billion (2017)
For more information: https://www.nyrstar.com/