Hyundai Everdigm
Korean heavy mobile equipment manufacturer Hyundai Everdigm serves the construction and civil engineering sectors with its fire trucks, concrete pump cars, hydraulic drills and more. The company migrated from its legacy PLM system to Dassault Systèmes’ 3DEXPERIENCE platform, using industry solution Digital Equipment Continuity to transform its product development, optimize its manufacturing operations and achieve a continuous data flow across the entire product lifecycle.
Customized heavy mobile equipment at scale
Popular in the construction and mining industries, Hyundai Everdigm’s E500 hydraulic drill combines high power and efficiency, making it ideal for tackling tough terrains. Engineered with a strong emphasis on quality and long-lasting performance, the machine’s design incorporates a powerful hydraulic system and fast, precise drilling to deliver a smooth, consistent operation, even in the most challenging conditions.
The E500 hydraulic drill is also the first product Hyundai Everdigm developed entirely on Dassault Systèmes’ 3DEXPERIENCE platform as part of a company-wide digital transformation. By taking advantage of Dassault Systèmes’ design and engineering solutions, Hyundai Everdigm reported greater efficiencies in the product development process as well as an improved design compared to previous models.
“We actively reflect the needs of our customers in the products we make for each country we serve, all while meeting the most stringent performance and quality standards,” said Yoo Jaeki, senior executive director at Hyundai Everdigm. “The E500 is our flagship export product. By designing the machine with Dassault Systèmes’ 3DEXPERIENCE platform, we reduced design time by about 20%.”
Digital renders of the E500 hydraulic drill generated on the 3DEXPERIENCE platform.
Engineering feats like this underscore Hyundai Everdigm’s commitment to customer-centric innovation and set the stage for ongoing advancements in customized heavy mobile equipment. Based in Korea, the company has built a strong reputation for delivering high performance hydraulic drills, fire trucks and concrete pump cars tailored to its customers’ unique, complex requirements.
“Our main differentiator is our customer-centered production system which gives us the flexibility to deliver truly tailored products,” said Lim Myungjin, CEO of Hyundai Everdigm.
Compared to most mass production models, Hyundai Everdigm’s custom approach might be considered more complicated, costly and time intensive, yet the company is finding ways to master this through digital transformation. One of the most significant steps it has taken is to move all its design and product lifecycle management (PLM) processes to the Dassault Systèmes solutions suite, using ENOVIA, CATIA, SIMULIA and DELMIA on the 3DEXPERIENCE platform. Its aim: to develop high-performing, innovative heavy equipment more cost effectively; mitigate errors at the production stage; and respond faster to complex customer needs.
Developing machinery in a robust CAD and PLM platform
After more than 10 years of using a computer-aided design (CAD) and a separate PLM system for medium-sized enterprises, Hyundai Everdigm was ready for change. Its legacy system struggled to manage large CAD assemblies, high volumes of design configurations for each piece of construction machinery, and the hundreds of part changes happening every day. This led to inconsistencies between design, the engineering bill of materials (EBOM) and the manufacturing BOM (MBOM).
“Errors in design and manufacturing data were driving up production costs, and it was hard for us to accurately estimate the cost of new projects as we didn’t have the insights we needed,” Yoo said. “We wanted to find a way of sharing up-to-date product information across the company in a timely manner. With its secure, integrated and scalable platform, Dassault Systèmes met our need for company-wide collaboration.”
Working with Dassault Systèmes and its business partner The One, Hyundai Everdigm set out a step-by-step implementation roadmap, covering three main phases. Phase one involved CAD and PLM transformation, covering data management, configuration management, EBOM and change management. In phase two, the company expanded to MBOM, routing, and work instructions with DELMIA. And in phase three it is harnessing integrated modeling and simulation (MODSIM) capabilities, new design functionality covering electric harness and piping design, as well as service BOM (SBOM) and spare parts management.
