NAAREA
In 18 months, the French startup NAAREA developed from the ground up the virtual twin of its 4th generation reactor – the XAMR – on the 3DEXPERIENCE platform to master its lifecycle. The company takes advantage of the Engineering Excellence and Capital Facilities Information Excellence industry solution experiences on the cloud to manage all design, engineering and manufacturing processes within a centralized ecosystem.
Micro reactor turns nuclear waste into clean and decarbonized energy
According to the International Energy Agency*, the amount of energy we consume worldwide is set to almost double between now and 2050 if we continue using power in the same way as we do today. Aside from the fact that supply will struggle to keep up with demand, intensifying pressure to reverse the tide on climate change leaves society no option when it comes to breaking our reliance on fossil fuels and moving to low-carbon energy production. In France, one company is working on a pioneering micro nuclear power plant to solve this challenge, delivering a reliable supply of clean energy to industrial companies and using up radioactive waste in the process.
NAAREA is on a mission to deliver abundant, carbon-free and decentralized energy at scale. To achieve its ambitious objective, the startup is developing XAMR® (eXtrasmall Advanced Modular Reactor), a fast neutron micro reactor. The reactor uses molten salts as coolant and long-life nuclear waste as fuel to produce heat and electricity without releasing any greenhouse gases. XAMR will also play an important role in the circular economy by turning highly irradiated spent nuclear fuel from conventional reactors into a new energy source.
* “Net Zero by 2050 – A Roadmap for the Global Energy Sector”, International Energy Agency, May 2021
00:00 – 00:14
Jean-Luc Alexandre, CEO and Founder, Naarea:
Naarea’s ambition is to participate in the planet’s decarbonization and to supply the energy demand that will be huge in the next 30 years. The main constraint is time.
00:15 – 00:26
Timothée Kooyman, Technical Director, Naarea:
We’re using the 3DEXPERIENCE suite from Dassault Systèmes, which provides the traceability, engineering and calculation tools needed to design our reactor.
00:27 – 00:37
Jean-Luc Alexandre:
Naarea is a young French company that develops fourth generation micro-nuclear generators (molten salts, fast neutrons) to produce electricity and heat from nuclear waste.
00:38 – 00:46
Timothée Kooyman:
It’s an extremely ambitious project. We want to do it quickly, without losing any information while ensuring a high level of traceability and safety.
00:47 – 01:03
Jean-Luc Alexandre:
The 3DEXPERIENCE platform is the backbone of the project over several decades. The virtual twin will not only allow design and development, but also will support safety and security demonstrations, manufacturing, deployment, operation and maintenance, until the reactor’s end of life.
01:04 – 01:41
Timothée Kooyman:
Naarea’s virtual twin is based on three pillars. The first one is the 3D modeling of the reactor and all its parts, on top of which we’re adding change management and configuration management. The second pillar is simulation.This means that we can do mechanical, thermo-hydraulics, fluid dynamics simulation and neutronics calculations. 3DEXPERIENCE enables us to carry out simulations directly, without having to go through time-consuming data conversion. And the third pillar is the traceability of engineering data, specifications and requirements. We can check that the job has been done correctly, by the right people and that it meets our needs.
01:42 – 01:52
Jean-Luc Alexandre:
A virtual twin helps increase startup speed and accelerate deployment. We managed to develop the first version of the virtual twin in just 18 months, which is a record.
01:53 – 02:02
Timothée Kooyman:
The cloud solution meant that from the outset we had a complete tool that would work straight away. There was no need to set up servers and an in-house IT department.
02:03 – 02:10
Jean-Luc Alexandre:
Naarea is an extremely complex multi-system project. We have a whole bunch of different disciplines that need to be brought together.
02:11 – 02:33
Timothée Kooyman:
There are about 30 systems. But each system is subdivided into 5 to 50 subsystems. So we have several thousand parts. All engineering teams work on the 3DEXPERIENCE platform, which allows us to do systems simulation. Using 3DEXPERIENCE enables us to have a single entry point. This means all the information is on one platform, and it’s authentic.
