HeliAir
Austrian HeliAir transforms standard helicopters into medical emergency centers using the self-developed interior concept KOKON designed on the 3DEXPERIENCE platform on the cloud. With the Passenger Experience industry solution experience, the company can manage the entire development process, use virtual reality to create immersive demonstrations and involve healthcare professionals in decision-making processes.
The feedback to the VR installation was great. Medics interacted with it and commented on how realistic the interior looked.
KOKON interior configures emergency helicopters faster
In an emergency when every minute counts, air ambulances play a critical role in saving patients’ lives. Up in the air, these flying medical centers carry the latest specialized equipment doctors need to deliver life-saving treatment. Every inch of capacity within the helicopter cabin is optimized so that crew have the space and flexibility to work effectively and easily access all the equipment they need.
One company specialized in developing these emergency medical services (EMS) interiors is HeliAir. The Austrian company is behind a self-supporting interior trim concept called KOKON, designed to simplify the integration of medical equipment into the helicopter by removing the need for special adaptations, and helping to reduce costs, labor and down-time in the process.
Lightweight and spacious yet robust, the KOKON carbon-fiber cabin has a grid system with attachment points to accommodate all sorts of equipment, fixtures and fittings, from medical devices for EMS helicopters to kits for security forces. Available as a standard option on the Airbus Helicopters H135, the patented airframe interior can be customized to suit any configuration and new equipment can be added without the need for additional certification. HeliAir develops each design from the ground up on the 3DEXPERIENCE platform on the cloud.
“Our aim was to make best use of all available space in the helicopter and reduce every kilogram of excess weight, which we’ve achieved with KOKON,” said Florian Bucher, head of design and production at HeliAir. “Customers choose to work with us because we handle maintenance, design and production in one organization, from one location, backed by industry-leading technology.”
Virtual Reality brings EMS interior to life
As an Airbus partner, HeliAir has long used CATIA as its main CAD software. An upcoming tradeshow in Las Vegas prompted it to move to the 3DEXPERIENCE platform on the cloud. Rather than transporting an entire helicopter to the event, the company wanted to unveil its pioneering KOKON concept using virtual reality (VR).
Working with its local technology consultant EBM, HeliAir moved its business operations to the 3DEXPERIENCE platform on the cloud and took advantage of its innate VR capabilities. Within a matter of months, the company was up and running on the platform and its interactive VR KOKON demonstrator was ready.
“It was important for us to have a local partner that talks the same language and they’ve done a great job moving us to the 3DEXPERIENCE platform,” Bucher said. “Their in-house experts are quick to help us resolve any challenges we face, and they regularly check in with us for feedback.”
At the event, prospective users appreciated the opportunity to virtually see KOKON in action and get a real sense of how the interior would look and function. The experience was designed in such a way that they felt like they were inside a real helicopter.
“The feedback to the VR installation was great,” Bucher said. “Medics interacted with it and commented on how realistic the interior looked. It gave them an accurate impression of how the equipment fitted within the helicopter and let them see how they could work within the space.”
