LM Wind Power
Wind energy’s contribution to mitigating greenhouse gas emissions cannot be overstated. Many variables need to be addressed when designing wind turbines. The persistent challenge of noise and noise regulations can be a limiting factor that constrains turbine operation, diminishes power output and increases production costs. LM Wind Power and Dassault Systèmes are engaging in a collaborative effort to pioneer simulation methods to address these challenges. Learn how they are using a combination of low- and high-fidelity simulations, harnessing the advanced capabilities of the SIMULIA PowerFLOW solver to enhances the precision of wind turbine blade design.
The significance of wind energy in mitigating greenhouse gas emissions cannot be overstated. However, the persistent challenge of noise, particularly the bothersome swishing sound associated with onshore wind turbines, poses a significant obstacle. Stringent noise regulations have been a limiting factor, constraining turbine operation, diminishing power output and inflating production costs. The adoption of larger rotor diameters in wind turbine designs has introduced its own set of challenges, coupled with increased prototyping costs. The presence of aerodynamic noise, influenced by factors such as rotational speed and the intricate design of turbine blades, further exacerbates community disturbances.
In response to these challenges, a collaborative effort between LM Wind Power and Dassault Systèmes has been underway to pioneer a simulation methodology to design optimal blade serrations specifically geared towards reducing trailing-edge noise in full-scale wind turbines. The crux of this initiative is developing a cost-effective simulation framework capable of accurately predicting noise emanating from two-dimensional blade sections when extrapolating to a full-scale wind turbine. This innovative approach bypasses the need for resource-intensive and expensive wind tunnel and field tests.
The methodology devised for this purpose leverages a combination of low- and high-fidelity simulations, harnessing the advanced capabilities of the SIMULIA PowerFLOW solver. This integrated approach enables the accurate prediction of noise levels over vast distances across complex terrains, covering kilometers of ground. The collaborative effort between LM Wind Power and Dassault Systèmes has culminated in a groundbreaking solution that not only addresses noise concerns but also circumvents the traditional challenges associated with wind turbine design.
