Bridge the gap between the virtual and real world to accelerate from concept to operations
HORYZN
HORYZN is a German student project at the Technical University of Munich (TUM) that is researching the use of drones to deliver defibrillators faster than an ambulance in emergencies. Implementing the 3DEXPERIENCE platform on the cloud enabled the centralization of all aspects of its fixed-wing drone, resulting in improved collaboration, elimination of the need for physical prototypes, and major time and money savings.
Life saving drones
We’ve all seen drones used for aerial photography, maybe even for building inspections. But imagine a drone that could save lives.
A group of students from HORYZN, part of the NEXT Prototypes E.V. Association – a non-profit student organization at the Technical University of Munich (TUM) in Germany – is designing exactly this. HORYZN’s electric vertical take-off and landing (eVTOL) fixed-wing drone can drop a defibrillator at an emergency site twice as fast as an ambulance on the road, increasing the survival chance of a patient suffering from a cardiac arrest by up to three times.
“We noticed many blind spots when it comes to emergency response times, especially in rural areas,” said Seongmin Park, computer aided design (CAD) lead at HORYZN. “The time it takes for the emergency services to arrive at a destination can be up to 20 minutes.”
But 20 minutes is too long considering that a defibrillator must be used within five minutes to be most effective. If used within this critical period, they can increase the survival rate of out-of-hospital cardiac arrest from less than 10% to 70%. Every minute counts.
Our unique aircraft can carry a payload of two kilograms at a speed of 120 kilometers per hour. Since the fuselage and wings are made from carbon fiber, it weighs only 22 kilograms in total.
A unique design, created in the 3DEXPERIENCE platform
The HORYZN drone, part of a project called ‘Mission Pulse’, was designed, tested and validated using Dassault Systèmes’ 3DEXPERIENCE platform on the cloud. The eVTOL drone benefits from the versatility of a quadrotor, which can take off and land vertically, and the speed and efficiency of aerodynamic lift you get from an airplane that flies and cruises.
“Our aircraft doesn’t need a runway,” said Park. “We have eight co-axial motors that allow the drone to take off and land vertically, as well as two propellers on our wing tips which allow horizontal flight. This means space is not a constraint. The aircraft can fly anywhere.”
This isn’t the drone’s only differentiating feature – it is fast, too. “Our unique aircraft can carry a payload of two kilograms at a speed of 120 kilometers per hour,” said Lucas Lindner, business lead at HORYZN. “Since the fuselage and wings are made from carbon fiber, it weighs only 22 kilograms in total.”
The drone can also hover for long periods so that an operator can safely lower the defibrillator from the drone to a patient. “One of the challenges for Mission Pulse is that, because of various regulations, we are not allowed to land a drone in close proximity to bystanders,” said Leonard Aupperle, project lead of Mission Pulse at HORYZN. “That meant we needed to develop a winch system to lower a defibrillator while the drone hovers at 50 meters. We added a parachute to ensure that, if something does go wrong, the drone can land safely and nobody on the ground gets hurt.”
Once the defibrillator is at the scene, anyone can use it easily – even if they’re not a trained medical professional. That’s because, once powered on, modern defibrillators provide spoken step-by-step instructions.
The path to success
HORYZN was established in 2019 with the motto of ‘prototyping the aerospace of tomorrow’. “Our first mission, ‘Silencio Gamma’, was to develop an eVTOL-type drone that could fly as energy-efficiently as possible over a predetermined flight path while doing certain maneuvers,” said Aupperle. “The eVTOL had to carry a payload with a specific weight and volume.”
While HORYZN completed Silencio Gamma successfully, it realized that to move forward with Mission Pulse, it would need 3D modelling software. “TUM already had a few CATIA V5 licenses, so we contacted Dassault Systèmes to see if it would sponsor more users,” said Seongmin Park, computer-aided design (CAD) lead at HORYZN. “However, after speaking with Dassault Systèmes’ education team, it soon became apparent that we could do so much more if we were to adopt Dassault Systèmes’ 3DEXPERIENCE platform on the cloud.”