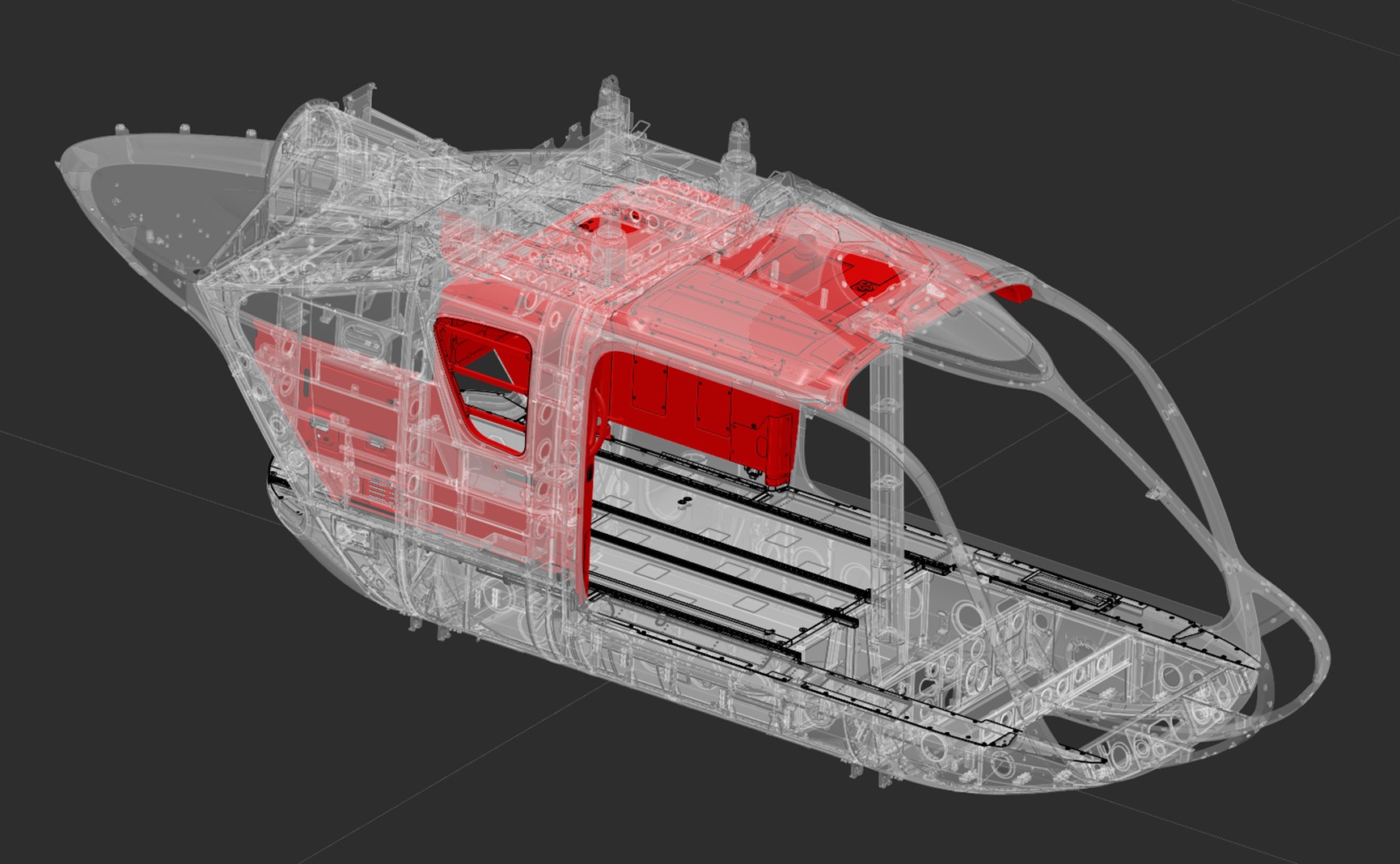
Medics validate virtual designs
The VR experience was so successful that HeliAir now uses it as part of its daily work. Designers create parts in 3D and test them out in virtual reality, seeing how they function in a particular configuration and whether they can be accessed easily.
“It’s now super fast when someone wants to change the design,” said Matthias Neuner, design engineer at HeliAir. “We can quickly mock it up in VR and visualize the distance between equipment within the cabin. It helps us to get designs right first time.”
This user-centric approach is transforming how HeliAir collaborates with its customers. Before, prospective users waited until there was a physical prototype before they could determine whether the interior setup worked for them. Now, a medic that will be working in the helicopter can try everything out in virtual reality before it’s built.
“We produce fewer prototypes and our customers have a much better idea of what they’re ordering,” Bucher said. “We now only need one or two workshops to go through the mockup and, in that time, we’re covering details such as where a latch should be positioned.”
An additional benefit of the platform is the opportunity for HeliAir to upsell its services and expand the scope of the complex projects it takes on. The agility of a modular design approach allows it to quickly develop custom solutions without impacting delivery times.
“Recently, a customer approached us to make some adaptors on our interior lining for their own equipment,” Neuner said. “However, once they saw the virtual interior, the project developed into a whole new EMS installation, which we finalized within months. We can pull up the designs and parts we need and adjust them according to each customer’s specific needs. The processes we have in design and production using the 3DEXPERIENCE platform help in every way to reduce time and cost.”
It’s easier for our production colleagues to see how parts look and understand where they go in the helicopter. The end-to-end development process is far more collaborative.