02:34 – 03:12
Jean-Luc Alexandre:
Assystem's role was to know how to configure the 3DEXPERIENCE platform and integrate all the scientific computing tools. Assystem has been able to mobilize top-level engineers in record time to achieve this integration. 3DEXPERIENCE makes it possible to guarantee a common platform for all our employees, and allows for digital continuity, which is absolutely vital on a project of this complexity. Today, any new complex project must have a virtual twin.
“When built, each XAMR reactor will be about the size of a bus so it can be sited close to its customer and does not require an external grid supply,” said Jean-Luc Alexandre, founder and CEO of NAAREA. “This makes it an ideal solution for providing decarbonized, accessible and secure energy to all, even those in remote regions or developing countries with limited electricity networks.”
“The reactor power is extracted using molten salt circuits to carry heat either to the customer or to a carbon dioxide turbine that generates electricity,” added Timothée Kooyman, technical director and deputy director of operations at NAAREA. “Waste heat from the turbine cooling is also recovered to supply heating or cooling to the customer. This high efficiency system means that the reactor can be cooled using the atmosphere as the heat sink and that no body of water is required for this purpose.”
Not only is NAAREA’s proposed energy solution pioneering, so is its development approach. The company is creating a functional version of XAMR in the virtual world first and using this integrated virtual environment to manage all its design, engineering and manufacturing processes. Everything is being handled on the 3DEXPERIENCE® platform on the cloud.
We managed to develop the first version of the virtual twin in just 18 months, which is a record.
First XAMR virtual twin
NAAREA successfully built its first virtual configuration of XAMR using CATIA on the 3DEXPERIENCE platform within just 18 months. By applying model-based system engineering (MBSE) methods – whereby all disciplines and systems are interlinked from the onset – NAAREA’s team of engineers was able to validate the architecture, size and functionality of the reactor, and define the interface between its subsystems in a virtual environment. This virtual twin will now serve as a continuous digital thread throughout the reactor’s entire lifecycle.
Engineers benefit from a secure environment to collaborate and access all the applications they need in one place. They can work on a shared virtual twin of XAMR that encompasses multiple dimensions including operational and safety requirements, dynamic behavior and functional analysis, 2D schemas and 3D digital mockup.
“We want to be on the market by 2030, so we need to move fast,” Alexandre said. “The best solution to achieve our goal is the virtual twin. It’s a fantastic accelerator. One of the best features is that we can design and simulate as we go, so we can test our ideas and see if they’re worth progressing. The 3DEXPERIENCE platform also supports us to work together in a really collaborative way.”
Regardless of which part or discipline they work in, NAAREA’s engineers can design in context, so a mechanical engineer can see what the hydraulics engineers and electrical engineers are doing.
“There are several thousand parts in the reactor connected to each other, and their interfaces need to be known to ensure that if I modify something, my colleagues are aware of it,” Kooyman said. “In the future, when I click on an object, for example a valve, I can find out who designed it, why, the associated calculations, requirements and specifications. I can also source the manufacturing and assembly records and find out when I’m going to have to replace it or carry out maintenance.”
NAAREA’s technology partner Assystem plays an integral role in making XAMR and its virtual twin possible. Backed by strong expertise in the nuclear sector, the engineering company delivers project management, integration and engineering services to NAAREA, helping to meet key milestones, stay in compliance with industry safety regulations, and keep the ambitious development plan on track.
“Assystem helped us to create the virtual twin of the reactor and build the links between all the subsystems, as well as the connected processes around them,” Alexandre said. “Their knowledge of the 3DEXPERIENCE platform means they know how to create the right parameters and workflows, and guide us to use these solutions to their full potential. We share the same vision and, together, we’re committed to decarbonizing the world.”