The One provides ongoing consulting, supporting the phased implementation of Dassault Systèmes’ applications, and delivering training and change management. Today, Hyundai Everdigm’s five business units – firefighting, concrete pumps, drillers, excavator attachments, and tower cranes – manage their CAD and PLM processes on the 3DEXPERIENCE platform.
“We’ve standardized our data management across the company while maintaining the uniqueness and efficiency of each team,” Yoo said. “The 3DEXPERIENCE platform gives us the flexibility to create and use independent workspaces. All stakeholders collaborate in one single environment, allowing us to share accurate product information across the company at the right time.”
Kinematics scenario of the E500 hydraulic drill on the 3DEXPERIENCE platform.
Connected heavy mobile equipment from design to production
Hyundai Everdigm transferred all legacy fire trucks, concrete pump cars, and hydraulic drill design data into the 3DEXPERIENCE platform. This is helping to track changes and design modifications for all heavy equipment, and accurately and efficiently generate the EBOM, saving significant time and cost.
“Previously, specification and variant management, design changes and compatibility reviews required a lot of manual, offline labor, which caused frequent errors,” said Hwang Unkyoo, team leader at Hyundai Everdigm. “Designers confirmed sales order specifications by email, put design data into the PLM, distributed drawings offline, and then notified relevant departments individually by separate emails or phone calls. Now, communication and product data is managed centrally so that EBOM configurations are verified in the planning phase, saving time and money throughout development.”
This continuous data flow carries through into production, meaning that each product is now managed as a single unified BOM. Using DELMIA, Hyundai Everdigm is working to automatically generate MBOMs and digital work orders that can be used on the factory floor. This makes it easier to manage custom specifications and plan production processes accordingly.
