NAOS Ship and Boat Design
Provide ship owners with high-quality designs for safe, high-performing, enery-efficient vessels.
Diverse demands in shipbuilding
The marine industry is a vast and diverse industry comprising vessels for leisure or commerce, each with their own set of specificities. The superyacht market, once reserved for an older population, is now attracting a much younger generation of owners. Their expectations run from greener and high performance vessels to more innovative and exciting designs. Cruise liners are experiencing a boom as more people choose to spend their vacations at sea. Here, passenger safety and experience are at the forefront of operators’ priorities. In the passenger and cargo transport sector, shipping capacity, operating costs and energy efficiency are among some of the key requirements evoked during business negotiations. Overall, marine vessels are complex undertakings that require the collective effort and expertise of multiple disciplines.
Roberto Prever, president of NAOS Ship and Boat Design (NAOS), leading Italian vessel design company, confirms these trends. “The sector for ferries and other passenger vessels, including mega yachts that can range up to 200 meters in length, is growing,” he said. “There are more and more people buying yachts or taking cruises, generating considerable demand for new and more high-performing vessels. The ferry business, which has stagnated for the past five years because of changes in environmental and safety regulations, is once again growing as many owners are starting to invest to renew their fleet.”
NAOS designs marine vehicles, including ro-ro (roll-on/roll-off) passenger and cargo ships, as well as yachts. Its customers are shipyards that build the final product, ship owners, and shipping companies that operate the vessels. “Our customers want a ship that is competitive in terms of operating costs, is green, consumes little fuel and has sufficient capacity to transport passengers and goods.”
Navigating a competitive market
Whether for commerce or pleasure, today’s ships are bigger and more ambitious. Shipbuilders seek design partners that can deliver the highest quality designs, which will enable them to improve productivity at the build level and reduce production costs. The more precise the design and the clearer the manufacturing instructions, the less time shipyards need to spend asking for clarifications or doing reworks. As a provider of vessel designs to a number of shipyards, NAOS knew that to create high-quality designs, it would have to streamline its design process and approach it in an integrated manner.
“Innovation is one of our biggest values,” Prever said. “Because all ship systems are interrelated and impact one another, different disciplines must work together more efficiently if we want to avoid design errors that can delay production and delivery of the vessel to the customer. In order to provide the yards with innovative, qualitative, and energy-efficient designs on the one hand and clear manufacturing documentation on the other hand, we need to be on the leading edge of technology. We have four sites, one in Italy, one in Spain, one in Croatia and one in Sweden. In each site there are employees with specific expertise. We cannot move people from one site to another to work on a project. The only way they can effectively collaborate with one another is if we provide them with the right tools and technologies to do so,” he said.
Unified environment for efficient, real-time collaboration
NAOS chose the 3DEXPERIENCE® platform and its Designed For Sea and Optimized Production For Sea industry solution experiences for ship design, analysis and manufacturing planning. “We selected the 3DEXPERIENCE platform because we believe it has the most advanced solutions for shipbuilding on the market,” Prever said. “It is exactly the type of collaborative solution I have been looking for since NAOS was founded over 20 years ago. Our four sites can work together as if everyone was physically in the same office, which is more productive. The marine industry is more traditional and “old-school” than other sectors such as aerospace and automotive. We decided to take advantage of the 3DEXPERIENCE platform to bring shipbuilding design into the 21st century as well.”
NAOS works with AITAC, a design house in Croatia, on some of its projects to design certain zones of the ship. “They have direct and secure access to our platform because 3DEXPERIENCE features role-based access control that allows us to define which information they can and cannot see,” said Miha Hribar, naval architect at NAOS. “We have a view of the entire vessel and can see what they are doing while they too can visualize what we are doing in the areas that are adjacent to theirs. Everyone can collaborate in real time, which streamlines the process and reduces design errors. 3DEXPERIENCE has definitely made working with our partners more productive,” Hribar said. A local Dassault Systèmes’ business partner, deployed the 3DEXPERIENCE platform at NAOS. “They helped us choose the right infrastructure and configured the platform at our different sites,” Prever said. “We also received full support from Dassault Systèmes that took into account our specific needs and our way of working. The relationship between Dassault Systèmes, NAOS and our partner is excellent.”
Big picture, big impact
NAOS’ end-to-end development has been given a boost with Designed For Sea as project stakeholders can access and work on the same 3D model, in real time. “With Designed For Sea, using the general arrangement plan, we can rapidly create a single Structure Functional Design master model that provides us with a complete overview of the vessel’s primary structures,” Miha Hribar explained. “All the other disciplines responsible for piping, safety or structural stability, for example, can access and work on this model to do their part. In this way, we can immediately detect where something can go wrong and correct any potential issues before sending the plans to the shipyard. This is important because by catching these issues early, we know the yard will not have to deal with them during the build phase when it’s much more complicated and costly to correct,” Hribar said.