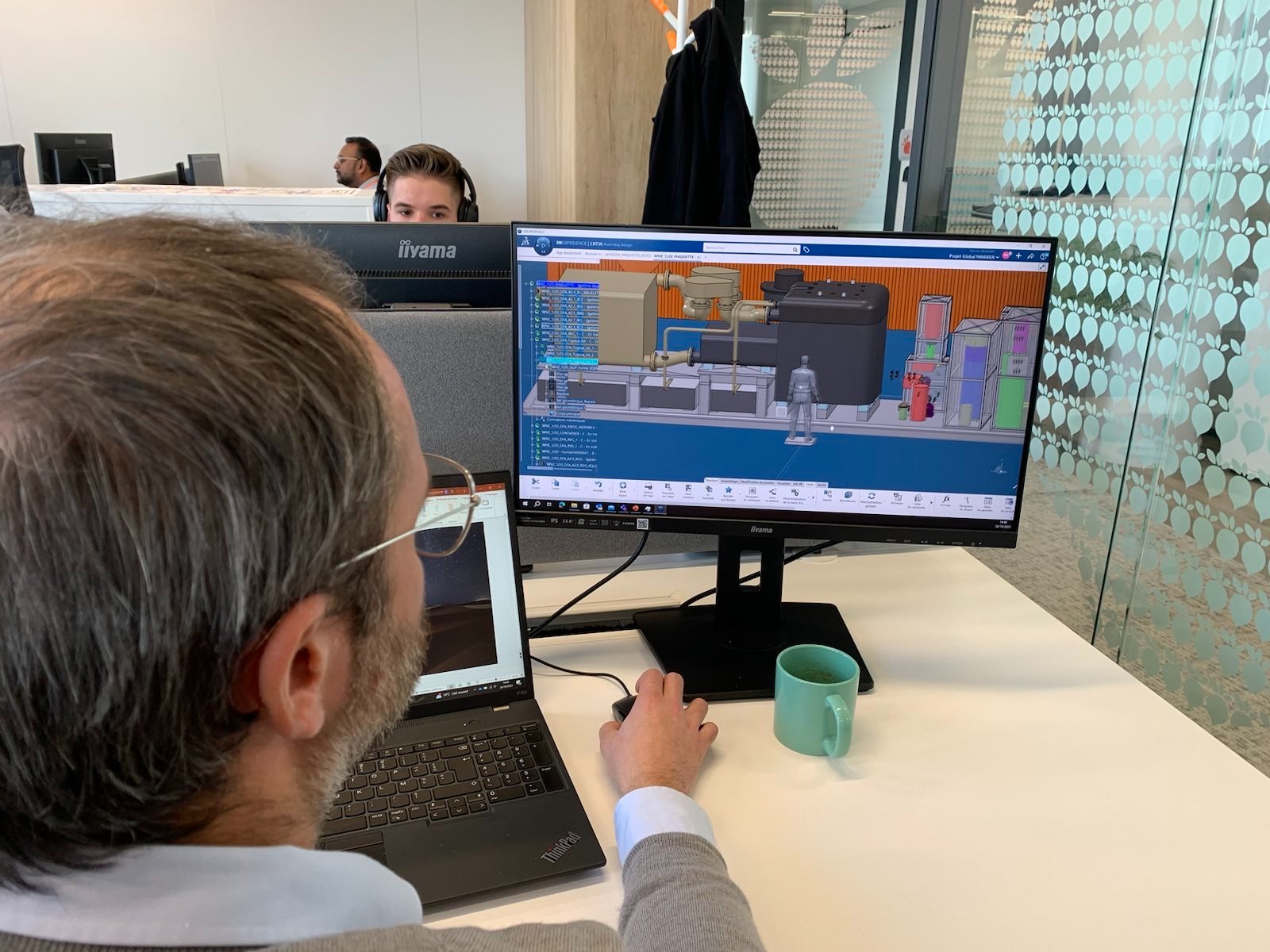
Virtual testing and simulation underpins safety
Not only is the ability to simultaneously design and simulate – widely referred to in the industry as a MODSIM approach – helping NAAREA to work faster, it’s also critical for getting XAMR certified with the regional and international safety authorities. NAAREA is running laboratory tests and feeding data from its experiments into XAMR’s virtual twin to test its safety features and analyze its operational performance ahead of physical prototype production.
