HYUNDAI HEAVY INDUSTRIES – ENGINE AND MACHINERY DIVISION
To strengthen its competitiveness particularly with dual-fuel engines, Hyundai Heavy Industries - Engine and Machinery Division implemented the 3DEXPERIENCE platform to manage everything from design to manufacturing.
Building eco-friendly engines for the marine industry
International shipping has set itself on a path to a zero-carbon emissions future. Targets drawn up by the International Maritime Organization (IMO), the United Nations agency responsible for regulating shipping, aim to reduce the industry’s greenhouse gas emissions by at least 50% compared to 2008 levels by 2050. The strategy, which supports UN Sustainable Development Goal 13, also calls for a reduction in carbon dioxide emissions by 40% by 2030, and 70% by 2050.
IMO’s vision is to phase out greenhouse gas emissions entirely within this century. The 2021 annual IMO symposium called for the industry to embrace new technologies, new fuels and innovation, adding that exciting research and development into low- and zero-carbon marine fuels is already underway.
One company leading the sustainability effort is Hyundai Heavy Industries – Engine and Machinery Division (HHI-EMD). Based in South Korea, it is one of the world’s largest marine engine manufacturers with a 35% share of the global marine engine market.
“In accordance with IMO regulations, HHI-EMD aims to become the world’s number one sustainable energy provider for ship propulsion and power generation for onshore power plants,” said An Kwang-hean, president & COO of Engine and Machinery Division. “IMO recently introduced stricter environmental regulations in the offshore industry and there has also been increasing pressure for eco-friendly energy in the onshore power generation facilities. To meet these demands and maintain the leading position in engine production, HHI-EMD is moving forward to develop the finest products, while investing in our technology development and production capacity.”
HHI-EMD, which has its own mid-sized engine brand HiMSEN, has recently shifted its attention to dual-fuel engines. These engines run on both liquid and alternative eco-friendly fuels such as liquefied natural gas (LNG), allowing them to run more efficiently and reduce pollutants.
“We’re seeing significant interest in alternative dual-fuel energy,” Kwang-hean said. “Using dual-fuel engines can reduce carbon dioxide, sulphur oxide and nitrogen oxide emissions noticeably compared to using diesel. As requirements for industrial decarbonization increase, dual-fuel engines are expected to make a significant contribution to the sustainable shipbuilding industry. That’s why we are focusing on this category and will continue to strengthen our position as an engine manufacturer specialized in eco-friendly business.” As HHI-EMD builds on its reputation as a world-leading engineering company specialized in engine development, it required a modern platform that would ensure continuity throughout the entire product development process, from engineering to manufacturing. It also needed to support three-way collaboration between HHI-EMD as the licensor, the licensee and ship owner, all of which are involved in engine decision-making. HHI-EMD found the answer in the 3DEXPERIENCE® platform.
“We have undergone a digital transformation to become a company with an engineering specialty,” Kwang-hean said. “As we expanded and developed the HiMSEN engine business, we found the need for systematic engineering collaboration with our licensees. We also needed to manage our data better.
Starting with our process innovation activities, we set up a new direction and strategy for implementation and deployed the 3DEXPERIENCE platform after reviewing the most suitable system that best aligned with our requirements.”
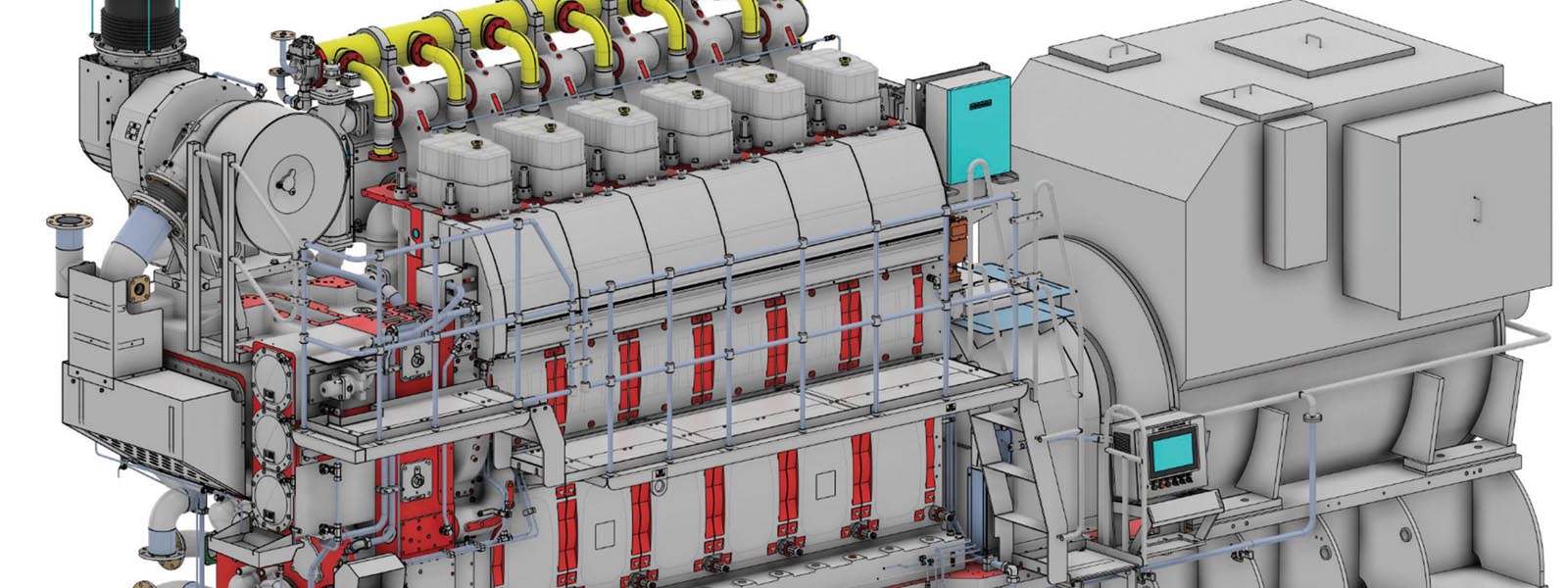
Going digital to gain competitive advantage
Today, the 3DEXPERIENCE platform plays a key role in helping the engine specialist manage its data effectively and operate efficiently to speed up product development, continuously enhance quality and drive costs down.
