Hirth Engines
German engineering company Hirth Engines specializes in developing two-stroke engines and adopted the 3DEXPERIENCE platform on the cloud to manage its data centrally. The Program Excellence industry solution experience provides the company with all the necessary functions and leads to increases in productivity and a continuous improvement in the quality of its products and processes.
Now that we work with the 3DEXPERIENCE platform, ordering obsolete parts is no longer possible; only finalized parts are released for the purchasing team to buy. And sales can respond faster to customer emails by going into the system and getting the insights they need.
Light two-stroke engines for power and performance
From a state-of-the-art workshop in Benningen, Germany, a young and dynamic team of engineers makes some of the most compact, light and fuel-efficient engines available on the market today. They work for Hirth Engines, building upon the German company’s long-established reputation as a pioneer in two-stroke propulsion technology. Everything about their approach is highly specialized. Collaborating closely with their customers, the engineers handle the entire development process for each engine in house, combining skilled workmanship with innovative technologies and techniques to deliver high-quality, reliable engines used in unmanned aerial vehicles (UAVs), light sport aircraft, snowmobiles and more.
Customers choose Hirth’s engines for their high power-to-weight ratio, delivering approximately two horsepower (HP) to every kilogram. Compared to four-stroke alternatives, Hirth’s powerful engines are lighter and have fewer moving parts, making them ideal for the demanding requirements of the UAV market, where flight endurance is key.
“Our mission is to accelerate innovation in the two-stroke engine market, drawing on our core competencies in cylinders, crank piston mechanisms, as well as engine calibration,” said Torsten Windorfer, head of research and development at Hirth Engines. “Our engine portfolio, which ranges from 8 to 70HP, is orientation independent and available in multiple configurations with options for box or in-line design according to our customers’ specific needs. It’s this customer-tailored approach that allows us to make the perfect engine for the most demanding applications, complete with full aftersales support.”
Renowned for its exacting standards, Hirth constantly looks for ways to improve its processes and become more agile so it can continue developing the best propulsion systems for the future of aviation. To this end, Hirth’s young team is always open to embracing new technologies. It’s this forward-thinking spirit which led the company to the 3DEXPERIENCE platform on the cloud and an opportunity to significantly improve process quality. Through digital transformation, Hirth is reducing late-stage design rework and removing unnecessary manual steps – critical in a highly skilled workforce doing hours of manufacturing by hand.
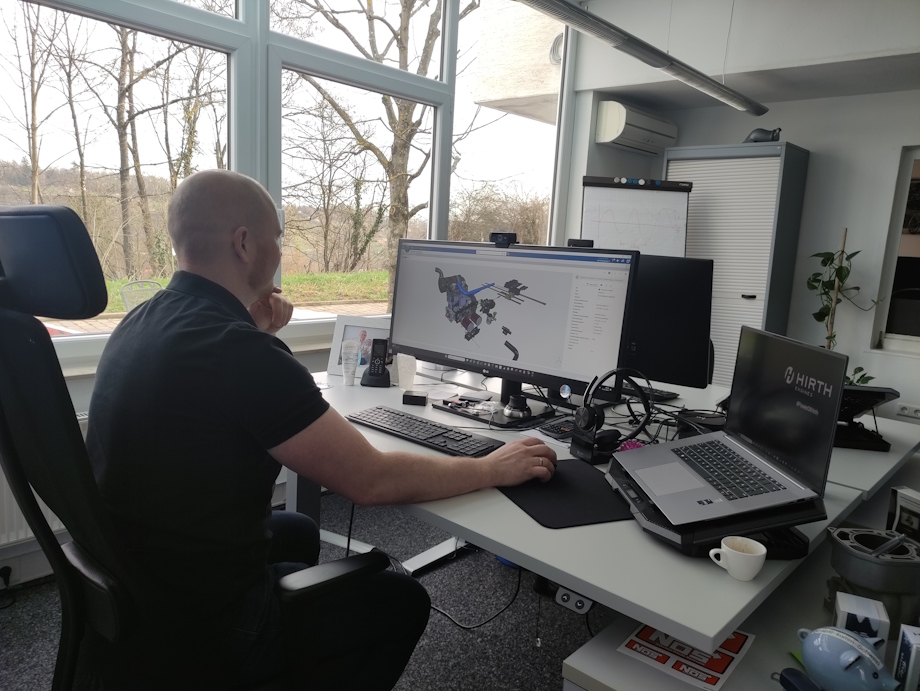
Platform addresses data management issues
Before moving its design and engineering processes to the 3DEXPERIENCE platform on the cloud, Hirth was already familiar with Dassault Systèmes software. Engineers used CATIA V5 to design all engines and components, and while the solution delivered all the capabilities they needed, they relied on a file-based system to store and manage all data, which was prone to error.