“With DELMIA, we resolved data inconsistencies by automatically generating MBOMs from a single-source BOM structure and linking EBOM and MBOM changes,” Hwang said. “The consistency of BOM data has improved by approximately 20% compared to before.”
Buoyed by this success, the manufacturer plans to generate the SBOM from the MBOM as part of its wider vision to transform the way it serves customers for the better. Having all this comprehensive information upfront will make it easier to create and share all technical documentation such as parts books and product manuals, and carry out predictive maintenance.
By leveraging MODSIM to run analysis in a platform environment, the simultaneous collaboration between the mechanical design and analysis teams was more efficient.
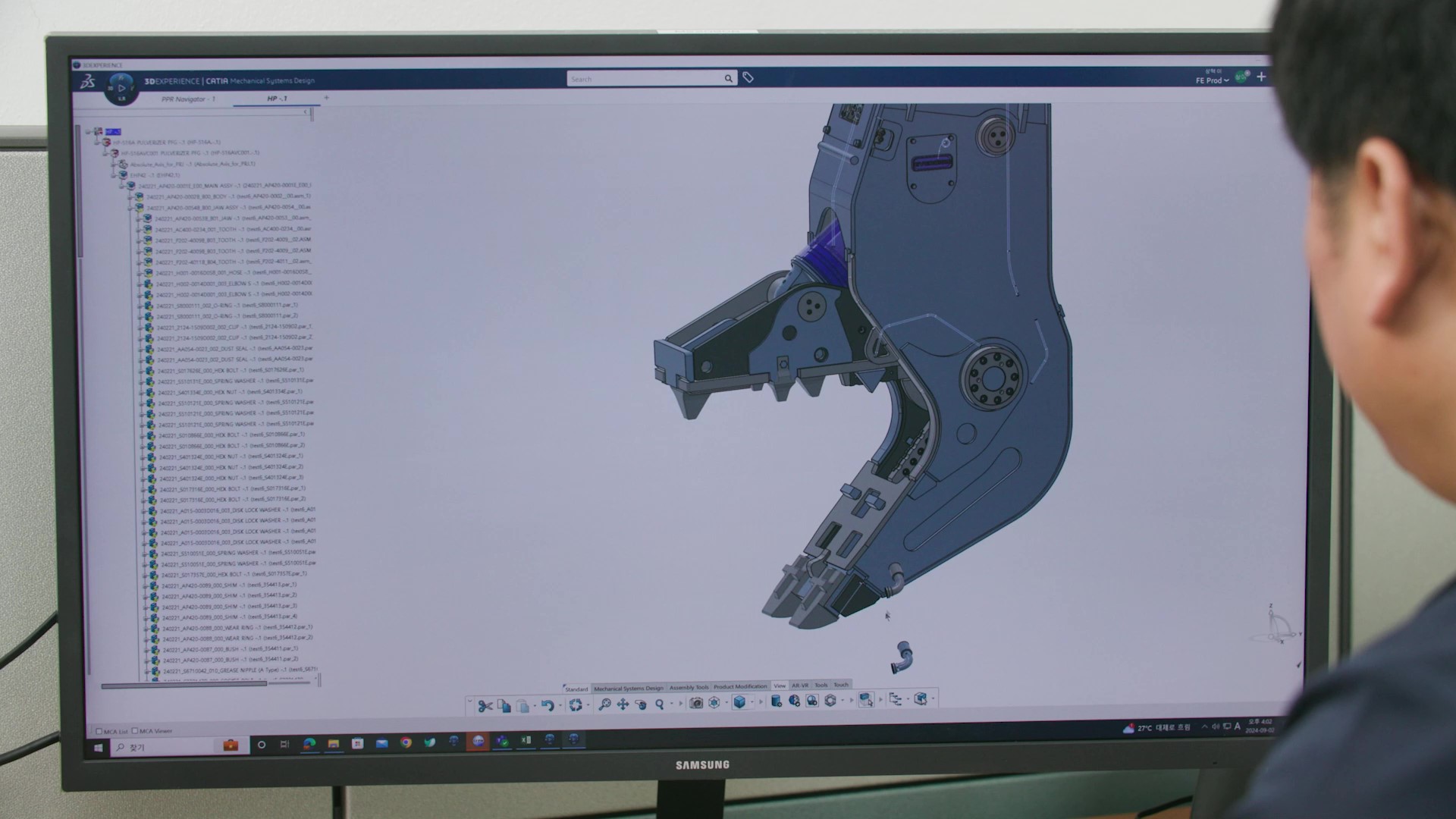
MODSIM speeds up development
Hyundai Everdigm is still part way through its digital transformation journey but is always looking to take advantage of new capabilities from Dassault Systèmes. Recently, the company concluded a MODSIM project, where mechanical engineers used Dassault Systèmes’ integrated design and simulation features in CATIA and SIMULIA to carry out structural and strength analysis on a fire truck’s base bracket and ladder.
The aim was to test the strength and safety of the base bracket with different loads on the ladder and come up with an optimal design. At the same time, the team wanted to see how it could work more efficiently within a seamless design-to-analysis collaboration workflow. Designers found they could more easily incorporate customer feedback into their work and quickly obtain analysis results to make iterative changes. Hyundai Everdigm is now applying this MODSIM approach to other projects.
“Previously, we did CAD and CAE simulations in different systems, making it difficult to incorporate design changes,” Hwang said. “The analysis process was time consuming with many iterations. By leveraging MODSIM to run analysis in a platform environment, the simultaneous collaboration between the mechanical design and analysis teams was more efficient. Being able to use both 3D design and structural analysis data has reduced overall development time by more than 30%.”
