Musashi Seimitsu Industry
Japanese automotive parts manufacturer Musashi is developing the next generation of powertrains for electric vehicles. The company selected the 3DEXPERIENCE platform and its Bid to Win industry solution to speed up product development time, harness simulation to handle new complexities and continue to deliver high quality products.
Reimagining Powertrains
Musashi Seimitsu Industry, an automotive parts manufacturer based in Japan, recognizes that one day, electric vehicles (EVs) will eclipse the internal combustion engine and is readying itself for when that happens. The company’s goal is to retain its leading position in the industry developing unique, innovative powertrain products that achieve “power-to-value” and are optimized for the current and next generation of cars.
“Automobiles are in an age of great transformation,” said Hiroshi Otsuka, president and chief executive officer of Musashi. “As major changes take place, whether it is in electrification or connectivity, the parts that are being engineered for conventional cars and new automobiles are changing too. Demand for traditional transmissions will diminish, but other parts for the motor, such as gear units—one of our specialties—will continue to exist. That’s why we intend to make reduction gears, which are required in the age of electrification. We want to become the number one supplier in the world of transmissions, gears and other items in which we excel.”
As it adapts for success in the age of electrification, Musashi has a unique opportunity to develop a new generation of powertrain parts optimized for EVs. “Regenerative brakes allow energy to be recovered during breaking,” Otsuka said. “For electric vehicles, there will be many changes in the strength requirements of the gears. So, even if the gears are shaped the same, their technology needs to be made suitable for the age of electrification. We do our best to carry out such development.”
With more combustion engines being switched for quieter running battery-powered vehicles, the company must also rethink the inherent properties of its parts to overcome two big obstacles: noise and weight. “One of our development projects is to create quiet gears that don’t make noise,” Otsuka said. “Current electric vehicles are heavy due to their batteries. Going forward, there is going to be an increasing demand in technology to lighten the vehicles and to make them more compact.”
To maintain its competitive edge and enhance its in-house research and development (R&D) capabilities, Musashi is increasing its global presence through partnerships and acquisitions. At the same time, a digital transformation is underway as the company seeks to streamline and integrate its global R&D and production data, improve operational efficiency and accelerate product development. Its implementation of Dassault Systèmes’ 3DEXPERIENCE® platform has been critical to achieving this.
“An integrated system like the 3DEXPERIENCE platform is now an essential requirement,” Otsuka said. “We needed something that matched the technological capabilities of our customers, like simulation software. The platform allows us to capture and store our internal knowledge and efficiently share and connect it all, as well as offer a service that enhances and deepens our contact with customers.”
The 3DEXPERIENCE platform is definitely essential. We want to be a company that can compete well in the world and survive. Solutions like this are indispensable for that.
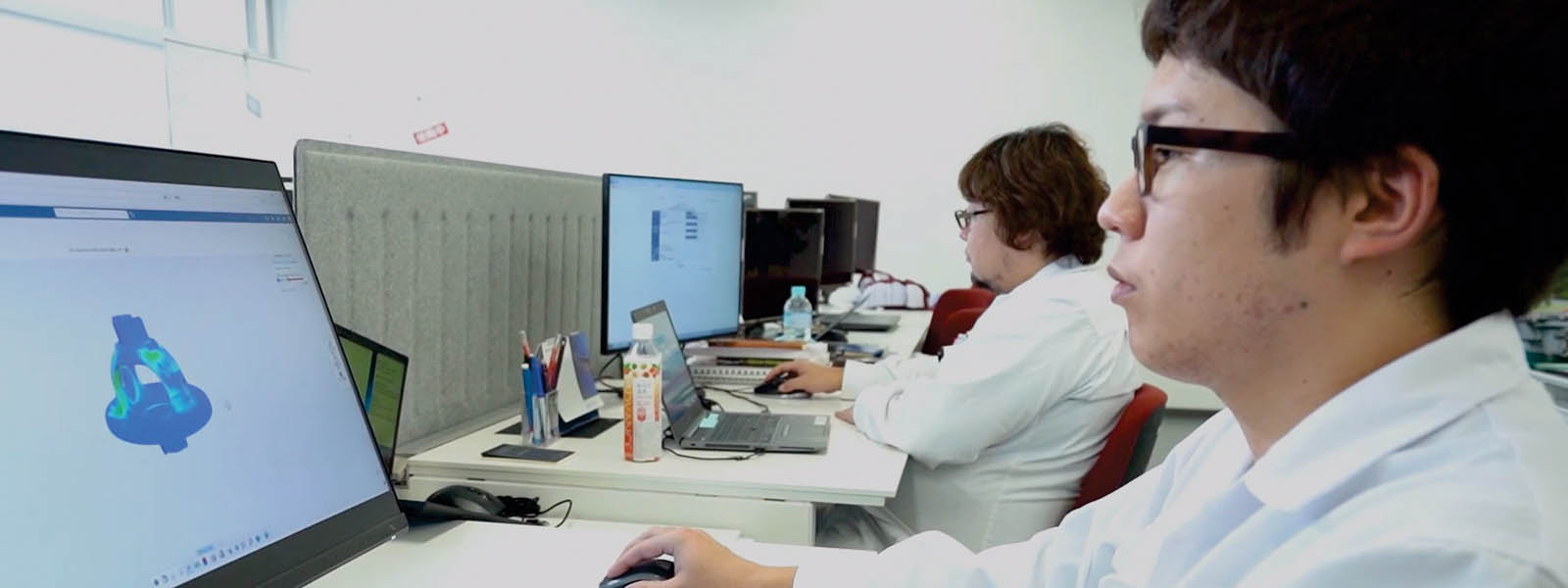
Centralized knowledge base
Before implementing the 3DEXPERIENCE platform, Musashi’s R&D and design capabilities were reliant on individual expertise, and knowledge sharing across the company was an impossible task.