“With the help of the 3DEXPERIENCE platform, we transform the way we work within our business unit and innovate to continue offering our products at a competitive price,” Kwanghean said. “We can share accurate information with our team in a timely manner and it helped to implement a data-driven, fast-paced digital business environment."
Working within a single unified environment allows engineers to focus on the pursuit of technological innovation and solving new engine design challenges as they no longer have to spend time switching between different applications and converting data.
“When using the previous system, the coherence between design data and product data management data was low,” said Kim Seungmin, senior manager of Engine and Machinery Division. “Design data, including 3D, bill of materials (BOM), drawings and related documents, were managed in different systems, resulting in inefficiencies in the design process and difficulty accumulating know-how. Because of the inconsistencies in our design data between each system, it was difficult to make revisions, track changes and modify all impacted elements. The 3DEXPERIENCE platform manages all this in one place and has changed our approach for the better.”
With the help of the 3DEXPERIENCE platform, we transform the way we work within our business unit and innovate to continue offering our products at a competitive price.
Standardizing design for efficiency
Because HHI-EMD makes engines according to its customers’ unique requirements, the specifications of HiMSEN engines differ based on projects. As part of the implementation, HHI-EMD has transitioned the 3D models for its HiMSEN engines to CATIA to allow its engineers to work fully within the 3DEXPERIENCE environment and effectively manage all engine options and derived models.
“Our main users of the platform are design engineers, focused particularly on mass production development of the HiMSEN engines,” Seungmin said. “They use CATIA for 3D modeling as well as ENOVIA and DELMIA for managing specifications, engineering BOM, and manufacturing BOM. It was important for us to be able to handle everything within a single platform.”
Now, engineers use CATIA to design every facet of the HiMSEN engine and build a standard library of parts in ENOVIA.
“The entire engine model is created using the dedicated capabilities in CATIA for Mechanical Engineering,” Seungmin said. “And with the specific functionalities offered we can easily model pipes. For 3D modeling, we also made a template that suits each business unit to build a standard library of parts to help with decisions around dimensions and shapes.”
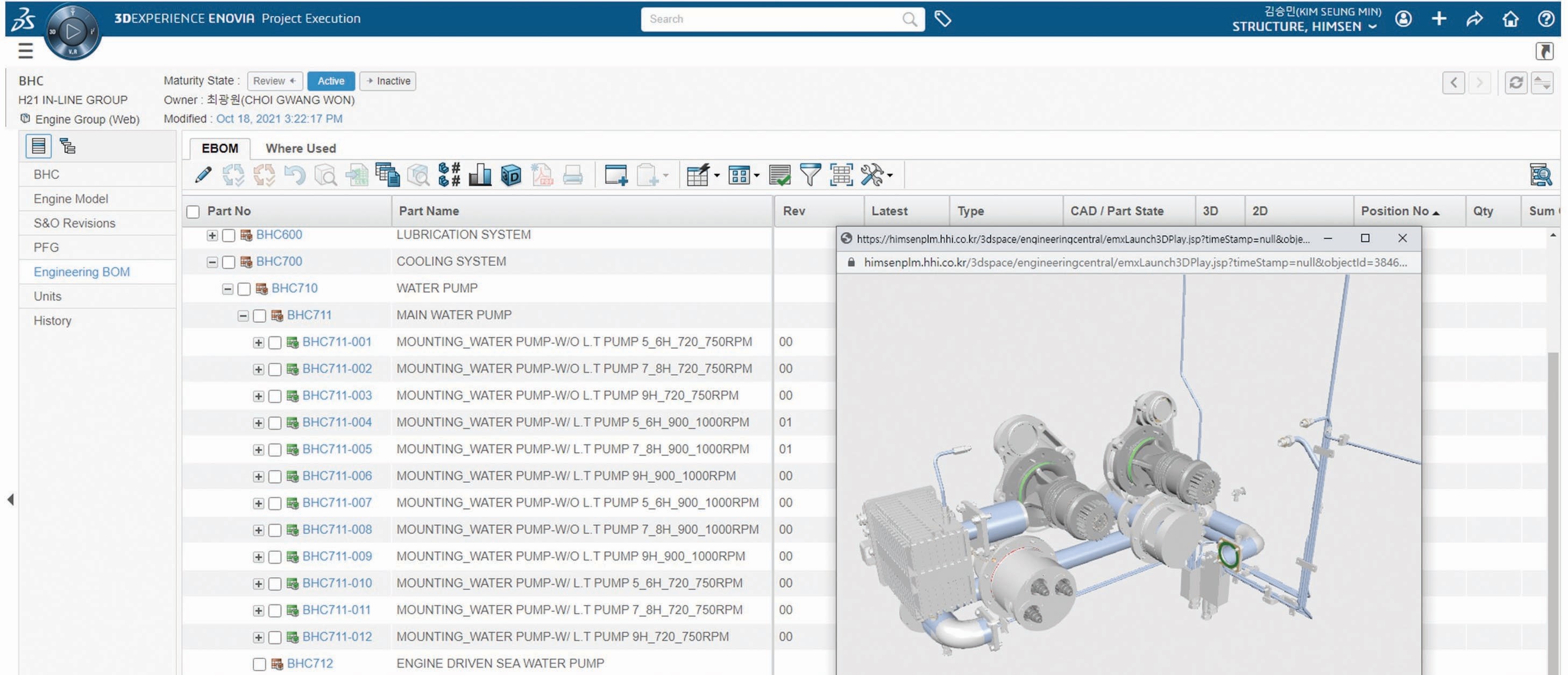
Automating BOM
HHI-EMD changed its working and design methodologies to get the most from the platform’s capabilities and work more efficiently.
“Adopting the 3DEXPERIENCE platform has allowed us to standardize our design methods and change our way of working to manage engineering data consistently and develop an engineering competence that meets global standards,” Kwang-hean said.
One area to benefit from this is the way in which engineers now generate the bill of materials.
