Hungarian Centre for Energy Research
The Hungarian HUN-REN Centre for Energy Research (HUN-REN EK-CER) is an expert in advanced fusion energy technologies and has developed an experimental SPI (Shattered Pellet Injection) system for the ITER project using the Digital Equipment Continuity industry solution. With the 3DEXPERIENCE platform on the cloud, seamless traceability of components in the product life cycle can be ensured and engineers and physicists can work together easily.
The machine protection systems making nuclear fusion power possible
In a laboratory in Hungary, a team of physicists and engineers are developing some of the crucial technologies needed to make nuclear fusion power a viable and safe reality. One of their most recent feats involved turning hydrogen gas into frozen pellets, shattering them, and cooling the unstable plasma with a spray of cryogenic materials – a recognized safety mechanism for shutting down plasma instabilities in a fusion power plant, also known as a tokamak.
Nuclear fusion is the same reaction that powers the Sun, and various international initiatives hope to recreate it on a scale to become a sustainable energy source for humanity. Success will come down to their ability to generate and harness that power, and quickly subdue it if something goes wrong. That’s where the Fusion Plasma Physics Department of the Hungarian HUN-REN Centre for Energy Research (HUN-REN EK-CER) comes in. Its Shattered Pellet Injection system was one of the first to produce and shoot large enough frozen hydrogen pellets according to the specifications set out by ITER (International Thermonuclear Experimental Reactor), the world’s largest tokamak presently being built in France.
When ITER’s reactor becomes operational, the plasma inside its chamber will reach around 150 million °C – ten times hotter than the center of the Sun – to generate a fusion reaction. The Shattered Pellet Injector will serve as what is essentially a cryogenic fire extinguisher. It will pre-empt sudden plasma disruptions by shooting and shattering frozen neon and hydrogen pellets (at minus ~268 °C), which cool the hot plasma before it risks melting or damaging the reactor wall.
Within two years, EK-CER successfully designed, built and commissioned the experimental injector system and produced the first frozen hydrogen pellets of a large enough scale required for the ITER fusion reactor. The entire system was developed using the 3DEXPERIENCE platform on the cloud.
“We built the fully operational experimental system in record time,” said Sándor Zoletnik, head of EK-CER’s Fusion Plasma Physics Department. “Projects like this involve teams of physicists and engineers working together to understand these complex plasma systems. We’re now at the stage where several large-scale experiments are working towards real nuclear fusion power applications. As we approach 2030, we need to achieve meaningful results and it’s through collaborative technology like the 3DEXPERIENCE platform that we’ll progress faster.”