“All our test data, simulation results and design modifications are logged in the virtual twin; this traceability is key for the safety authorities and helps us be sure that we can manage any changes and detect any discrepancies in the configuration management,” Alexandre said. “We’re excited about how the virtual twin can be used as part of the regulatory process to demonstrate the reactor’s safety.”
NAAREA uses the simulation capabilities in SIMULIA on the 3DEXPERIENCE platform to test all manner of scenarios ahead of building XAMR. They include simulating the behavior of the reactor material, as well as mechanical, thermal-hydraulic, fluid dynamics and neutronics calculations.
“The reactor is cooled with molten salt mixed and fueled with irradiated spent fuel from previous generation reactors,” Kooyman said. “It’s something we’re working to understand better and we want to move forward quickly. Within five years, we want to complete all engineering stages without losing any information, guaranteeing a good level of traceability and safety.”
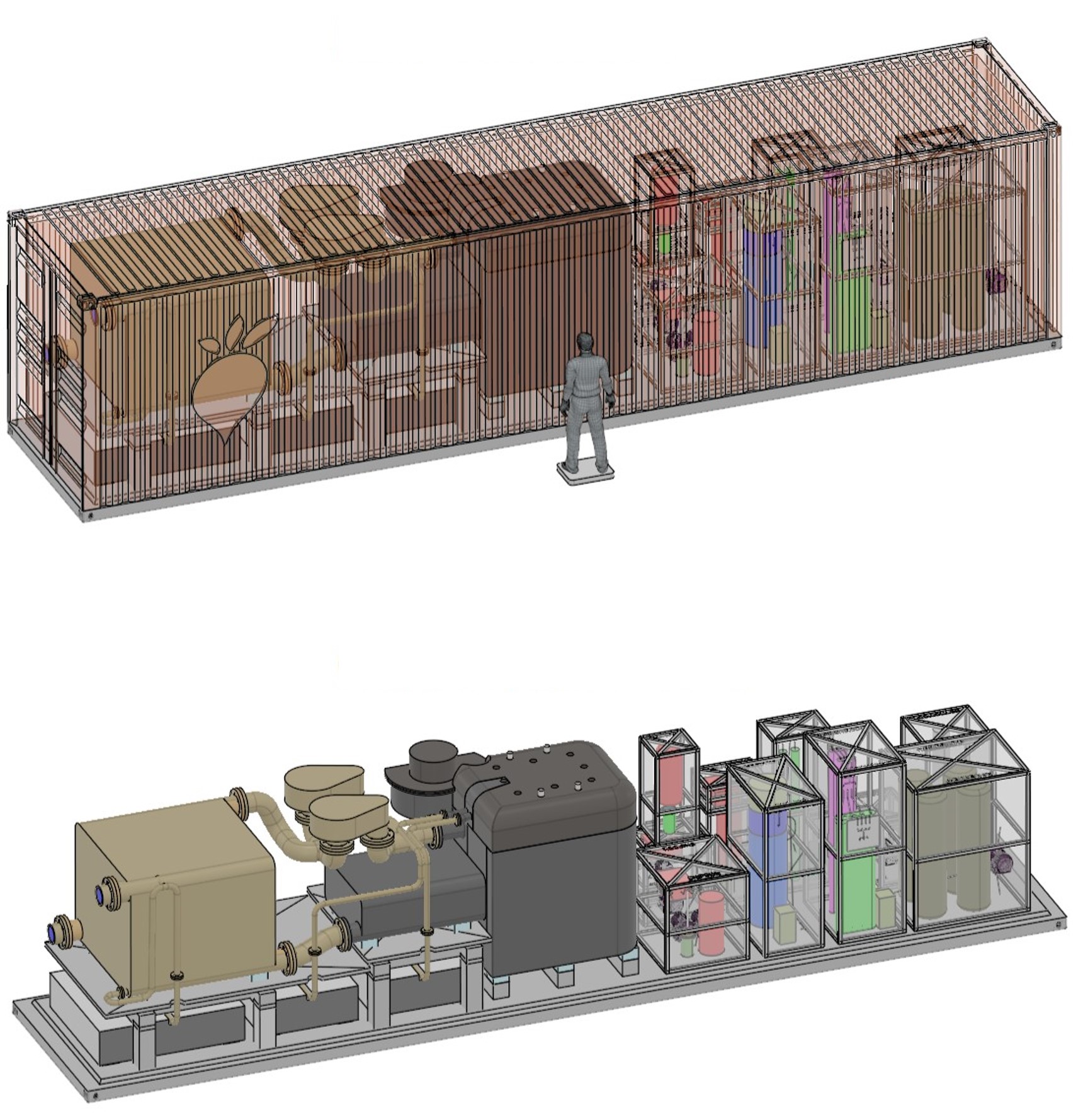
Connecting systems and people in one platform
Opting for a cloud-based implementation has given NAAREA the freedom to bring its vision to life at an unprecedented pace – and the opportunity to scale up as its business needs evolve.
“We have a very ambitious target of bringing reactors into commercial service before the end of the decade,” Kooyman said. “By using a cloud-based platform from the outset, we gained a complete tool that we could work on immediately without having to set up servers and an in-house IT department.”
ENOVIA on the 3DEXPERIENCE platform manages the high volume of data being produced and makes it easy for users to securely store and access the information they need. It also supports change and configuration management – critical as each sub system within the reactor reaches different levels of maturity.
“As our designs evolve, we need to know which versions to work on and at which stage of the development process every component and system is,” Alexandre said. “ENOVIA ensures full data traceability, so we don’t lose sight of where we are and which sub systems to validate.”
Cutting-edge technology is not the only factor that will make XAMR a reality; it’s also the people behind it, and NAAREA recognizes the importance of making its digital-first approach part of its wider company culture.
“We need our users to understand that the virtual twin is a single point of data and they must put everything into the platform, including their knowledge and ways of working, to get the most out of it,” Alexandre said. “When you work on complex products like XAMR, issues tend to arise from human error and the virtual twin will help to prevent this. Having all information stored in the 3DEXPERIENCE platform will also be critical for ongoing training, both in terms of onboarding new employees and showing eventual customers how to operate XAMR.”