Cloud platform keeps projects on track
HeliAir benefits from the innate advantages that come with a cloud-based installation, particularly in terms of supporting remote working. The team visit customers, log in to the platform via a browser and involve them in the design process. This same connectivity is invaluable for sharing product designs with other departments across the organization, including production and assembly.
“You don’t need a license to view the 3D data, so it’s easier for our production colleagues to see how parts look and understand where they go in the helicopter, rather than relying on drawings and part numbers,” said Marco Sattlegger, design engineer at HeliAir. “The end-to-end development process is far more collaborative.”
The 3DEXPERIENCE platform’s robust data and project management capabilities are proving invaluable for keeping HeliAir’s complex projects on track. ENOVIA helps to ensure that everyone is aware of what they need to do and when, and know they are always working with the latest information.
“ENOVIA supports us to arrange our resources better,” Sattlegger said. “We can set up a time plan and track the exact status of a project. And with all work packages presented in 3D, it’s easier to launch new projects.”
Full data traceability supports HeliAir to remain compliant with strict aviation regulations and ensure nobody tampers with parts that they shouldn’t.
“We do all the lifecycle management in the 3DEXPERIENCE platform,” Sattlegger said. “We can see if a part has already been certified and which areas we can’t make changes to. ENOVIA freezes them.”
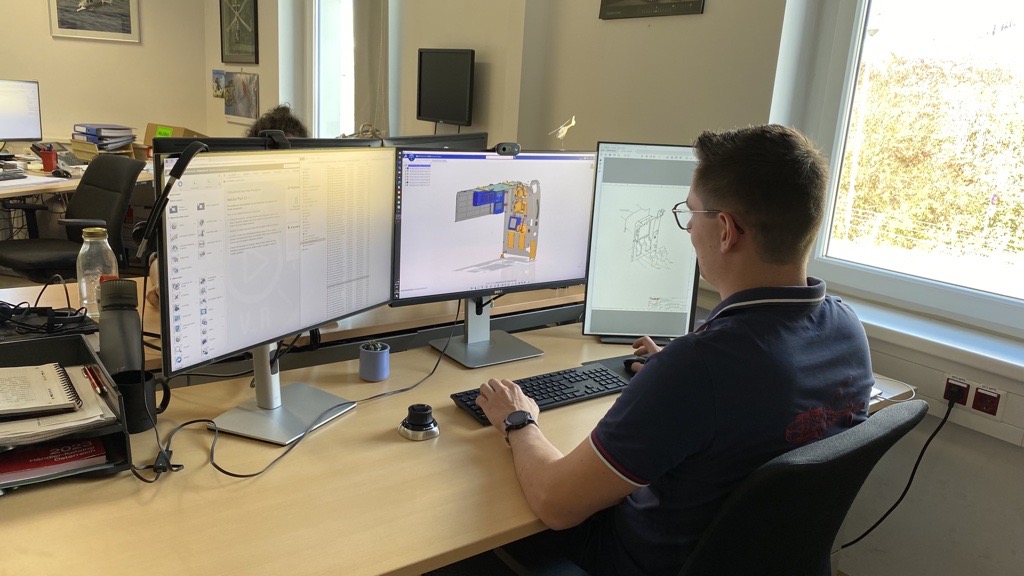
Designing lightweight yet robust parts
HeliAir uses CATIA on the 3DEXPERIENCE platform to design every element of the KOKON interior. Bucher and his team benefit from its sheet metal and freeform shape design capabilities – essential for creating state-of-the-art composite components.
“There is a good reason why most of the aerospace industry already uses CATIA,” Sattlegger said. “We appreciate the ability to do freeform designs and benefit from CATIA’s parametric capabilities. For example, we can now quickly and accurately change the thickness of the interior lining depending on the medical equipment we’re attaching to it.”
Developing interiors for helicopters comes with its own unique set of challenges, particularly in terms of ensuring every component is as lightweight and robust as possible so it can withstand high gravitational force (G-force) in flight.
“Different conditions determine how much weight the helicopter can carry before takeoff, so every kilogram counts,” Neuner said. “Everything needs to be light and strong; even a tablet holder isn’t a standard piece of equipment as it must withstand up to 20 G-force. The requirements are so much more. Using CATIA, we achieve that not necessarily with material thickness but geometry. We’re constantly adapting designs to stay within strict parameters.”