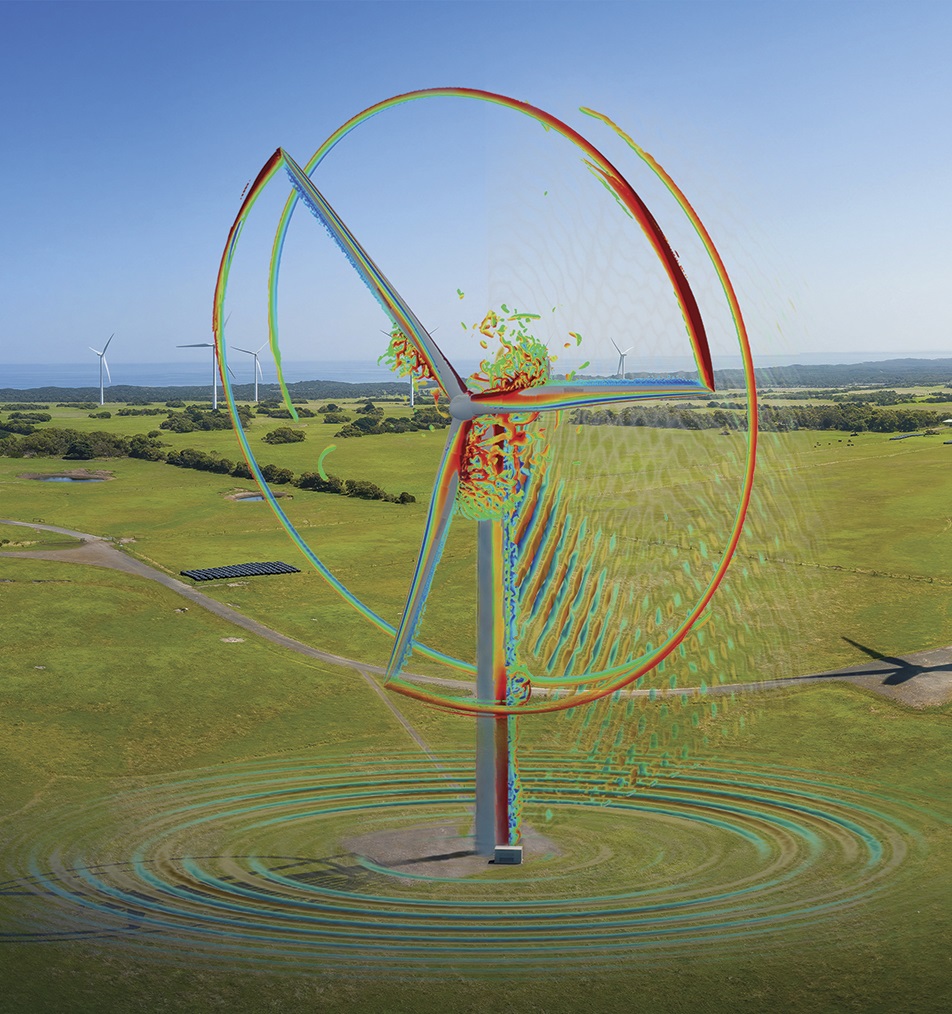
Crucially, the efficacy of this solution has undergone extensive validation through rigorous field tests. Guannan Wang, SIMULIA Champion and the lead acoustic engineer on this project, expressed the transformative nature of this achievement, stating, "This marks a new era for virtual prototyping and digital twin design, eventually leading to digital noise certification of wind turbines for us." This breakthrough signifies a pivotal shift towards a more sustainable and technologically advanced future in the realm of wind energy, where digital simulations play a central role in optimizing performance while minimizing environmental impact.
This marks a new era for virtual prototyping and digital twin design, eventually leading to digital noise certification of wind turbines for us.
Challenge
Stringent noise regulations are enforced by governments for wind turbines. LM Wind Power, a prominent player in the wind energy sector, specializes in designing and optimizing wind turbine blades for a range of Original Equipment Manufacturers (OEMs). Their primary focus is on enhancing both performance and reducing noise emissions to drive down the overall cost of energy production. Despite being a leading blade manufacturer, LM Wind Power faces challenges testing their blades due to limited access to operational wind turbines.
Moreover, the conventional approach of physical testing is beset by drawbacks such as high costs, logistical challenges and a reliance on weather forecasts, leading to frequent delays. These factors collectively make the process cumbersome and less efficient in achieving timely and cost-effective results.
Solution
The introduction of a digital twin replicating the full-scale wind turbine provides a rapid and efficient avenue for executing design iterations and modifications. This virtual representation facilitates continuous testing within a comprehensive virtual wind tunnel environment, eliminating the need for oversimplifications. The simulation has been thoroughly validated through real-world field tests, demonstrating its remarkable accuracy. Utilizing SIMULIA PowerFLOW, the airflow and resulting noise emissions are meticulously studied, enabling the generation of an auralized noise signal on realistic terrain. This functionality proves invaluable in supporting design studies for noise-suppression add-ons.