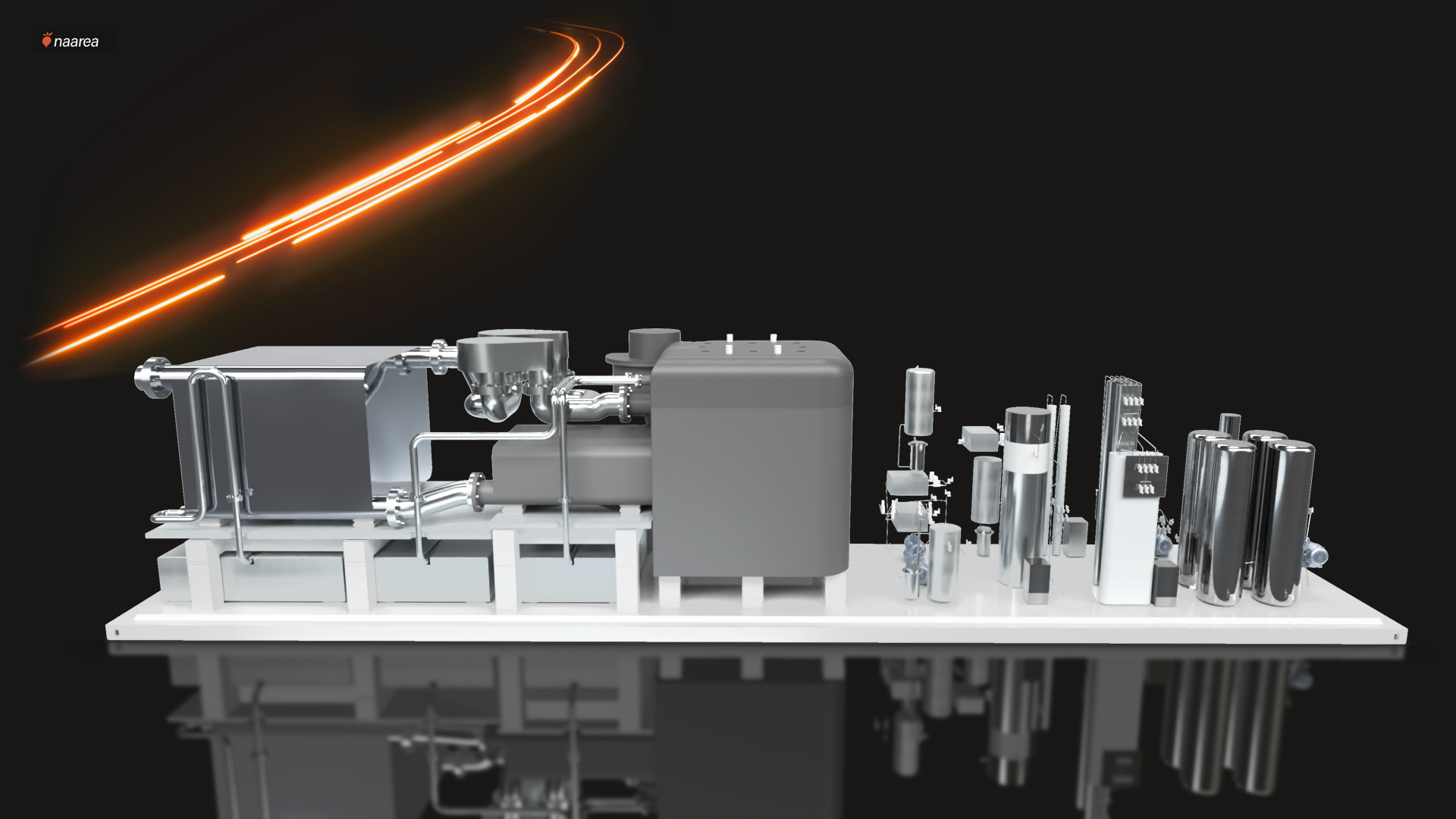
A full-service low carbon energy provider
Once NAAREA completes phase two of its development cycle and successfully commissions a fully operational physical prototype, it plans to quickly progress to full-scale production of its reactors. In the meantime, it will use the virtual twin and 3DEXCITE’s commercial content generation capabilities in the 3DEXPERIENCE platform to deliver an immersive virtual experience of XAMR and share its progress with potential investors and customers.
“3DEXCITE is incredible when you want to show a concept that doesn’t exist yet,” Alexandre said. “Until we’ve built the XAMR, it’s hard to convey what exactly we’re working on and how we’re doing it. These realistic representations of the reactor are key for communicating to our partners, stakeholders, investors and customers what they’re investing in and the journey we’re on.”
And that journey doesn’t end once NAAREA successfully builds its reactors. The company intends to manage XAMR throughout its entire lifespan, covering everything from transport and on-site delivery to implementation, training, security, insurance, operations and maintenance, all the way through to neutralizing each micro generator and managing its end of life. NAAREA intends to be a full-service provider. Its customers will simply pay for the energy they use. At the heart of this strategy is the virtual twin.