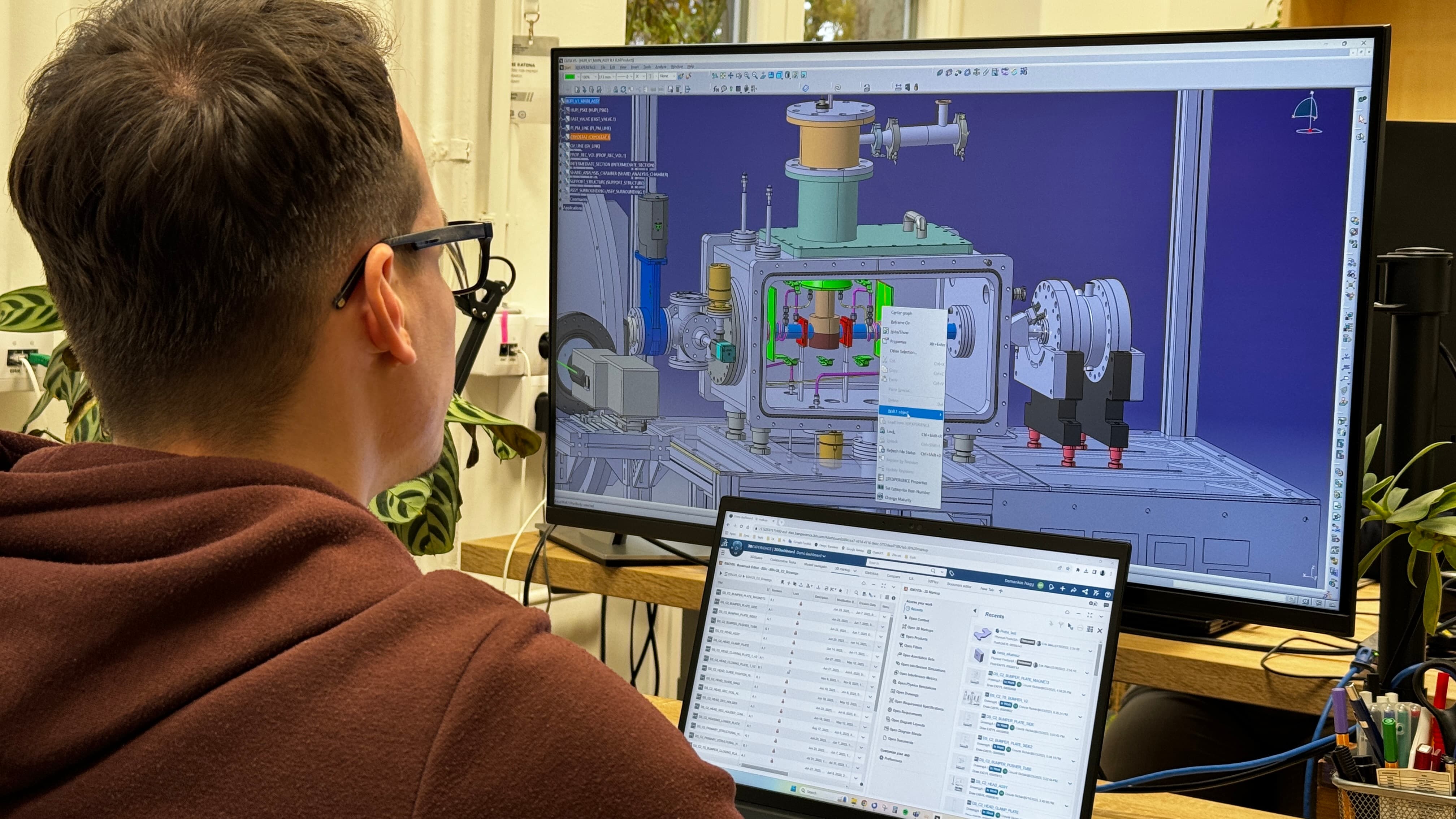
Reaching milestones faster through CAD and PLM integration
EK-CER secured its contract with ITER for the experimental injector system in 2020 and began producing its first frozen hydrogen pellets a year later. Over the following months, EK-CER explored how to make different-sized pellets and successfully launch and shatter them within milliseconds.
Central to EK-CER’s success was its ability to collaborate and track all design work within the 3DEXPERIENCE platform. EK-CER’s engineers created all the experimental injector system’s components in CATIA V5. Thanks to POWER’BY, they could seamlessly integrate all product data and 3D models within the 3DEXPERIENCE platform, allowing them to access and share information centrally.
“The 3DEXPERIENCE platform proved the best choice for CATIA integration and collaborative engineering,” said Erik Walcz, chief engineer at EK. “The seamless connectivity between our existing CAD application (CATIA V5) and the 3DEXPERIENCE platform for product lifecycle management was a big reason for the implementation. It’s made it easier for us to work concurrently on the CAD models. And our physicists can now see exactly what’s happening in the 3D models and provide feedback.”
EK-CER’s involvement in initiatives like ITER means that it’s important for its engineers to have access to industry-leading tools like CATIA, which allows them to bring complex ideas to life and innovate at speed.
“We were able to reach key milestones quickly as a result of our fast design work using CATIA in the 3DEXPERIENCE platform,” Zoletnik said. “We also used CATIA to develop all the camera holding structures and diagnostics equipment.”
As we approach 2030, we need to achieve meaningful results and it’s through collaborative technology like the 3DEXPERIENCE platform that we’ll progress faster.
Cloud keeps EK up to date
EK-CER opted for a cloud version of the 3DEXPERIENCE platform to save upfront costs and achieve the flexibility and scale it needs as it takes on these types of projects.
“We didn’t want to take on additional personnel to maintain the new IT environment,” Walcz said. “Cloud access has been a big help for us, especially as a great deal of our work ended up being done remotely. It meant we could continue developing the Shattered Pellet Injector and effectively collaborate with each other, even when we weren’t in the office together.”
Working closely with its technology partner CAD-Terv, EK-CER is successfully transforming how it manages its product data and design templates in the 3DEXPERIENCE platform. The organization benefits from CAD-Terv’s extensive experience with Dassault Systèmes software and trusts in its ability to highlight the functionality and features it needs.
“They’ve helped us redesign our entire design environment and transform how we store our design templates, moving from traditional offline libraries to a modern cloud-based, centralized repository in the 3DEXPERIENCE on the cloud,” Walcz said.