“Before, we manually exchanged data between our CAD, PDM and in-house BOM systems,” Seungmin said. “All 3D models, 2D drawings and part list data from the CAD and other systems were sent to the BOM system after an internal approval. Then, after going through modification and manual inputs, the final BOM data was sent to the in-house enterprise resource planning (ERP) system. Now, we use DELMIA to generate the production BOM from the approved design engineering BOM to reduce errors. We can also make changes to a design and all associated drawings, models and BOM data automatically update too.”
As it sees the benefits of this approach, HHI-EMD is now looking at ways it can further achieve a seamless data flow across the entire product development lifecycle.
“We plan to extend the scope of BOM in our manufacturing process,” Seungmin said. “This will enable us to connect the specification and engineering BOM to the manufacturing BOM and achieve a consistent and trackable BOM management system.”
The company also uses ENOVIA to handle change management as efficiently as possible.
“We use ENOVIA’s change management capability to clarify what to change and attach all related documents,” Seungmin said. “Then, the model and BOM is approved and automatically revised. This entire process can be monitored through a personal dashboard.”
We can work in multiple windows simultaneously with different parts in real time within the platform.
Ongoing digital transformation
Taking advantage of the standardized workflows on the 3DEXPERIENCE platform, HHI-EMD has been able to seamlessly connect the dots across its product development processes, from design and engineering to manufacturing to ERP. As it grows its engineering competence and pursues new joint ventures, the platform will also enable HHI-EMD to collaborate seamlessly with new licensees and ship owners, from wherever they are in the world.
“We can work in multiple windows simultaneously with different parts in real time within the platform,” Seungmin said. “Our partners and customers can view 2D and 3D models on the web without having to open the CAD file. Also, when we share 3D models of large assemblies, they load much faster and this makes the process more convenient.”
In parallel with the platform implementation, HHI-EMD consulted Dassault Systèmes to develop a longer-term digital transformation strategy for its evolving business.
“The project confirmed that development time, production cost, commissioning and quality could all be improved by taking advantage of the latest technology in design, R&D, production and quality control,” Kwang-hean said.
Based on this, HHI-EMD has established a strategic digital roadmap for the next three to four years, covering 10 milestones.
“We currently have around 120 internal and external design engineers using the 3DEXPERIENCE platform,” Seungmin said. “Soon, we plan to introduce advanced planning and scheduling on the platform to strengthen our product development competitiveness and, ultimately, we plan to expand our use of the 3DEXPERIENCE platform to make our production site even smarter.”

Focus on Hyundai Heavy Industries – Engine and Machinery Division
Based in South Korea, HHI-EMD is the world’s largest marine engine builder with an approximate 35% share of the global market. As well as making its own brand of mid-size engines under the HiMSEN brand, the company is also a leading manufacturer and supplier of eco-friendly marine facilities and onshore energy plants including eco-friendly gas supply system Hi-GAS, NoNOx selective catalytic reduction system, and ballast water treatment systems.
For more information: www.hyundai-engine.com