“Moreover, we can show this 3D model to the ship owner, who can ask for modifications in the early development stages when changes have the least impact on costs and schedules,” added Luigi Abati, designer at NAOS. “Even people who are not accustomed to viewing 3D models can easily understand what they are looking at. With the 3DEXPERIENCE platform we can rapidly explore several design scenarios to evaluate different options and discuss them with the customer before choosing the best one.”
The 3D master model is also the foundation for all downstream analyses and simulations. Simulation engineers use it to perform finite element analyses to help, for example, optimize a vessel’s weight for more fuel efficiency. “We can use the existing master model instead of having to remodel the area we need to analyze each time,” Hribar said. “From the same master model, we can also automatically generate drawings for use by classification societies and create the manufacturing documentation for the shipyard, saving us and them a considerable amount of time.”
NAOS expects to redure design time by up to 40% with Designed for Sea
Managing complexity
The 3DEXPERIENCE platform helps NAOS manage the complex nature of ship design. “In Designed For Sea each 3D element is not just a geometric object but a full-featured item with parameters and attributes that remain part of its definition throughout the ship’s lifecycle,” Abati said. “The history of each object is stored in the 3DEXPERIENCE platform for future reference and reuse in new projects. Designed For Sea also enables us to easily create the bill of materials (BOM) from the 3D master model with information such as block weight, center of gravity, costs, or supplier information for the shipyard.”
NAOS uses its own standard catalogues to make sure designs comply with company standards. “The 3DEXPERIENCE platform is very flexible because we can adapt the catalogues to our and the yard’s needs,” Hribar said. “This is in stark contrast to other, more rigid, programs that require us to ask their editors to implement any changes.”
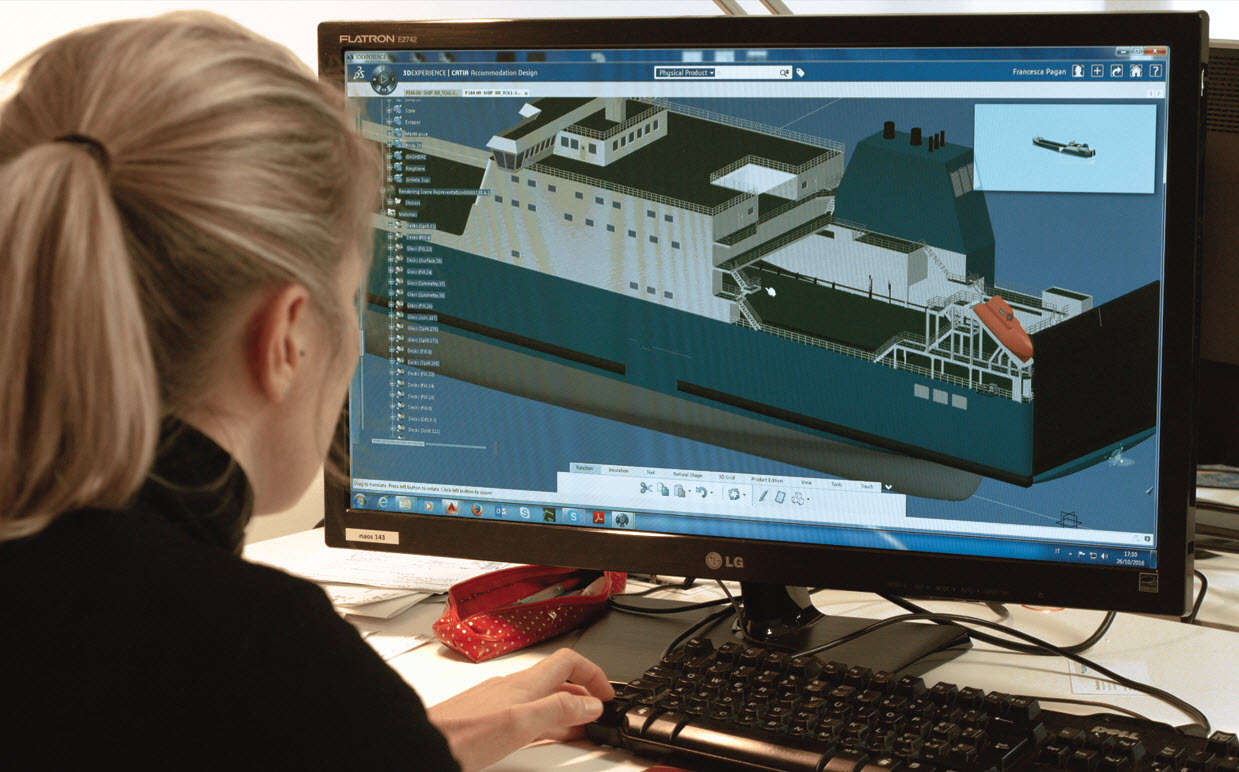
Significant productivity improvements
Designed For Sea has accelerated the design process thanks to rules that automatically execute certain tasks. “In the past, modeling was a more manual process, Hribar said. “Now with Designed For Sea’s knowledge management features, we can automate the design process by applying previously defined rules, which saves us a lot of time. Based on the first project we worked on using this industry solution experience, we expect to reduce design time by up to 40% in the near future,” Hribar said.