Dassault Systèmes’ education team demonstrated how the HORYZN students could do everything they needed – including project management and collaboration – across all the various processes, from initial ideation to prototyping and validation – all within the same cloud-based platform.
“Until that point, we were all working independently using different software solutions and platforms for the various parts of the development process,” Park said. “We realized we could work much more efficiently using the 3DEXPERIENCE platform on the cloud.”
And so, Dassault Systèmes sponsored the HORYZN team’s access to the platform. “Migrating from one platform to another can be very difficult,” Park said. “However, we’ve had so much support, which has made the whole process incredibly smooth.”
Once the senior members of the HORYZN team were up to speed with the platform, they could set up a learning system. “We’ve had a new recruiting phase in the past couple of weeks,” Park said. “I developed a workshop to transfer knowledge to new members. Preparing this was enjoyable. It was easy to explain the thought process behind the different apps arranged on the dashboard, and how they could be used in conjunction with modeling, collaboration and project management. After going through the process of learning everything, being able to pass that knowledge on was really rewarding.”
The integration of modeling and simulation helped us improve and verify our designs. For example, when designing the fuselage, we must find the optimal way to introduce loads. With SIMULIA, it’s easy to simulate the impact of carrying various weights – and we can do this right at the ideation stage.
A streamlined design process
Because the 3DEXPERIENCE platform is hosted in the cloud, there’s no lengthy implementation. The HORYZN team was able to access all the apps it needed immediately. “Using CATIA on the platform, we instantly saw improvements to the design process,” Aupperle said. “It’s so much more streamlined now. All the functionality previously contained in different tools is now in the same place.”
Individuals no longer work in silos. “Before this implementation, each design team member would work independently on a design on their device,” said Park. “They would then upload that design to a third-party app. Other team members would then have to manually download that file to their own devices to continue editing. Since we all now work in the same environment, we don’t need to do any of this. There’s no danger of the file we need getting lost or damaged, and we know we will always be working on the latest version of a design. Moreover, we save a lot of time because we don’t have to keep opening different apps.”
With everyone working together in the same environment, collaboration has improved. “The streamlined workflow has meant that everyone knows the current status of a project,” said Park. “From a project management perspective, this is useful. I can see the changes that have been made and quickly see what everyone is working on.”
“For the structure team, it’s also essential that they can see what the CAD team is doing and keep track of the various parts to assess the manufacturability,” added Aupperle. “The 3DEXPERIENCE platform made this possible.”
An integrated approach
The HORYZN team also now benefits from an integrated modeling and simulation (MODSIM) approach, meaning simulation drives the entire development of the Mission Pulse drone, from beginning to end. “The integration of modeling and simulation helped us improve and verify our designs,” said Aupperle. “For example, when designing the fuselage, we must find the optimal way to introduce loads. With SIMULIA, it’s easy to simulate the impact of carrying various weights – and we can do this right at the ideation stage.”
All the designs of the internal structures of the Mission Pulse drone were validated in this way, saving the HORYZN team significant time and money. “Being able to simulate load tests and verify our designs before building the drone has been transformational for us,” said Park. “In the past, we would physically build a prototype and only when it broke would we realize something was wrong. We crashed nine or ten prototypes working this way – which was costly and time-consuming.”
Once designed, the various parts of the drone have been brought together into a 3D model. “Everything came together perfectly,” said Park. “Seeing the final drone come to life was incredible.”
Feedback so far has been incredibly positive. “We’ve had fantastic feedback from big industry players, politicians and other organizations working on similar projects,” said Lindner. “We’ve also had a lot of press coverage. Overall, we are delighted with what we have achieved.”
Being able to simulate load tests and verify our designs before building the drone has been transformational for us. In the past, we would physically build a prototype and only when it broke would we realize something was wrong. We crashed nine or ten prototypes working this way – which was costly and time-consuming.
