Neta Auto
As Chinese electric vehicle brand Neta Auto focuses on its rapid global expansion, its strategy of developing affordable luxury electric cars requires a keen focus on costs and productivity throughout product development. Neta Auto uses the 3DEXPERIENCE platform to manage all design, engineering, and manufacturing processes, bringing significant cost savings and reducing the product development cycle.
With the ability to spot design and system integration errors by using simulation at the prototype stage, Neta Auto has achieved
fewer issues
cost savings in R&D
Luxury electric car designed to be affordable
The Neta GT electric coupe has all the hallmarks of a premium sports car except for its price tag. Its maker, Neta Auto, retails the luxury electric car at around half the price of similar vehicles on the market today. Much like the rest of its electric vehicle (EV) portfolio – the Neta U and Neta V SUVs, and the Neta S sedan – the Hozon-owned Chinese manufacturer set out to create a sports car that’s both appealing and affordable without compromising on the interior or on safety.
Inside, Neta Auto’s EVs are packed with innovative smart cockpit technology, including the latest navigation, automatic parking and power energy management capabilities, to deliver a comfortable and safe driving experience.
“We want everyone to enjoy a premium driving experience while helping to make our planet a better place,” said Zhang Yong, CEO of Neta Auto. “We have successfully developed a RMB200,000 EV [equivalent to €25,000] that competes with cars costing more than double the price while offering superior performance, safety, quietness, comfort, and intelligence.”
Balancing innovation and cost
Neta Auto has moved fast to grow its EV market share, launching four models in quick succession and rapidly ramping up production. To master the innate complexity that comes with developing multiple high-tech vehicles while keeping costs in check, the company has invested in the latest digital capabilities to streamline its product development. Today, Neta manages its global design, engineering and manufacturing processes on the 3DEXPERIENCE platform.
“We are making forward-looking investments in our technology and products,” Zhang said. “Our plan is to design new electrification products, including fast-charging technologies, high-efficiency motors and new EV models two to three years in advance of when they’ll come onto the market so we’re always ahead of consumer trends. The 3DEXPERIENCE platform helps to shorten our research and development (R&D) time and substantially reduce costs; it is a very efficient tool.”
We’re using the platform to construct a multi-configuration, multi-stage, module-level DMU, which helps to improve the quality of the first engineering prototype. The reduction in management costs by integrating the design structure and engineering bill of materials (BOM) through ENOVIA is evident, resulting in a clearer engineering perspective.
Accelerating product development
One of Neta Auto’s key objectives for moving to the 3DEXPERIENCE platform was to speed up its product development cycles. The company’s previous product lifecycle management system was unable to keep up with its rapidly growing organization and product portfolio. Every new EV Neta builds adds a layer of complexity to the company’s value chain, creating the need for more transparent data sharing and communication, both internally and with suppliers.
“We face new challenges in styling design, engineering development and product production, including communication and collaboration with suppliers,” said Dai Dali, CTO of Neta Auto. “To become more efficient, we needed to accurately transmit data and share information in real time. By creating an environment for synchronous design, development and verification, we can shorten the R&D cycle from eight to six months and accelerate our product launches.”
Because Neta Auto’s engineering and process departments now have early access to design data, they can carry out design and engineering analysis in parallel and identify any system integration issues before progressing to the next stage of the development cycle. From here, they build detailed, accurate digital mock-ups (DMUs) of each vehicle. Achieving a continuous data flow from one stage to the next helps to avoid version control issues and reduce the inefficiencies of manually sharing data.
“We’re using the platform to construct a multi-configuration, multi-stage, module-level DMU, which helps to improve the quality of the first engineering prototype,” said Lu Ruozhen, deputy general manager of the Project Management Center at Neta Auto. “Before, when the general layout engineer arranged a new component in the vehicle, they would then export it to the design release engineers for specialized design, which was both inefficient and prone to error. The reduction in management costs by integrating the design structure and engineering bill of materials (BOM) through ENOVIA is evident, resulting in a clearer engineering perspective.”