“We had many folders where we saved different parts and moved them back and forth,” said Samuel Allag, development engineer at Hirth. “If you accidentally changed a part name, then you could easily lose it. And only R&D could access the files, which added to our workload as we dealt with information requests. When working remotely, it took a long time to load big assemblies and we risked overwriting our work.”
Hirth’s technology partner Schwindt Digital suggested the 3DEXPERIENCE platform on the cloud as a solution. Schwindt Digital understands how Hirth operates and created a technology roadmap to address its data management challenges.
“We didn’t have a product lifecycle management system before,” said Antonio Colaciello, development engineer at Hirth Engines. “When Schwindt Digital showed us a proof of concept, we were excited to see how the 3DEXPERIENCE platform could change the way we work for the better.”
Hirth moved fast to digitally transform and Schwindt Digital has been there every step of the way. Early on, it supported the manufacturer to modify its workflows to take full advantage of the platform, including setting up a new release and issue and change management process in ENOVIA.
“It was a lot of work for us initially as we had to change our approach to issue and change management,” Colaciello said. “Before, everything was done much more manually with a lot of going back and forth making changes to printed out drawings. Sometimes, we encountered problems with parts that didn’t fit. This is no longer happening since we’ve added in tolerances and made the change management process more transparent and automated.”
Centralized collaboration on cloud boosts productivity
More companies like Hirth increasingly trust in the cloud as an environment for their mission-critical processes. Again, Dassault Systèmes business partner Schwindt Digital demonstrated the value of a cloud-based platform and its inherent data security.
“They showed us how Dassault Systèmes encrypts data as well as all the security measures in place, including regular audits,” Allag said. “It gave us confidence that our data would be secure, and there have been no issues complying with our customers’ security requirements.”
Now that Hirth’s engineers work within the 3DEXPERIENCE platform on the cloud, they can collaborate remotely and easily see what their colleagues are working on.
“Our performance is far better,” Allag said. “We can work from anywhere in the world, as long as we have internet access. This connectivity also makes it possible to work simultaneously on a product as we can see live updates and you can’t overwrite yourself, even in the same assembly.”
Making the switch to the cloud-based platform makes it easier for different teams across Hirth, including the sales, purchasing and production departments, to gain access to the data they need at any time. This helps to boost productivity and reduce the number of mistakes that arise from using outdated or wrong information.
“One of our core objectives was to improve database operations and transition from paper to digital drawings,” Windorfer said. “Instead of printing out drawings to share with the production and purchase departments, they can see the assembly and parts and extract the required data. Now that we work with the 3DEXPERIENCE platform, ordering obsolete parts is no longer possible; only finalized parts are released for the purchasing team to buy. We’ve also improved efficiency as they can automatically generate the needed PDF and step files. And sales can respond faster to customer emails by going into the system and getting the insights they need.”
This new, centralized approach also improves the way Hirth communicates with its customers – something the company hopes to improve even further in future.
“The 3DDrive storage application on the 3DEXPERIENCE platform is very handy for quickly sharing files with customers,” Colaciello said. “Every exchange is carried out within a single, collaborative space. One day, we might even use the 3DEXPERIENCE platform to share 3D models and work together on designs.”
We were excited to see how the 3DEXPERIENCE platform could change the way we work for the better.
Better connections improve quality
Centralized data management is not the only benefit of the 3DEXPERIENCE platform. Hirth’s engineers appreciate the platform’s intuitive interface and the ability to work on parts and components within the context of the wider engine assembly.
“The new user interface is easy to use,” Allag said. “We can see all the tools and functions and customize the dashboard according to our specific needs. Being able to view the engineering connections in the assembly design is really helpful. If you’re connecting a bolt to a bore, you click on those parts and the rest of the model automatically goes invisible. We also enjoy the relations tool, which allows you to highlight certain parts and see all the connections together with the bill of materials. It’s ideal if you want to use the same parts in different engines or connect different sub-assemblies together.”
Greater visibility helps to continually enhance traceability and quality, ensuring that every part is appropriately checked and signed off before progressing to the next product development stage.
“The release role in ENOVIA is great for tracking changes and directing approvals to the appropriate person or team,” Colaciello said. “For example, if we need to make a minor change, it doesn’t necessarily need to be approved by the head of R&D. Similarly when our quality engineer sees that a part is wrong and needs changing, it can be done straight away.”

Faster time to value
Now that Hirth is up and running on the 3DEXPERIENCE platform, it is reaping the rewards of its digital transformation. Key to the company’s success so far has been its willingness to adapt its workflows, embrace change, and carefully plan which data to import into the platform, ensuring there are no ghost links or missing parts.
“The integration step is key,” Allag said. “We did a lot of pre-assessments with Schwindt Digital to get this right. You also don’t have to move everything upfront. We realized that we only needed to transition the engines, parts and data that we currently work on. This way, the time to value is much faster.”
Looking ahead, Hirth plans to take advantage of ENOVIA’s project management capabilities and extend its use of CATIA for electrical engineering and wire harness design. The company also sees value in the platform’s computational fluid dynamics simulation capabilities, available in SIMULIA.