“From the beginning, I knew we needed to develop our product within an integrated virtual environment where everything is linked,” Alexandre concluded. “Our vision is to use the virtual twin for everything, from sourcing the fuel and creating the molten salt to building, installing and operating the reactor; it’s the cornerstone of our entire development plan. We’re a game changer, and so is Dassault Systèmes and the virtual twin. Having them onboard brings a great deal of credibility to what we’re trying to achieve and will help us get there faster.”
Discover more about the Engineering Excellence industry solution experience.
Discover more about the Capital Facilities Information Excellence industry solution experience.
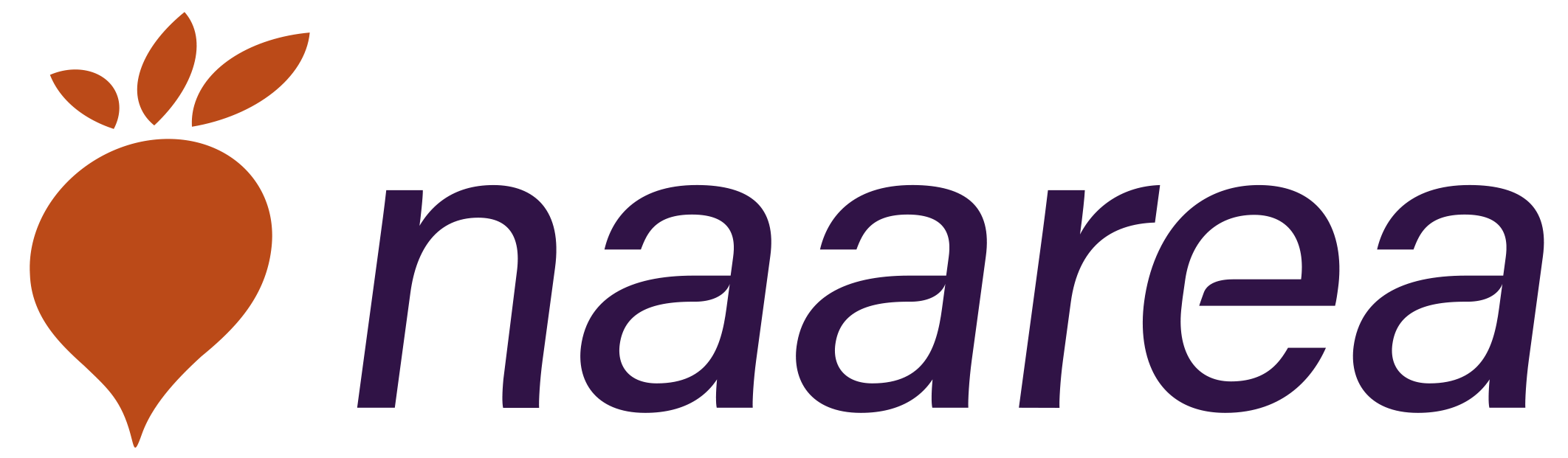
Focus on NAAREA
NAAREA is a pioneer in fourth-generation micro-nuclear power and the inventor of XAMR. Through science and innovation, NAAREA is contributing to the advent of a safe, decarbonized, circular, non-intermittent, decentralized and economical energy solution produced from industrial waste, which broadens the scope of renewable energy. Its vision aligns with the 17 United Nations Sustainable Development Goals and is based on the conviction that the climate is our heritage and that in order to protect our planet and our species, a major evolution is necessary to break the energy deadlock and decarbonize our future.