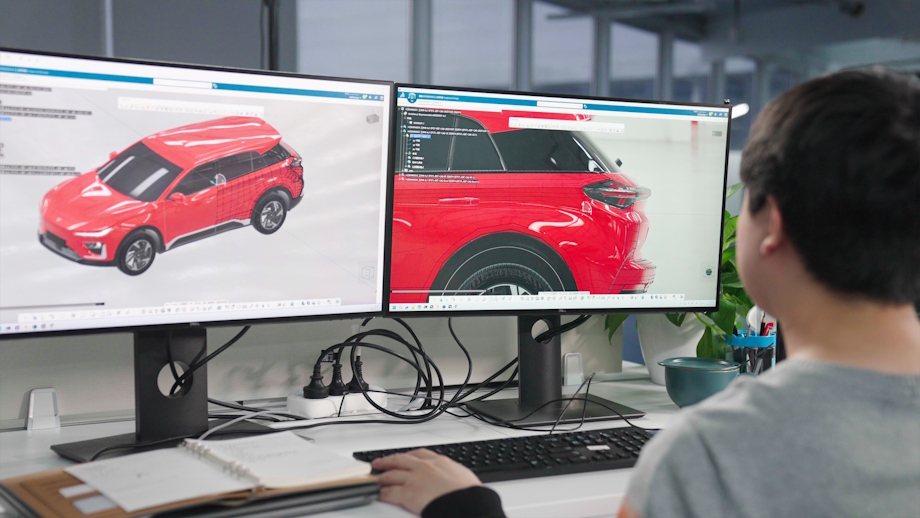
Integrated systems and engineering disciplines
Before moving to the 3DEXPERIENCE platform, Neta Auto already used CATIA V5 to design its first EVs. The company now uses CATIA on the 3DEXPERIENCE platform for all new product development.
“With the 3DEXPERIENCE platform, we can easily access our legacy design data in CATIA V5 through POWER’BY, so we can collaborate effectively without changing our tools,” Lu said. “Engineers from multiple disciplines such as general layout, dimensional engineering, structural design and wiring harness design can all work within the same data model.”
Achieving greater synergies between mechanical and electronic design is proving crucial, particularly when developing complex products such as electric driving systems and range extenders. Neta Auto uses the 3DEXPERIENCE platform to foster closer links between all disciplines and systems.
“Developing electric motors, batteries and controls requires us to integrate upstream and downstream disciplines, from concept design to electrical engineering,” Lu said. “Our aim is to make collaboration more efficient, data flow faster, and accelerate the entire iterative process of product development. In the early stages of product development, design engineers and BOM engineers can collaborate on information such as material usage and configuration for individual vehicles, enabling early improvements to optimize costs.”
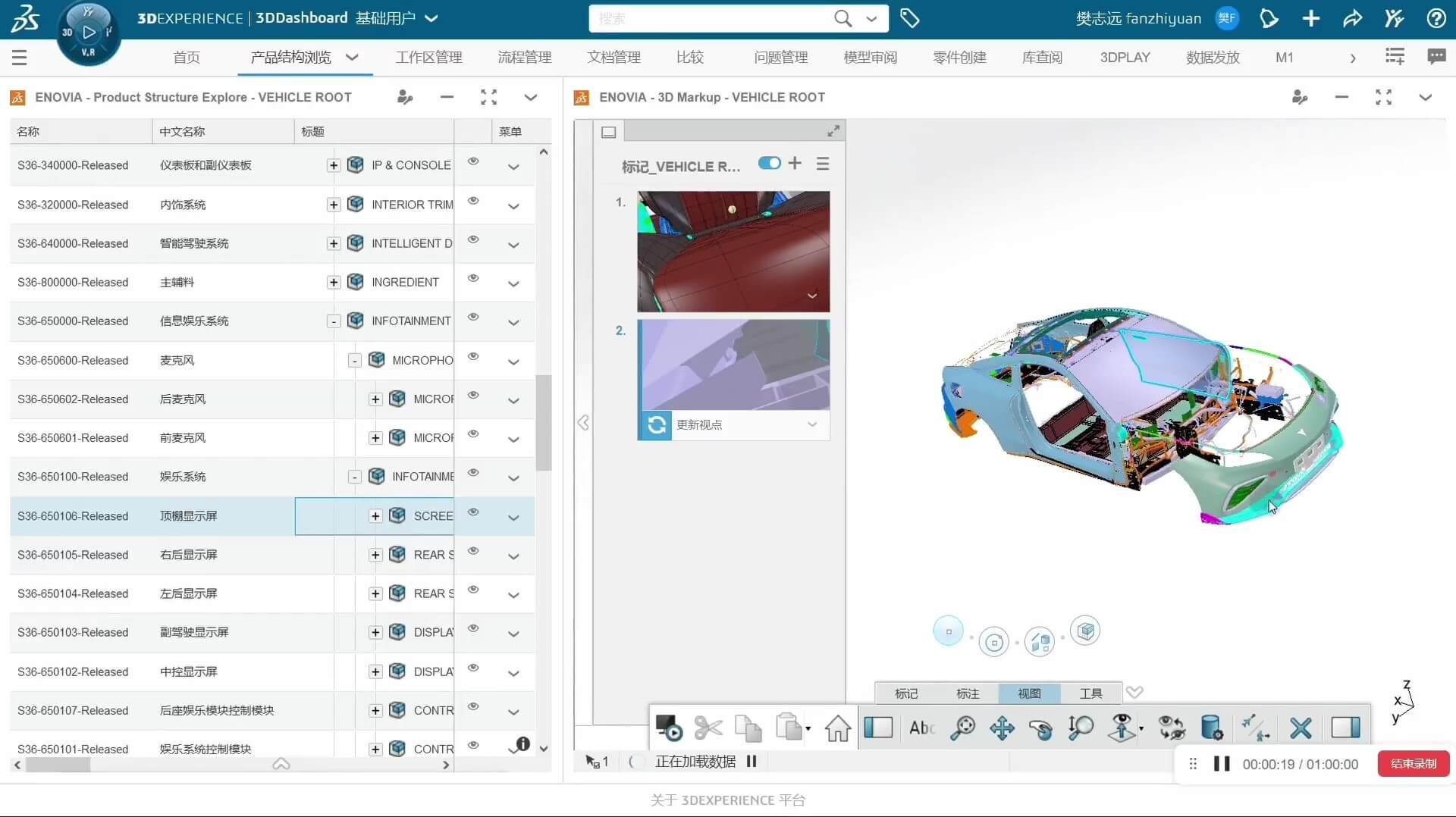
Consistency boosts quality
Neta Auto takes advantage of ENOVIA’s product data and change management capabilities on the 3DEXPERIENCE platform to achieve a continuous data flow from one development stage to the next and maintain traceability of all modifications with full version control. It is also standardizing its global business processes by building a unified configuration library, parts library, and product structure to ensure everyone works consistently and maintains the same level of quality regardless of the vehicle or part they’re working on.