“In our case, our technology expertise is often aligned with our human resource talent,” Otsuka said. “There is naturally a difference in knowledge between a person with 10 years’ experience and a new employee. Therefore, I have been always interested in how people can visualize their experiences and share it with their team. We must also find ways of better connecting our global development teams. To do this, the deep knowledge within our talent has to be made into a visible system, not just a collection of phone calls and e-mails.”
Musashi is using the 3DEXPERIENCE platform to capture this essential knowledge and share it more widely across its teams. This not only helps to improve internal expertise, but also to harness the power of collaboration. “Development is not something that is carried out just in Japan,” Otsuka said. “Development is carried out all over the world. We have developers in the United States, China and elsewhere, and they must be connected laterally.”
With a unified knowledge base, Musashi’s team now pools their expertise and focuses on innovation. “We are enhancing our skills and doing what we can to stay ahead of the competition,” Otsuka said. “As new technology is constantly being developed, we must learn how to take advantage of it. We want to innovate, and innovation only results from embracing change.”
“Much of the work that we were involved in before was dependent on individual skills,” added Takahiro Sakuma, group manager of the CAE Research Group in the R&D Division at Musashi. “Now, we save everything on the 3DEXPERIENCE platform, from upstream requirements to how they incorporate the requirements into functions. Our knowledge is collected in one place and this database of information will lead to future innovation.”
Processes are now standardized across the company too, thanks to the ability to create templates and log best practices on the platform. “Using ENOVIA project management on the 3DEXPERIENCE platform, we’ve created a template of operations and nothing is ever left out,” Sakuma said. “Before, design operations had different flows and tools. Now, we use the 3DEXPERIENCE platform to connect all processes between design and computer aided engineering (CAE). The sharing of information is going well and helping to increase operational efficiency.”
Musashi’s designers and engineers in different departments and locations are now able to work together more effectively and collaborate efficiently throughout the product development cycle. “In the past, it wasn’t possible to know exactly how much work others had already done if they weren’t in the same division as you,” Sakuma said. “Now, we can see it under product management; we’ve built connections with others. We have also found the platform invaluable for managing requirements. By sharing how much is required, we can see what we need to do. In the past, project management wasn’t carried out on one system. So, we were not really sharing what was going to be done or how much progress had been made. By managing all our projects on the 3DEXPERIENCE platform with ENOVIA, we share information and see the progress we’re making.”
“It is now possible for the whole R&D division to use accurate data,” added Yuta Kosugi, member of the CAE Research Group at Musashi. “I think this will promote even more collaboration between groups.”
Digitally validating designs
One of the main reasons Musashi chose the 3DEXPERIENCE platform is because of its ability to support the CAE tools its workers are already familiar with. Connected operations and tools are leading to improved project oversight across disciplines as well as enhanced analysis—critical for the company as it develops new cutting-edge products.
“In addition to using apps like project management to obtain an understanding of the work that other members are doing, I also use apps for analysis to carry out validation of the structural analysis of our products,” Kosugi said. “What I like the most about the 3DEXPERIENCE platform is that we can link things like CATIA designs with analysis data.”
Because all systems run from a single platform, data sharing and analysis has become seamless. “Before, we exchanged data via a file server,” Kosugi said. “However, by using project management and other 3DEXPERIENCE platform apps, we exchange data on the platform efficiently. I think that’s the function I am pleased with the most.”
Using CATIA for design and engineering and SIMULIA for realistic simulation on the 3DEXPERIENCE platform, designers and engineers make changes to a new product design at any stage of the process and use virtual testing and simulation to validate the part in detail—checking information such as bore distortion, bending stiffness, load distributions, stress fields and fatigue safety factors. This has reduced the need for physical prototypes and tests, helping to speed up the development process.
“As for CATIA, we created a mechanism that uses parameters to generate shapes straight away,” Sakuma said. “We then use the 3DEXPERIENCE platform to connect it to simulations. We have created a system that enables designers to easily carry out analysis. Before, when changes were made to the continuity of data or shapes, another step was required to handle these amends. Now with the 3DEXPERIENCE platform, we can easily carry out analysis even after changing shapes.”