For more information: https://www.naarea.fr
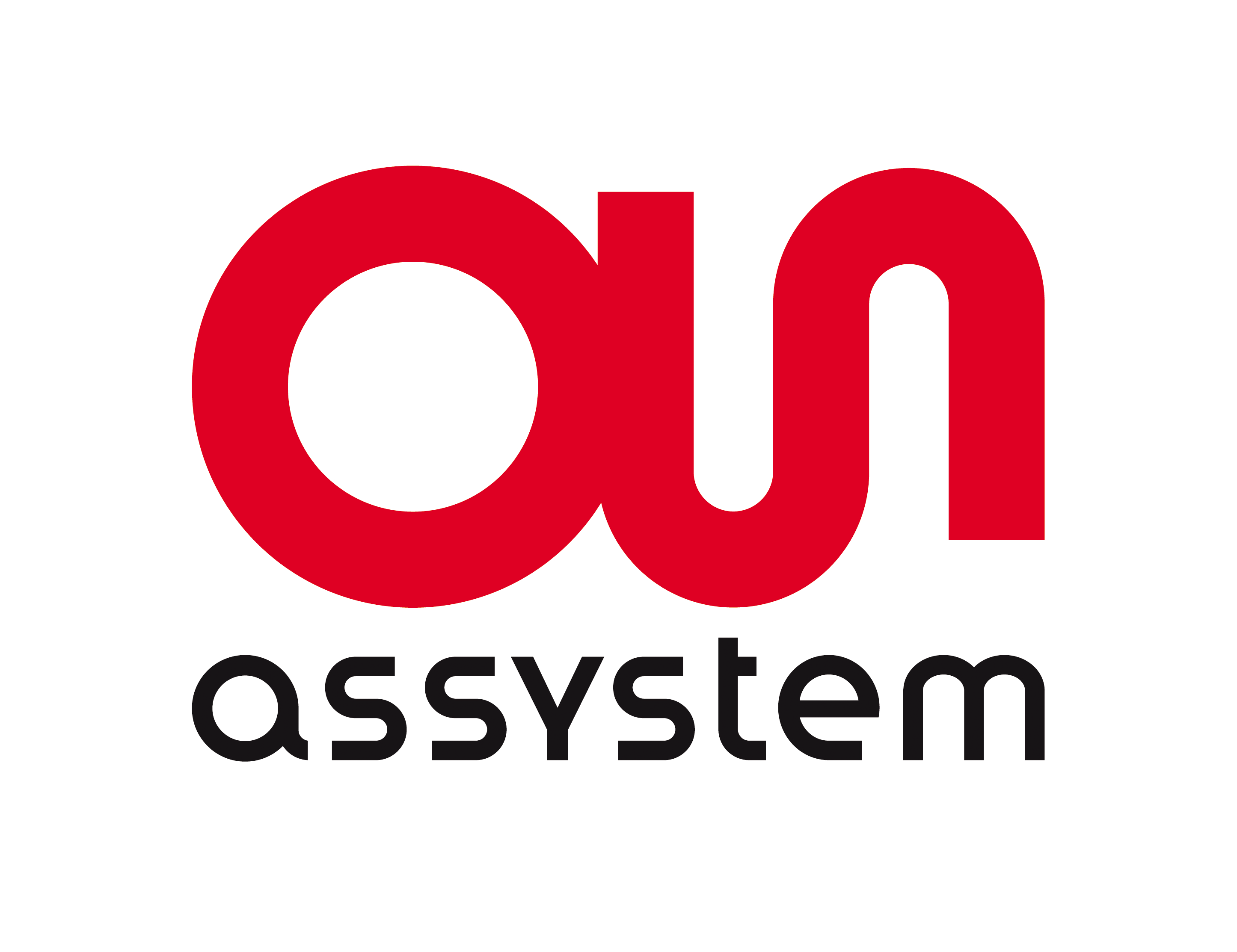
Focus on Assystem
Assystem is an independent, international company with one key mission: to accelerate the energy transition throughout the world. Drawing on more than 55 years’ experience in highly regulated sectors subject to strict security and safety requirements, Assystem provides its customers with engineering and project management services, as well as digital services and solutions to optimize the performance of complex infrastructure projects throughout their lifecycle.
For more information: https://www.assystem.com