“We began with a sketch of a vessel’s internal and external structures and systems and continued with a more detail design through to definition of the manufacturing details,” Abati said. “This integrated approach enabled all departments to concurrently work on their part and see how everything fits together. Any possible clashes or interferences were immediately visible,” he said. “Even when manipulating large assemblies, we had excellent performance,” he added. “Another benefit with the 3DEXPERIENCE platform is that all the applications we need are integrated in one single environment. This significantly reduces errors that often arise when translating data from one format to another.”
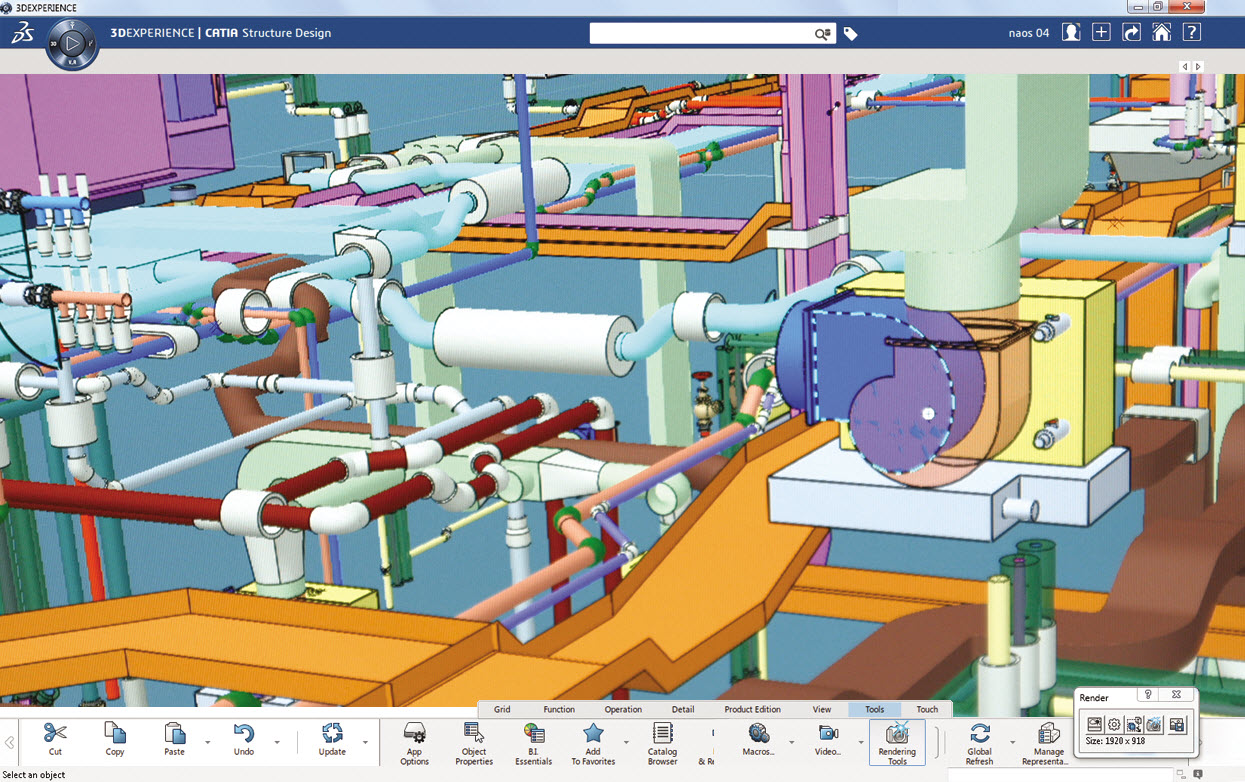
Effective manufacturing planning
Shipyards need manufacturing documentation to guide them during the build process. “They expect us to deliver assembly drawings, for example, with nesting features to show them where to cut the plates and instructions on how the ship should be assembled block by block,” Hribar said. “We use Optimized Production For Sea to generate the manufacturing plan comprising 3D assembly documentation and simulations as well as detailed instructions for each task. In the past, we didn’t have the link with the master model so every design unit had to be created from scratch. With Designed For Sea and Optimized Production For Sea, we can automatically generate manufacturing instructions from the 3D master model for the shipyard thanks to the associativity between the design and manufacturing planning information,” Hribar said. “Through better collaboration, we can deliver first-time-right designs to the shipyard that is able to build the associated ship without any problem,” Abati added.
