Achieving sustainable growth in engineering, procurement and construction management
Information is often considered to be an organization’s most valuable asset. But simply having data isn’t enough. What’s most important is how that data is made available to employees so that it can be maximized.
The executives at India-based L&T Energy Hydrocarbon (LTEH) – an engineering, procurement and construction (EPC) company providing integrated ‘design to build’ solutions to large and complex hydrocarbon projects worldwide – know this only too well. While they were amassing data at breakneck speed, it was held in 27 different home-grown applications and systems that had little to no integration. This was hampering productivity and impeding effective collaboration.
Since everything the company does is custom built, there are no standard processes. LTEH receives the front-end engineering design principles from the client which provides the preliminary scope of work. It’s up to LTEH to design and deliver all materials on time and on budget while adhering to various health and safety and sustainability requirements.
“The non-standard nature of our business meant that, over a period of years, our information repositories spiraled out of control,” said Atul Paranjape, LTEH’s vice president of group digital and IT. “Each time a client came to us with a new requirement for their project – for example, to produce a specific amount of energy from a wind farm – we developed a system for it. Before we knew it, those systems had multiplied. This made it challenging for our business executives to generate accurate reports. They were scrambling for information and comparing irreconcilable systems.”
As the industry became increasingly cost-centric, LTEH realized it needed to improve its productivity to retain its leading position. To do this, it was necessary to connect its different data silos for more in-depth insights into developing, planning, building, operating and decommissioning projects.
We are no longer wasting time searching for information – everything we need is instantly accessible in the platform in a standardized format, saving us around 20% of working time.
The search for a unified solution
LTEH wanted a comprehensive data management system that pulls information from its multitude of applications and applies business intelligence and analytics to a virtual twin of its various projects. It also wanted a collaborative workspace where relevant stakeholders can plan together, share and view project progress, make updates, manage changes and minimize risks. By enabling more efficient, data-driven management of its operations, LTEH believed it could deliver cost-effective projects, achieve better circularity of materials and drive a more sustainable operation.
Recognizing that creating its own data management system would be time- and resource-intensive, LTEH sought an established platform to build upon. “After reviewing various options, we decided to use Dassault Systèmes’ 3DEXPERIENCE platform on the cloud,” Paranjape said. “It was already used by our defense and shipbuilding businesses, so we knew it was flexible and agile enough to accommodate our evolving requirements. That was important to us since our project needs are changing all the time.”
The 3DEXPERIENCE platform helps LTEH to track, measure and predict project progress more accurately.
Connecting the dots
LTEH’s evolving needs were also considered during Dassault Systèmes’ ongoing value engagement process – a practice that not only demonstrates the value of the 3DEXPERIENCE platform on the cloud, but formalizes the shared actions that need to be taken for LTEH to achieve its goals. The value engagement process comprises four key steps:
Assessment: The first step involved Dassault Systèmes and LTEH work together to identify the key business needs that serve to justify the implementation. This included developing a thorough understanding of LTEH’s existing data silos and assessing which could be integrated into the new platform.
Definition: By analyzing LTEH’s existing business processes, LTEH’s priorities were defined. To support accurate planning and monitoring across all phases of its projects, LTEH needed to have data that was accurate and easy to visualize in real time.
Commitment: Here, Dassault Systèmes demonstrated exactly what could be achieved with the 3DEXPERIENCE platform on the cloud, proving the value of the implementation: that actionable insights lead to informed and efficient decision making.
Delivery: Dassault Systèmes’ engineers then worked together with LTEH’s R&D team to implement the solution and execute the plan, delivering on-site training along the way. Implementation began with the integration of schedules and customized dashboards.
For LTEH, the value engagement process is not a finite process – it’s an ongoing collaborative approach. “In a business like ours, it’s not a case of simply finalizing a list of specifications that are then delivered on,” Paranjape said. “That’s why we really appreciate Dassault Systèmes’ approach to value engagement, a continuous process, constantly assessing how our requirements are evolving, how the technology is transforming and what new opportunities are out there for us.”
The 3DEXPERIENCE platform supports immersive virtual reality reviews where LTEH’s customers can do checks via virtual walkthroughs.
A multi-dimensional twin for EPC projects
Today, LTEH has established a common digital thread across all its systems with the 3DEXPERIENCE platform on the cloud. Its NETVIBES dashboards configured to meet its data science requirements ensure that progress is tracked in a contextualized 3D virtual twin of its projects. LTEH can now provide immersive virtual reality reviews for its customers, enabling them to “walk” through the virtual twin of their construction works, for example, to check for clearances and issues.