EK values the ongoing support from CAD-Terv as it gets up to speed on the platform. Its involvement in complex projects such as ITER means that EK has industry-specific requirements that need resolving fast.
“When we contact them for help, they respond very quickly and always have a solution,” Walcz said. “For example, we had an issue managing different revisions of the same component in CATIA V5. They pointed us towards a solution released in a platform update. Now, the platform automatically renames different revisions so we can easily open multiple versions of the same component in a single session.”
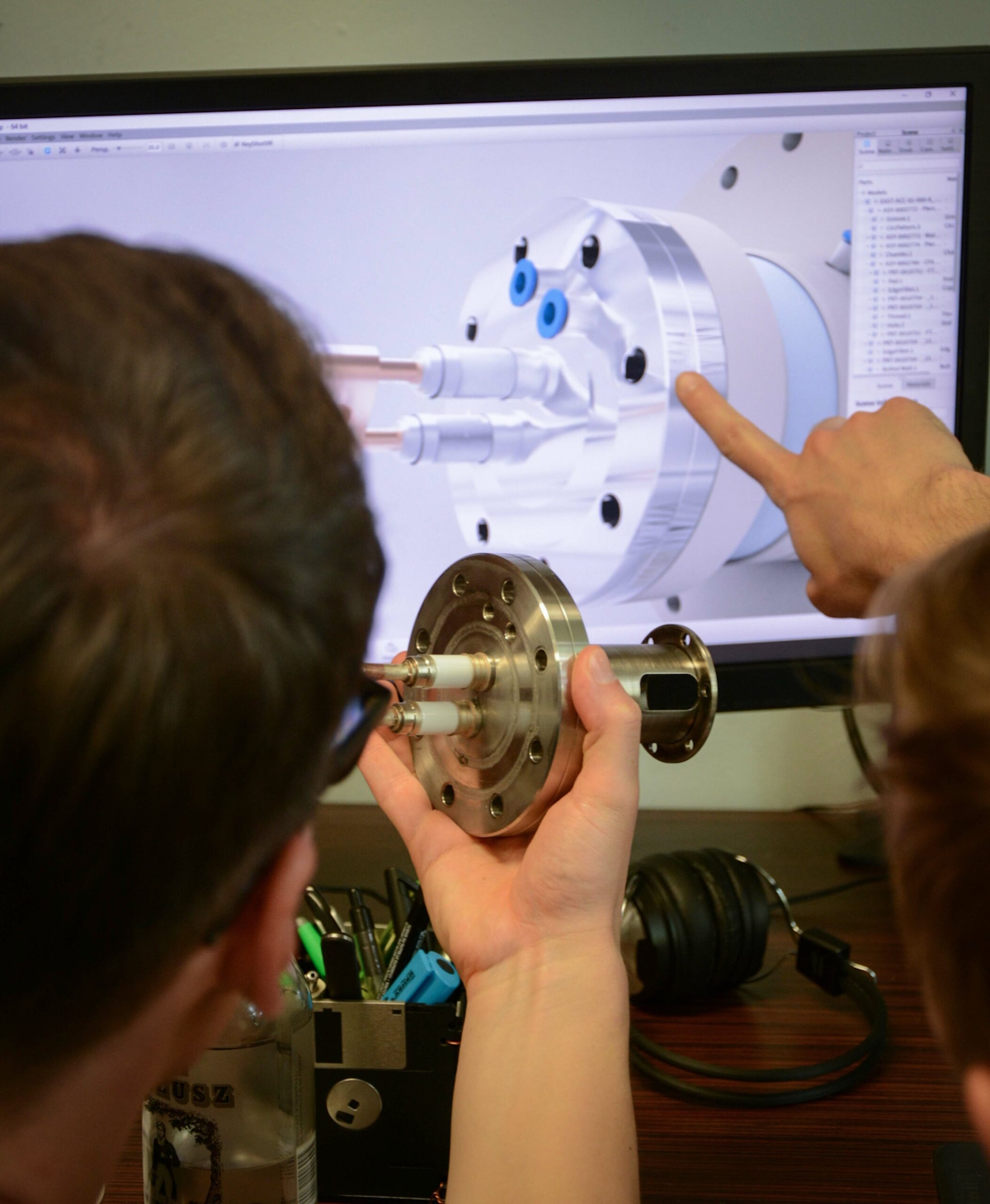
Full traceability of design changes
As well as benefiting from the 3DEXPERIENCE platform’s collaborative design features, EK-CER appreciates the ability to trace all design changes and see the impact of any modifications within the context of the whole 3D design model. This has proven critical for coordinating the work carried out by engineers working on different components of the Shattered Pellet Injector. ENOVIA on the 3DEXPERIENCE platform delivers the comprehensive change management capabilities to handle all modification requests.