“With ENOVIA, we have established a more standardized process for data release and design changes, helping to continuously enhance quality,” Lu said. “Our centralized configuration library can be used to develop an entire vehicle structure, part or assembly, making it easy to quickly replicate and adjust designs and meet the rapidly changing needs of the market.”
Through virtual prototyping, we reduced the time it takes to release a product by one month.
Simulation saves time and cost
Neta Auto’s engineers are increasingly exploring the benefits of a unified modeling and simulation (MODSIM) approach to identify potential design issues and solve them early on. They use CATIA across the entire R&D vehicle design process to define the overall vehicle plan and key parameters. The styling department then designs the vehicle’s surface before it goes to the general layout team for structural strength analysis. They use SIMULIA to test the body, chassis, enclosures, interior and battery pack and simulate creep and deformation under sunlight to refine plastic components.
“In the platform, we conduct simulation analysis to improve and optimize our structural design,” Dai said. “It means we no longer need to perform as many as 40 physical tests per project, equal to cost savings of over RMB 2 million [€260,000]. And through virtual prototyping, we reduced the time it takes to release a product by one month.”
Neta also values the ability to identify and address design and system integration errors virtually rather than having to rectify them during manufacturing, which leads to even greater cost savings.
“We’re encountering nearly 20% fewer issues at the prototype stage, saving us almost RMB 10 million [€1.3 million] in R&D costs,” Dai added.
The 3DEXPERIENCE platform supports Neta Auto with DELMIA’s multi-factory governance capabilities across their global production plants.