“Every project we do includes multiple dimensions which we have added to our virtual twin,” Paranjape said. “We started by adding time to create a 4D experience. Then we added budget as a fifth dimension. Other critical dimensions such as safety, quality and collaboration followed so we can visualize, measure and predict progress in each of these dimensions. We call it a multi-D twin.”
As a result, the company’s virtual twin represents much more than a collection of assets. “This is not an asset twin, it is a project twin,” Paranjape said. “The schedule acts as the foundation, but we then add all our operational transaction systems such as manufacturing, supply chain and costing. All of these feed into the virtual twin model and we see everything in a 3D context, with dashboards to show progress.”
The data will help us to identify bottlenecks and potential delays, providing an early warning if we are about to miss a major milestone. Overall, this will ensure timely and well-informed decision making and effective collaboration.
Democratizing data
Now all employees, teams and stakeholders can collaborate in real time and access a single source of accurate project data. “We’ve gone from 20 users to 400 users in just a few months,” said Neerav Mehta, the company’s joint general manager for project control and digitalization. “That’s thanks to in-depth training in areas including constructability simulation, data science experience and predictive analytics.”
Employees can access KPIs captured from project schedules, enterprise resource planning (ERP) systems and LTEH’s in-house applications that interact with end users to capture deep data for EPC projects. The company uses ENOVIA to collaborate, for example in monitoring project progress, issue management and profit margins.
The on-cloud direct and secure access to all information brings much needed speed and accuracy to decision making. “Our previous on-premise implementations weren’t giving us the speed we needed, and we were reluctant to go with public cloud at first since data science was always on private cloud,” Paranjape said. “But Dassault Systèmes demonstrated a proof of concept which convinced us. Now that we’ve migrated our data onto cloud, we’ve discovered that we can operate in near real time with no lag. We can also receive updates to the solution immediately – we don’t have to wait for updates.”
The entire value stream is benefiting. “We are no longer wasting time searching for information – everything we need is instantly accessible in the platform in a standardized format, saving us around 20% of working time,” Paranjape said. “Because the dashboards present information to our executives in an easy-to-digest format, they can make decisions much faster – and that dramatically improves productivity across the whole business.”