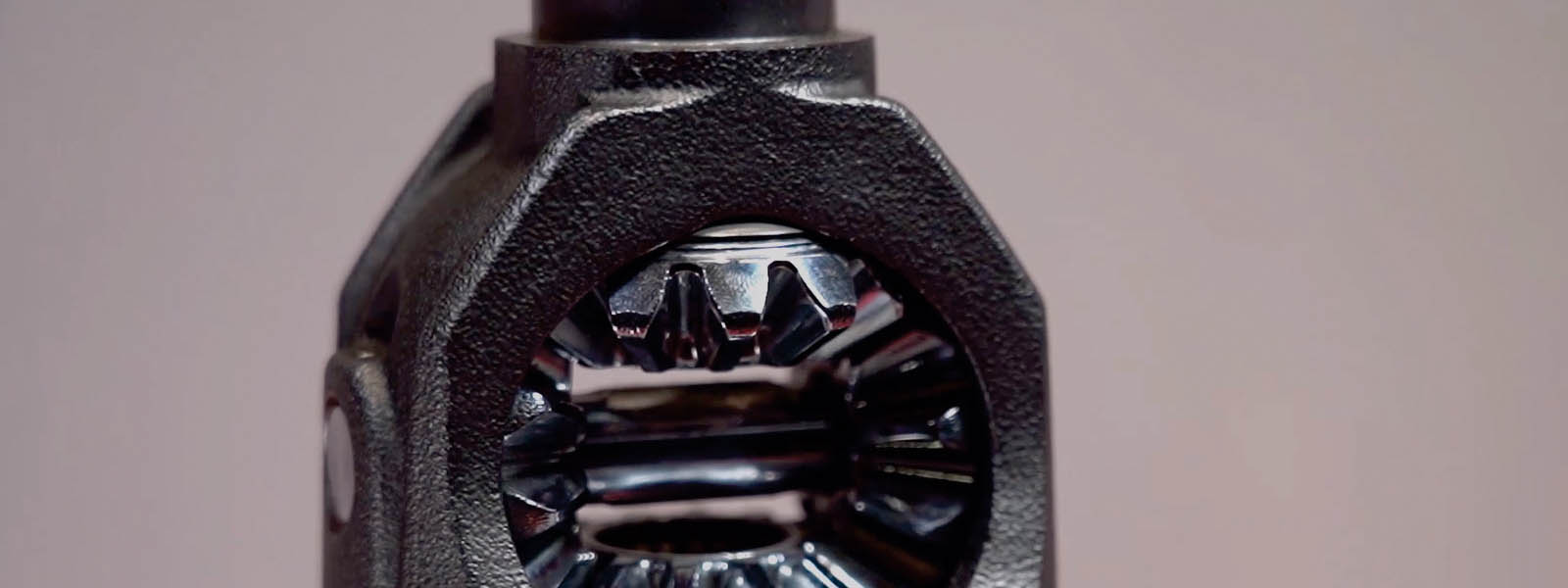
Speeding up R&D
Backed by the 3DEXPERIENCE platform, Musashi can concentrate on accelerating its product development to keep up with its clients’ demands as the manufacturing lifecycle for new cars continues to shorten. “Up to now, it would take about five years to develop a new car,” Otsuka said. “If it involved completely new technological mechanisms, it takes more like ten years. If there were any problems with a new model, it was fixed before new development proceeded. But technology is changing this and the development of an electric vehicle, which has no engine, takes only half that time. We want to halve the time it takes to develop a new car, and this requires extremely fast product development processes.”
Seamless links between CAD and CAE open the door for modeling and meshing automation, and simulation-based design optimization. It means that reworking designs from scratch is now a thing of the past. “As for the speed of development, we are emphasizing the use of the latest technology to accelerate it,” Otsuka said. “What used to take the most time in development was the process of making physical prototypes and testing them. Using today’s technology and replacing that process with a virtual step shortens our development time considerably. That is the direction we are taking.”
Using the project management feature of the 3DEXPERIENCE platform, we’ve created a template of operations and nothing is ever left out.
A truly global competitor
Otsuka believes that as the automotive industry continues to evolve, technology platforms like the 3DEXPERIENCE platform will no longer be a nice to have, but a must have.
“Going forward, we’re going to be in a world where a company can’t survive without virtual modeling and simulation technology,” he said. “Not having a platform that can be used in every country would have a huge impact on competitiveness. The 3DEXPERIENCE platform is definitely essential. It will soon be something that everyone has—something that they couldn’t compete without. We want to be a company that can compete well in the world and survive. Solutions like this are indispensable for that, and the rest will be up to us—how well we can make full use of them.”

Focus on Musashi
Musashi Seimitsu Industry is a global automotive and motorcycle parts manufacturer supplying global OEMs and Tier 1 companies worldwide. Headquartered in Toyohashi, Japan, the company has 33 manufacturing sites across Europe, North and South America, China and South East Asia producing automotive powertrains and components, transmission gears, camshafts and other drive parts for motorcycles.
For more information: www.musashi.co.jp/en