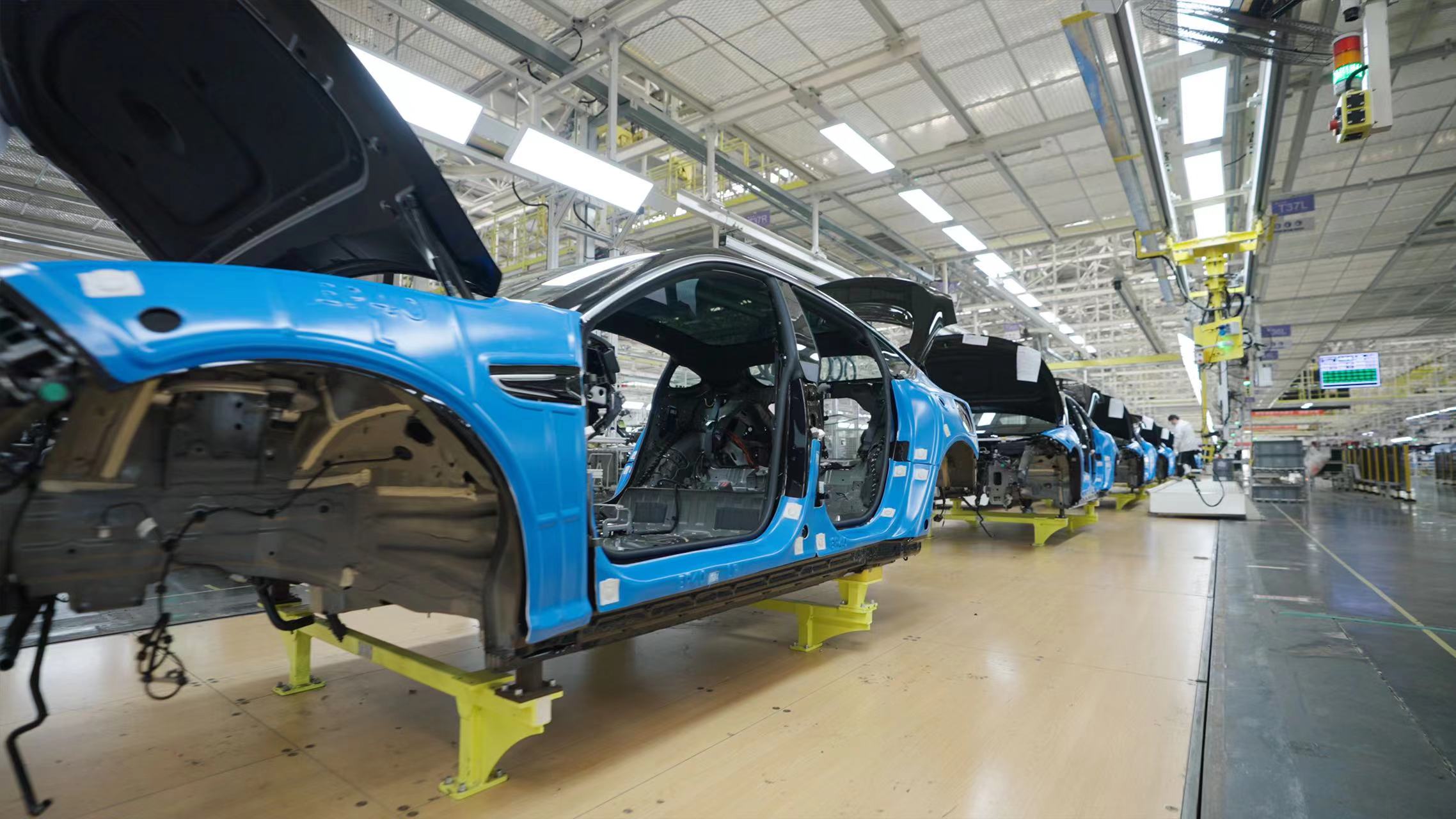
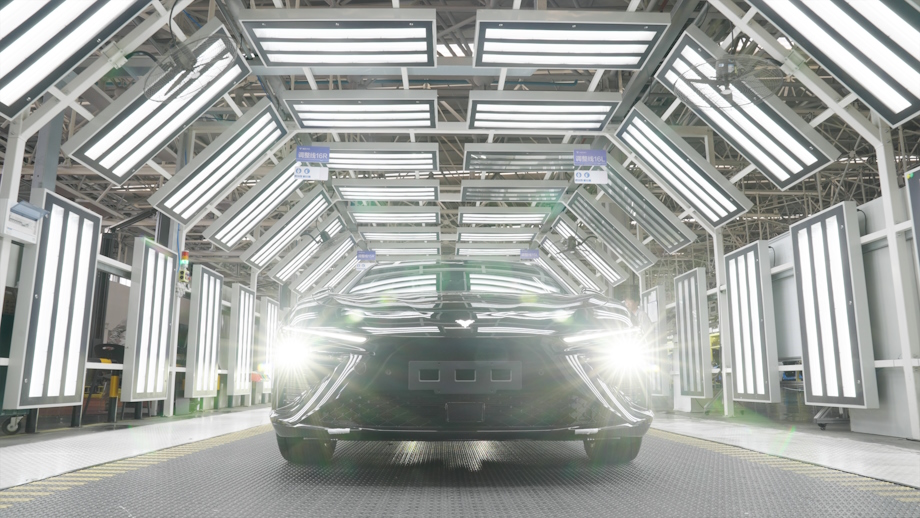
Scaling up global production and sustainability
To support its rapid expansion, Neta Auto takes full advantage of the platform’s end-to-end functionality and benefits from DELMIA to plan and optimize its production processes, ensuring every plant follows the same procedures and standards. This will be instrumental as the company scales up its globalization efforts and sets up more of its lean and intelligent welding, painting and assembly plants overseas, including a new factory in Thailand set to produce around 20,000 new EVs per year.