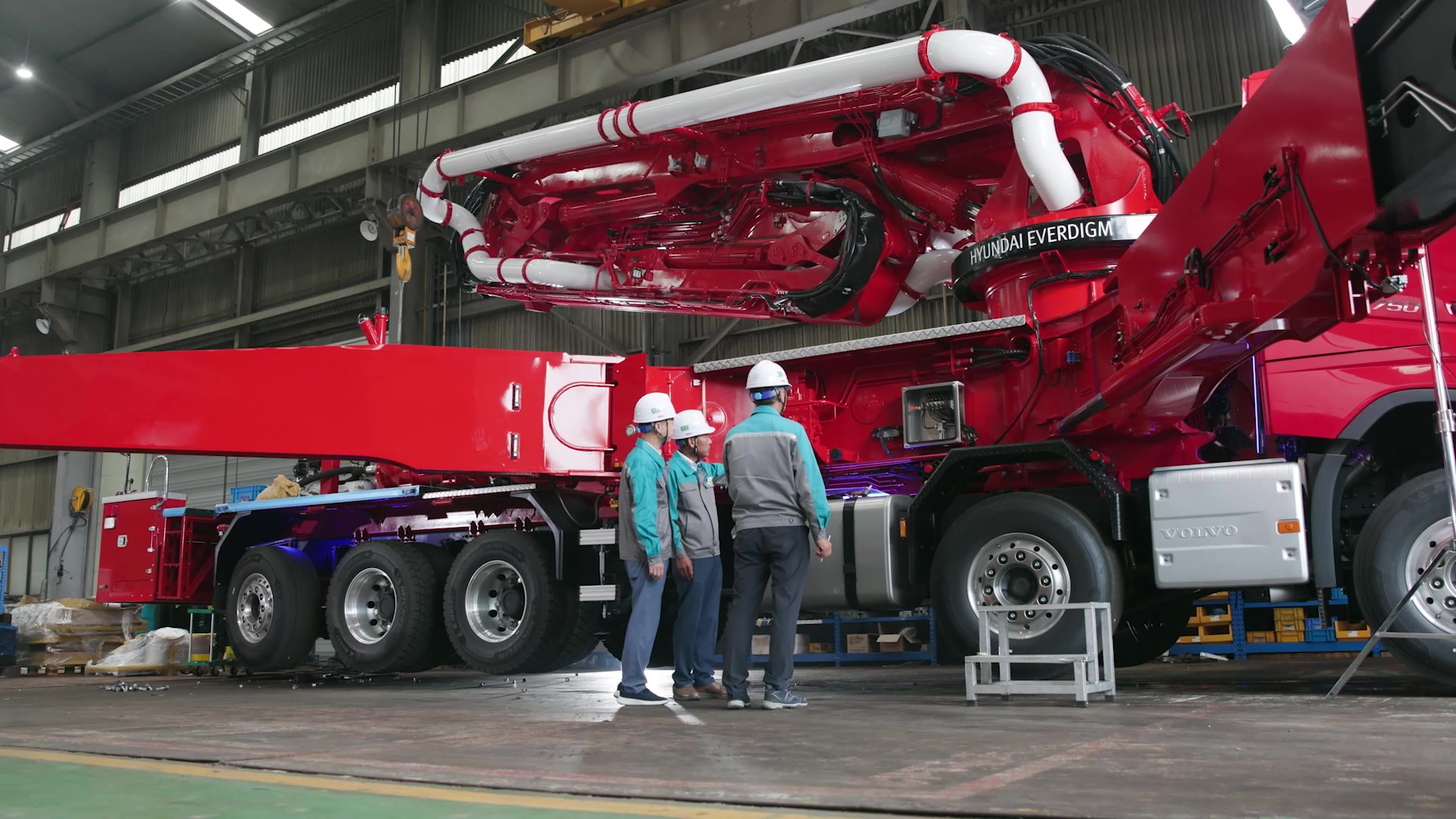
Towards digital manufacturing
Hyundai Everdigm is now exploring how it can bring greater efficiencies to its production processes and intends to upgrade its manufacturing execution system and manufacturing operations management to DELMIA Apriso. It will introduce the production scheduling management system to effectively plan and optimize production lines, material flow and cycle times. “The goal is to realize cost savings by reducing inefficiencies in production and strengthening inventory management,” Yoo said.