“We have a number of different engineers working on the same project and each one is dedicated to a specific part of the device,” Walcz said. “These parts must integrate seamlessly within the wider system, so it was helpful to see the changes made by our colleagues in almost real time and understand the implications on the final design.”
Walcz and the rest of the EK-CER team also value how easy it has become to share and communicate design updates with physicists and other stakeholders involved in developing these innovative fusion energy technologies.
“The 3D Markup feature in the 3DEXPERIENCE platform allows us to add notes and draw on the CAD models, making it much easier to present the work we’re doing intuitively,” he said. “Another major benefit is the user-friendly interface and the web-based access with model viewer integrated into the process.”
The 3DEXPERIENCE platform proved the best choice for CATIA integration and collaborative engineering. It’s made it easier for us to work concurrently on the CAD models. And our physicists can now see exactly what’s happening in the 3D models and provide feedback.
Supporting future energy projects
Beyond the experimental Shattered Pellet Injector system for ITER, EK-CER is already using the 3DEXPERIENCE platform on the cloud in several other nuclear fusion and energy-related initiatives. Having a centralized and standardized IT environment makes it easier for its engineers to transfer between different roles and projects.
“Work is already underway on another ITER project to develop a fast shutter device and we’re using the 3DEXPERIENCE platform with CATIA for all CAD work; it’s our design application of choice,” Zoletnik said. “Now, regardless of which organization or country we build our innovative systems and technologies for, we can use the same tools. It makes it easier for people to switch from project to project and work as efficiently as possible.”
“Without the platform, these types of projects would be very challenging to handle,” Walcz concluded.
Discover more about the Digital Equipment Continuity industry solution experience.
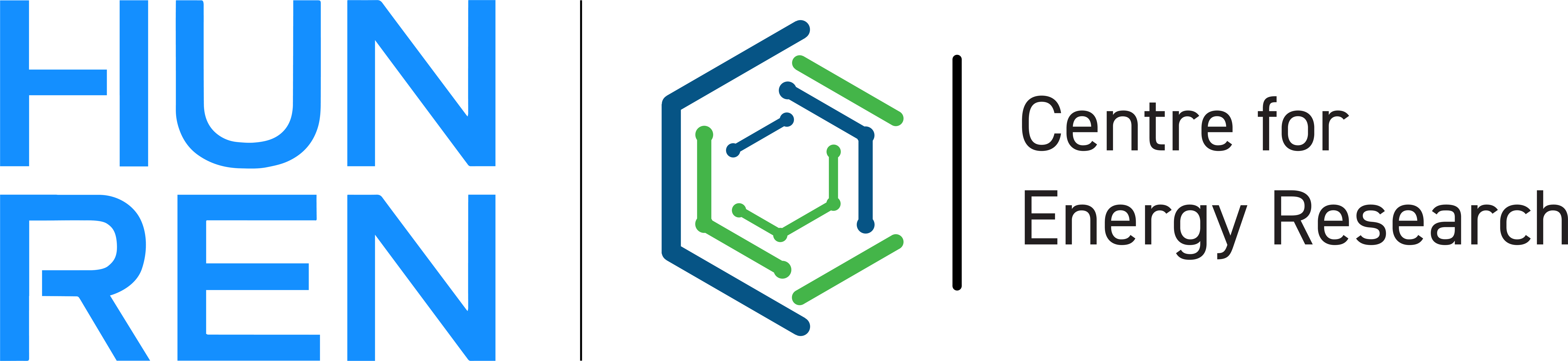
Focus on the Hungarian Center for Energy Research
The aim of the Hungarian HUN-REN Centre for Energy Research (HUN-REN EK-CER) is to carry out basic, applied and developmental scientific research of international standard in the fields of nuclear energy, functional materials and nano systems, environmental protection, energy efficiency and energy security.
For more information: www.ek.hun-ren.hu
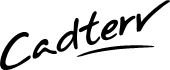
Focus on CAD-Terv
CAD-Terv Engineering Ltd. has been offering professional services for the implementation of Dassault Systèmes 3DEXPERIENCE solutions since 1997. The company assists its clients in choosing the ideal program suite and hardware by solving company-specific issues and organizing product demonstrations. It also offers consultations to help users with their everyday work, as well as tailor-made training courses.
For more information: www.cadterv.hu/en/