“DELMIA’s multi-factory governance capabilities support us to consider the quality and regulatory requirements of different factories,” Lu said. “It helps us better coordinate and manage factories in different geographies and achieve higher efficiency, quality and sustainability, thereby enhancing competitiveness and reducing operational risks and costs.”
In line with its vision to contribute to the advancement of sustainable mobility worldwide, Neta Auto hopes to also make its own processes more energy efficient and gain a clearer understanding of the wider environmental impact of its entire value chain.
“Enterprises like us must contribute to energy conservation, carbon emission reductions and the sustainable development of our planet,” Zhang said. “The platform helps since we were able to significantly reduce the number of physical prototypes resulting in resource and energy savings. On our journey to transform our enterprise into a global car brand, we believe the 3DEXPERIENCE platform is central to our success, helping us to bring our EVs to market as quickly and efficiently as possible.”
00:00 – 00:30
Zhang Yong, CEO, Neta Auto:
We started out producing smart electric vehicles to make this Earth a better place and promote the use of clean energy. At the same time, we want consumers to enjoy using high technology, at low prices. The big industry trends in the future will definitely be electrification and intelligence. So we need to make some forward-looking investments in technology and products.
00:31 – 01:04
Dai Dali, CTO, Neta Auto:
For a start-up automotive company like Neta Auto, it’s very important to launch products quickly and efficiently, and apply the latest technology to meet customer needs. The 3DEXPERIENCE platform has effectively shortened the time we take to release our digital prototypes by one month. It has also reduced problems during prototyping by nearly 20%, saving almost €1.3 million in R&D costs. We chose the 3DEXPERIENCE platform because it can unify various business processes, from product planning to production.
01:05 – 01:17
Lu Ruozhen, Deputy General Manager of Project Management Center, Neta Auto:
The platform can provide timely, accurate and traceable R&D data management for the entire vehicle development process, across disciplines, departments, and regions. It can also resolve differences caused by version changes.
01:18 – 01:41
Dai Dali:
From styling design to the distribution of engineering data and to production, we aim to reduce the project completion time to six months. Our styling department uses CATIA to complete the surface design, and will then share the surface data with the design team working on the general layout. Our engineers use CATIA for the overall design including data verification to spot issues in early phases.
01:42 – 01:53
Lu Ruozhen:
Using ENOVIA as a product data management platform in the early stages of product development, design engineers and bill of materials engineers can collaborate on information such as material usage and configuration usage for each vehicle.
01:54 – 02:17
Dai Dali:
We do analysis engineering simultaneously with design on the platform. SIMULIA is used to analyze structural strength of the body, chassis, closures, interior, battery pack and other common components. In the past, we performed more than 40 actual tests in one project. But now we’ve replaced them with simulations, which has saved us over €260,000 in expenses.
02:18 – 02:33
Lu Ruozhen:
DELMIA helps manage the quality and regulatory requirements of different factories, and achieve higher efficiency, quality, and sustainability. This enhances competitiveness and reduces operational risks and costs.
02:34 – 02:46
Zhang Yong, CEO, Neta Auto:
Dassault Systèmes’ solutions have the capability to help enterprises achieve these energy-saving and emission reduction goals.