All of these benefits are transforming the customer experience. “By expediting all of our business processes, our response times have improved,” Paranjape said. “Also, because the 3DEXPERIENCE platform is a multi-CAD solution, it means we can work seamlessly with any customer’s engineering team, no matter what products they use. We can import 3D models with metadata from any CAD platform, and we can also export to whichever solution our customer prefers, without any loss of accuracy.”
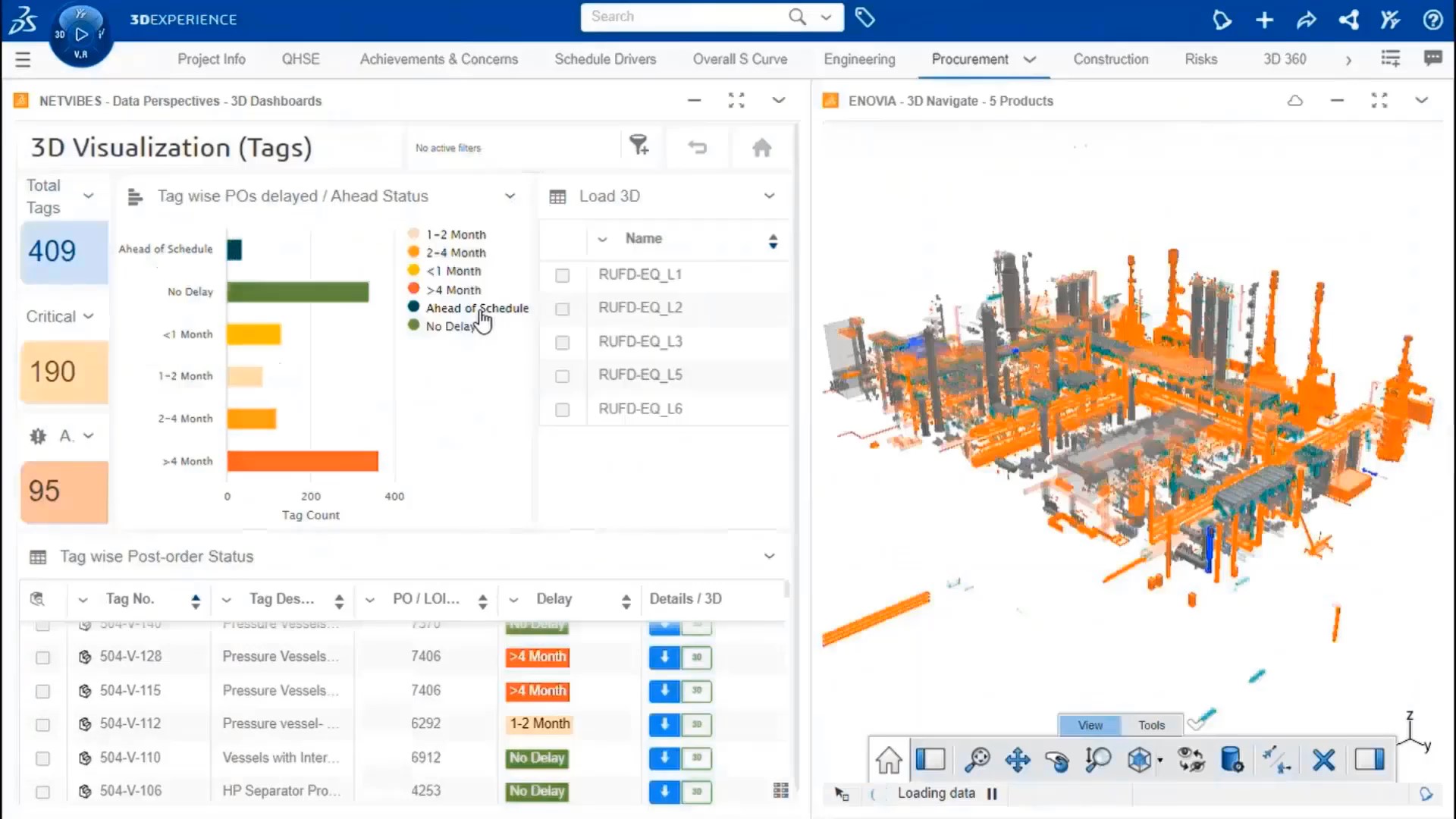
A foundation for a better future
The next stage of the project is to go beyond reporting by adding predictive analytics into the mix. To achieve this, Dassault Systèmes is working alongside LTEH to extract knowledge from past projects to proactively make accurate predictions for the future. “This will allow us to understand not only what has already happened, but to predict what might happen next,” Paranjape said. “We’ll be able to pinpoint issues and make adjustments to correct a problem before it occurs, for example.”
“The data will help us to identify bottlenecks and potential delays, providing an early warning if we are about to miss a major milestone,” Mehta said. “Overall, this will ensure timely and well-informed decision making and effective collaboration.”
LTEH also hopes to get to a position where it can pass on virtual twins of current projects to its customers. “Passing on the virtual twin will give them a foundation for growth and help them future-proof their business in the same way that we are doing for our organization,” Paranjape said. “This is a massive win – it demonstrates that we really care about our clients’ future.”
For a better understanding of engineering, procurement and construction management
EPC stands for engineering, procurement and construction.
Engineering, procurement and construction (EPC) generally covers the full lifecycle of a project. This means an EPC company will generally be responsible for the full project management, working closely with key players in the construction industry.
The engineering stage includes initial designs and scoping works. The procurement stage involves the purchasing of all necessary materials. The construction phase covers the final build.
Discover more about the Capital Facilities Information Excellence industry solution experience.
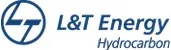
Focus on L&T Energy – Hydrocarbon
Established in India in 1939, L&T Energy – Hydrocarbon caters to the entire hydrocarbon value chain covering the oil and gas processing, petroleum refining, chemicals and petrochemicals, and fertilizer sectors. Over recent years the company has consistently demonstrated timely project delivery deploying end-to-end capabilities, including design, fabrication and installation of large process platforms, living quarters, subsea systems, piping and other transportation and installation works. The company is a wholly owned subsidiary of Larsen & Toubro Limited (L&T), a US$21 billion technology, engineering, construction, projects, manufacturing and financial services conglomerate.
For more information: https://www.lnthydrocarbon.com/