Looking further ahead, the company intends to take advantage of more simulation and digital manufacturing capabilities in the 3DEXPERIENCE platform to improve factory efficiency. This includes building a virtual reality appraisal system so that products, as well as production and assembly processes, can be verified in the virtual world to save time and costs.
“Our manufacturing vision is to build a smart factory powered by the 3DEXPERIENCE platform, where we will digitalize a lot of data from the production process and use it for decision-making to boost productivity,” Lim said. “In the long term, we plan to introduce virtual reality, where customers can experience real products in a 3D virtual environment. Together with Dassault Systèmes, we’re excited about how else we might use its virtual twin capabilities to optimize our factories and grow our reputation as a global leading manufacturer.”
FAQs
Heavy mobile equipment is a term used to describe large machinery primarily used in industries like construction, mining, forestry, and agriculture to handle tasks such as excavation, transportation, and heavy lifting. Hyundai Everdigm manufactures specialized heavy equipment like concrete boom pumps, tower cranes and fire-rescue vehicles.
Discover more about the Digital Equipment Continuity industry solution experience.
00:00 – 00:28
Myung-jin Lim, CEO, Hyundai Everdigm:
Hyundai Everdigm is a global company that manufactures construction equipment and emergency response equipment. We are pursuing our journey to grow into a global company by using virtual twins and digital factory tools through a strong partnership with Dassault Systèmes.
00:28 – 00:53
Jae-ki Yoo, Management Support & Finance Executive Director, Hyundai Everdigm:
Hyundai Everdigm needed a way to share accurate product information across the company. The 3DEXPERIENCE platform was designed with scalability in mind, making it a great fit for us.
00:53 – 02:01
Unkyoo Hwang (Ph.D.), Team Leader, Hyundai Everdigm:
Since we implemented the 3DEXPERIENCE platform for our five business divisions, we were able to significantly improve our collaboration by creating and utilizing independent dashboards: firefighting, concrete pumps, drilling rigs, excavator attachments, and tower cranes. This helps us handle numerous design files and hundreds of part changes that occur every day. As a result, data consistency has improved by approximately 20%.
Now we perform analyses in a single platform environment using MODSIM. This helped to improve simultaneous collaboration between the mechanical design team and the analysis team. And the ability to reuse 3D design and structural analysis data has reduced the overall development period by more than 30%.
With DELMIA, we are able to automatically generate MBOMs from the Single Source BOM structure. This helped us to reduce data inconsistencies and errors as we now have a link between EBOM-MBOM so changes are reflected in both. Compared to the past, we have improved the consistency of our BOM data by approximately 20 percentage points.
02:01 – 02:18
Jae-ki Yoo, Management Support & Finance Executive Director, Hyundai Everdigm:
Hyundai Everdigm's manufacturing vision is to build a smart factory platform. The goal is to eliminate production inefficiencies, lower production costs, increase product competitiveness, and reduce costs by strengthening inventory management.
By focusing on these areas, we aim to improve overall efficiency and profitability.

Focus on Hyundai Everdigm
Hyundai Everdigm is a developer and manufacturer of construction machinery such as pumpers, tower cranes and attachments, as well as fire trucks and disaster response equipment. The company serves the global market through a network of 150 dealers and 4 overseas subsidiaries in 110 countries. Its vision is to enhance the competitiveness of its existing products through continuous R&D, and to provide differentiated value to its customers by expanding its product portfolio and service areas.
For more information: https://hyundaieverdigm.com/main/
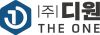
Focus on The One
The One is a Dassault Systèmes business partner providing comprehensive solutions in product lifecycle management and system integration. Based in Busan, South Korea, the company has built a strong reputation in the engineering and manufacturing sectors, offering advanced services that help companies navigate the challenges of digital transformation.
For more information: http://d-1.co.kr