Being able to refine and validate all parts early on speeds up the transition to production. And because all designs are now parametric, HeliAir reduces the risk of errors at the assembly stage.
“The step to a physical part is now much later,” Bucher said. “We refine all parts digitally and we can be sure there isn’t a mismatch between our data.”
The processes we have in design and production using the 3DEXPERIENCE platform help in every way to reduce time and cost.
No limits to KOKON's potential
Based on the success of its digital transformation so far, HeliAir plans to extend its use of the 3DEXPERIENCE platform and is evaluating how it might take advantage of SIMULIA’s simulation capabilities.
“We’re interested in using SIMULIA’s simulations for testing composite part structures,” Bucher said. “For me, the cloud platform concept makes it easy to add new tools and packages as we require them depending on the projects we take on. That flexibility is really impressive.”
With some major EMS installations already under its belt, HeliAir is excited about the potential of KOKON and is exploring how it may expand its interior lining concept to other helicopter models and use cases. In the meantime, the 3DEXPERIENCE platform supports the company to exceed its customers’ expectations and quickly launch state-of-the-art EMS helicopters into service.
“We work in parallel with the helicopter OEM so that as soon it’s off the production line, we’re ready to install the interior,” Sattlegger said. “We usually have three weeks to integrate KOKON before it goes into service. These types of projects are only possible because we have the 3DEXPERIENCE platform. Without it, they would take too long and medical equipment would become outdated. This way we can handle more complex projects and get helicopters off the ground and into the skies faster.”
Discover more about the Passenger Experience industry solution experience.
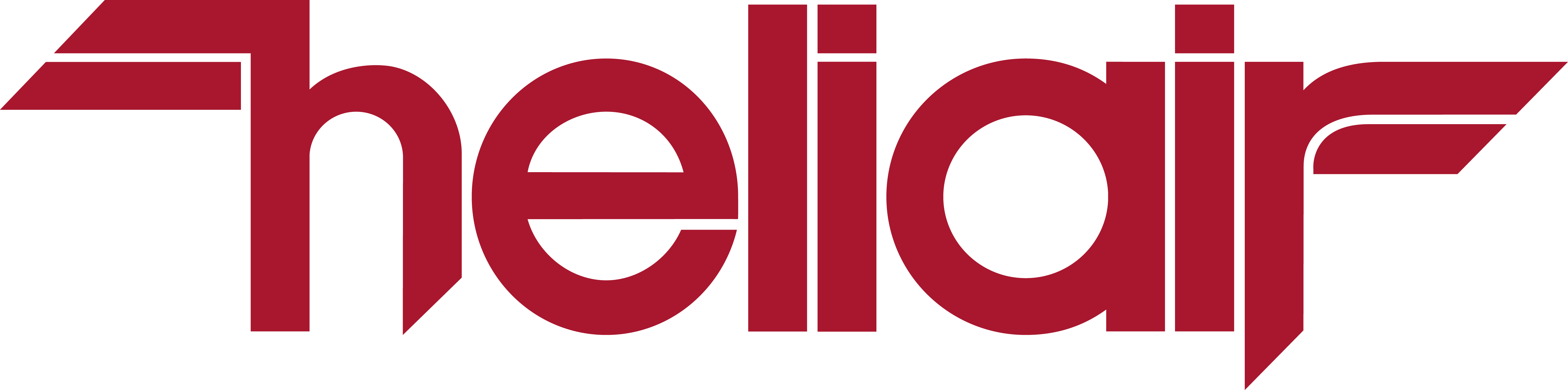
Focus on HeliAir
Based in Austria, HeliAir is one of Europe’s leading helicopter maintenance and service centers covering all aspects of fleet operations. The company is an internationally operating helicopter and aircraft maintenance and service provider for EASA Part 145, Part M, as well as a fully licensed design, manufacturing and certification center for EASA Part 21 G and J.
For more information: https://heliair.eu

Focus on EBM
EBM provides consulting, implementation services and training for Dassault Systèmes’ 3DEXPERIENCE platform applications CATIA, ENOVIA, DELMIA, SIMULIA and 3DVIA. Its specialists possess more than 20 years of experience in analyzing the customers’ requirements and designing solutions tailored to their needs. They conduct projects in compliance with industry standards, optimizing the benefit for the customer.