Bring design to the next level
The 3DEXPERIENCE platform enables NAOS customers to experience the ship design at a very early stage and helps ensure all their requirements are correctly met. “Displaying a 3D model on a big screen during customer presentations always has a big impact on them,” Prever added. “The customer is happy to walk through the digital model and see what the ship will look like. They have the impression that they’re really inside.”
When asked how NAOS wants to be perceived by its customers, Prever responded: “I would like to hear that they are happy with their vessel and that they are making money with it,” he said. “Our customers know that a NAOS design results in a safe and efficient vessel that complies with, and even exceeds, international rules and requirements. Our strategy is to become a leading-edge company in the ship design business. In my opinion, the 3DEXPERIENCE platform and dedicated Marine & Offshore industry solution experiences definitely help elevate our design process to the next level. With them, we hope to become one of the most advanced companies in our field.”
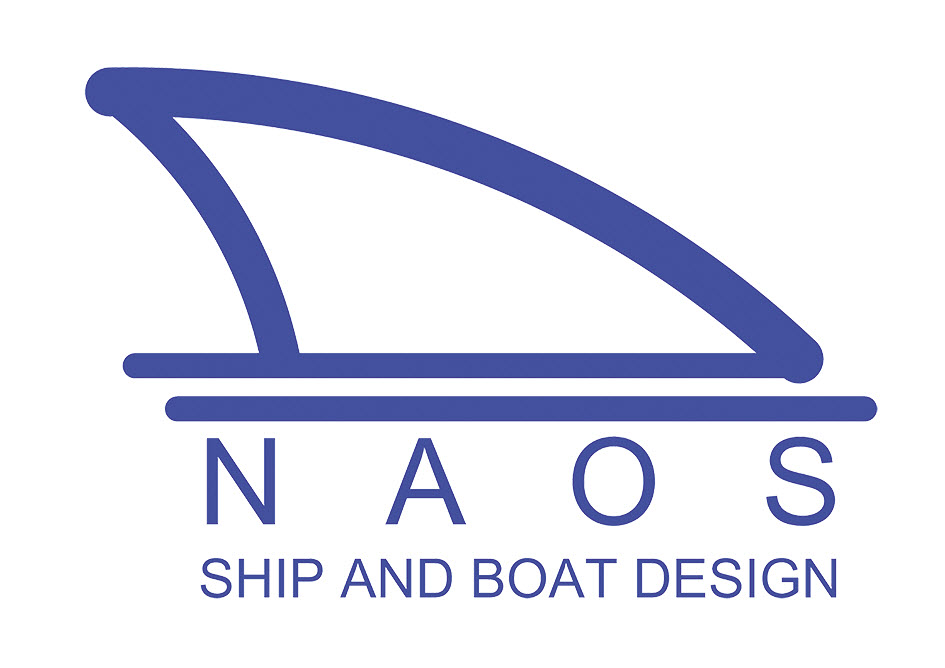
Focus on NAOS Ship and Boat Design
Leading Italian marine vehicles design company.
Services: Feasibility studies, consultancy, complete basic design including specifications, weight, hydrodynamic, safety and stability evaluations, structural calculations, classification drawings, workshop drawings
Employees: approx. 30 (combined)
Revenue: approx. 3.0 M€
Headquarters: Trieste, Italy
For more information: www.naos-design.com
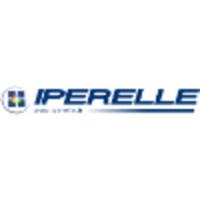
Focus on Iperelle
Iperelle was founded in 2002 and since then, the company has further developed its PLM expertise, supporting customers of all sizes operating in different fields ranging from mechanics, design and construction of molds, consumer goods, technological equipment, aerospace, transportation and planning and design services. It delivers end-to-end support from conception, design and simulation of a product to workshop preparation, technical documentation and management of its complete lifecycle. Iperelle is Dassault Systèmes’ premier partnerin Italy delivering industry solutions based on the 3DEXPERIENCE® platform and its ENOVIA® CATIA® SIMULIA® and DELMIA® applications as well as educational certification.
For more information: www.iperelle.it