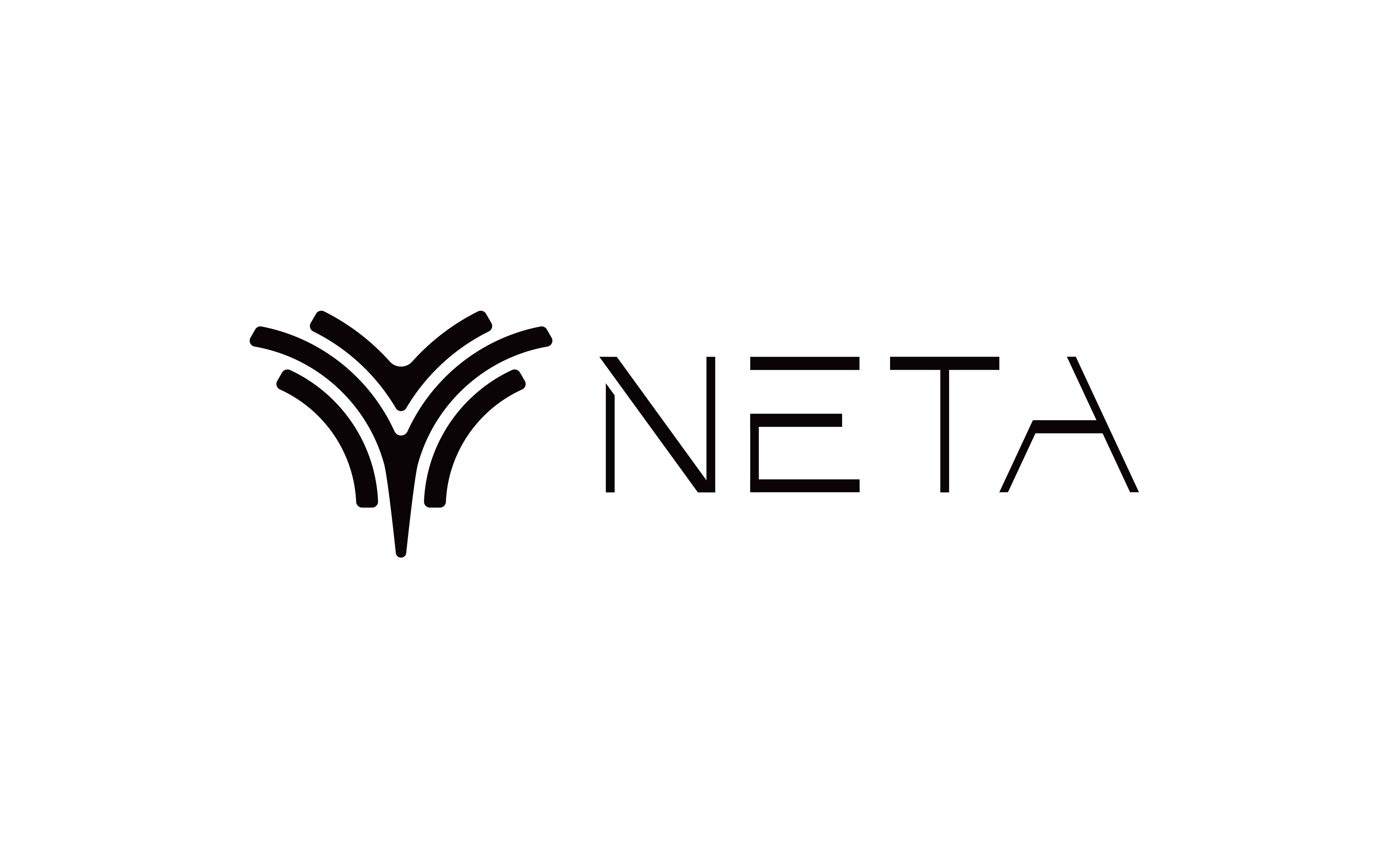
Focus on Neta Auto
Neta Auto is part of Hozon New Energy Automobile, an innovative technology company in China that integrates hardware products and software services. Founded to “make intelligent EVs for all”, Neta Auto is on a mission to break the norm by making the driving experience more intelligent and accessible. The company is dedicated to promoting the continuous evolution of electric vehicles and playing a leading role in the latest technology development trends.
For more information: http://netaauto.co