“At the moment, it’s laborious for us to manually design the whole wiring harness,” Allag said. “With the new functionality in CATIA, we’ll be able to simply drag components in. Since we’re doing a lot more wiring and electrical connections ourselves, we’d benefit from a faster process. We’re also looking into simulation to improve our products further, especially in terms of using lighter and more efficient materials and components. SIMULIA has these features, and we like the idea that it’s all connected on the platform.”
As the company develops its next generation of two-stroke engines for UAVs and pursues innovative propulsion concepts and sustainable, alternative fuels, it’s confident in the power of the 3DEXPERIENCE platform and its partnership with Schwindt Digital and Dassault Systèmes to support its continued evolution.
“We’re beginning to see the clear benefits of moving to the platform,” Windorfer said. “And our collaboration is a true partnership. We receive excellent support and feel valued as a customer. It’s a real win-win.”
We’re also looking into simulation to improve our products further, especially in terms of using lighter and more efficient materials and components. SIMULIA has these features, and we like the idea that it’s all connected on the platform.
Discover more about the Program Excellence industry solution experience.
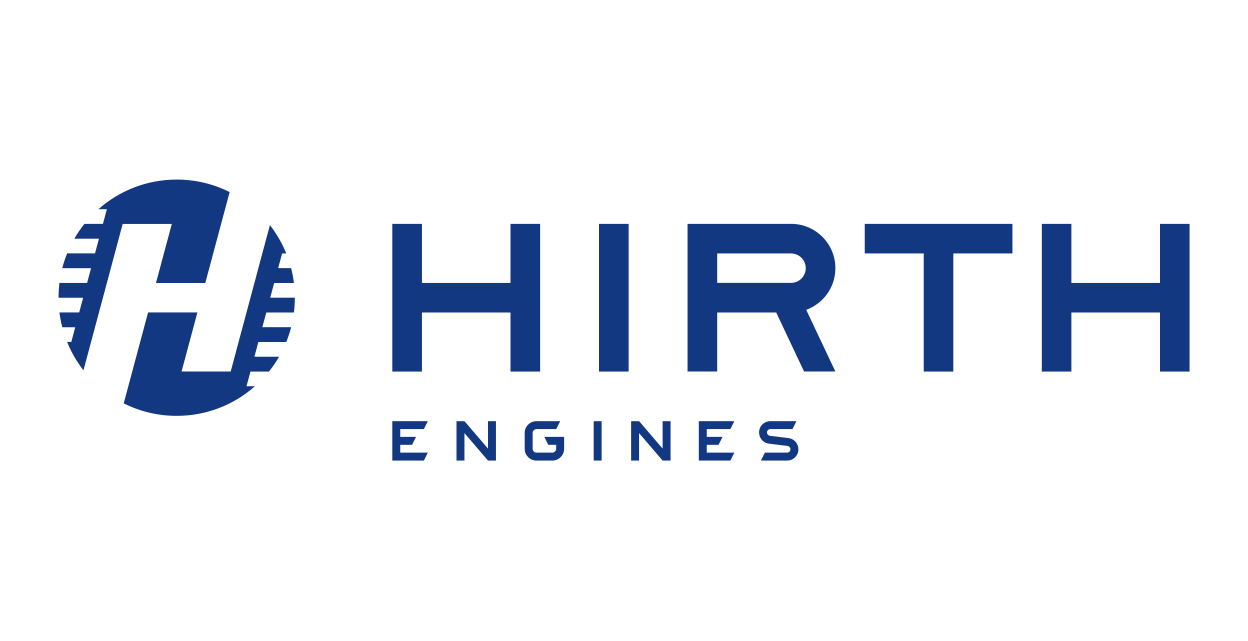
Focus on Hirth Engines
Hirth is a pioneer of two-stroke engines for light and recreational aircraft, UAVs, snowmobiles, hovercraft and fire engine pumps. The company has solid foundations in European heritage and German technology expertise, backed by engineering excellence and innovative business practices. Hirth’s international presence allows worldwide adoption of its industry-leading engineering solutions.
For more information: https://hirthengines.com
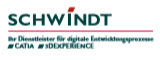
Focus on Schwindt Digital
With more than 30 years of experience, Schwindt Digital’s purpose is to help businesses achieve their full potential. The Germany-based company’s experienced consultants possess specialized knowledge of digital process optimization solutions covering the full 3DEXPERIENCE platform suite, including CATIA and ENOVIA. With digitalization, innovation and sustainability at its core, Schwindt Digital designs customized solutions to tackle the most challenging technical issues, backed by virtual and in-person training and 24-hour service. Schwindt Digital is a founding member of 3DX Alliance, a group of Dassault Systèmes partners with the mission to empower digital transformation for local and global customers across industries with the 3DEXPERIENCE platform.