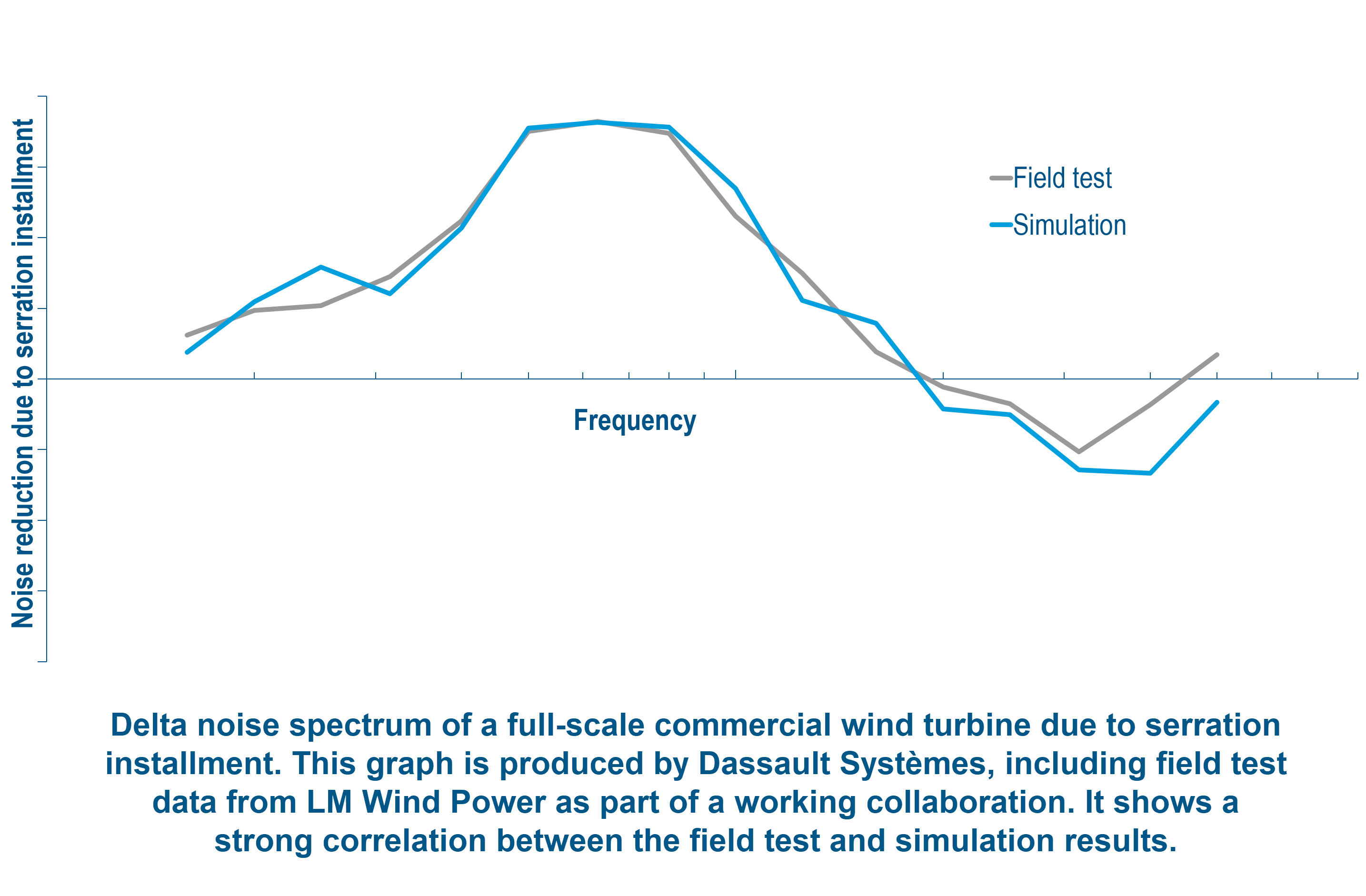
Benefits
- Optimized Blade Shapes: Streamlined access to an unlimited and controlled digital wind tunnel empowers the optimization of wind turbine blade shapes. This avoids the need for field tests and ensures precision in design adjustments.
- Efficient Design Iterations: The digital twin framework allows for swift design iterations, facilitating quick adjustments and modifications. This agility contributes to faster turnaround times in the design process.
- Cost Reduction in Energy Production: By eliminating the reliance on traditional field tests and offering a more controlled virtual testing environment, the solution significantly reduces the overall cost of energy production.
- Compliance with Noise Regulations: The capability to auralize noise signals on realistic terrain aids in meticulous noise-suppression add-on design studies, ensuring compliance with stringent noise regulations.
In essence, this innovative approach enhances the precision of wind turbine blade design and offers a range of benefits, including cost-effectiveness, compliance with regulations and an accelerated design lifecycle.
Focus on LM Wind Power
LM Wind Power (“Company”), a GE Vernova business, is an industry-leading developer and manufacturer of high-quality rotor blades for onshore and offshore wind turbines with blade services solutions and a global manufacturing footprint, headquartered in Denmark. LM Wind Power has produced over 270,000 blades since 1978, corresponding to 152 GW installed capacity. As part of the Company’s sustainability journey, LM Wind Power became the first carbon-neutral company in the wind industry in 2018 and is committed to building Zero Waste Blades by 2030.