Thinking for the future
The HORYZN team is now working towards achieving operational authorization for its Mission Pulse drone. By demonstrating the feasibility of the idea, it hopes that the concept may be picked up by a company that could take it to market. “We are working with the aviation authority here in Germany on achieving operational authorization,” said Lindner. “This will be the hard part. However, urban air mobility is a very new industry. That means we must push boundaries if we want to change how we travel in the future. Being part of this initiative and this wave of innovation is incredibly exciting. We believe we have created a prototype product that will have global appeal and, most importantly, help save lives.”
There’s even more potential for the future. “In the years to come, this technology could be adapted for emergency EpiPen deliveries or to drop off emergency drugs, for example,” said Aupperle. “There’s many possibilities to explore.”
The team is looking forward to using more of the 3DEXPERIENCE platform in future projects.
“The platform has so much to offer for us,” says Lindner. “ENOVIA, for example, can help us with project management and to further integrate our teams. We can make better use of the 3DEXPERIENCE Edu community, where we can share ideas and best practices with other student groups like ours. We are also interested in using GEOVIA for modeling the planet to find and better calculate the locations of where to drop off the defibrillator, and, eventually, we hope to use the platform to help us apply model-based systems engineering to our processes. Ultimately, we need a future-proof platform to continue prototyping the aerospace of tomorrow. The 3DXPERIENCE platform is exactly that.”
This is only the beginning. As the students involved in the Mission Pulse project move on into employed work, their experience with the 3DEXPERIENCE platform will prove invaluable.
“It’s been a privilege to use such professional software before we enter industry,” said Lindner. “What’s great is that it’s not a watered-down version – we are using the actual tools that we will go on to use at work.”
“Many of the biggest aerospace companies, including Airbus, Boeing and Embraer, use the 3DEXPERIENCE platform,” said Park. “That means the experience we have had in working with the platform may be very beneficial in our future careers.”
Aupperle agrees, adding that the 3DEXPERIENCE platform has demonstrated how to work as part of a team in a professional way. “It has allowed me to learn how to manage a big project effectively and collaboratively,” he said. “This will undoubtedly be useful as we enter employment.”
Discover more about the Reinvent The Sky industry solution experience.
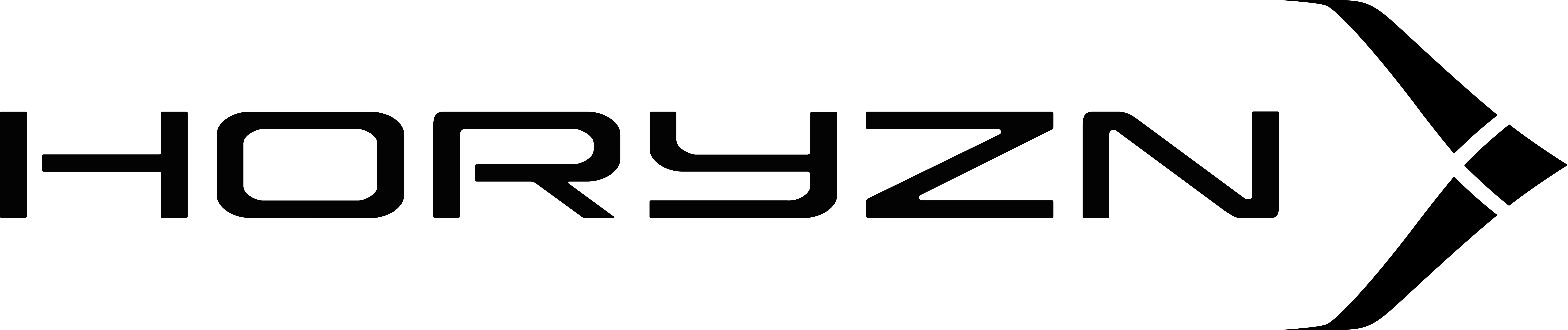
Focus on HORYZN
Founded in 2019, HORYZN is a student initiative consisting of 80 Bachelor, Master and PhD students from the Technical University of Munich (TUM). Its goal is to apply the theoretical knowledge gained in education by developing electrical vertical take-off and landing (eVTOL) unmanned aerial vehicles. As an international and interdisciplinary team, HORYZN comes up with innovative solutions for real-world problems.
For more information: https://horyzn.org/